Question 42: Is the investment justified to convert an older hydrogen production unit from a solvent CO2 removal system to a pressure swing adsorption (PSA) system?
EPSTEIN [Flint Hills Resources, LP (FHR)]
My analysis suggests that this kind of a modification is not economically justified for the small solvent system hydrogen production unit operating at the Flint Hills Resources Pine Bend Refinery. While it is true that a PSA unit is more efficient than a solvent unit, the capital required to convert between the two is too high.
If I assume a hydrogen production efficiency (defined below) of 500 BTU per scf (standard cubic foot) for the solvent unit and 380 BTU/scf for the PSA unit, an energy value of $4 per MMBTU (million BTU), and a daily production of 15 MMscfd (million standard cubic feet per day) hydrogen, then the annual value of this modification would be $2.6 MM. Over a 20-year project life and targeting a 15% rate of return, a project would be justified to spend around $16 MM in capital to capture this value. My calculations at other capacities indicate that the capital justified is roughly $1 MM per MMscfd of hydrogen production.
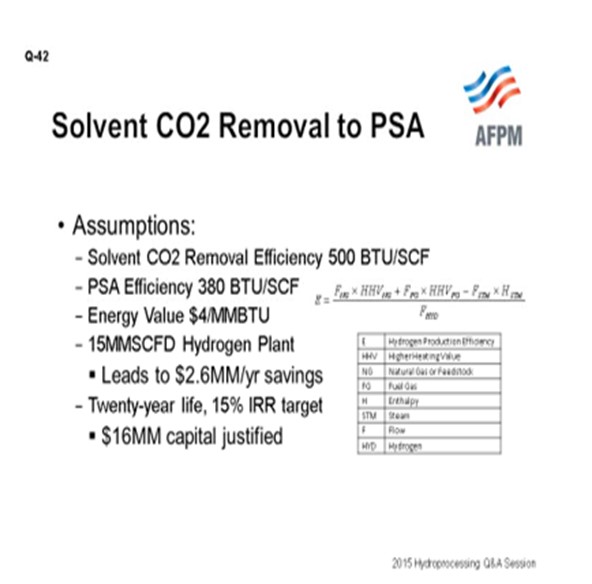
The capital modifications necessary to convert from a solvent unit to a PSA unit include:
1. Purchasing and installing the PSA system.
2. Modifying the unit control system to interface with the PSA control system.
3. Processing the low-pressure purge gas from the PSA system. The reforming furnace associated with the solvent unit is unlikely to be configured to process fuel gas and purge gas. Either new burners will be necessary, or the hydrogen-rich purge gas will need to be compressed into the refinery fuel system.
4. Modifying the unit heat integration. If the solvent reboiler is driven by the process gas, this heat will have to be removed through a new heat exchanger. If this heat is removed through the production of steam (which would likely be required to achieve the hydrogen production efficiency mentioned above), the steam drum may have to be resized for the additional flow. The cost of these modifications is likely to exceed the value created. There are potential savings from switching to a PSA unit including:
5. Avoided cost of methanator catalyst replacements,
6. Potential avoidance of low-temperature shift catalyst replacements if that equipment is bypassed in the PSA scheme, and
7. Avoided cost of solvent chemicals.
I believe that the more likely economic justification will occur if the decision is made to build a new PSA-based hydrogen production unit. The incremental capital to increase the capacity of the unit by the capacity of the solvent unit will likely be justified by annual savings in efficiency.
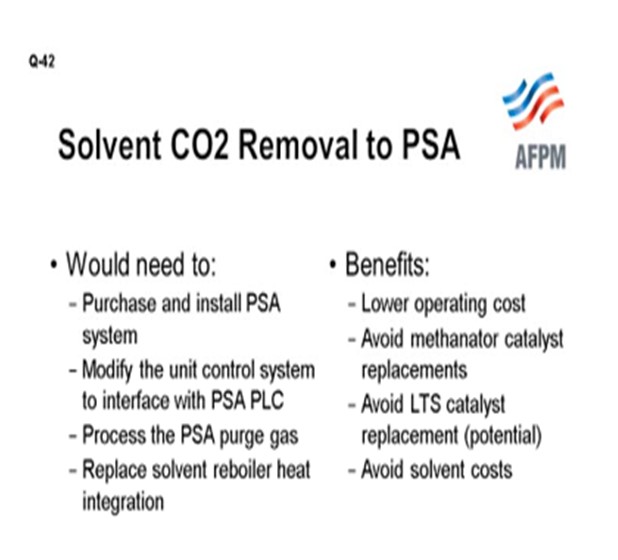
PEDERSEN (UOP LLC, A Honeywell Company)
If we take a look at a simple schematic comparing the equipment required for PSA versus that for a solvent system, we can see that, in concept, the PSA is much simpler. Starting from scratch, the clear choice is a PSA system. Not only is this operation simpler and easier to operate and start up, but it is also less equipment; and therefore, less capital expense. The product has a much higher purity, which can be of value in the refinery hydroprocessing units. Paul already talked to us about some of the considerations for making a switch. One key point that he highlighted is the fact that in the design of the PSA system, typically a high percentage of fuel firing the steam reformer heater is waste gas from the PSA, and accommodation of the heater for that case would have to be made.
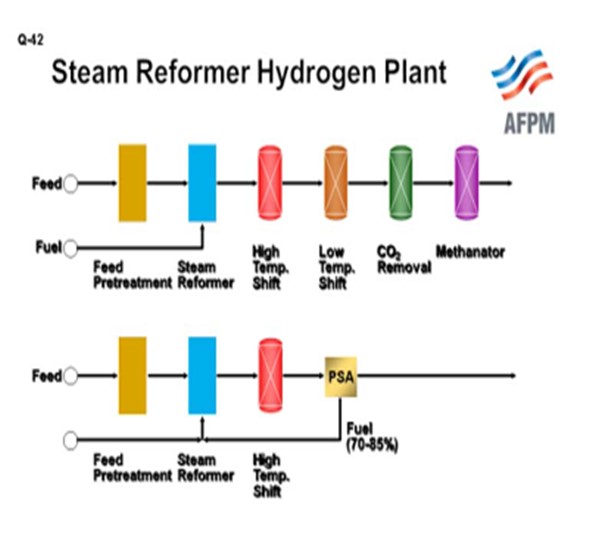
On the next slide, we have a summary of some points regarding the value of PSA. Additional factors regarding evaluating the consideration of switching the upgrade or purification system include the following questions: Is the current system at its end-of-life? What is the salvage value of the hardware? What is the cost of lost opportunity for extended down time if there was a decision to replace equipment? One other consideration with making the switch is that it will de-rate the unit. Net hydrogen production from an existing plant will decrease significantly, since a substantial fraction of the produced hydrogen is lost into the PSA waste gas and ends up in the fuel gas system or, preferentially, as fuel in the steam reformer furnace.
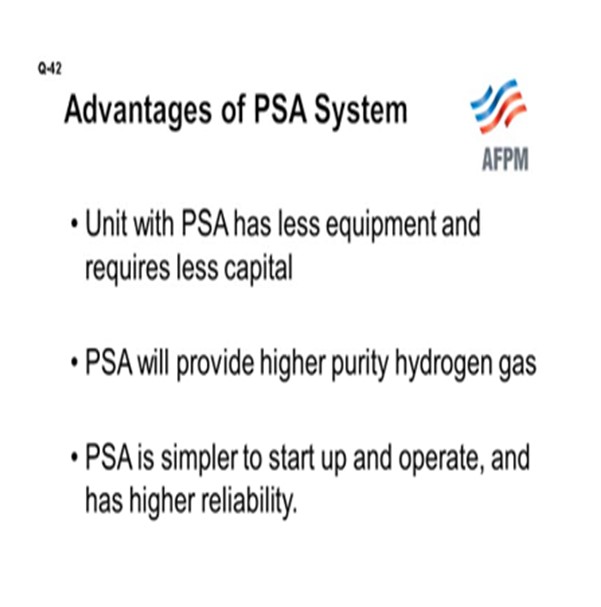
And lastly, downstream units have centrifugal recycle gas compressors that have been designed for an optimum gas gravity. If we upgrade the purity and, consequently, reduce the gravity of the makeup gas, there will be a significant impact on the performance or utility of the existing compressors.
UOP is a primary provider of PSA technology. In the past, we were also a primary provider of solvent CO2 removal systems. We are not aware of any request for project studies of this type in the past 30 years.
MIKE ADKINS (KP Engineering, LP)
Just a prologue to some of the comments. Again, to steal some comments from a panelist and also from this morning, I will say, in a question like this, that often the answer in our engineering solutions is, “It depends.” And of course, I am sure you will believe my comments are not biased, even though I work for an EPC (engineering, procurement, and construction) [laughter] company, as opposed to Paul Epstein’s comments. But also, as Daryl Dunham said this morning, although I am not a hydrogen expert, I have traveled with a few. So, what I am trying to say here is that when you convert from a solvent-based plant to a PSA-type plant, you will reduce hydrogen capacity. However, you will see an increase from somewhere around a 95% hydrogen purity going to up to 99.99% in a PSA unit that UOP can provide. From what we have seen in the plant studies, it really revolves around utilities. Most refineries view hydrogen as a utility. So do the hydrogen partial pressures, for instance, in your hydrotreaters make a difference to you, from an economic standpoint?
And then also, steam value comes into play. A PSA unit will have a higher steam production than a solvent unit. Furthermore, a PSA unit will have less overall feed and fuel rates compared to a solvent unit. So, while your feed is a little higher in a PSA unit, your fuel is significantly less. Those are some of the considerations that we have investigated.
SUE SIMPSON (Johnson Matthey)
This is a plant- or site-specific decision. Increased purity, improved operating efficiency, and reduced fuel costs are benefits to be considered with a PSA. This conversion, however, has not been observed in the industry without being subsidized. If improved hydrogen purity is needed, the PSA unit will allow that requirement to be met. The PSA provides purity of 99.999% compared to about 95% purity for the CO2 removal system.
If the product is used in a hydrocracker, a major benefit to high purity gas would be longer cycle lengths. However, the hydrogen recovery would be decreased to about 85 to 90% with the PSA (typically, it is greater than 95% for a CO2 removal system). This could require an approximately 10% higher feed rate. This additional capacity would need to be available in the reformer or at least have the ability to retrofit additional capacity with other technology, such as a gas-heated reformer.
A PSA should improve operating efficiency by allowing a reduction in the steam-to-carbon ratio and an increase in the reformer exit temperature. In addition, the operating costs for a PSA constructed of mainly vessels and valves should be significantly less than for the CO2 recovery system using solvents and pumps that can have fairly large power expenses.
If the reformer is using natural gas as fuel, the PSA purge gas can satisfy a large portion of the fuel by resulting in reduced operating these costs. However, modifications to the burners would most likely be required. Heat integration would also have to be investigated. Without the CO2removal system, heat could be removed from the process and used elsewhere.
Older plants typically have a two-stage shift section [high-temperature shift (HTS) followed by a low temperature shift (LTS)]. The CO exiting the LTS should be at a low level and is a key component for the PSA. The low level of CO should result in a PSA that is smaller than a typical hydrogen plant with an HTS alone.
Can the benefits of a high purity product, improved operating efficiency, and reduced fuel cost of a PSA justify the decreased recovery, additional reformer capacity, and heat integration modifications? This would have to be evaluated by a specific site and typically has not been observed in the industry.
HOLGER WEBER, RAJU NATARAJAN, and NICK MUSICH (Linde Engineering North America Inc.)
Linde’s current concept for hydrogen production is to separate all impurities in the synthesis gas with a PSA unit. The investment decision to convert a solvent CO2 removal system in an older hydrogen product unit to a PSA system needs to be investigated on a case-by-case basis. Numerous factors – like the condition of the existing plant, the respective process parameters, and the utility costs, especially the steam value – affect the decision making. Some general guidelines are:
1)If the refinery is short on H2, it is generally not recommended as the PSA will lose 10 to 15% of the H2.
2)If CO2 is being recovered for the merchant market, a PSA is generally not going to be economical.
3)In addition to the PSA, the impact on the following will need to be considered: burners, emissions, velocities in the convection section, fan capacity, additional steam production, and process gas cooling.
4)If the refinery has hydrogen-rich streams that can be integrated in a new PSA system, it will improve the economics.
5)Since the purity of H2 from the PSA is much higher, hydrogen utilization in the hydrotreater or the hydrocracker (or other H2 users) would be better and would minimize hydrogen losses in the purge.
6)The H2 plant may be able to eliminate the low temperature shift converter, which is somewhat difficult to maintain.
7)Since the purity from the PSA is much higher, hydrogen utilization in the hydrotreater or the hydrocracker (or other H2 users) would be better and would minimize hydrogen losses in the purge.
8)The plant may be able to eliminate the low temperature shift converter, which is somewhat difficult to maintain.
GOPI SIVASUBRAMANIAN (Amec Foster Wheeler)
The economics of the conversion varies based on the requirement of high purity hydrogen and its application. The factors that need to be considered are the purity of hydrogen required, the utilization value for the CO2 stream, and the steam balance.
The economics also should take into account of the cost of replacing reformer burners and marginal loss of hydrogen. production capacity.