Question 43: For PSA units, what are the typical inspection techniques, frequency of inspections, and issues discovered? What are the criteria for retiring an adsorber?
EPSTEIN [Flint Hills Resources, LP (FHR)]
At Flint Hills Resources Pine Bend Refinery, external ultrasonic testing is performed on areas of concern (welds, heat-affected zones, attachments, or identified stress risers) every five years. To date, no areas of concern have been identified in the PSA vessel inventory. Internal wet-fluorescent magnetic particle inspection is expected to be performed on the areas of concern after 30 years, which has not yet occurred. Internal peaking measurements of the long seams are also to be taken during the internal inspection. Data from the external and internal inspections will be used to develop a risk-based inspection protocol going forward. This may decrease the interval between internal inspections.
WRIGHT (Hunt Refining Company)
From my inspection friends, I learned that we use wet fluorescent magnetic particle testing, PT (dye penetrant testing), visual, and phased array on the adsorbers. We do an external inspection every five years and an internal, every 10. We have an old Howe Baker PSA systems that was revamped to a modern PSA, and we found weld cracks around some abandoned support rings as a result of that renovation. We would retire any vessel when the minimum wall thickness was reached or excessive cracking around these support rings.
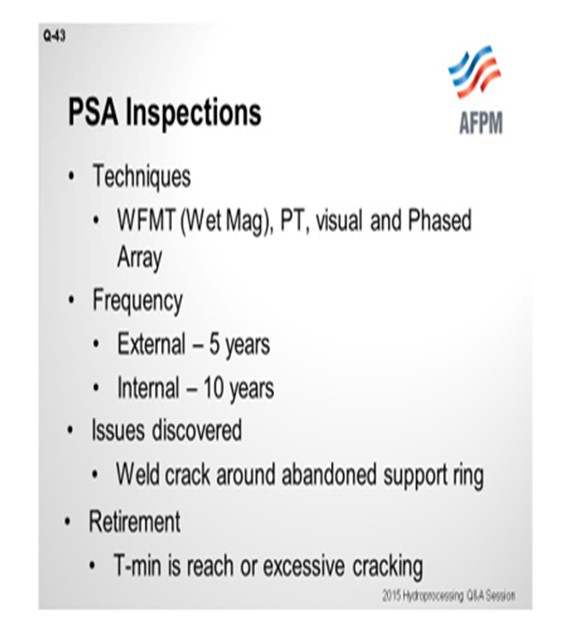
PEDERSEN (UOP LLC, A Honeywell Company)
UOP typically recommends doing UT (ultrasonic testing) inspection every three to five years. One point with regard to UT: It is very valuable to get fingerprint or reference measurements right after fabrication or early after the unit has been started up, so you have a basis for comparison versus future test results. Increased frequency of inspection is recommended as the vessels age. For more details on addressing inspection and retirement of vessels, please refer to the 2010 NPRA Q&A Answer Book, Question #8.
HOLGER WEBER (Linde Engineering North America Inc.)
It is Linde’s experience as a leading H2 PSA supplier that adsorber vessels are subject to cyclic service and therefore designed for a certain fatigue lifetime, mostly 15 or 20 years. During this adsorber lifetime, the adsorber vessels needs to be periodically inspected. The frequency and kind of inspections are different depending on location and need to be checked with the local inspection authorities. The inspection methods are either visual testing of the welding seams from inside of the adsorber vessels and/or hydrostatic testing. Since for both inspection methods the adsorbent material needs to be removed and cannot be reused, the respective inspections authorities might accept alternative testing methods (e.g., ultrasonic testing from outside).
At the end of the fatigue lifetime of the adsorber vessels, the operating permit can normally by extended, based on specific inspections of the adsorber vessel. The respective inspection regulations are also locally different and need to be checked with the responsible inspection authority.