Question 45: What is the maximum allowable limit for the iron content of a reforming catalyst? Is this limit the same for semi-regenerative and continuously-regenerative catalysts?
DUBIN (Axens North America)
We have seen that the maximum allowable iron on catalyst cannot be reduced to a simple number. Historically, about 3,000 wppm is the level at which we see yield start to suffer, but not every wppm of iron has the same impact on the unit. Iron deposited on the surface of the catalyst, usually from corrosion-related byproducts, tends to have less of an impact on the overall performance. Some units have tolerated quite a high level of iron as long as the iron stayed on the surface of the catalyst bead. However, if the iron is able to migrate into the center of the catalyst bead, then the quantity needed to hurt yields could be much less than the 3,000 wppm I noted earlier.
As the iron migrates, we see the larger iron species hindering redispersion during regeneration. The yield penalty seen from this loss of redispersion mirrors that of a decreased metallic function for a given octane. Higher inlet temperatures are needed to meet a given octane, and subsequent loss of reformate is observed.
This slide shows a microprobe analysis of catalyst moving inward from the outer surface of the catalyst. You can see that the alumina is distributed uniformly throughout the catalyst particle. The iron concentrates on the outer surface of the bead, but we see that very little of it has migrated to the core. Under what we would consider low chlorine conditions, or sufficiently moist conditions, the migration of iron is mitigated. However, under higher chlorine content or drier reaction zones, the iron movement can increase and migrate into the center of the bead, leading to reduced yields. We consider a high chlorine environment to be 1.2 wt% to 1.3 wt% chloride on catalyst and dry being less than 10 wppm moisture in the recycle gas. Note that moisture tends to inhibit the migration of iron into the center of the bead.
Getting to the second aspect of the question about the allowable limit of iron on catalyst, we use the same limit on iron for fixed-bed and moving-bed reactors; however, the impact is not quite the same. For moving-bed reactors, the iron is distributed evenly across the catalyst due to the nature of the catalyst circulation, whereas in fixed-beds units, all of the iron deposit is in the first reactor. If the first reactor catalyst is sufficiently poisoned, the reforming reactions will move into the second reactor, and so on. However, it is difficult to play catch-up with the reforming reactions due to the endothermic nature of the reaction. Long term, it is hard to catch up on octane with a poisoned first reactor. For cyclic units, we have seen that the poisoning of the first reactor is essentially the same as a fixed-bed unit. However, with the swing reactor present, you have the ability to change out the first reactor catalyst if the catalyst underperforms
for whatever reason.
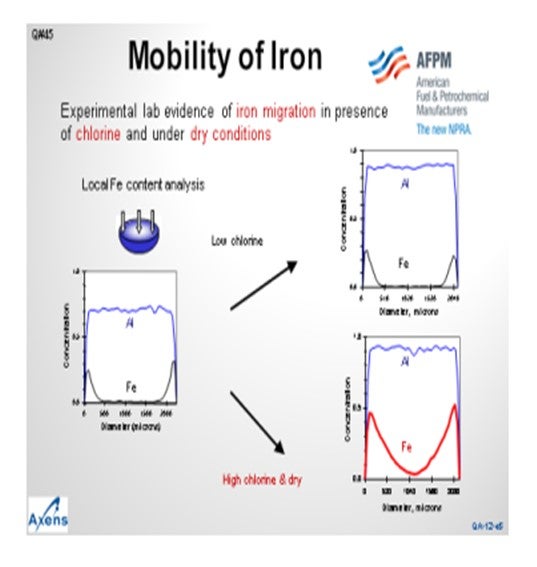
PIZZINI (Phillips 66)
It is really just a practical consideration regarding iron. We had a semi-regen unit that had to shut down, drop screen, and reload the first reactor without the benefit of a coke burn. We had removed most of the catalyst and were down to just the dust and fines. We then experienced a dust collector event on the vacuum truck. The dust contained pyrophoric iron since it had not been through a burn. In this case, the vacuum truck was set up with a nitrogen purge. However, the investigation showed that the truck did not have enough nitrogen purge. So just keep in mind that the iron can be pyrophoric, even on a reformer.
PATRICK BULLEN (UOP, A Honeywell Company)
UOP agrees with Axens that the situation is complicated.
DUBIN (Axens North America)
The maximum allowable iron content on catalyst cannot be reduced to a simple number. Historically, we have seen that at approximately 3,000 wppm, the impact on yields from iron starts to become significant. However, every ppm of iron on the catalyst is not equal in its effect on the unit. Often, iron that has deposited on the surface of the catalyst, typically from corrosion-related byproducts, has a limited impact on the overall performance of the catalyst. In several
instances, we have seen that the catalyst was able to tolerate high levels of iron while still performing at or near the expected level of conversion.
The quantity of iron needed to cause deterioration in the performance in certain circumstances can be well less than the 3,000 wppm mentioned earlier if the iron migrates to center of the bead from the outer surface. We have experience with a client who saw a decrease in performance at a lower content of iron on the catalyst. However, a significant portion of the iron in this situation had migrated to the center of the bead. As the iron migrates to the center of
the bead, platinum becomes less accessible as the larger iron molecules – e.g., FeS (iron sulfide)– plug the pores of the catalyst. The yield penalty observed during an iron poisoning situation mirror that of loss of metallic function. Higher average bed inlet temperatures would be required to compensate for the lost metallic function leading to decreased C5+ yields.
In Axens’ view, the iron contamination limit for semi-regeneration and continuously regenerative catalyst are the same, but the long-term operation with high iron catalyst is not. As the iron in the feed is distributed across the continuously regenerated catalyst evenly, the impact can be lessened or even delayed due to the catalyst circulation. For a semi-regeneration unit, the sulfur will accumulate on the first bed, potentially killing the activity of the first bed before the iron would theoretically migrate to the second bed; ‘theoretically’, because not many refiners would be able to maintain reformate production at an acceptable level with the long-term poisoning of the first reactor. Even moderate poisoning of the first bed in a semi-regeneration unit is a concern as it is unrealistic that a refiner can play ‘catch-up’ in subsequent reactors to meet the desired conversion due to the nature of the reforming reactions. Cyclic operations suffer from the same overall concerns as a semi-regeneration unit, but with a swing reactor present, the unit has the ability to replace catalyst on the fly when the yield penalty from poisoning is no longer acceptable.
PIZZINI (Phillips 66)
P66 also experienced a catalyst unloading issue related to pyrophoric iron on a lead reactor which had to be dropped and screened in an unburned condition. The presence of iron led to a vacuum truck dust collector event when vacuuming fines from the lead reactor. This was found to be the result of insufficient N2 purge on the vacuum truck.