Question 43: In order to meet RMACT 2 regulations for reducing regenerator vent gas HCl and Total Organic Carbon, some refiners use caustic scrubber vent gas wash tower systems for treating the regenerator vent gas. What has been your experience with respect to corrosion problems? Which equipment (Venturi scrubber, wash tower) and piping have corroded more often? What changes have been made in procedure and/or metallurgy to minimize corrosion?
Brad Palmer (ConocoPhillips)
We have three CCRs with vent gas scrubbers; all are carbon steel, and all have experienced corrosion problems.
Fouling in the scrubber vessels and in the vent-gas lines has been severe and caused under-deposit corrosion in these areas. Corrosion in the scrubber vessel has included pitting of the walls, bottom head and thinning of nozzles. Thin spots in these vessels have been built back up and nozzles replaced as necessary. Corrosion of internals has been severe, including distributors, trays, demister pads and off-gas lines. Internal piping, equipment and vent-gas lines have been replaced.
Responses to the corrosion have primarily been mechanical. One unit has sand blasted their scrubber tower and coated the walls and bottom head with Belzona; the next turnaround will reveal whether this has been effective. One unit has changed metallurgy of their weld overlay and upgraded their demister metallurgy. One venturi scrubber has been upgraded to Hastelloy C-2000. The only operational change has been to increase the scrubber purge rate to reduce solids and salt concentrations.
Michael Windham (UOP)
The reactions taking place in the venturi scrubber/VGWT are as follows:
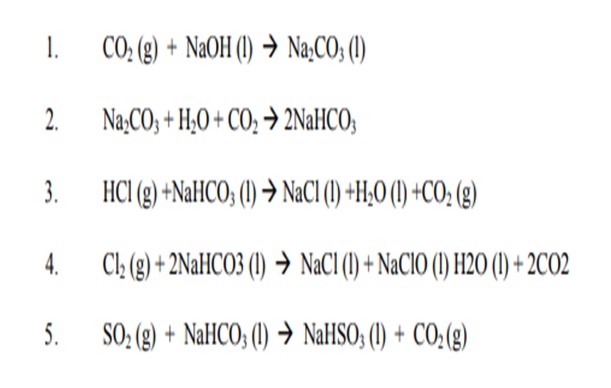
We learned from the past:
-There are two problems that can occur. One problem is if there is too much build-up of Na2CO3 and NaHCO3 due to too much caustic being injected and/or not enough draw-off, the Na2CO3 and/or NaHCO3 will precipitate out of solution and begin to cause plugging. The other problem is if there is insufficient Na2CO3 or NaHCO3 due to not enough caustic being injected and/or too much draw-off, there will be insufficient Na2CO3 and/or NaHCO3 to react with the HCl, Cl2 and SO2 in the vent gas then we have corrosion.
-Some unit claims they follow our guidelines for operation of VGWT but still they have corrosion. There might be other reasons to contribute to fouling and corrosion of the scrubber and downstream piping:
1-The vent gas enters the scrubber at ~450o C (842 oF) but the temperature of the caustic is ~40 oC (104o F). The caustic can get vaporized by the hot vent gas, resulting in the formation of the sodium salts (fouling) in the scrubber. (This has not been confirmed yet).
2-Sudden changes in the regeneration tower operation may contribute to formation of the salt. (Example: If amount of the Chlorides in the vent gas to the VGWT were suddenly increased or decreased, or temperature of the vent gas suddenly changed because of high coke). ( Not confirmed yet).
Which equipment (Venturi scrubber, wash tower) and piping have corroded more often?
The extent of the problem varies from unit to unit. In general, some of the units experience some type of plugging and corrosion every 6 months. In one case the unit has been in operation for slightly less than 2 years and is already on their 5th venture scrubber. The plugging (fouling) and corrosion of Venturi Scrubber and the line downstream of the Venturi Scrubber to bottom of Vent Gas Wash tower occurs more often since the majority of the acid neutralization occurs in the Venturi Scrubber
Erik Myers (Valero)
Valero has experienced similar corrosion challenges with this type of treating.