Question 43: In both Extractive Distillation and Liquid-Liquid Extraction units, foaming in the Extractive Stripper column leads to solvent carryover and unit upsets. What are the determinants of foaming, and how do you determine foaming risk? Is continuous antifoam injection necessary? What are the countermeasures do you take to minimize this risk?
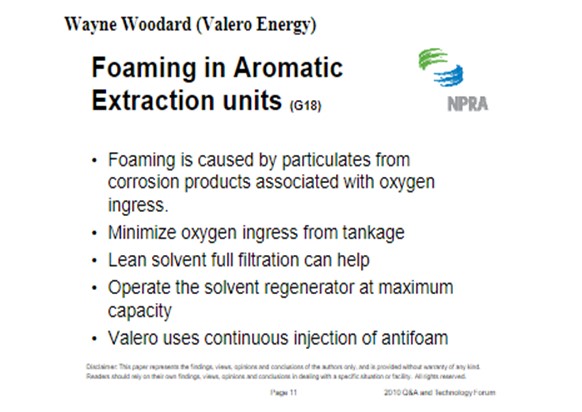
Greg Harbison (Marathon Petroleum)
Marathon has two liquid-liquid extraction units. Both are fed from reformers. We continuously inject anti-foam into the stripper feed. The only foaming events we have observed have been after the loss of anti-foam injection. In one case, we observed foaming in less than one day. In our existing extraction units, we equip our injection systems with a pressure alarm on the pump discharge to notify the operators when the injection system trips off-line. On our unit currently in construction, we will also install a back-up pump. We feel the risk of foaming upsets justifies the cost of the anti-foam.
We typically target a 1.0 ppm level of anti-foam in the stripper feed. There are several factors that will affect a system’s ability to foam. Some of the areas we watch closely include low stripper pressure, lighter feeds, and high stripper feed temperatures. These operating variables will cause the stripper feed to be more prone to flashing which directionally shifts the system towards foaming. Extractor reflux should be monitored to prevent the build-up of light compounds in this stream.
Lowell Pless (Tracerco)
We would suggest using gamma scans on the stripper column to confirm or deny that foaming is the root cause of the operational problems. If foaming is indeed the culprit gamma scanning could be used to determine the effectiveness of antifoam, to optimize the antifoam rate, and to study the effect of other process variables on the operation of the stripper column.