Question 41: How do you manage operating flexibility to maximize profits in a changing margin environment during a hydrocracker cycle?
McARTHUR (Phillips 66)
Frequently, market conditions will reward the refineries that have a little flexibility in shifting their product yields among conversion units. We try to do that where that flexibility exists. For a hydrocracker, a primary knob is just overall conversion. Decreasing conversion will enhance distillate yield, increasing conversion, gasoline yield. The amount of flexibility depends on quite a few factors including the heater limitations, firing limitations, feed pre-heat, fractionation limitations, and also the type of catalyst in the reactor. There is some amount of flexibility downstream of the reactor in the fractionation portion of the unit, with specific targets on product flash and distillation endpoints. In our two-stage hydrocrackers, we have made a little use of first- versus second-stage conversion to make small shifts in our product yields. Small changes in recycled cutpoint can be done as well to help improve or help optimize a little on product flexibility. And then lastly, we will redistribute products to different conversion units, to the extent possible, such as moving gas oils from the hydrocrackers to FCCs or to ULSD units to optimize our product slates. Here, there is quite a bit of consideration that must be given to limitations in the feed piping lineups, for example, as well as the impacts on product quality.
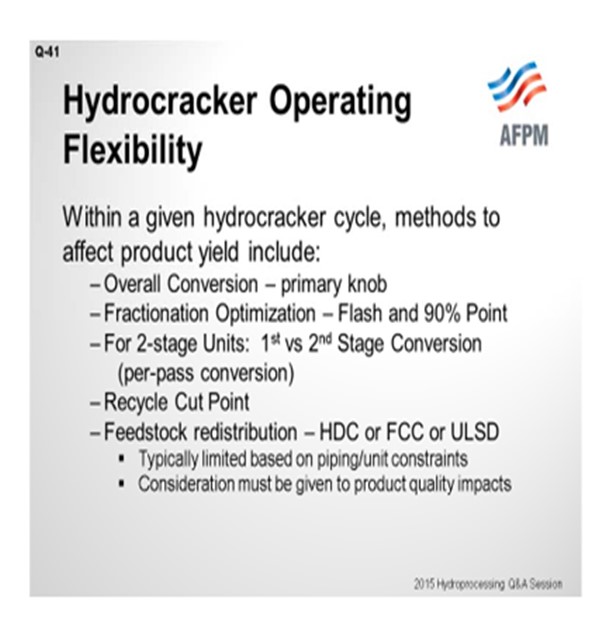
Lastly, looking to the next catalyst loads, making use of flexible cracking catalysts can give a little more room on these flexibilities I mentioned earlier, but they may come at the expense of overall activity level or run length.
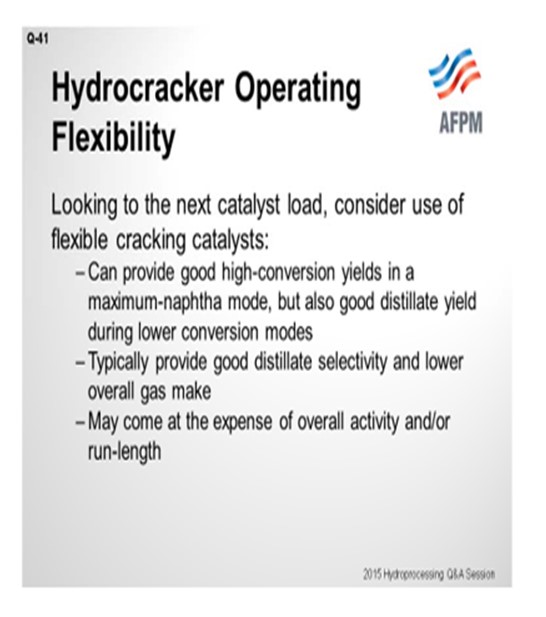
MORELAND (Valero Energy Corporation)
My comments are very similar to Scott’s. Conversion is a variable we can use to maximize either volume gain or distillate selectivity. Some of our partial conversion hydrocrackers will actually lower conversion in a maximum gasoline mode to send more unconverted oil to the FCC versus running higher conversion to make more diesel. This chart shows an example from one of the LCO hydrocrackers from a recent catalyst selection at the low crude price now. Lowering conversions on these units, whether with the current catalyst or a new catalyst, provides higher margin at lower conversion somewhere in the 10 to 20% range even looking at different catalyst types. Additionally, cutpoints can be varied to maximize the most valuable products. We have play with diesel endpoints. And then on hydrocracker catalyst reloads, we are using multiple economic margin scenarios for reloads for maximum flexibility. Typically, we will use five or more different price sets; and sometimes, they can yield different answers as to which is the preferred catalyst.
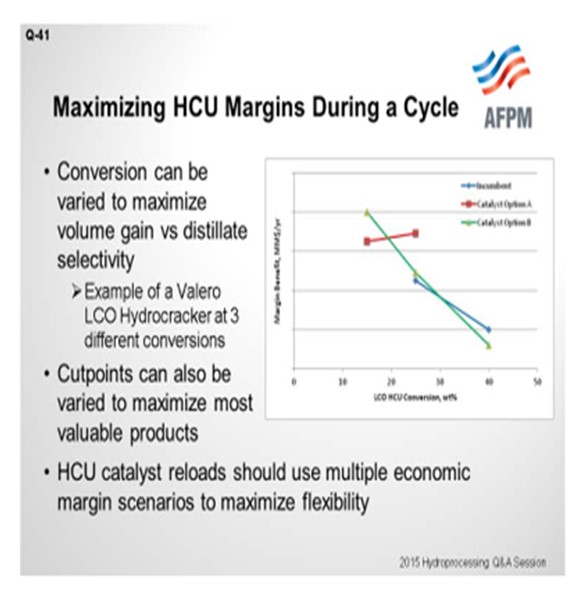
WRIGHT (Hunt Refining Company)
Just to echo what has been said, within the past six to nine months, we changed the hydrocracker from a max diesel to the max naphtha mode, increasing conversion and cutpoint and such. The flexibility question around when the refinery is asked to be flexible so that we can accommodate an economic BTU (British thermal unit) barrel we purchased.
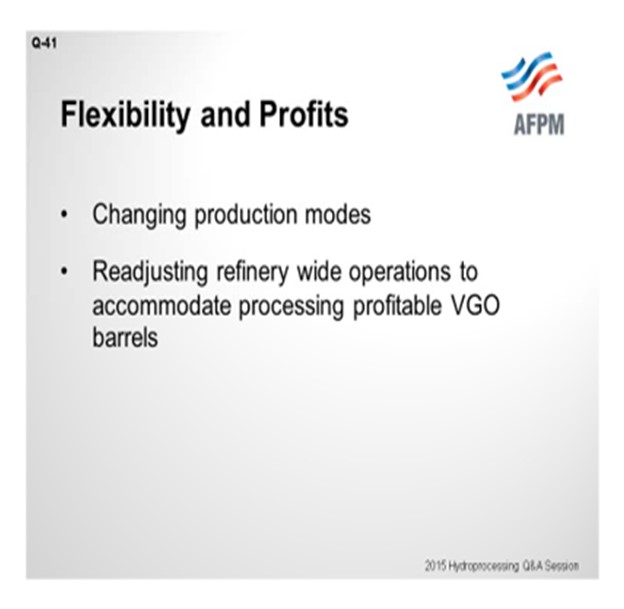
GARY HAWKINS (Emerson Process Management)
It is difficult to provide a concise answer without knowing the nature of the feed, the flexibility of the catalysts loaded in the reactors, and the capability to provide sufficient quench which could constrain increases in throughput. There are other constraints, such as maximum allowable differential pressure across the catalyst bed, but these are less dynamic and more of an issue closer to the end of run. The key is being able to deliver the feedstock to the reactors at the operating conditions that maximize the conversion of the feed to the product of highest value, whether it be gasoline this week and diesel next week. Once the feed enters the reactor, the chemistry happens and it is left to the downstream fractionation to separate the products. This is where the product fractions can be maximized through the application of a multivariable predictive controller on the fractionator. Being able to easily change the cost function of the optimizer to reflect current market opportunities will improve the results. Also see Question 45.
DAVID VANNAUKER (Haldor Topsoe, Inc.)
The hydrocracking catalyst selection sets the operating unit flexibility for the entire cycle. Some units run in a constant mode, while other units operate with a range of conversions to better match the seasonal gasoline and diesel demands. Having a system with sufficient hydrotreating functionality is key for the maximum diesel operation. Having a hydrocracking catalyst with sufficient conversion flexibility is valuable to make the desired product slate. For example, picking a catalyst that is very diesel-selective may limit the high conversion flexibility during a high gasoline demand period. There are a variety of solutions. Key selection variables included the number of months in each operating mode, the unit feed slate, the crude slate, operating pressure, and unit configuration are all key variables that impact upon the final hydrocracking catalyst selection. A detailed study is warranted to make the best decision.
JOE FLORES (Criterion Catalysts & Technologies / Zeolyst International)
During times of changing margin environment, refiners may choose to load a flexible cracking catalyst system into their unit. We define a flexible system as one with moderate activity that has the ability to switch between a max conversion mode – typically producing max naphtha – and a lower conversion mode, which will produce higher amounts of middle distillate. With this type of system, the refiner can vary the split of naphtha to distillate production to take advantage of changing margins. One must realize that tradeoffs often need to be made during the catalyst selection process. To operate at high conversion and achieve acceptable cycle lengths usually requires a high activity catalyst with reduced middle distillate selectivity and higher light ends make. A lower activity catalyst usually has higher middle distillate selectivity and lower gas make but must operate at higher temperature, potentially delivering a shorter catalyst cycle length than desired, if the refiner switches to a max conversion mode.