Question 44: Contaminants in aromatics extraction unit feeds such as chlorides and oxygen are difficult to measure, and can lead to operational issues (such as fouling / corrosion / erosion, etc) in the extraction unit. In your experience, what are the primary effects of these contaminants, and how can one manage these impacts?
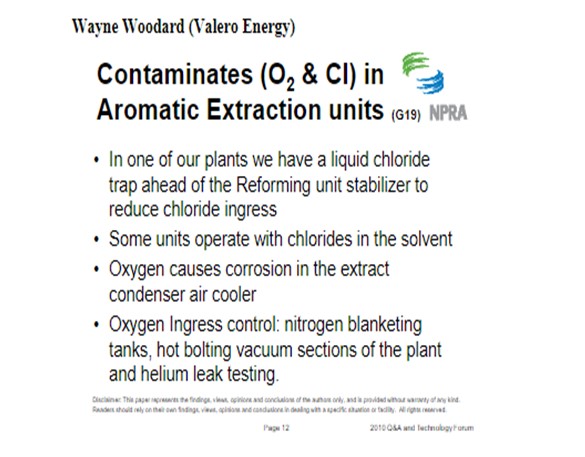
Greg Harbison (Marathon Petroleum)
Most of Marathon’s experiences with contaminants that affect solvent quality are with oxygen. Oxygen can enter the unit from solvent storage, feed, and re-run tanks. Any vessel operating under a vacuum can also be source of oxygen. Most of our issues with corrosion have occurred in the stripper and recovery column reboilers. We have also seen cases of extractor tray fouling. Our reboiler metallurgy has been upgraded to Duplex stainless steel to improve exchanger life.
Oxygen will attack the solvent, breaking down the solvent into acid those results in high acid number and low solvent and overhead water stream pH. The solvent’s acid number and pH are routinely monitored by our quality control lab. We also monitor the pH of the overhead water. Typical pH ranges are 5.5-6.0 for the solvent and greater than 7.0 for the overhead systems. Solvent can be broken into acids that will stay with the solvent, and acids that will vaporize and end up in the overhead water boots. A neutralizer is used to control the solvent’s acid number and pH, typically injected into the stripper overhead or circulating solvent stream depending on the unit.
Nitrogen blanketing all feed, solvent, re-run tanks is very beneficial in keeping oxygen out of the unit. In the case of solvent containing tanks, we ensure they are nitrogen blanketed because oxygen contamination has a significant effect on the solvent quality, performance, and corrosivity. These systems need to be periodically checked to ensure that they are operating properly. Nitrogen blanketing off-test product tanks may not be in place at a lot of locations due to the lack of nitrogen utilities with-in a tank farm. If the off-test tank is not blanketed, minimizing the generation of off-spec material and/or reducing the re-processing of the off-test material will help improve solvent quality. If the unit has experienced solvent quality issues when reprocessing “wet solvent” and/or off-test material, the addition of neutralizer pro-actively can minimize the impact of the incoming oxygen. Whenever possible, Marathon blends off-test material to the gasoline pool, minimizing the potential for oxygen getting into the unit.
Marathon has minimal experience with chloride contamination. We have recently had an incident where water excursion in the platformer was followed by a low pH and high acid number excursion in our solvent. The normal addition rate of neutralizer was tripled for several days to catch the excursion. The key for minimizing chlorides in the aromatic extraction unit is to prevent chloride migration from the reformers.
Solvent regeneration is critical to remove the degradation products of oxygen and chloride contamination. The degradation products of the oxygen attack on the solvent can result in the formation of heavy compounds that can only be removed by accumulating in the solvent regenerator. This material can build to levels requiring the solvent regenerator to be shut down and cleaned out. The frequency of clean out is dependent on the ability to protect the solvent from oxygen and chlorides. One of our units can operate 2 years without the need to clean out the regenerator.
Phil Thornthwaite (Nalco Company)
Where sulpholane is used as the extraction solvent, the ingress of oxygen can lead to the degradation of the solvent to form acidic species. The oxygen reacts with the sulpholane to form an aldehyde intermittent and liberate SO2. Further reactions with both oxygen and SO2 propagate to form acidic polymers. The reaction of the aldehyde with oxygen forms weak carboxylic acids while strong sulphonic acids are formed from the reversible reaction of SO2 and the aldehydes.
These acidic degradation products can lead to significant corrosion with the highest rates being observed at the vapor – liquid interface in equipment such as stripper reboilers.
The polymers formed from the degradation are not soluble in the sulpholane solvent and will drop out of solution at higher concentrations. In addition to the insoluble polymers, corrosion by-products will add to the total solids loading of the solvent. The presence of solids may lead to in sufficient quantities this will lead to erosion by the solid degradation/ corrosion products carried in the circulating solvent and fouling of critical exchangers. Additionally, these solids are good foam stabilizers, and this can result in foaming in the recovery tower.
In order to prevent the degradation of the sulpholane solvent, it is recommended that the storage tanks are nitrogen blanketed to prevent oxygen ingress. If there is some degree of oxygen ingress, companies like UOP recommend the use of phenolic based antioxidants to terminate the auto-oxidation reactions that form the degradation process. However, while any further degradation may be minimized, the existing degradation products present in the solvent can still cause significant corrosion.
An approach that Nalco have used is the use of an oxygen scavenger as this will result in the formation of a magnetite (Fe3O4) layer of the metal surface which would provide a protective scale. This scale effectively mitigates any corrosion whilst eliminating the oxygen that takes part in the degradation reactions. This is an advantage over the antioxidant approach since it will minimize any further degradation of the Sulpholane while mitigating the corrosion in the system until the quality of the solvent improves.