Question 40: Has anyone experienced high chloride levels in off gases from the lock hopper of a pressurized regenerator? What are the consequences of the high levels (i.e. fouled burner tips)? What are ways to mitigate the problem?
Greg Harbison (Marathon Petroleum)
Marathon has not experienced any high hydrogen chloride concentrations in Lock Hopper off gases from the two CycleMax regenerators that we operate. We have also not experienced problems with fouled burner tips due to high hydrogen chloride in the fuel gas to a heater.
We recover as much hydrogen as feasible from the Lock Hopper off gas. We route the Lock Hopper off gas to the net gas separation section of the Platformer, recovering most of the hydrogen. Thus, only a small portion of the off gas is routed to the fuel gas stream, and the resultant hydrogen chloride concentration in the combined fuel gas stream is low. In our units, this has not led to any burner tip fouling. We believe this to be a key factor in avoiding problems in the downstream fuel gas system.
Our first Cyclemax unit is a revamped semi-regen stacked reactor system that was originally intended to be a CCR Platformer at our Detroit refinery. This unit been in operation for over 5 years and there have been no fouling issues with heater burner tips. Our second unit is a CycleMax on Marathon’s latest Platformer in Garyville. This unit has operated for less than 9 months, and there have been no issues with high HCl in the Lock Hopper off gas. The HCl concentrations in the net gas and booster gas to the Lock Hopper are usually in the 2 to 4 ppm range. The combination of low HCl and the recovery of most of the Lock Hopper hydrogen in the separation (recontacting) system have not caused Marathon problems with burner tip fouling.
We also use a chloride guard bed on the net gas hydrogen stream leaving the unit to remove HCl and minimize the potential for downstream chloride related fouling. Overall, as in the case of burner tip fouling, Marathon has had no experience with fouling in other equipment due to high hydrogen chloride content in the Lock Hopper off gas in our pressurized regenerator systems.
We find that maintaining any HCl in the vapor phase is beneficial to preventing fouling. Insulating and/or heat tracing fuel gas lines will help minimize the impact of HCl related fouling in the fuel gas system. Using a source of hydrogen chloride free gas to the Lock Hopper would be helpful as well.
Although not specifically queried, our atmospheric CCR units do not experience burner tip fouling from the lock hopper vent gases either. This stream enters the heater directly with its own nozzle, not into the fuel gas system at the unit.
John Clower (Chevron)
Lock hopper off gas from a pressurized style regeneration system is hydrogen produced in the reactor section. The net hydrogen takeoff from the reactor section to the regeneration section may come upstream or downstream of the net hydrogen chloride treater. If corrosion or fouling issues exists in the regeneration hydrogen section, a refiner should consider moving the net hydrogen takeoff downstream of the chloride treater.
The function of lock hopper gas is to facilitate the changing operating pressure at the lock hopper from regeneration tower pressure to reactor 1 pressure.
The hydrogen off gas from the lock hopper will either be directed back to the separator or to the fuel gas system. This gas may contain as much as 1+ ppm chloride (depending on lock hopper conditions and hydrogen source) and some catalyst dust.
High chlorides in the fuel gas can cause fouling of mesh blankets in knock out drums, and corrosion of SS burner tips leading to cracks.
If the lock hopper of gas is the source of fouling or corrosion, mitigations include:
•Route the hydrogen off gas away from the fuel gas system, incurring the cost of compression but recovering a hydrogen rich stream •Adding a chloride guard bed to the lock hopper gas that passes to the fuel gas system
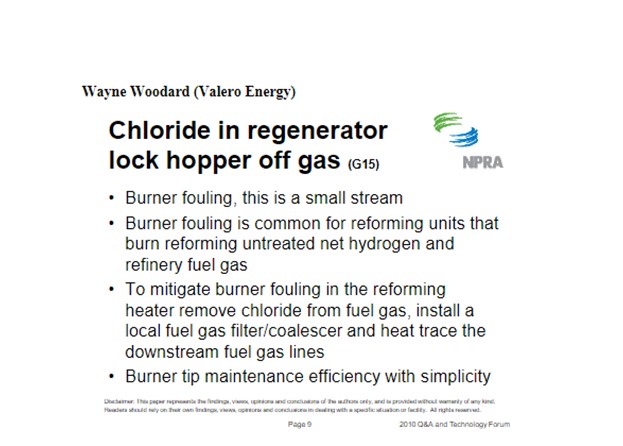