Question 46: Are refiners modifying the operating conditions in reforming units, for example, chloride on catalyst, in order to capture margin differences between natural gas, used as fuel, and liquid products?
KOONTZ (HollyFrontier)
I will start with a bit of review of some reactions, and then I will get into a couple of examples of what we have done at HollyFrontier. Of course, the downside to reforming is that the liquid product has less volume than the feed to the unit due to physical laws inherent to the chemical reactions. First, the high-octane product will have a higher density than the feed; and second, some portion of the feed will be cracked to LPGs and fuel gas in the process.
There are three main classes of reactions in the reformer: dehydrogenation, dehydrocyclization, and isomerization. An example of dehydrogenation is the conversion of methylcyclohexane to toluene. The octane is increased by 46, but the downside is that the liquid volume decreases about 17%. This reaction happens very quickly in the reformer.
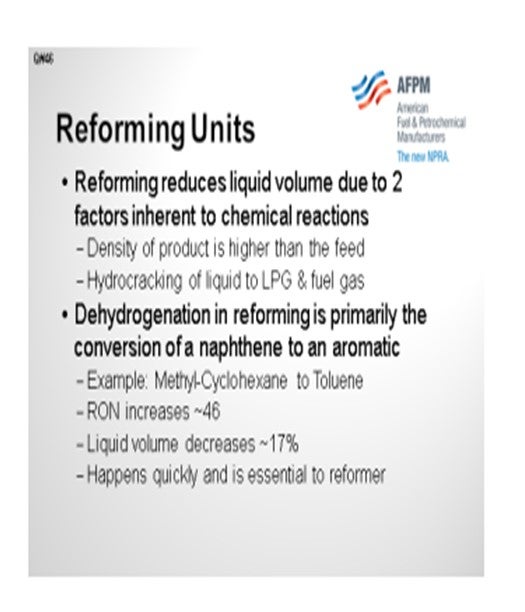
The second main reaction is dehydrocyclization, which is the process of a paraffin going to a naphthene and then ultimately to an aromatic. The example shows normal heptane (n-heptane) going to toluene, which has a large octane increase of 120. However, it also has a massive liquid volume decrease of 27%. A few refiners might be tempted to try to avoid this reaction; but unfortunately, it is necessary because you cannot really get the octane of a straight-run naphtha much above about 70 (R+M)/2 without this reaction.
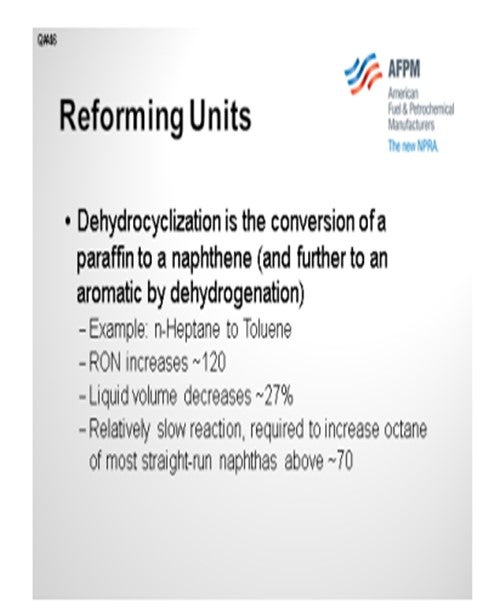
The third major reaction is isomerization, which is the process of changing the carbon structure of the molecule. The example shows normal hexane going to 2,2-dimethylbutane. The octane increase is about 67. The beauty of this reaction is that the liquid volume is essentially unchanged. So, in many respects, this is the preferred reaction. Of course, not all isomerizations have this big of an octane improvement.
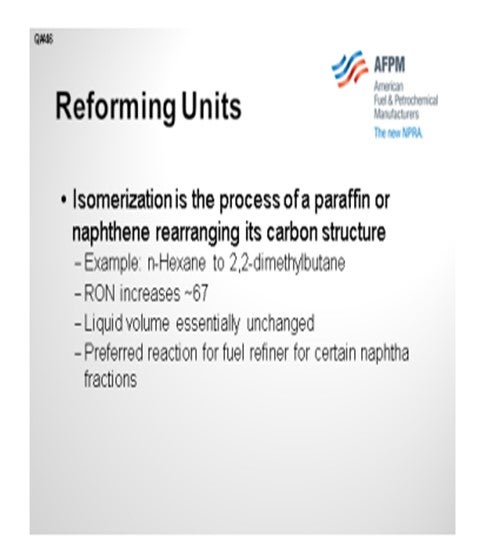
Finally, hydrocracking is generally undesired in a reformer. The example on the slide shows normal hexane going to two propane molecules. In this case, the liquid volume has increased significantly; however, the value of the propane is dramatically less than the value of the gasoline that it was when it started. Of course, that is even more so the case today with the high price of crude relative to natural gas.
So specifically, HollyFrontier has several older semi-regen reformers that operate at relatively high pressures to reduce the coking with the goal of achieving an acceptable run-length between regenerations. The reality of the current large differential between crude and natural gas has forced HF to look hard at the operation of these reformers. The price differential between crude and natural gas always drives us to minimize the severity of octane of these reformers, but
we also have to deal with our day-to-day constraints. The price differential would tend to push us to regenerate more quickly, but that is often not advantageous. The reason is that the outage time, due to the additional regeneration, is usually not enough to make up for the higher liquid yield.
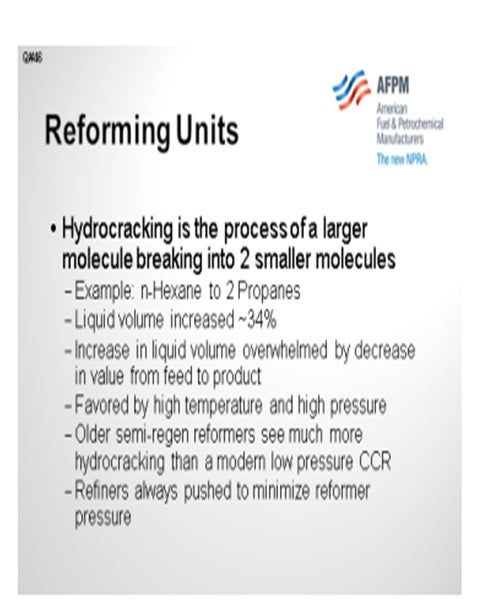
As mentioned earlier, being able to produce E10 gasoline is, of course, of benefit for lowering severity. This is especially valuable for a high-pressure reformer. Some refiners separate aromatics for sale as chemicals. At one of the HollyFrontier sites, we deal with the particular process of extracting benzene. We have reviewed this quite a bit. For example, the conversion of normal hexane or methylcyclopentane to benzene results in a liquid volume
reduction of 32% or 21%, respectively. Initially, you see that that benzene has a much higher price than gasoline, but its higher price is almost wiped away when you consider the reduction in volume that you get for making it.
An alternative for some refiners might be to isomerize that C6 portion of the gasoline, instead of trying to make it into benzene, and then recover the benzene. We are evaluating this option at one of our sites. Of course, I want to mention that C5s should always be routed away from a reformer because they have no chance of making an aromatic. Unfortunately, they do have a good chance of cracking, especially in a high-pressure unit. C5s should generally be directed to an isomerization unit.
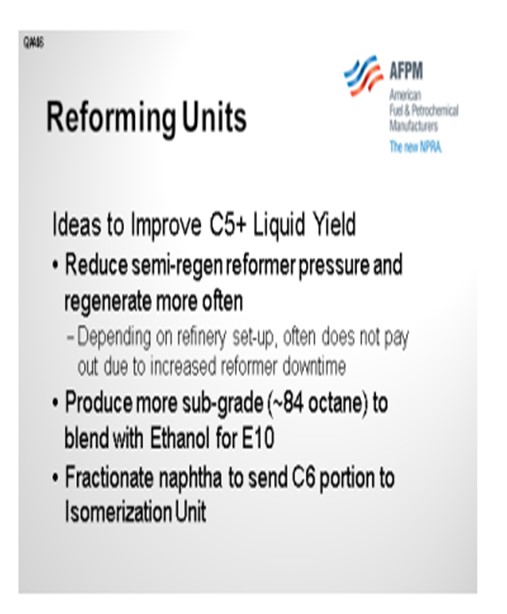
At one of our units, we have occasionally reduced the feed rate to a semi-regen reformer, which allows us to significantly increase the volume yield of the overall refinery. At our El Dorado plant, we have taken advantage of the lower feed rate by lowering the pressure on this particular reformer by about 75 psi. As a result, we see our liquid volume yield go up by approximately one percent. The unit does not have a net gas compressor. In order to lower the
pressure, the net gas must be compressed through the recycle compressor to “get into” the hydrogen header. Since the feed rates are reduced, the hydrogen-hydrocarbon ratio stays about the same for the lower recycle gas rate.
At another plant that also has a fairly high pressure semi-regen reactor, we have a unit with a compressor between the low-pressure separator and the high-pressure separator. This unit was designed to take the net gas off of the high-pressure separator. However, excess hydrotreater
makeup compression at downstream units now allows the net gas to be taken from the low-pressure separator. This yields a larger hydrogen-hydrocarbon ratio because the recycle compressor does not have to process that net gas, so the pressure in the unit is run a little bit lower. Of course, this depends on being able to have a compressor downstream that can handle lower pressure net gas. One downside is that the net gas purity is lower since it came from the
lower pressure separator.
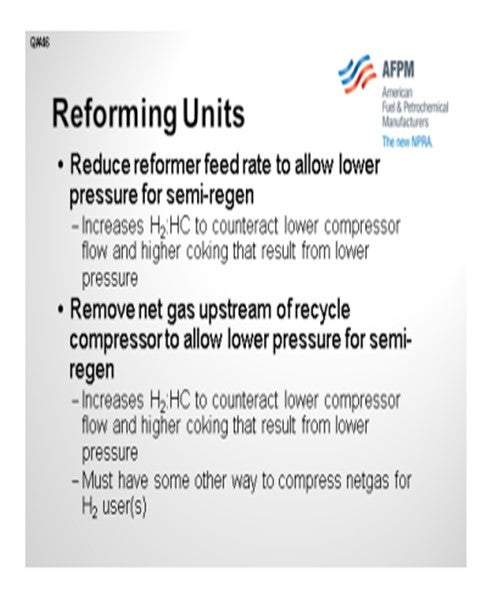
The original question asked about chloride on the catalyst. HollyFrontier has not attempted to modify the chloride on catalyst, so I do not have any comment about that scenario.
MUEHLBAUER (Valero Energy Corporation – Benicia Refinery)
Similar to what Mark just said, we believe that operating the reformer is all about meeting the octane pool demand while maximizing the liquid volume yield. That has been the same strategy we have used regardless of natural gas prices changes. It has always been the most economic strategy. The exception is that if the refinery is hydrogen-limited, then you will have to factor the hydrogen economics into that decision as well. But more specifically to the chloride on
catalyst, we have actually found that the chloride drives the acid function on the catalyst in the ring-closing reactions.
Reducing the amount of chloride on catalyst can directionally improve liquid volume yield. In some cases, we have under-chlorided up to about 10% of the manufacturer’s base recommendations. We have done that in about a third of our reformers. On the other two-thirds, we actually operate about 5% lower than the recommendations. Some units operate the last reactor above the manufacturer-recommended chloride levels because we are heater-limited in those particular units. So, if you do not have the furnace, then the chloride will help you.
Even at the 10% level, these changes are very subtle: no more than up to 0.3 vol%. Therefore, it is directionally helpful. If you go too far, you could get catalyst agglomeration issues. We found that it is advisable to calibrate your local lab with either the licenser’s lab or some standard lab that you trust, just to be able to see some of these changes.
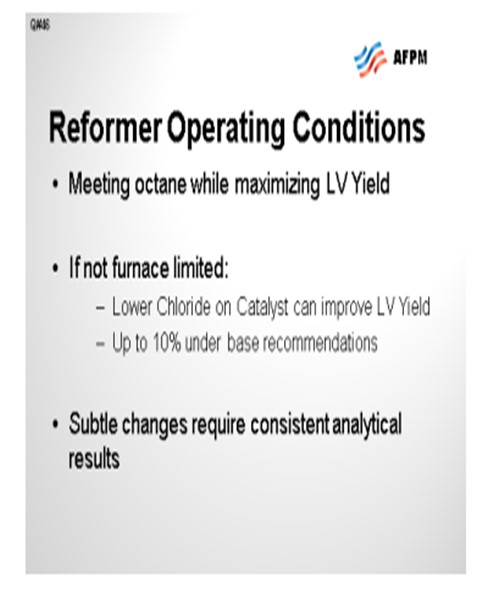
KOONTZ (HollyFrontier Corporation)
Naphtha reformers are critical units for U.S. refiners to increase the octane of straight-run naphtha for gasoline blending and to produce GT-BTX® for the chemical industry. However, the downside of reforming is that the product C5+ liquid volume is significantly lower than that of the feed. This results from two consequences inherent to the chemical reactions. The high-octane product is higher density than the feed, and some of the feed is cracked to LPG and fuel gas.
There are three main classes of reactions that increase the octane of the product: dehydrogenation, dehydrocyclization, and isomerization. Dehydrogenation is primarily the process of a naphthene producing an aromatic and hydrogen. As an example, methylcyclohexane could be converted to toluene and hydrogen. This process would increase the RON (research octane number) of the MCH (methylcyclohexane) by ~46, but it would also reduce its liquid volume by ~17%. This reaction happens quickly and is primarily catalyzed by the metal function of the catalyst.
Dehydrocylization is the process during which a paraffin produces a naphthene and hydrogen. The naphthene will generally proceed to an aromatic via dehydrogenation. As an example, n-heptane could be converted to toluene and hydrogen. This process would increase the RON of the nC7 (normal heptane) by ~120, but it would also reduce its liquid volume by ~27%. This reaction is the slowest of the primary reactions in a reformer. The ring-forming is primarily
catalyzed by the acid function of the catalyst and the dehydrogenation is due to the metal function. It results in a large reduction of liquid volume; but without it, the octane of a typical full-range naphtha can get no higher than 60 to 70.
Isomerization is the process of a paraffin or a naphthene rearranging its carbon structure; for example, n-hexane (normal hexane; nC6) could be converted to 2,2-dimethylbutane. This process would increase the RON of nC6 by ~67 with essentially no change in liquid volume. The reaction rate falls somewhere between dehydrogenation and dehydrocyclization and is primarily catalyzed by the acid function of the catalyst. For a fuel refiner this is generally the ideal
reaction; however, most other isomerizations do not result in such a large RON improvement.
Hydrocracking is the fourth main class of reactions in a reformer and is generally undesired. As an example, n-hexane plus hydrogen could be converted to two propane molecules. The reaction is favored by high temperature and high pressure and is primarily catalyzed by the acid function of the catalyst. This process would increase the liquid volume by ~34%, but the value of propane is tied more closely to that of natural gas than to crude oil. With
the price of crude near historical highs and the price of natural gas near historical lows, the volume increase is nowhere near enough to make up for the decrease in value.
Older semi-regeneration reformers were designed for higher pressures to reduce coking and enable the unit to run for an acceptable time between outages to regenerate. The impact of the large differential between crude and natural gas more greatly affects a reformer operating at
higher reactor pressures due to increased hydrocracking. This would generally drive the daily optimization to minimize reformer octane (i.e., severity or temperature). It would also push a refiner to regenerate catalyst in semi-regeneration reformers more often to avoid the EOR (end-of-run) conditions when reformer temperatures and hydrocracking are higher. However, the increased yield from the regeneration must be balanced with the lost opportunity due to the outage.
Producing sub-grade gasoline for blending with 10% ethanol can be a significant benefit for a refiner having a reformer with low liquid product yield. The lower octane of the sub-grade (~3 points lower) allows the refiner to run the reformer at lower severity or bypass sweet naphtha around the reformer directly to gasoline.
Some refiners separate aromatics from the reformate for sale to the chemical industry. One particular aromatic that HF (Editor’s note: HF stands for HollyFrontier in this response) has evaluated is benzene. The conversion of n-hexane or methylcyclopentane to benzene results in a liquid volume reduction of 32% or 21% respectively. The increased price of benzene over gasoline primarily reflects this reality. An alternative for a refiner would be to send the C6
portion of the naphtha to an isomerization unit to avoid the volume loss inherent to a reformer.
C5s should always be routed away from a reformer and generally to an isomerization unit. C5s will not form an aromatic, but they could hydrocrack to LPG and fuel gas in a reformer (especially in a high-pressure unit).
Reformer yield can be improved by lowering the feed rate, especially for a semi-regenerator. Reducing the feed rate can be accomplished by fractionation to route light naphtha to isomerization and heavy naphtha to distillate, or via the crude slate to reduce the total straight-run naphtha. The HF ElD (Holly Frontier, El Dorado, KS) reformer takes advantage of this at times and lowers the reactor pressure by as much as 75 psi. This increases the product C5+ liquid
yield by as much as 1 LV%. The unit does not have a net gas compressor due to the high separator pressure. At low rates the pressure is reduced and the recycle compressor also compresses the net gas (lowers recycle rate). However, due to the lower feed rate, the H2: HC
ratio and coking rate both remain about the same.
HF Cheyenne has reduced its semi-regeneration reactor pressure in a different way. The unit has a low pressure and a high-pressure separator with a compressor in between. The unit was designed to take the net gas off of the HPS (high pressure separator). However, excess hydrotreater makeup compression allows net gas to be taken from the LPS (low pressure separator) and yields a larger H2: HC ratio. The reactor pressure can now be run lower (higher liquid yield) and achieve the same coking rate due to the higher H2: HC. One downside is that the net gas is lower purity having originated from the LPS.
HF has not attempted to modify the chloride on catalyst in its reformers to alter the acid function of the catalyst. It is recommended that you consult your catalyst supplier before attempting a change such as this.
SUBHASH SINGHAL (Kuwait National Petroleum Company)
Chloride on catalyst is maintained at a desired level (1 wt% to 1.2 wt %) for optimized catalyst performance and to ensure that balance of metal and acid activity. At KNPC, we never alter chloride on catalyst to shift yields to gas/LPG.