Question 46: What are the main considerations in converting a fuel hydrocracker into lubes services in terms of equipment modifications and catalyst selection?
SIVADASAN (UOP LLC, A Honeywell Company)
The conversion of a fuel hydrocracker to a lube hydrocracker mainly depends upon the product quality requirements and unit constraints. If you are producing lube-based stock as your main product, then the operating parameter needs to be examined in detail. If you are trying to produce maximum quality distillate along with lube oil, then the distillate product quality will determine the operation of the unit.
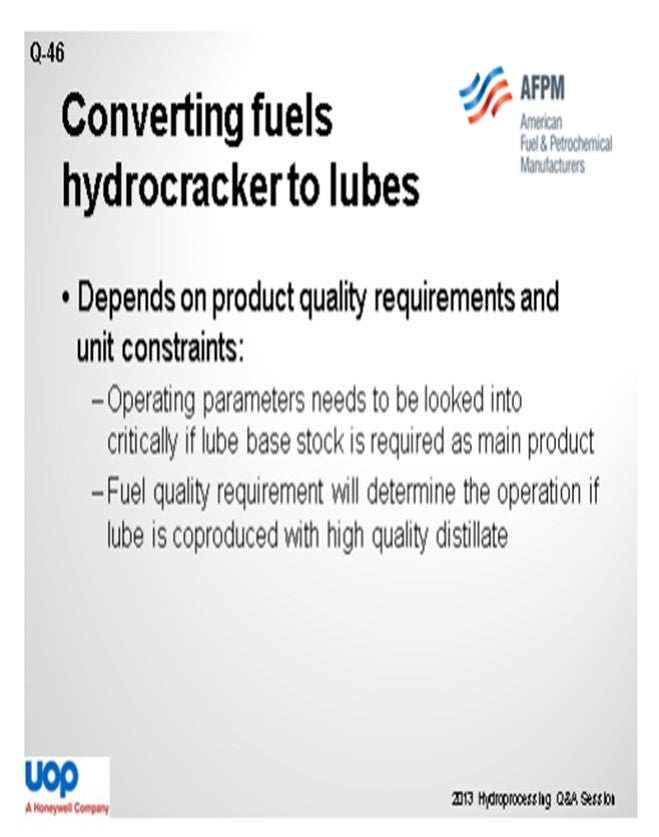
When you are looking into conversion, the two main important parameters are the feed quality and the catalyst. The feed needs to be heavy enough to give that desired viscosity for your lube-based stock. Try to eliminate the aromatic streams and limit the cracked stocks in the feed blend. When choosing a catalyst, it is better to go with the high hydrogenation catalyst to give you a good Viscosity Index (VI) and also to produce low sulfur/nitrogen (S/N) unconverted oil (UCO) for the downstream unit. Once you are going with the high hydrogenation catalyst, there will be changes in the hydrogen consumption in the unit; so, you will need to look into whether your hydrogen system is capable of handling the extra hydrogen that may be required when choosing the high hydrogenation catalyst.
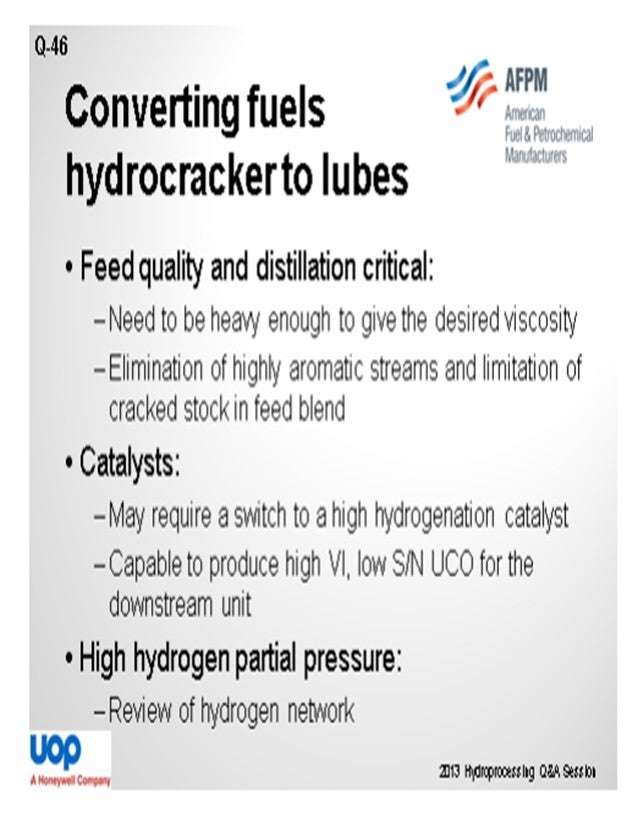
When you move into the operations, you have to look into the conversion severity. That, again, depends upon the type of operation you are doing. So if you are in a recycle mode operation, you will try to optimize the conversion per pass to have a good saturation. When trying to move from recycle mode to once-through mode, you will need to look into other parameters like LHSV, treat gas rates, and mass rate of the unit. Once you change the operating parameters, you will need to take into account whether or not your fractionator will be able to handle that kind of operation. You may have to modify your fractionator to see the changed operating conditions.
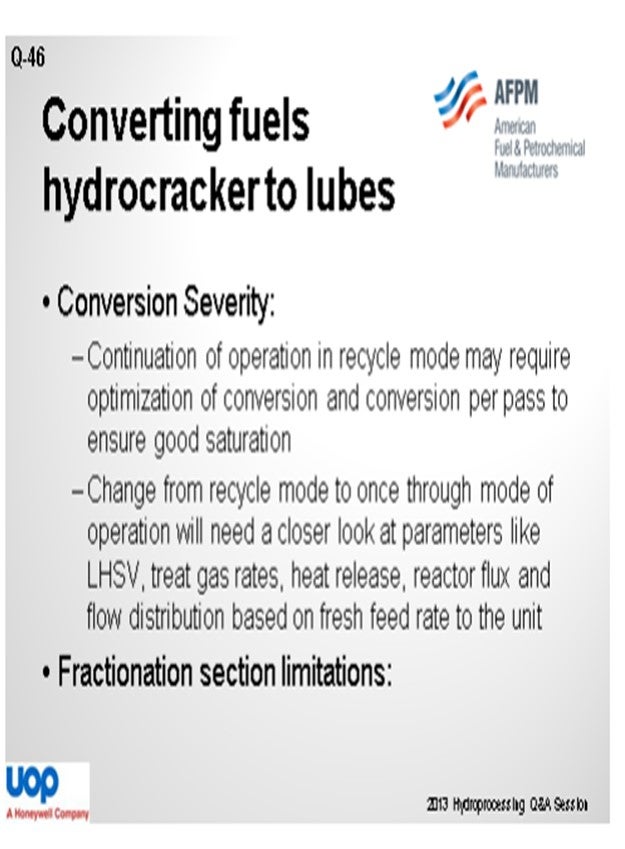
GATES (Motiva Enterprises LLC)
If you are considering converting your hydrocracker to a lube's unit, the engineering concerns are going to be very unit dependent. In general, you will be processing heavier feeds in the lube service, so you will need to be concerned about waxing, separation problems, and instrumentation concerns, for example. The potential issues will be throughout the unit, so you will want to evaluate the pre-heat section, reactor, and catalyst choice, as well as separation and distillation. All of those areas must be carefully evaluated. Again, our recommendation is to make sure you have a detailed discussion with your unit licensor when you evaluate such a unit change.
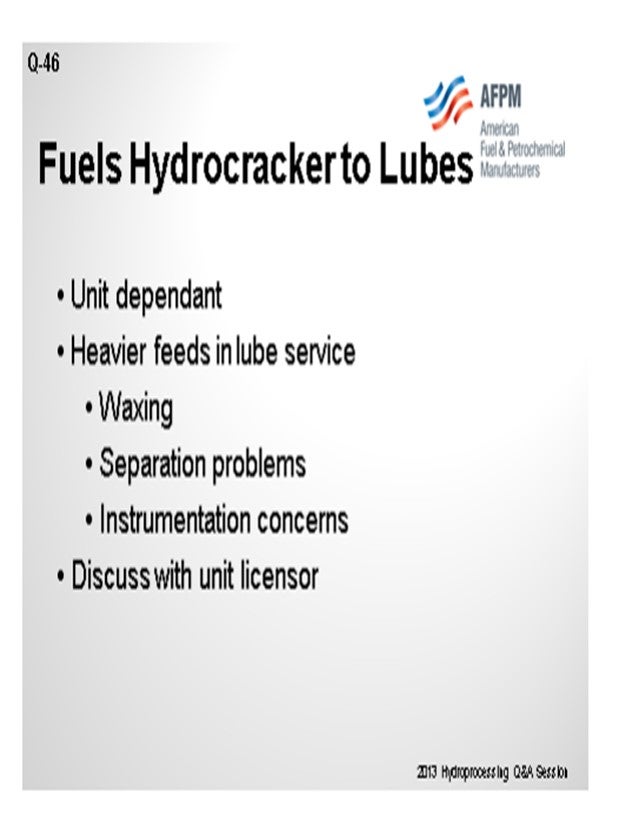
RAJESH SIVADSAN (UOP LLC, A Honeywell Company)
Conversion of a fuel HC to lube HC depends upon the product quality requirements and unit constraints. If the desire is to make lube base stock as a main product, then a closer look at all the operating parameter is required. On the other hand, if co-production of lube base stocks with high quality distillate fuel is required, then the fuel quality requirement may control the operating conditions.
• Feed quality and distillation range become critical for lube base stock production. Feed needs to be heavy enough to produce desired viscosity lube base stock product. It is desirable to limit any cracked stock and/or to eliminate highly aromatic streams like lube extract or heavy cycle oil (HCO) in the feed blend.
• For making high quality Group III type lube base stocks, high hydrogen partial pressure is desired, and evaluation of the unit hydrogen partial pressure may be required.
• Catalyst type also plays an important role in lube base stock production. Distillate selective catalysts tend to be good lube base stock catalysts, although a switch to a catalyst with high hydrogenation capability for unconverted oil (UCO) is desired.
• Conversion severity also plays a role in the degree of hydrogenation and the viscosity of the UCO. Conversion needs to be in line with pressure, LHSV, and catalyst selection.
• If the unit is designed for the recycle mode of operation with high conversion to fuels and the new objective is to maximize lube base stock production, then the operation needs to be optimized by dropping and optimizing the conversion per pass to ensure that conditions are suitable for good saturation.
• If the unit is designed for recycle mode of operation and it is converted to a once-through mode of operation to produce lube base stocks, then different considerations may apply, depending on the feed rate to the unit. If the fresh feed rate is maintained the same as the previous case, the reactor flux and flow distribution need to be looked into at the overall lower charge rate to the reactor. If on the other hand, the fresh feed rate is increased to match the hydraulic capacity of the unit and to produce similar quantities for fuels, then parameters like LHSV, treat gas rates, and heat release need to be looked into critically.
• UCO for lubes will most likely go to catalytic dewaxing/hydro isomerization downstream, which may be sensitive to sulfur and nitrogen content. The choice of pre-treat, HC catalyst, and the process conditions need to be capable of producing high VI, low S/N UCO required for the downstream unit.
• The fractionation section needs to be evaluated to make sure it can handle the changes in flow rates of different streams and increased UCO rate.