Question 43: What is your experience with intermittent mud washing of single-stage and two-stage desalting? What are the advantages of continuous versus intermittent mud washing?
SOLOMON (Athlon Solutions)
I was supposed to have a follow-up question after we talked about some good practices; but you know, mud washes are necessary. You have to do them to keep those vessels clean. We recommend, obviously, doing a mud wash survey. Let us see how we are doing, check the condition of the mud wash headers, and make sure we are getting good flow and have good pressure there. One thing to keep in mind is that sometimes, again like Eric mentioned, you have to use whatever water you have. Hopefully, you are not using your wash water to do your mud wash, because then you will not be doing a very efficient desalting during that time.
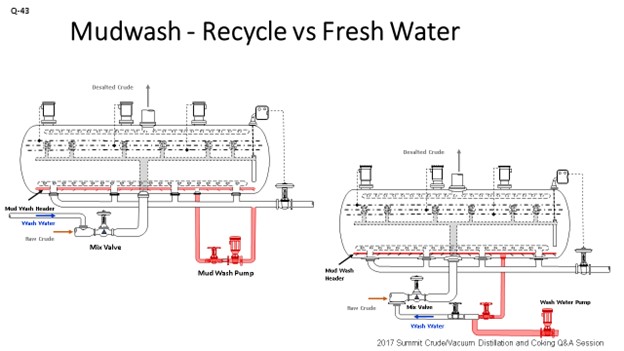
There are, obviously, some advantages of continuous mud-washing. You just set it and leave it. It just happens all the time. There are disadvantages. Of course, it can create excessive turbulence within the quiet zones of the desalter. It could also actually help grow that emulsion layer that tends to sit at the water oil interface.
The problem with intermittent washing is that it just does not happen sometimes. Right? The operators are too busy. You forget about it, and it does not get done. Before you know it, you are building up lots of mud in the vessel. You are losing your effective area and cutting down residence time.
So, there are pluses and minuses with both options. I typically like consistent operations because there is usually less cause for concern and less opportunity for something to go wrong or be forgotten. Those are my answers to the throwback questions.
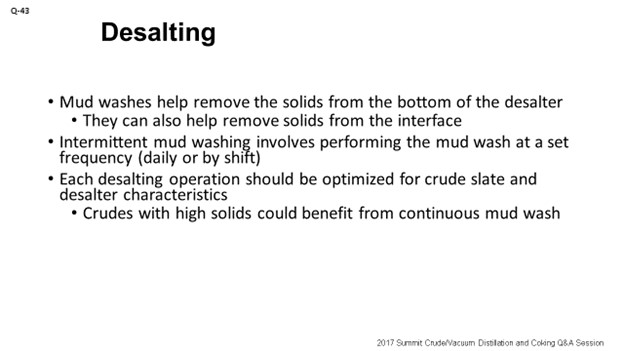
LÉGARÉ (Andeavor Martinez Refinery)
I do not have anything else to add. Kevin covered all of it well.
RAÚL ROMERO (NALCO Champion)
We have experience with continuous and intermittent mud washing systems. Basically, with high solid crudes, continuous mud washing generates a solids-stabilized emulsion at the interface that, in general, can make the performance of the desalter worse than intermittent mud washing. This is one of the cautions we must make when we are proposing continuous mud washing. I agree that sometimes mud washing may not be done as frequently as it should be, but it may be preferred – in the current environment of high solids in crude – to keep discontinuous mud washing compared with continuous mud washing. We can test that when we profile a desalter. One way to check the effectiveness of that solution is to measure solids buildup in the profile.
SOLOMON (Athlon Solutions)
Yes. Very, very true. As I mentioned, you just have to watch that rag layer to make sure it is not getting out of control. Do the profile; get the operators out there to look at the try lines. There are also some new nuclear devices that can be inserted which allow you to actually watch how that rag responds and provides the operator with the ability to draw off that rag, if it is growing. So, there are some tradeoffs. You just have to watch and understand your systems and know what is best for your operation.
JAMES JOHNSON (Marathon Petroleum Company)
I have taken the stance that you either mud wash continuously or not at all. An intermittent wash allows the solids to build up in the vessel; and when the sludge touches a nozzle, that nozzle will stop flowing. Upon inspection, the desalters that are washed intermittently will have a considerable sludge layer whereas there is no sludge in a desalter that is continuously mud washed.
Concerning an emulsion build based on a continuous mud wash, we have not seen any correlation between continuous mud wash and emulsion growth. If anything, intermittent mud washing can cause the problem; because when a second-stage is being washed, a slug of solids is being introduced to the first-stage mix valve versus solids going back to the bottom of the water layer.
DARYL HANSON (Valero)
I agree with Jim’s comment. We prefer to go fully to continuous mud wash, varying the strength for optimization. One of the key factors that drives us to that point is wastewater treatment. Wastewater treating does not like to see consistent water quality: Variable oil and solids loading is not good. So, stabilizing water quality will be worth a lot more than any benefits you may get from intermittent mud wash, which, in my mind, are nothing.
ANDREW SLOLEY (Advisian WorleyParsons Group)
I have a quick question. We have been talking about the mud wash and the solids content. Mud washing is clearly related to the solids content. Does the panel have any comments on, if they are going to do intermittent versus continuous, what solids content would cause a plant to choose an intermittent mud wash instead of a continuous mud wash? What percent of solids in the crude would cause them to switch from an intermittent to a continuous mud wash?
SOLOMON (Athlon Solutions)
I do not have an answer.
HAROLD EGGERT (Athlon Solutions)
If the solids become an issue and they are actually cycling up in the interface instead of leaving with the water, chances are those solids are oil-coated. You really need to talk with your chemical supplier about potentially evaluating a wetting agent that will allow the solids to be water-contacted to get off the oil. These solids will go out the bottom of the desalter with the water phase. It is when they are oil-coated that then they tend to agglomerate at the interface and create stable emulsions.
KEVIN SOLOMON (Athlon Solutions)
Mud Wash Best Practices
-
Conduct a mud wash study to understand the duration needed and impact on the unit. Mud washing can be continuously or at some frequency and duration, so understanding the optimal mud wash practice at your refinery is very important.
-
Conducting pressure and flow surveys around the mud wash system can help confirm the condition of mud wash header versus design.
Advantages of Continuous Mud Wash
-
Consistency: just set it and leave it.
Disadvantages of Continuous Mud Wash
-
Can create excessive turbulence in the water quiet zone that may cause wider emulsion layer in the desalter and
-
Can create slugs of oil and solids to the wastewater treatment plant. A little at a time is usually better than a lot for a short period of time.
Advantages of Intermittent Mud Wash
-
Desalters require a quiet time/zone that allows settling of solids and water, and the agitation allows break.
-
Intermittent mud wash can be done if desalter wash water needs to be used as mud wash.
Disadvantages of Intermittent Mud Wash
-
Inconsistency because this process is often forgotten or skipped by operators if there are other demands in the unit.
ERIC LÉGARÉ (Andeavor Martinez Refinery)
The primary purpose of a mud wash is to suspend and remove solids that have accumulated in the bottom of the desalter. Some desalting operations use the mud wash to remove solids (asphaltenes and oil-wetted inorganic solids including iron) that have accumulated in the interface of the desalter. The desalter level may be lowered to accomplish this goal in some of these operations.
There are typically two types of operation for a mud wash. The first is a continuous mud wash with brine water being recirculated through the mud wash header on a continuous basis, while the second is an intermittent mud wash where the mud wash is operated on a set frequency.
Each desalting operation needs to optimize the mud wash for its particular crude unit operation. Crudes with high solids loading will most likely require more rigorous mud wash procedures. Past optimization of intermittent mud wash operations would recommend that the brine effluent be monitored at the start of the mud wash cycle and be allowed to continue to run until the brine clears up or no additional solids settle in the sample bottle. For some systems, this may be a few minutes while others may take several hours.
The typical minimum mud wash frequency for intermittent mud wash operations is once per day or once per shift. Continuous mud wash operations should optimize the flow rate based on maximizing the mud wash flow while not impacting average brine quality.
The process engineer or chemical supplier monitors sludge buildup by temperature mapping of the lower sections of the desalter. This data provides some indication if sludge is building up.
Depending on the desalter design, the outlet piping of the brine system should be monitored to ensure that there are no plugged outlets.
A typical mud wash system utilizes recirculated brine water through a dedicated mud wash pump and a mud wash header within the desalter. Many systems utilize a mud wash header that has downward-pointed nozzles at intervals of approximately six feet. If the nozzles are 3/8” pipe, a typical flow rate target would be a minimum of 10 gpm (gallons per minute) per nozzle. Best Practices require a flow meter to verify and a globe valve (recommended) to adjust the mud wash flow rate.
There are variations in the design of the mud wash header and specific design changes have been installed by various refiners. Many of these involve additional nozzles or modifications to the header piping.
Some desalters have a mud wash header that is split to various sections of the desalter.
Best Practice recommends that the mud wash be recirculated brine and not fresh desalter wash water. Fresh water is sometimes used as it saves on the design of the mud wash pump but may rob desalter wash water and result in reduced desalting efficiency when mud washing.
Though the mud wash is generally beneficial to the desalting operation, if operated incorrectly, it can stabilize emulsions and impact desalter stability. Examples of this would be:
-
If the level is too low when the mud wash is started, oily solids from the interface can be pulled into the recirculation and stabilize emulsions. These oily solids can cause excessive oil in the brine during a mud wash.
-
If the flow rate of the mud wash is too high, then – even if the desalter level is sufficient – the interface can be sufficiently disturbed (or the water residence time reduced) such that oil is increased in the brine effluent.
For two-stage desalters, it is typically recommended that the second-stage desalter be mud washed first. This procedure order is typical when the brine from the second-stage becomes the wash water to the first-stage. However, if either of the above conditions results in high levels of oily solids going to the first-stage mix valve, emulsions can be stabilized in the first-stage, potentially causing unstable operation.
Operations with high solids or heavy crudes can route the second-stage mud wash to alternate dispositions rather than the brine going to the first-stage as wash water.
During turnaround, the mud wash header should be inspected for missing nozzles and tested for pluggage.
CHRIS CLAESEN (NALCO Champion)
Mud washing should be done intermittently as it creates extra agitation in the vessel that can lead to increased solids and water carryover. In a lot of systems, mud wash comes from the wash water; this operation reduces the wash water rate at the mix valves. The frequency and duration of the mud wash depends on the crude slate; mainly, the solids content and how well it is removed. The washing of the second-stage desalter vessel needs special attention. If the sludge is sent with the brine to the first-stage desalter vessel, desalter upsets and reduced desalting/solids removal can occur.
DENNIS HAYNES (NALCO Champion)
Optimized intermittent mud washing has the benefit that contaminants can settle through the water phase and the interface is not disturbed when the mud wash is off; yet the desalter can be purged of mud when the mud wash is on. There have been cases where too high of a mud wash frequency has negatively impacted solids removal because of the disturbance of the desalter interface. However, since each intermittent mud wash contributes an elevated amount of purged solids mud to the wastewater treatment plant, continuous mud wash has the merit of a more consistent effluent brine quality.
PHIL THORNTHWAITE (NALCO Champion)
In short, the key to effective mud washing is to use it as frequently as possible for as short a duration as needed. It is relatively simple to perform a mud wash study, and these ideally should be carried out annually to ensure the current procedures are still effective or after any significant changes in crude feed or crude solids levels. Some mud wash systems, especially on large vessels, have a split-header arrangement that washes different sections of the vessel in sequence so that the correct flow through the nozzles can be applied to clean that section of the vessel. They can be automated; however, it is recommended that some manual checks be carried out before the mud wash commences. For example, if the effluent water is oily and if there is a problem with a persistent emulsion layer, care should be taken, and it may be beneficial to defer the mud wash to a later time when the desalter operation has stabilized. This is a consideration when looking to use a mud wash on a second-stage desalter since the effluent from this vessel is often used as wash water for the first-stage desalter. With high levels of solids in that water, it can precipitate an upset in the first-stage desalter; and consequently, it is not common to find a mud wash system in a second-stage desalter.
As for continuous mud wash, one has to question the need. If frequent short bursts are sufficient to keep the vessel clean, using the mud wash continuously may offer no real benefit. In fact, it may impact desalter performance as the constant flow of water via the mud wash header will impact water residence times that may impact the effective resolutions of the oil and water emulsions. However, it is accepted that for crudes with very high solids contents, continuous mud wash may be of benefit, but it would have to be evaluated on its own merit.
RAÚL ROMERO (NALCO Champion)
General observations on practices for different desalters on intermittent mud washing are the following:
-
Mud washing flow rate has a design consideration based on desalter size and type of header and nozzles installed. Design flow rate should provide suitable agitation to remove solids that have settled in the desalter. Mentioned flow rate is not always applied or even known. Operating procedures should include that flow rate, and all shifts should apply the same criteria.
-
Mud washing duration and frequency should be defined by a field test based on solid removal efficiency. This practice should also be normalized for all shifts.
-
Header pressure downstream of flow control valve gives an idea of potential nozzle plugging (higher header pressure drop at the same flow rate suggests nozzles plugging contribution to poor distribution).
-
Old designs still use steam as mud washing fluid. It can generate higher desalter instability and less effective solid removal than proper water mud washing design.
-
Two-stage desalter system: Generally, the first stage should require more frequent mud washing than the second stage since most of the total solid removal is done in the first stage.
-
Second-stage mud washing should require more attention since removed solid can impact on the first stage. Some designs include facilities to run desalting wash water in parallel during this event, but it is likely to reduce its percentage on crude, reducing desalting efficiency.
Continuous versus intermittent mud washing:
-
Most of the desalting systems are designed for intermittent mud washing, despite the fact that it can be run continuously.
-
Continuous mud washing contributes to clean effluent from solid and hydrocarbon on a short-term basis (one to two days), but it tends to accumulate solids in the interphase, increasing the emulsion layer and its stability. If filterable solids in the crude feed are high or variable, they will be detrimental for desalter operation and performance. In the following table, a desalter profile is shown when mud washing was changed from continuous to intermittent. Please observe that a solid accumulation in #1 (lower tri-cock) was eliminated which improves emulsion resolution.
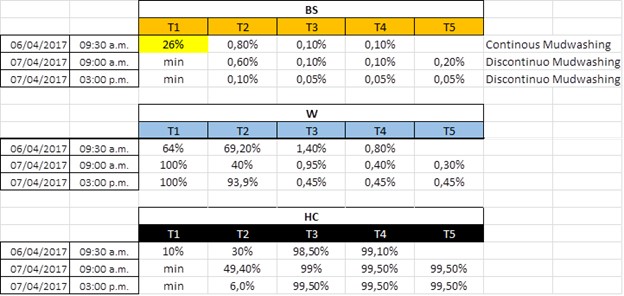
GLENN SCATTERGOOD (NALCO Champion)
Intermittent mud washing allows us to manage and minimize the accumulation of solids in the bottom of the desalter vessel. The intermittent washing also minimizes the disruption caused by the mud wash. As more high solids crudes are processed in our geography, the mud wash is receiving a higher level of attention and priority.
SAM LORDO (NALCO Champion)
Both techniques of mud washing, when designed and applied properly, are useful in minimizing the buildup solids in desalters.
The key to intermittent mud washing is frequency and duration at the proper waterwash nozzle velocity. Most designs are for intermittent operations.
The key for a continuous mud wash system is the design of the spray nozzle header and the angle of the nozzle: too sharp of an angle, the higher the potential for moving the solids up into the interface, which is the common issue with continuous mud-washing operations. Too high of nozzle velocity is another issue that is common with continuous mud washing; again, the issue being moving the solids into the interface. But if properly designed, then continuous mud washing can be operating with minimal impact on the interface.