Question 40: What crude properties and process conditions are you monitoring as part of a crude slate change?
LÉGARÉ (Andeavor Martinez Refinery)
Before I go into my answer, I just want to make sure the audience knows that Ross and I are going to be handling this one in slightly different ways. I will be looking at more of the upstream part of this topic, prior to running the crude, including what steps you go through; so, essentially, the crude MOC process. Then I think you are all going to hear Ross speak for the first time.
McDANIEL (KP Engineering, LP)
I do speak.
LÉGARÉ (Andeavor Martinez Refinery)
Yes, he does speak. He is not up here just to balance the panel.
Andeavor, as I mentioned, uses a Management of Change process to evaluate any new crude stocks or new feed or intermediates coming into the refinery. The MOC is stewarded by the crude unit support engineer. The MOC process already engages all of the downstream unit support engineers as well. It looks at the assay, the different cuts off the crude unit fractionator, and downstream impacts, to confirm compliance with any established IOWs (Integrity Operating Windows). The MOC is initially based on the crude assay, which is of limited value these days. We attempt to obtain a sample in advance in order to get the sample data into the MOC evaluation documentation.
Prior to the MOC – because not everything makes its way to the MOC process, there is a panel that is comprised of both technical and commercial personnel who look at that crude, as well as the value of the crude relative to other crudes being processed or considered for purchase. Crude quality is measured as quality relative to already-approved crude stocks. Operating experience within the company is also of value. Have we run these crudes somewhere else?
Lastly, operating experience with your onsite process chemical supplier is one area where your suppliers can provide real value if they have experience processing this crude elsewhere. The chemical suppliers can have more coverage than the one site with which you are typically dealing. If you are a small refiner, you probably do not have that many crude units in your network. So, leveraging the chemical vendor’s experience and getting some of the feedback from them are very useful parts of this process.
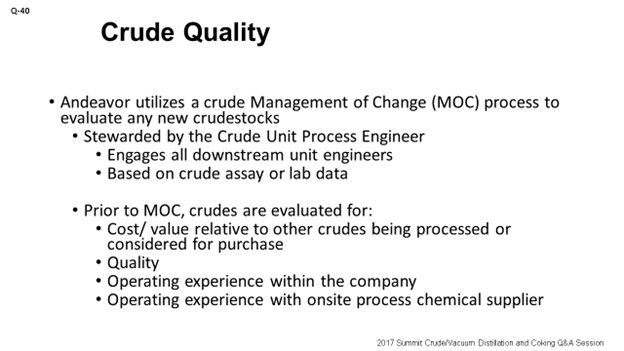
We compare new crudes against other lookalike crudes by reviewing the assay data to see if it compares to something else, we have in our approved MOC database. Like I mentioned earlier, getting samples of the crude before it is delivered is preferred. We have been successful making this happen in the past. We want to try to get enough of the samples so we can run them through our lab, as well as give them to our chemical provider because they can do some stability testing with it in their labs as well. We will look at the normal properties that correspond to IOWs; for example, TAN, sulfur, distillation, chlorides both total and organic – which has become popular lately, pH, asphaltenes, and CCR (Conradson carbon residue). Look at stability based on what crude tanks you think you will be using to store this material. Not all refiners have the luxury of having segregated crude tankage. Looking at stability is an important part of the process of bringing in a new crude.
Test the crude for H2S (hydrogen sulfide); because we have noticed that if you are bringing it in by ship, you need to ensure that you are monitoring the safety of your personnel. If the crude has high H2S content in the vapor space, there may be special procedures you can implement to mitigate that risk. If you can segregate the new crude in tankage, you can also test its quality as delivered because the assay can differ from the as-delivered material. Please refer to the paper I presented at the 2016 Q&A on crude and chloride management for additional information on this topic.1
If the new crude was approved for processing but flagged as being difficult to operate, I recommend running the crude between Tuesday and Thursday. On Monday, people are coming back from the weekend and catching up on email. On Friday, they are looking forward to the weekend, and 9/80 schedules may limit the number of personnel onsite. The weekend is not a good time to implement any sort of major change on a refinery. So, Tuesday to Thursday is the sweet spot. Promote starting the crude rate slowly – maybe 10 to 20% of that MOC limit – to see how the desalters react. See how the fractionator overhead chemistry reacts. What does your pH look like? What do your overhead chlorides look like? What is your caustic injection having to do to maintain the pH? What are your filmers and neutralizing amines doing? All of these should be monitored when you are changing crude slate, and Ross will be talking about that more. Look downstream to see if it is a light crude or a crude slate that will be going lighter than the current slate you are processing. Start looking at your NHT (naphtha hydrotreater). What are the feed tanks looking like for your NHT? Likewise, if it has the slate going heavier, look at the coker feed tank. Look at your coker samples and see what the distillation looks like.
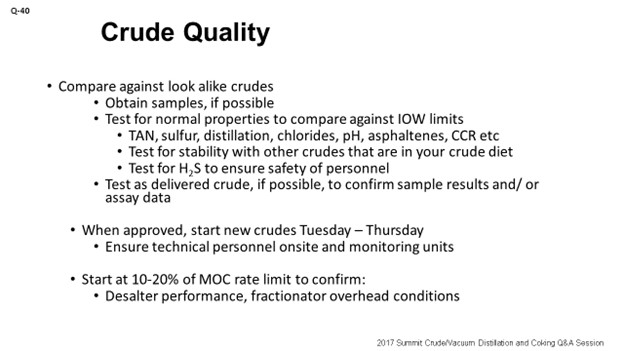
If chlorides were flagged, make sure you are tracking them downstream because those chlorides will partition in your crude unit. They will be going to different parts of the refinery. If everything looks normal or within acceptable ranges, then you could start to consider increasing the crude rate up towards your MOC limit. I suggest increasing rate by 10 to 15%, maybe 20%, of the MOC limit on a shift-by-shift basis, as long as all monitoring is still in place. In the past, we have considered instigating some PI (process information) alarms that will go directly to email or text. If something abnormal comes in, you would get real-time analysis straight to your phone. So, even on an off-hours basis, you can respond and take the appropriate action. Lastly, if that crude did not run at all like the purchaser said it would, please let them know.
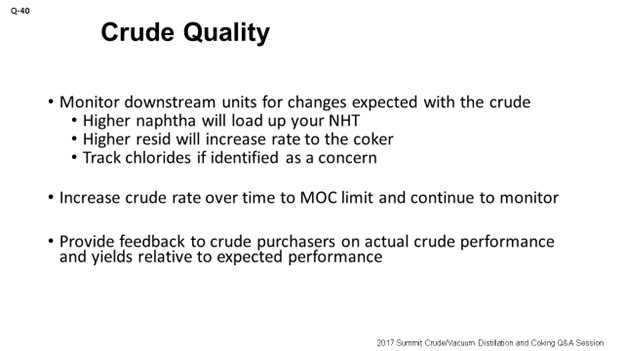
McDANIEL (KP Engineering, LP)
When we both got this question, I realized that I took it as a question of, “What if we are a facility that does not have a lot of tankages for an ideal situation where you can take different crude slates and blend them into one dedicated feed tank, so you have a nice steady die?” Some Operations folks just do not have that capability. What ends up happening is that they have to go from light to heavy and heavy back to light on a regular basis, so it becomes more of a normal routine. What that routine usually consists of is that the Blending, Scheduling, and/or Economics & Planning Groups developing a plan and a schedule and trying to let Operations folks and the unit engineer know the proposed crude slate changes ahead of time. But when that is about to happen, the question is: What should operations really monitor? Often, you are relying mostly on a well-experienced board operator and a unit engineer who will watch and pay attention as that crude slate happens.
Some of the key parameters to consider really depend on the predicted yields you are getting from your LP (linear program) model. That is what you rely on to make adjustments and then notify the downstream units. Attention should then be given to the API and viscosity coming in to determine adjustments to your heater outlet temperatures. It is likely a crude you already run, so you know expected ranges for these parameters. However, adjusting parameters ahead of time will prepare you to handle that crude slate change without having any major shifts.
Flash zone temperatures: If you have an FCC unit, you probably want to watch the crude Concarbon (Conradson carbon) and the metals – in particular, nickel and vanadium – because they can become a major problem if you are not prepared for the temperature change. This is often a very simplistic mode which most people are used to handling. Eric did a better job of addressing this issue for a brand-new crude coming into the facility.
LOGEROT (Prosys Inc.)
A few questions ago, you heard me bring up the subject of procedural automation. I am going to bring it up again because Ross talked about how you want to have your most experienced operator on the board; or, that you would like to have your most experienced operator watch for a few key items. To some extent, you can automate that process as well. So, if you know the two crudes (the crude with which you started and the crude that is coming in next), then you will be relatively sure of what your operating condition and timing will be for the new crude. You can set up your control system to automate that process to ramp up control settings. For instance, look at timers and other process conditions to give you indications of when you will need to start moving process control settings. So, again, if you have an experienced board operator, you can ask that operator how you accomplished that transition last time. Then, based on what that person did, you can start automating the procedure. Talk to your engineers about what you think are the optimum procedures for making the transitions. Again, if you can write down the procedure and what to watch for, you can usually automate the control system.
JORDAN SMITH (NARL Refining LP)
You touched on the idea of the crude not always matching the assay. In those situations, have you ever gone back to the supplier and said, “I did not get value. I did not get the yields” and tried to get any compensation or reimbursement? Or is that just not something that happens?
LÉGARÉ (Andeavor Martinez Refinery)
I will have to respond that the lawyers would not let me say anything about this topic.
THEISS (Marathon Petroleum Corporation)
I think you just have to be careful because you can have a lot of things happen in transit with crude. Right? I mean, they can go over multiple tanks and multiple terminals and pick up impurities that you do not know have mixed into the crude. So, that is a concern. As far as what the assays say or what you think it is, it may translate different as it gets into your plant.
LÉGARÉ (Andeavor Martinez Refinery)
In addition, when we talk about tank farm and segregation, it can play into the crude supplier’s argument. If the crude is mixed with any other crude in your tank farm, then they can claim that the tank farm mixing and blending was the culprit, not the purchased crude.
WARREN LETSZCH (TechnipFMC)
I just want to ask the refiners if you routinely compare the performance of your refinery with what the LP has predicted for that crude to see if you are making the money, you think you will. Is that routine, or is it just something that happens? I may have gotten the impression from the comments you made that at times, the crude oil analysis was not necessarily all that great. I am just wondering whether you guys really look at that on a careful basis and whether you even – for instance, when you run your crude unit – are really making the amount of gasoil that it is saying you are making.
LÉGARÉ (Andeavor Martinez Refinery)
Warren, we do look at that analysis. The crude unit engineer will look at the actual yields compared to the assay yields, compare the two, and then let the crude purchasers know if there is a difference. The crude unit engineer also gets into more detailed analysis around the mass balance on the crude unit and looks at that in real-time as well.
THEISS (Marathon Petroleum Corporation)
We do as well. Some frequency depends on our plant-to-plant personnel and resources, but we do try – as best as we can – to compare LP yields versus actual yields.
McDANIEL (KP Engineering, LP)
I think most clients are looking at both. Right? They are looking at what they actually got from the raw crude coming in – versus what the assay showed, as well as the output or the product yields. Most of our clients do that evaluation.
JEFF ZURLO (Suez Water Technologies & Solutions)
Building on the assay mismatch question, Eric, you mentioned that you would like to get crude samples, whenever possible, to do your own testing. How much lead time do you need to get those samples? Secondly, how successful are you at getting those samples in time to provide useful analysis on that run?
LÉGARÉ (Andeavor Martinez Refinery)
Jeff, thanks for the question. I think the answer is multifaceted. How successful are we in getting samples? I will say that probably less than 50% of the time. It helps, for example, if the Northern California site is looking at it; but sometimes, another refinery in our system has already taken a partial delivery of the cargo. We have worked with some of our crude purchasers to set up relationships to get samples of the crude when it is located at the source. We will send those samples to our labs by Federal Express to ensure they get to us in time to generate lab data. The MOC process can sometimes take up to a week to complete, so there is usually enough time to get the results when we get the samples. The operations engineer works closely with the lab to find out if there was anything abnormal about the crude, and then he/she actually captures it in the MOC paperwork. As an example, one of the pre-startup issues identified was to look at as-delivered qualities, compare them, and then give a green light to move forward or a red light to notify Management.
SHANKAR VAIDYNATHAN (Fluor Enterprises, Inc.)
Are any of the panelists or people from the operating companies in the room using augmented artificial intelligent systems, such as IBM Watson, to schedule and select the opportunity of the optimum crudes?
ROGER METZLER (Baker Hughes, a GE Company)
Certainly, if a refiner decides to blend the dumbbell crude himself, he knows what he is getting into. But what about crudes being received in the pipelines from various terminals and such? I know that over the last few years, there were concerns with some of the dumbbell crude blends for the various spec crudes. Is the industry getting a handle on that issue? Is that somewhat out of control? Are you able to identify the dumbbell crudes and know what you are getting? What is the status of that?
THEISS (Marathon Petroleum Corporation)
Yes. We are going to dive a little into that during a Town Hall discussion here.
SOLOMON (Athlon Solutions)
Yes, and we will talk quite a bit about the effects of the upstream on downstream, as well as opportunity crudes; so, stay-tuned.
CHRISTINA McDOWELL (Andeavor)
Just to put the fear of God into everyone, as they were saying in the beginning: As California goes, so goes the rest of the nation. I get to work on some of the regulatory end of the business, and there are some discussions in the Bay Area about requiring refiners to permit new crudes through the permitting process. I just want to give you a heads-up.
LÉGARÉ (Andeavor Martinez Refinery)
We call Chris “Little Miss Sunshine” at the refinery, by the way. [Laughter]
BILL CATES (Hunt Refining Company)
As a small independent inland, we do not have the luxury of having other styles. We are often trying to look for opportunity crudes. Purchasers are saying, “Okay, six months from now I want to buy this crude.” Normally I hear, “Two days from now, I want to buy this crude.”
THEISS (Marathon Petroleum Corporation)
Our process is similar to what Eric described. It can vary. It can be one to two months ahead of time. Usually, it is not a couple of days. I think we have the right to say “no” in most situations.
JAMIE McDANIELS (Athlon Solutions)
Regarding the H2S in the crude oil that you anticipate receiving into your facilities, do you have a limit on the amount you can accept? How do you mitigate various H2S concerns, depending on the ranges you anticipate coming in with the crude oils?
LÉGARÉ (Andeavor Martinez Refinery)
I will take that. Yes, we do have established limits. We have employed scavengers during the offloading process. As far as mitigations, the safety protocols put the operating personnel in fresh air when they are handling crude.
GAMBOA-ARIZPE (CITGO Refining & Chemicals, LP)
We employ something very similar within CITGO. One of the concerns with the scavengers, as many of you know, is the effect on corrosion downstream in the crude unit, particularly in the naphtha sections. Actually, some of the scavengers – the triazines, a lot of which are amine-based scavengers – tend to degrade and end up affecting that particular section of the tower. So, H2S is an issue, but equally as dangerous is H2S mitigation with scavengers and just knowing what your refinery can manage.
BRAD MASON (NALCO Champion)
Since my peer has a question, I thought I would join the group. I think this is a really good question because it talks of everything that is not on the assay. You guys are very skilled; you are doing the LP modeling. But would you not all like to know all the field experiences with these crudes that are not included? Right? Solids. Does the crude have H2S scavenger you do not know about? What is happening in your overhead? What could happen in your overhead? So, there are number of organic acids that will come through. Would you not like to know about that as well? There is now technology about which you may not be aware. There are things you can do in the field. There are things you can do before you process them, which goes to that question before about whether you even get a sample off the pipeline off the ship. There are some things that you can do beforehand to give you a warning and then you can decide mitigation strategies. Then there are things you can put online that catch the gaps that you thought you covered in all of this screening methodology, which is not perfect. It can then catch an upset control through the DCS or online or with the senior operator and minimize that upset time. Those things exist today. So, if you guys are interested in knowing more, come see me at the NALCO Champion booth at lunch.
JOSH WOOD (LyondellBasell Industries)
I have a couple of questions. The first question is: For the new crudes you are asked to evaluate, what percentage would you say you have actually turned down? Just a rough number: 50%? 80%? 90%? Or, do you mostly run all the crudes that make sense, economically?
My second question has to do with what, I think, Eric, alluded to earlier: that when you bring in a new crude, you do not exceed the rate that you put in your MOC. So, I am just curious how you are able to define that rate, given the multiple crudes that you could potentially be processing and knowing that certain properties change with different blends. It just seems like that has to be a challenging to specify. I am just wondering if you do specify that, do you ever hit that rate, realize there is no constraint, and then go back to the MOC and change the rate limit you would then be able to run with the new crude?
LÉGARÉ (Andeavor Martinez Refinery)
Great questions. The first question was: How many crudes do we turn down? I guess it would be not too many. Right? [Laughter] But it does happen, and it has happened. By the time it gets to the technical folks, it has already passed through a certain number of screens. The Commercial folks already bought off on it before it got too Technical. It has not happened very often, but we have had a few situations where we have said no.
As far as starting a new crude, I think what I said was somewhere between 10 and 20% of the MOC limit, to start off. That amount will be based on what our Planning Department thinks they have in the tank, with regard to the ratio of the new crude versus whatever we had in the heel. We do get alignment with Operations and share that information at Production meetings, so everyone is totally aligned on what we are doing. There have been times where the response by the refinery definitely told us we were running more than the 10 to 20%. That data got fed directly back to the Planning Department. They will then cut back on that tank and bring in another tank where we know the crude and quality of what we will be processing.
The last question was about going back and changing the MOC limit, if everything was fine at the MOC limit. That has also happened in the past.
JEFF ZURLO (Suez Water Technologies & Solutions)
I have a follow-up comment to the gentleman who asked the question about how many crude oils are turned down. Unless it is a brand-new crude, once it is out of the ground, someone somewhere is going to buy it and process it. So, to Eric’s point about the industry experience, he is right that knowing the industry experience is important.
Additionally, remember that the properties of the new crude are important in and of themselves. However, you also need to consider the blended mixture that will be charged to the crude unit, because it is the combination of the crude properties and the mixture’s blend which will impact the unit’s operation. The blend of all of the crude oils, plus other fluids (such as slop oils and purchased intermediates), may impact downstream refinery operations differently than the effects of utilizing the single crude oil itself. So, it is vital to know what is being blended with that new crude to anticipate the potential issues and corrective actions.
GAMBOA-ARIZPE (CITGO Refining & Chemicals, LP)
Yes. Some of the flexibility for addressing that question also depends on the tankage capabilities of a refinery. So, it is fairly obvious that if you have many tanks, you will have more flexibility to absorb crudes that you otherwise would not take. If you could say, “Okay, I am going to dilute it over time with a diet with which I am familiar,” then obviously the refiners will be all over the map when it comes to that flexibility. Some refiners have plenty of tanks; some wish they had more tanks. But ultimately, the crude supply itself, like Jeff Zurlo said, once it is extracted from the ground, will be bought by someone. It is just a matter of ensuring that you can manage it at your facility. Those with more tanks have more flexibility to do so, if it is new to them.
LÉGARÉ (Andeavor Martinez Refinery)
I was going to say it sounded like Bill’s when he picks up those crudes at the end if no one else wants them. (Laughter)
BILL CATES (Hunt Refining Company)
Yes, we need more than one tank.
ERIC LÉGARÉ (Andeavor Martinez Refinery)
Andeavor utilizes the crude MOC process to identify and review any possible hazards associated with any new crude being proposed for the refinery. The crude unit engineer stewards the technical review and engages the downstream unit process engineers to review it from their unit’s perspective. Prior to the MOC, the crude assay is reviewed by a multidiscipline panel which decides whether it is acceptable for purchase. Factors that can influence the decision include:
-
Cost/value relative to other crudes being processed or considered for purchase,
-
Crude quality,
-
Operating experience within the company, and/or
-
Operating experience with your onsite process chemical supplier.
Crude quality should be compared against similar crudes already approved for processing at the refinery. Obtain crude samples, when possible, to confirm the properties listed in the assay. Ensure that sufficient sample volume (three to five quarts is recommended) to pre-test for crude compatibility with other crudes in your tank farm. If the ship is delivered over water, confirm the H2S content in the sample to ensure that the H2S content is below your company’s threshold for wharf operations. If not, notify the appropriate Operations personnel to employ the proper safety mitigations.
Ensure that any anomalies in the assay are flagged in the MOC. For example, high total and/or organic chlorides in the assay should be confirmed by testing a sample during the offloading process to confirm that the level of organic chlorides is not higher than expected. Asphaltene stabilizers should be injected if crude stability is a concern. Test the delivered crude prior to feeding it to the crude unit if your crude tankage is sufficient. This step allows you to confirm that the delivered crude matches the assay and/or the samples tested. The delivered crude should be within your operating limits (TAN, sulfur, distillation, asphaltenes, total and non-extractable chlorides, and pH).
Troublesome crudes can be ramped up over time, if your tankage allows. The crude should start at 10 to 20% of the MOC limit and increase in 10 to 15% increments on a shift-by-shift basis, if downstream data supports it. Look at desalter performance (amps, brine quality, and salt removal efficiency), crude fractionator overhead pH, chlorides, NH3, etc. as an indication of crude performance. Is your caustic injection having to be increased to your crude unit to address a drop in overhead pH? Was that expected based on the crude assay? Monitor the dew point to salt point margin in your crude fractionator overhead system to ensure that sufficient temperature margins are being maintained relative to your defined targets or IOWs.
Downstream units can look for higher coker feed rate due to a heavier crude slate or higher naphtha production if the slate is lighter. High total and/or non-extractable chlorides in the crude should be monitored in downstream hydrotreaters to confirm how they partitioned in the crude fractionator. Monitor cetane number in the product diesel, if that was identified as a potential problem in the assay.
New opportunity crudes should start to feed the crude unit on Tuesday through Thursday to ensure proper operational and technical support for the new crude as it makes its way through the refinery. It is also a good practice to provide feedback to your crude purchasers, if there are any noticeable differences in actual versus predicted unit performance for the crude being processed.
The following slides are from the presentation I gave during the Crude & Coking P&P session of the 2016 AFPM Q&A.
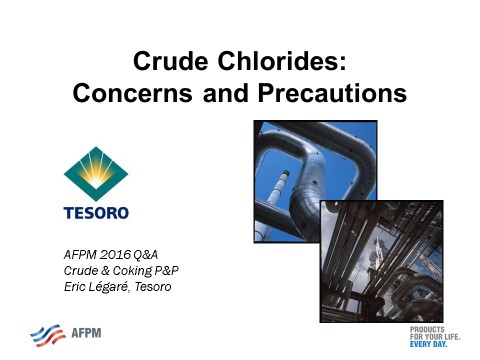
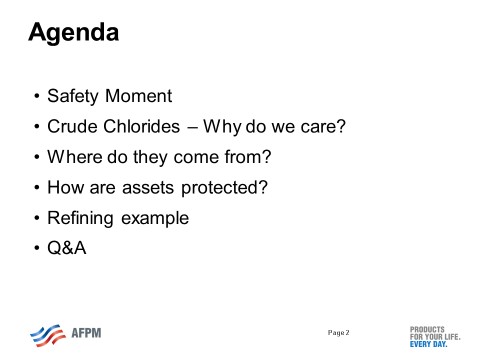
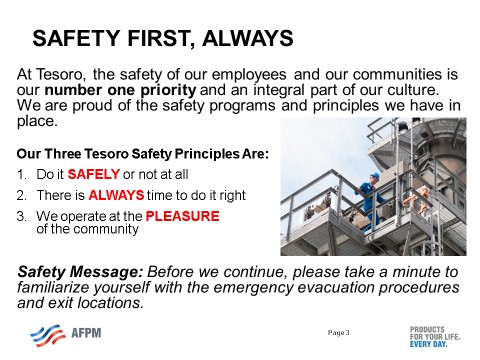
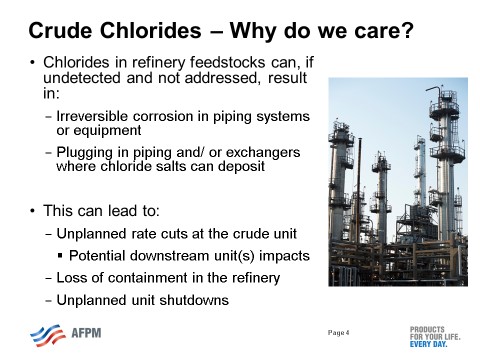
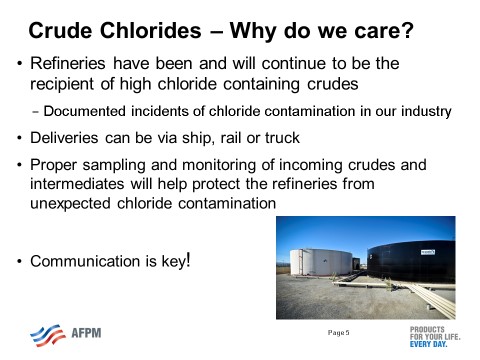
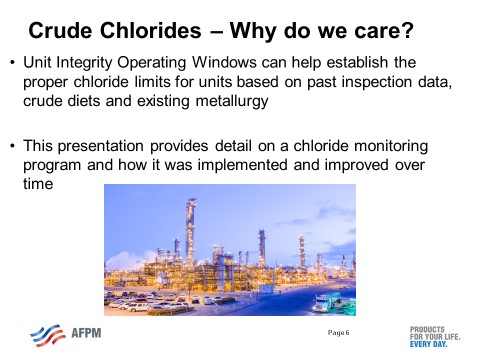
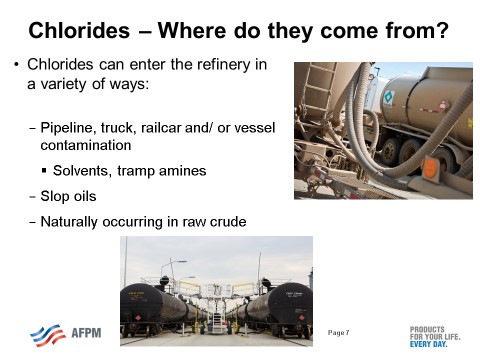
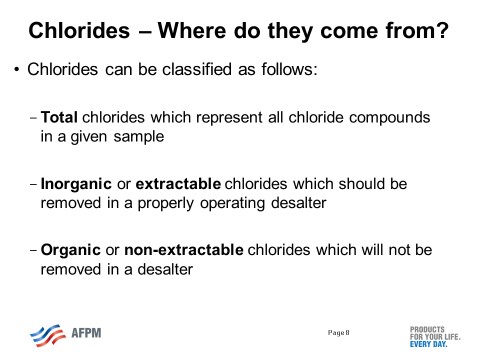

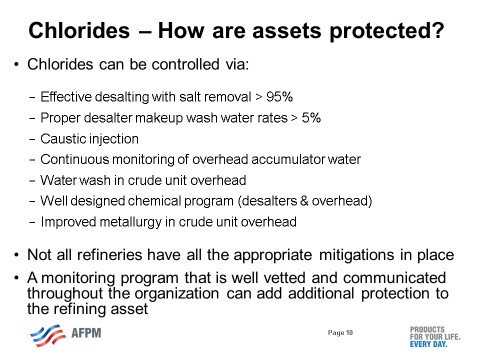
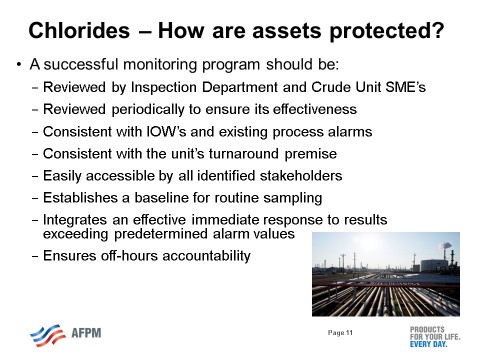
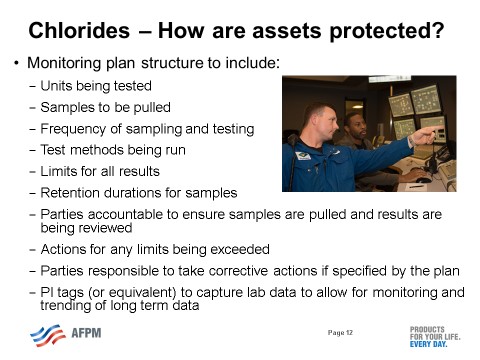
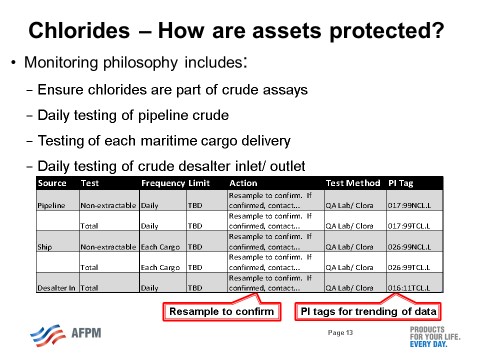
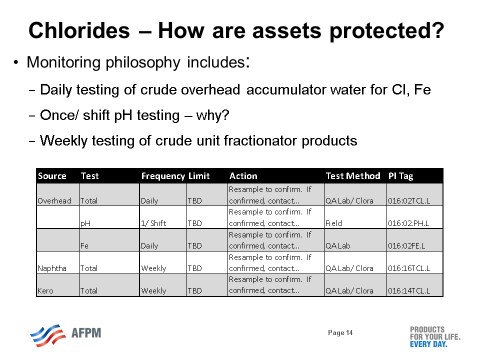
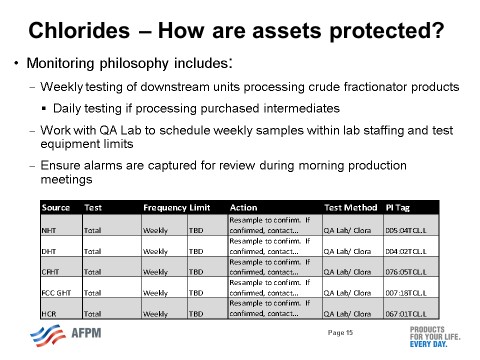
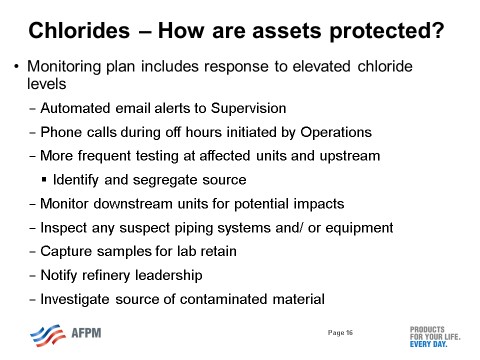
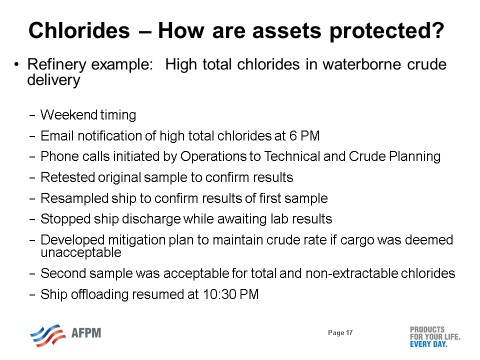
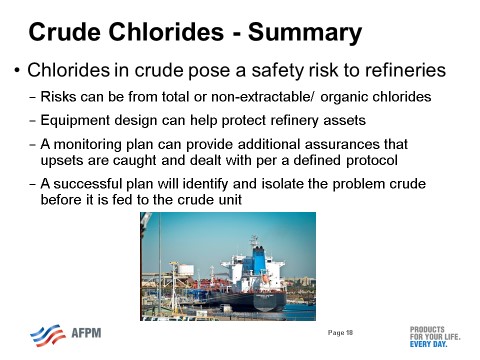
W. ROSS McDANIEL (KP Engineering)
This process can be as detailed or be as simple as your facility deems worthy; however, I do not believe many have an intricate system. Operations usually relies on its Economics & Planning and Blending departments to notify the unit engineer and Operations of the expected crude and when it will make a dramatic change. This department predicts product yields and desired cut point changes. This information is usually given to experienced board operators who know what changes they should make to adjust for a lighter crude slate or, say, a heavier sour crude slate.
Some key parameters to monitor are the following:
-
Predicted yields;
-
API, viscosity, and salt content in and out of the desalters;
-
TAN (total acid number) and sulfur in preflash, atmospheric, and vacuum towers;
-
Heater outlet and flash zone temperatures on preflash, atmospheric, and vacuum towers; and,
-
Crude carbon residue and metals (nickel and vanadium) for facilities with catalytic cracking units (FCCU).
Also, assuming the crudes are compatible and tankage is available, to avoid crude capacity limits in either the overhead or bottoms circuits, many refineries mix crudes to produce a single crude blend within an acceptable API range.
CHRIS CLAESEN (NALCO Champion)
A newly introduced crude or blend requires an MOC and detailed evaluation of the crude oil assay plus other proprietary techniques that predict effects on wastewater, desalting, corrosion, and fouling. The MOC involves all refinery units, including tank farm, processing units, and wastewater.
DENNIS HAYNES (NALCO Champion)
Some key properties to monitor – besides the basics of API and salt concentration – are viscosity, TAN, and solids concentration. There are some locations that also periodically test for amines, relative asphaltene stability, phosphorus in crude, and extractable acidity. One key process condition is to monitor the pH of the desalter wash water compared to effluent brine to see what chemistries are being extracted from crude (specifically, bases or acids). Other process conditions to monitor are crude conductivity in the desalter compared to dehydration.
RAÚL ROMERO (NALCO Champion)
A typical refinery approach to newly introduced crude or blend requires an MOC and detailed evaluation of the crude oil assay through specific computing tools where crude cut yields and properties are assessed and compared to different unit constraints to allow a safe and profitable run of the new blend. General feedback from the industry is also considered.
Analysis of impacts on desalting, corrosion, fouling, and the wastewater system should be also considered as part of the MOC. This analysis starts from crude reception and tankage covering process units and wastewater treatment facilities. Some of the properties and process conditions to check on new crude should include:
-
Base Sediment & Water (BS&W)/Filterable Solids: This should be considered as one “operating window” to increase operation reliability of the CDU (crude distillation unit) since it impacts on desalter operation (stable rag layer emulsions), slop generation, and CDU and downstream units fouling (including delayed coker furnaces). BS&W/filterable solids should be measured not only on crude reception, but also on crude feed to CDU.
-
New Crude and Potential Crude Blending Electrical Conductivity: Conductivity can have some relation with high metals and TAN. High conductivity crudes increase desalter amperages and decrease grid voltages, which deteriorate electrical field and water separation.
-
Organic Acids (like acetic acid) and Trap Amines Present in the Crude from Upstream Treatments: Acids can make desalted crude caustic injection less effective for corrosion control and also generate higher variability on overhead condensate pH control. Trap amines, generally from H2S scavengers, increase desalter brine pH making emulsions more stable and can increase salt deposit potential in the main fractionator. Both acids and trap amines increase COD (chemical oxygen demand) on effluent brine.
-
Non-Desaltable Salts: These are more difficult to detect with traditional lab test methods, and they generate more HCl (hydrochloric acid) on the crude overhead system.
-
Organic Halogen Solvent: This solvent can also be present in crude feed if a new source is considered. It can affect both CDU overhead systems and, basically, naphtha HTs forming NH4Cl (ammonium chloride).
-
Crude Mix Compatibility: Asphaltene stability (not only C6-7 insoluble) is a key parameter to track fouling on crude preheat trains and furnaces (even on convection sections).
-
Nitrogen (N) and Sulfur (S) Content: Both its content and proportion can affect SWS units’ performance. If stripped water is used as desalter wash water, a higher content of SH2 and NH3 will affect the CDU main fractionator and overhead system fouling. It also impacts wash water requirements for the hydrotreater, FCCU, and coker light-end unit to keep ammonium bisulfide and chloride concentrations under control.