Question 44: What are your Best Practices for co-processing streams in hydrotreating units?
WRIGHT (Hunt Refining Company)
I am going to approach this excluding renewable fuels because Scott will talk about that. In our refinery, we co-process in three hydrotreaters. The first one is our hydrocracker where we do both straight-run and coker gas oil. What we watch for there are changes in the feed composition due to the cyclical nature of the coker and the affects that we see in the hydrocracker reactor in the fractionation section because of that.
Our second one is our diesel hydrotreater wherein we process straight-run diesel. Besides coker gas oil, it is also a big consumer of cracked naphtha for us and also straight-run kero. If we are charging a lot of light material in the front end, then we will typically observe some backend fractionation limitations; that is, they are not able to get all of the light ends out the back side. On the naphtha hydrotreater, we have one where we process both straight-run and coker naphtha, and we run into reactor ΔT issues due to the olefin exotherms that we have to keep an eye on.
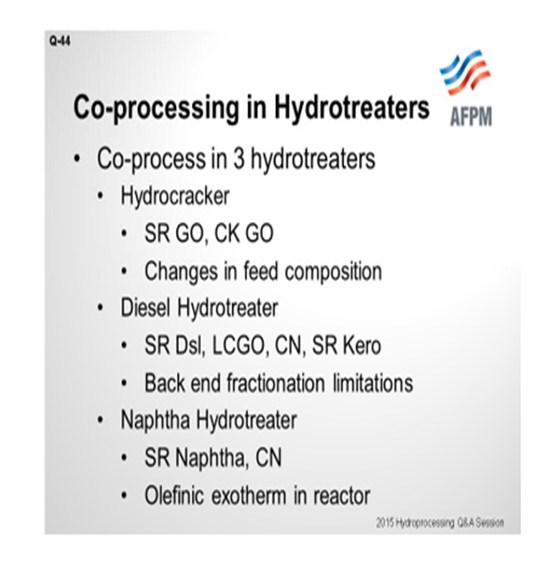
TEMME (Albemarle Corporation)
Looking at the question, there is some inference that it was co-processing of coker naphtha or biofuel in, say, a ULSD unit. So, in order to save time, I am going to skip to the last point saying that a higher pressure/higher hydrogen availability is going to have a little more capability to deal with these streams effectively, whereas lower hydrogen partial pressure/lower hydrogen availability streams might be a little more stressed. So, the higher hydrogen partial pressure unit, even though with a little a downgrade, in terms of the resulting hydrogen reduction or hydrogen partial reduction, is still more capable.
The one watch-out we would advise is to ensure that when co-processing these cracked feed or biofuel materials, the resulting operating conditions do not present problems in Bed 1, in terms of its capability and stability. So if you see too high of an exotherm develop, that is an indication of very high hydrogen consumption, which can lead to localized hydrogen starvation. With this operating condition, the resulting problems of potential gumming, polymerization, coking, and amount potential of worse gas/liquid distribution can occur.
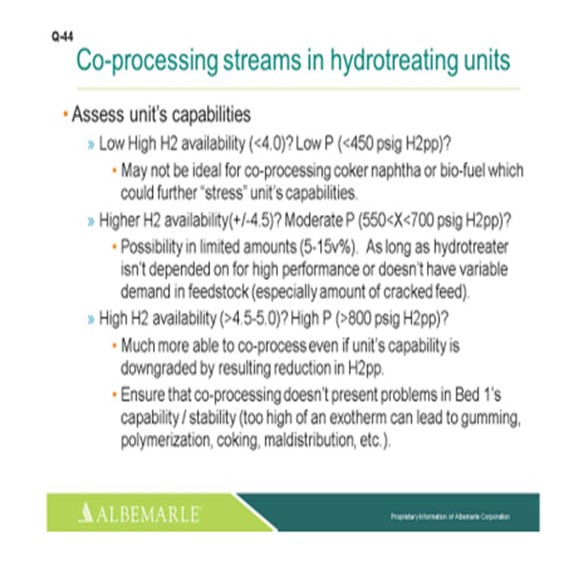
McARTHUR (Phillips 66)
Phillips 66 has some experience with co-processing renewables in a couple of our refineries for distillate production. Feedstocks contain compounds which lead to higher than typical CO2 as a byproduct. CO2 will result in carboxylic acid formation downstream when reactor effluent cools off. In addition, the ammonium carbonate salts will precipitate and lead to corrosion issues. So renewables co-processing requires consideration of impacts not just to the product qualities in a hydrogen consumption, but also on metallurgy constraints within the unit, as well as washwater practices.
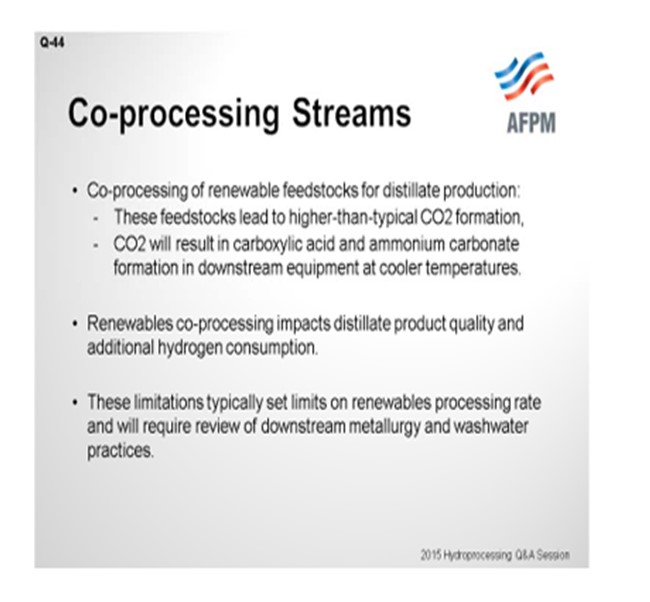
PETER BENDTSEN (Haldor Topsoe, Inc.)
Co-processing of fossil-derived hydrocarbon streams in a hydrotreater provide some inherent benefits in terms of requiring little or no additional processing equipment (lower CAPEX) and often with the option of being able to process more barrels of crude while using the existing refinery setup. However, while co-processing streams may help overall refinery processing capacity and economics, it may, at the same time, add complexity and concerns to the individual hydrotreating unit. In a co-processing scheme, there are often a number of potential issues and concerns to consider. Typically when co-processing, a lighter stream is added as an additional stream/feed component into a heavier feed hydrotreater. This can be naphtha boiling material being added into diesel or VGO hydrotreaters or diesel added into VGO hydrotreating unit.
We have seen cases where the coker naphtha has had to be routed to various hydrotreating units in trying to operate the coker unit at full capacity. As examples, we have seen coker naphtha added to all types of hydroprocessing units ranging from ULSD, FCC pretreatment, and as feed or quench to hydrocrackers.
Co-Processing in Hydrotreaters – Adding Naphtha: One of the inherent issues with most coker naphtha is the fact that it contains silicon. The silicon is added to control foaming in the coker drums and is a well-known catalyst poison. Therefore, when routing coker naphtha to a hydrotreating unit, silicon poisoning of the main bed catalysts now becomes a major concern (depending on concentration in total feed) and silicon guard catalysts are required for the catalyst load which ‘steals’ active main bed catalyst volume. In addition, the coker naphtha turns to vapor at the unit operating temperature and effectively lowers the hydrogen partial pressure in the given service. The lower hydrogen partial pressure directionally impairs the catalyst system performance and stability.
Another caveat from adding coker naphtha is the fouling potential of the system (preheat and catalyst bed) in that the coker naphtha contains very reactive diolefins and olefins resulting in early pressure drop concerns. Also, with the very reactive diolefins and olefins in the feed mix, good temperature control becomes a key element to consider through catalyst loading and operational strategy for the hydroprocessing unit.
Hence, adding coker naphtha to a specific hydrotreating unit may be profitable, but there are a number of potential issues that need to be considered. These potential issues can be resolved via changes to the operating guidelines and the use of a tailor-made catalyst loads.
Co-Processing in Hydrotreaters – Adding Diesel: In the case of co-processing diesel and gas oil, cross-contamination of the final product is a concern. For instance, color specification for ULSD becomes of significant concern. There are concerns when gas oil is blended into the diesel, as this may limit a hydrotreating unit to a lower operating temperature due to aforementioned ULSD product color concerns.
Co-Processing in Hydrocrackers: When adding coker naphtha or LCO to a hydrocracker, the same issues mentioned above may be raised, but it can also add complications as to the selectivity of the hydrocracking catalyst system.
General Considerations: One of the drawbacks in adding coker naphtha to a heavier service is that it is important to have sufficient fractionation capacity. Energy efficiency can also be a concern. Initially, the coker naphtha needs to be split from the total coker product; but then, it is blended into a heavier medium for the co-processing. And again, this stream will have to undergo additional fractionation to separate the products.
Another area of concern should be the product quality requirements when co-processing. No matter if a unit is taking the combined distillate output from the distillation tower or if the coker naphtha is added to a heavier service, it can be difficult to obtain all of the individual product stream quality specifications.
Generally speaking, co-processing fossil-derived streams in hydrotreating units require a thorough check of the existing catalyst loading/functionality and downstream equipment. The amount of gas/vapor in the loop may shift significantly; hence, a fit-for-purpose check may be required for all separators, piping, stripper, and/or fractionator section. In addition, it is recommended to do a heat balance check on the unit to make sure the co-processing scheme is viable.
As can be understood from above, there are a number of considerations and concerns that need to be addressed before endeavoring into a co-processing mode operation. Haldor Topsoe, Inc. has vast experience in the above and will be able to assisting in such evaluations. In addition, Haldor Topsoe, Inc. has vast experience in co-processing of renewable fuels, which introduces a large number of additional issues that have been discussed in previous Q&A sessions.
AMIT KELKAR (Criterion Catalysts & Technologies)
Many different combinations of co-processing of streams is practiced in the industry. A number of factors need to be considered when co-processing different streams:
1. Cracked feeds – such as LCGO (light coker gas oil), HCGO (heavy coker gas oil), and LCO – are high in olefins and aromatics and result in high top bed delta T and increased H2 consumption. Recycle and makeup compressors should have enough capacity to handle new conditions.
2. Diesel range material is often processed in a FCC PT unit; backend fractionation has to be able to remove diesel from bottoms FCC feed if you want to recover the diesel from the feed to the FCC.
3. Coker naphtha is co-processed in ULSD and FCC PT units, and the unit needs to have the flexibility to handle the higher top bed ∆T. In fact, many units process 5 to 10% coker naphtha in the feed, especially at EOR to provide additional exotherm when the heater is maxed out. In addition, the impact of Si contamination may require some silicon trap material, if processing coker naphtha routinely. The olefins in the coker naphtha can be a concern for increased pressure drop (from polymerization of olefins), especially if diolefins are present in the coker naphtha. Many units process small amounts of coker naphtha (e.g., 5% of total feed rate is coker naphtha) routinely without difficulty.
4. In addition, coker-derived streams and LCO often have high nitrogen, so washwater capacity and REAC (reactor effluent air cooler) metallurgy needs to be evaluated to ensure safe operation for higher NH4HS (ammonium bisulfide) concentration.
In addition, some units successfully practice co-processing in blocked operation. Consideration here on minimizing the cuff when switching between feeds is typically the primary concern.
Co-processing can also refer to inclusion of renewable feedstocks, i.e., vegetable oil and animal fats, which can be co-processed with traditional diesels in existing ULSD units. Catalyst selection should be considered carefully as these feeds contain oxygen. Additional items to be considered and reviewed during a management of change or equivalent process evaluation would include items such as:
1, New feed components and side reactions;
2. Higher hydrogen consumption;
3. Accumulation of CO, CO2, and other lights in recycle gas;
4. Undesirable product cold flow properties depending on co-processing percentage in the feed;
5. Fouling resulting from poisons Na (sodium), P (phosphorus), and Cl (chloride) and diene formation and polymerization; and,
6. Coking and corrosion