Question 45: What criteria and requirements that you use to determine mixing equipment for crude tankage? How do you map the sludge level? What methods do you use for sludge removal to shorten time to clean the tank?
MAJI (Essar Oil Limited)
Question 45 is actually a combination of three questions. The central issue here is the sludge. There are many purposes of using crude tank mixtures, many of which are listed on the slide. The purpose of the crude tank mixer might be for homogenization–in terms of density, viscosity, or temperature–or its purpose may be to control BS&W to reduce or eliminate sludge or the blending of crudes. We do blend crudes for processing. All 12 of our crude tanks are fitted with either jet mixers or side-entry propeller mixers. The tanks, which are fitted with jet mixtures, have been in operation for last 10 years. So far, we have not faced any operational constraints due to sludge formation; so, we believe that jet mixtures are doing a good job. BS&W and sludge control is our main purpose of the mixtures.
Side-entry mixtures are also doing an equally good job. In our tank, we have six numbers swivel angle side-entry mixtures which are mainly to control BS&W. The specific gravity and viscosities of crudes that we handle vary widely from a very light crude to a very heavy crude. Our tank diameters are quite large: 92 meters, which is about 300 feet. We do have occasional problems in controlling BS&W with both types of mixtures. The jet mixtures require a little more power than the side-entry mixtures.
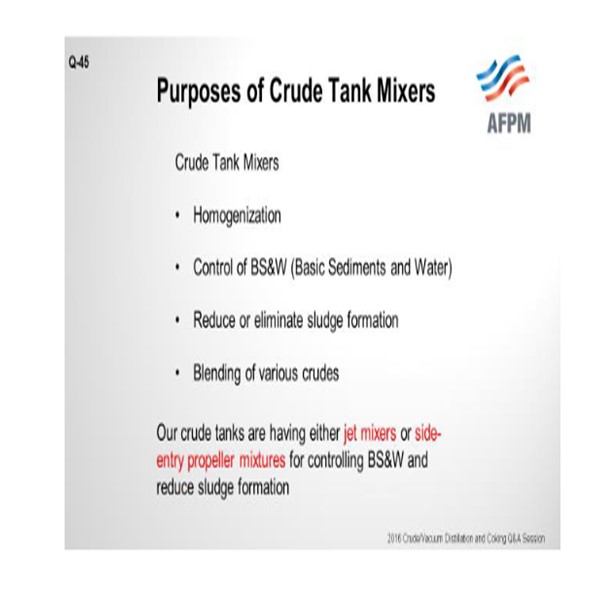
Since sludge formation cannot be totally eliminated, a Best Practice would be to periodically map the sludge as part of the Operations process, as well as part of the Scheduling & Maintenance plan. There are three main ways the sludge level can be mapped. Manual probing is the weighted-gauge method. It is very simple; so obviously, its accuracy is not that good. The second way is acoustic profiling because it gives a very accurate measurement of the sludge, but it is a very costly method. Thermography is a type of infrared imaging that can be used for uninsulated tanks. By circumferentially scanning the tank from the outside by using a thermal imaging camera, it is possible to determine the layer between the sludge and the oil. With that method, we are estimating the sludge volume. We have carried out both the manual method and infrared thermography. Infrared thermography shows a little higher amount of sludge compared to the manual method.
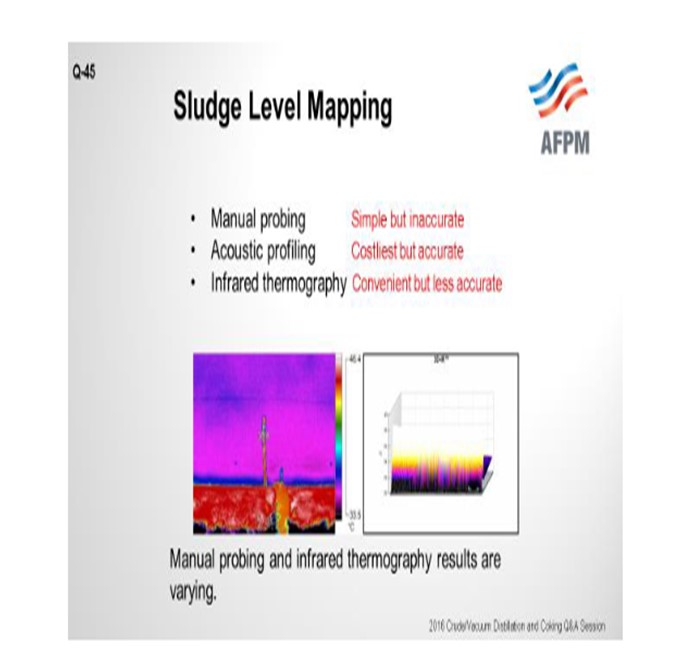
Regarding tank sludge removal, we normally use one of the three methods. The first is very conventional. We reduce the volume of the tank content so much that the tank legs will be resting on the bottom plate. Then, we will take some diesel-type material and circulate it while keeping our steam coils on. This step basically melts the waxes and dissolves the asphaltenes. Next, we drain it out. We repeat this operation quite a number of times until our sludge volume comes down. The sludge is then dislodged with the water jet, taken out from the cleanout doors, and centrifuged to less than 10% oil content for disposal. This method is very cheap and very simple, but it takes four to five months for an 80-meter (260 feet) diameter tank. This conventional method has been improvised by using a powerful vacuum track for taking out the sludge from the tank floor. This modification has reduced the time requirement from four months to two months.
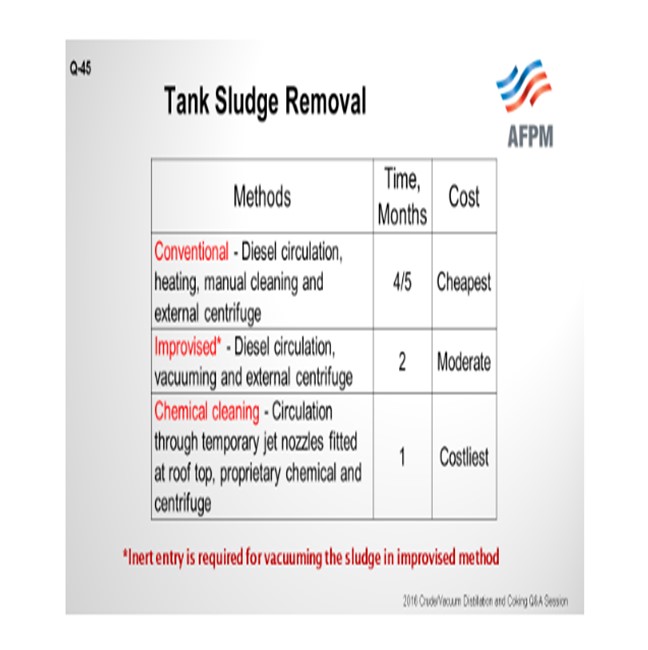
I would like to mention one safety aspect here. Once we are reclaiming the sludge from the tank, inert-entry will be required to eliminate pyrophoric-related issues. A further 50% deduction in time is being claimed by a vendor. We are in discussion with them, and they are to fix multiple nozzles on the rooftop. Then based on the sludge analysis, they will use a proprietary chemical. to Circulation will then be established using diesel, which will be heated by using a steam-heat exchanger. We are supposed to extract 95% of oil from the sludge. The time estimate of one month is really challenging for cleaning an 80-meter diameter tank. So, if we are successful, that will be a benchmark for India.
BASS (HollyFrontier Corporation)
For crude tank mixing, we generally rely on propeller mixers on crude tanks. While they are not perfect, it has been adequate for us. Typically, our tanks are notof the size of the tanks Maji discussed. Since ours are smaller, propeller mixers have been adequate in most situations. As far as sludge production, HollyFrontier has not had many issues with sludge generation being rapid enough for us to need to map the sludge on a regular basis. The tank inspection frequency typically drives the timing of our tank outages, not our sludge accumulation. Most of HollyFrontier refineries have multiple crude tanks to allow for tankage to be taken offline to clean without major interruption of supply.To maintain sufficient operational flexibility with the desired crude blends, we will do some pre-blending upstream. In some instances, we will run with lower feed inventory for a short period of time to allow for tank cleaning.While we do that, shortening the tank outage duration is still desired; so, what we have done is cut the sludge with a diesel stream such as LCO (light cycle oil) and then centrifuge directly from the tank in question. We have used some portable tanks to pump the sludge oil mixture out of the tank to allow centrifuge at an offline period to shorten the downtime of the tank.
SAMUEL LORDO (NALCO Champion) The most common mapping method is manual thief samples from the top of the tank. We have a proprietary method called the Hot Water Circulation Method. The technology we use is well proven, effective, and recovers the oil in the sludge for safe processing. It uses chemistry which generally allows us to clean crude tanks, almost regardless of the size, within20 to 30 days. The resulting solids are almost hydrocarbon-free. The amount of hydrocarbon you recover actually ends up paying for the job. Some customers have actually made money off of cleaning their crude tanks. Alternative methods I have seen include thermal imaging and radar/sonar. The mapping with a thief has the advantage as it can also collect sample of the sludge.