Question 47: For units not challenged by standpipe fluidization, are there benefits to reducing fresh catalyst 0-40 um particle content?
TODD HOCHHEISER (Johnson Matthey)
There are multiple benefits to reducing fresh catalyst 0–40-micron particle content for FCCs not challenged by fluidization. A significant portion of the 0-40 content cannot be retained in the FCC. Therefore, reducing the 0-40 content will result in less fresh catalyst being lost shortly after being added.
Lowering fresh catalyst losses has numerous advantages. Fresh catalyst addition rate and therefore fresh catalyst expense will be lower. On the reactor side, lower losses can result in lower slurry ash content, improved heat transfer in the slurry circuit, and reduced slurry heat exchanger and slurry tank cleaning frequency. For units with slurry filtration systems, lowering fresh catalyst 0-40 content will reduce particulate load. On the regenerator side, there will be less fines generated for disposal. If the FCC has a wet gas scrubber, the scrubber purge will contain less solids reducing the impact to the purge treatment and wastewater treatment units.
Stack particulate matter can also be reduced when shifting to a lower 0-40. Most of the fresh catalyst 0-40 content leaving the regenerator should be captured by the ESP or third stage separator. For units with underperforming ESPs or third stage separators, the 0-40 content reduction could have a noticeable impact on particulate matter compliance. The opacity reduction is not expected to be as large as the particulate matter reduction since opacity is preferentially impacted by microfines.
There are cases where shifting to a coarser particle size distribution has helped turboexpander performance. The fines lost directly from the fresh catalyst had a larger average particle size. In these cases, the coarser fines helped to clean the deposition of microfines on the turboexpander blades. This benefit strongly depends on the performance of the third stage separator.
In order to make the shift to a lower 0-40 content, the entire particle size distribution can be shifted in the coarser direction. This is accomplished by adjusting atomization in the spray drying process. It is recommended to speak with your catalyst supplier regarding their ability to shift spray dryer operation and the impact it may have on other catalyst properties. Another way to reduce to a lower 0-40 content is through classifying. Classifying to remove small particles is usually accomplished by wind sifting. Classifying will add to the fresh catalyst expense. The fresh catalyst expense when classifying includes standard production costs plus the cost of classifying along with disposal or reprocessing of the fines. Reducing 0-40 content through classification produces a cleaner cut compared to making the reduction during spray drying. Classifying effectively removes the front end of the distribution curve rather than shifting the particle size distribution curve.
Although the benefits discussed can be realized, for some FCCs the magnitude of the benefits will not be significant. For these units, maintaining 0-40 content can provide protection if unplanned FCC incidents occur. A cyclone hole, refractory or coke spall, or slide valve operational issues are just some of the challenges that unexpectedly arise and at that time the 0-40 content may be needed.
ZHEN FAN (Norton Engineering Consultants, Inc.)
If not fluidization limited, reducing in fresh catalyst 0–40-micron content will result in reduced losses from both the reactor and the regenerator. Of course, the attrition rate of the fresh catalyst will also contribute to the 0–40-micron fraction of the circulating inventory and may mask any improvement in losses seen by dropping the fresh catalyst 0-40 content.
MICHAEL FEDERSPIEL (W. R. Grace & Co.)
Typically, FCC catalyst is manufactured such that the particle size distribution of the fresh catalyst is within the range most suitable to circulate in a wide variety of FCC units.
The average particle size is typically manufactured to be in the middle of the Geldart’s “Aeratable” zone (see figure 1) and the smallest particles (0 to 20 µm) are minimized due to FCC cyclones inherent inability to retain those particles (see figure 2).
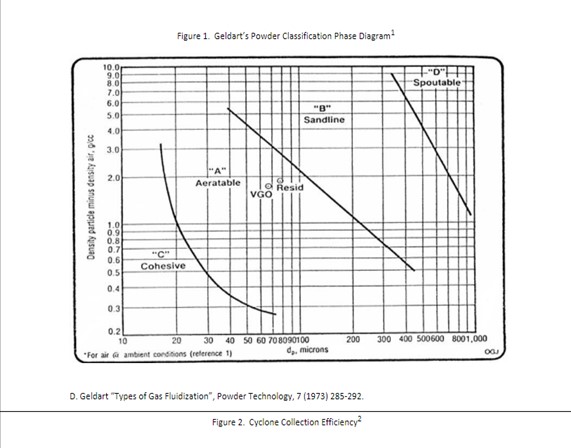
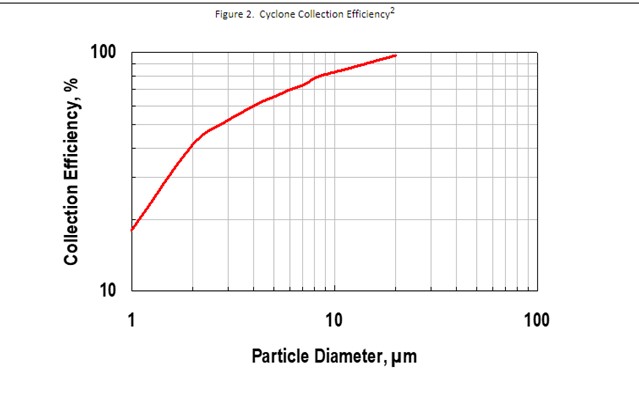
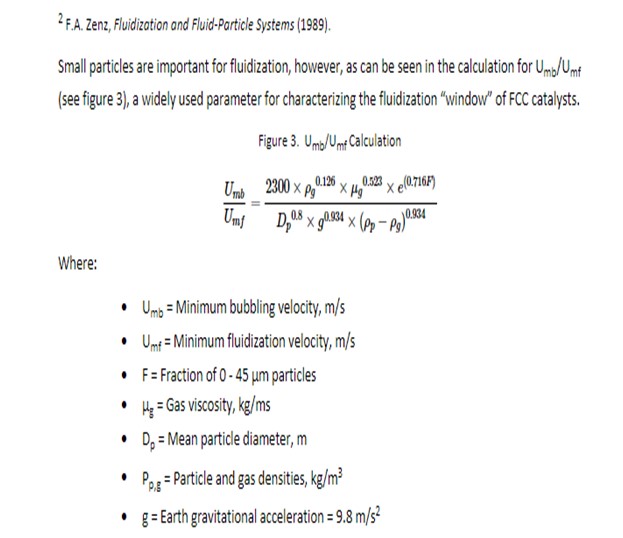
Small particles are important for fluidization, however, as can be seen in the calculation for Umb/Umf (see figure 3), a widely used parameter for characterizing the fluidization “window” of FCC catalysts.
From the equation above, we note that 0 to 45 µm catalyst plays a role in improving the fluidization window. These small particles serve to fill the voids between larger particles and slow down de-aeration of gas from the catalyst.
Maintaining catalyst fluidization at all times is critical to FCC operation. In addition to the health of the catalyst; the unit operations, and the mechanical design and condition of the equipment will all play a role in catalyst fluidization.
If there are no concerns regarding the fluidization of the catalyst in the unit, there may be some benefits to reducing the amount of the smallest particles in the fresh catalyst.
Reducing fresh catalyst 0 to 40 µm material can help reduce stack opacity. The smallest particles have the biggest impact on opacity, as they are closest to the wavelength of the light projected during the opacity measurement, are typically not retained by the cyclones. While fines are generated during the normal circulation of FCC catalyst, reducing the amount coming in with the fresh catalyst can help reduce stack opacity.
If a refinery has developed a hole in their cyclones, and since they are no longer able to retain the small particles in the unit, reducing fresh catalyst fines content can reduce the amount of material passed to either the slurry or scrubber/ESP. This can improve product quality of the slurry oil or reduce waste material handling from the regenerator side. If the refinery has a power recovery expander, this could also help reduce erosion on the turbine.
Grace offers some flexibility in our fresh catalyst formulations to help those refiners who could benefit from reducing fresh catalyst 0 to 40 µm content. Additionally, there are companies that offer catalyst classification and screening. It’s important to work with your supplier to make sure you understand the potential risk and benefits of reducing fresh catalyst 0-40 µm particle content.