Question 40: Economic drivers dictate the need to process more difficult feedstocks, such as cracked stocks and diesel feeds with high distillation endpoints. What are typical guidelines regarding minimum hydrogen partial pressure for a given feedstock? (High-level answer with details will be discussed in the Hydroprocessing P&P.)
LIOLIOS (DuPont Clean Technologies)
We are treating feedstocks with higher endpoints and greater volumes of cracked feedstocks. Certainly, you are faced with refractory sulfur species that are harder organic nitrogen compounds, which then inhibits sulfur removal and polyaromatics. Higher hydrogen partial pressures are required to achieve diesel specifications and maximize catalyst life in a conventional treater.
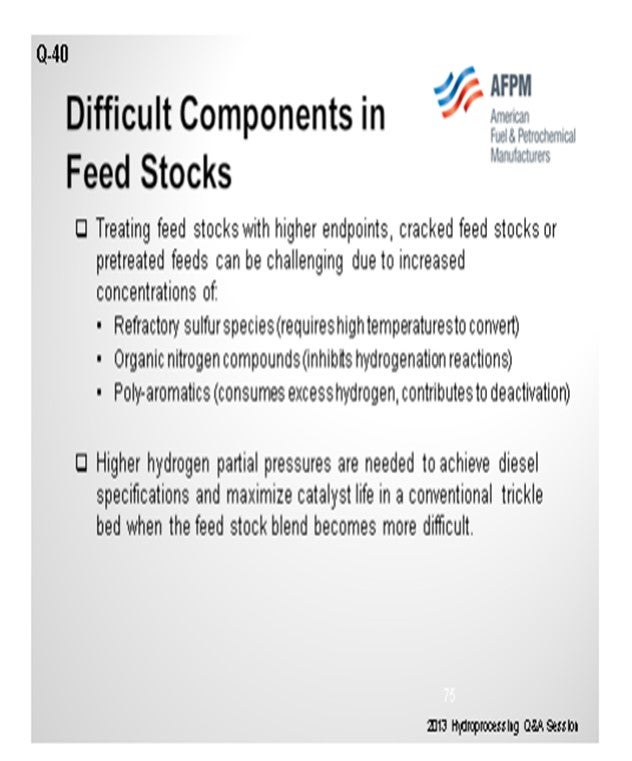
The next slide shows some typical operating pressures on straight-run and cracked stocks, as well as typical hydrogen uptake. It is always important when you talk about hydrogen partial pressure that you ground yourself in what the meaning of hydrogen availability: the amount of hydrogen gas actually in the bed, which is makeup, recycle, and quench divided by the chemical hydrogen consumption.
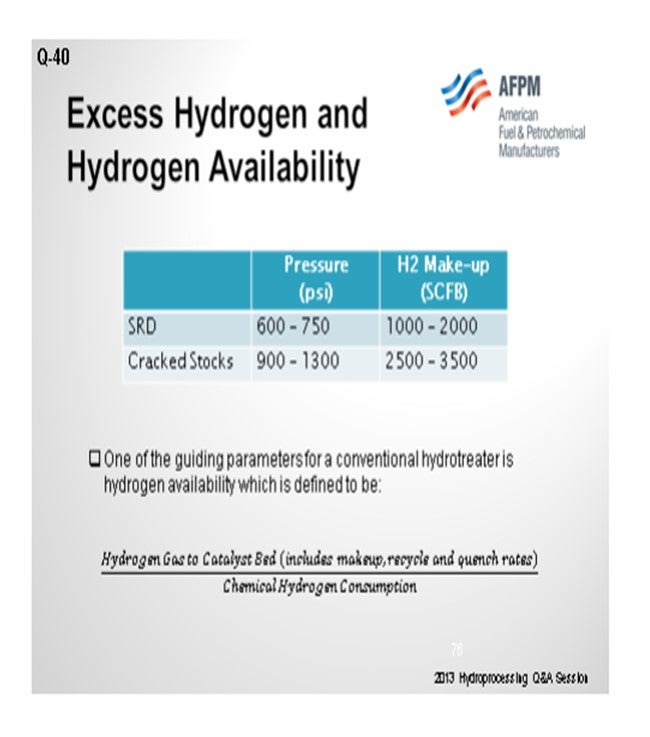
The next slide shows some average ranges of hydrogen availability: the ratio on different feedstocks from straight run through cracked feedstocks to blends of the different ones, basically ranging anywhere from 2:1 up to 5:1 or greater on the more difficult feedstocks. So how do you get to higher hydrogen availability in an existing unit? Certainly, by increasing the purity of your makeup hydrogen, makeup gas rate, and purge rates. Then, if you have the availability, increase the hydrogen recycle rate. Higher pressures may be required. Of course, combinations of different catalyst systems (such as nickel molybdenum and cobalt molybdenum), at the higher pressures to remove nitrogen, will most likely be needed as they inhibit the refractory sulfur removal.
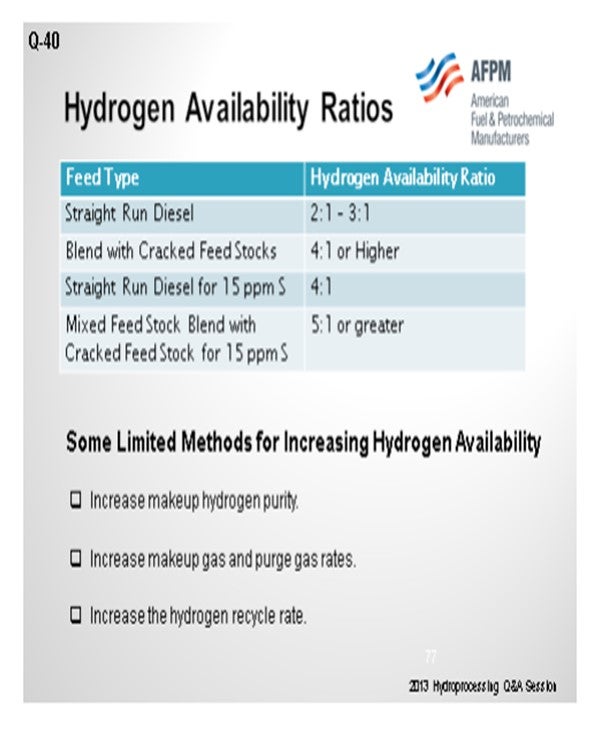
As you get farther along on whether or not to revamp, you will want to consider additional new reactors, new recycle compressors, and makeup gas compressors. We have a typical conventional unit revamp where you put in an additional reactor upstream of the older reactor. It generally involves an additional hydrogen recycle compressor and related treating of H2S before the recycle compressor.
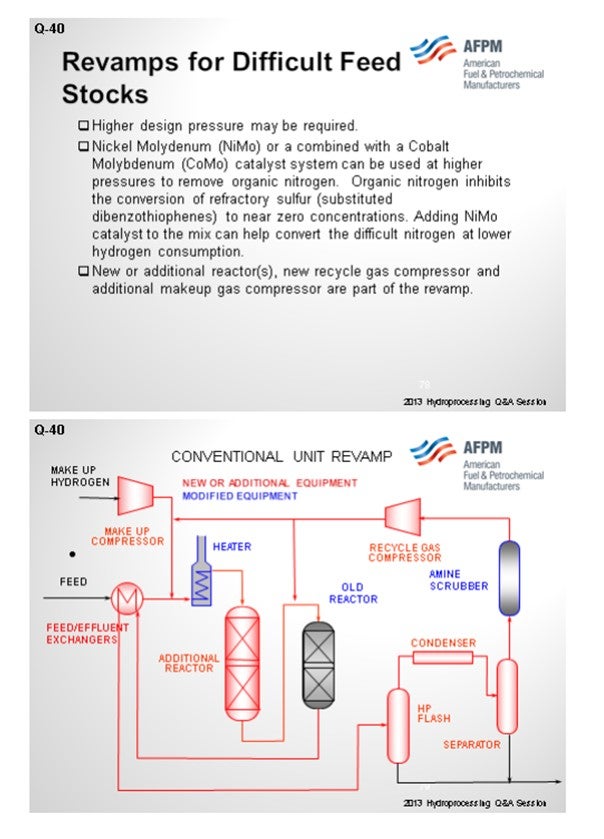
An alternative revamp scenario is using liquid hydrocarbon processing, IsoTherming®, which can provide some ways of getting to this in, hopefully, a more cost-effective revamp. The concept is that you would add a standalone reactor and a heater upstream of the existing trickle bed reactor. You can take out some of the simpler reactions and some of the harder sulfurs in a liquid phase reactor and not have to affect the recycle gas compressor or recycle gas treaters. Many of the studies we have done show this to be an economically viable revamp alternative.
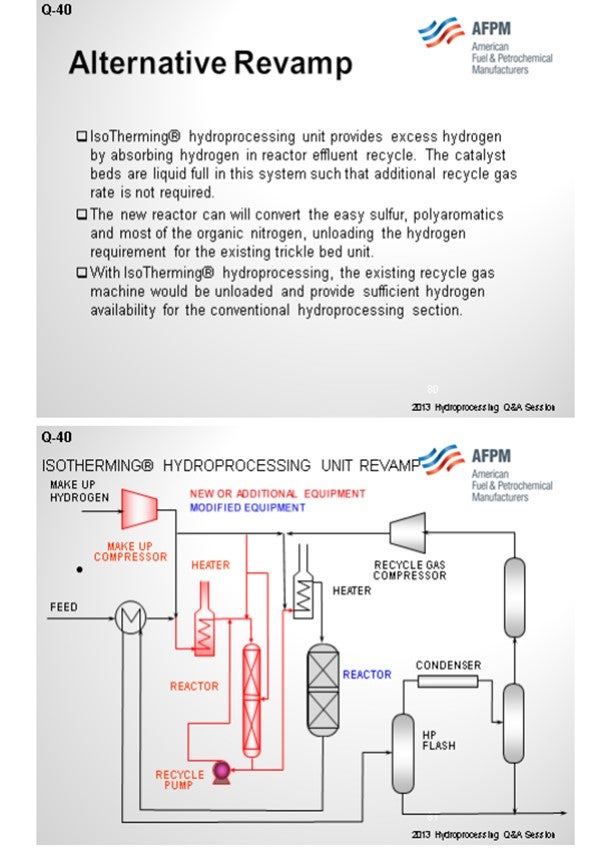
WATKINS [Advanced Refining Technologies (ART)]
In most units, hydrogen partial pressure has a moderate impact for temperature on your weighted average bed temperature. ULSD definitely has a large impact, so we will want to make sure that partial pressure is fairly high. I know that is not necessarily a quantitative answer. But as you said, it also has an impact on HDN. So, if you are allowing your partial pressures to drop, then it will have an impact on HDN, which will ultimately impact pre-ULSD; and also, for aromatics and PNA saturation, if you are using that for anything, in terms of volume swell or meeting targets for cetane and things like that.
It will also have an impact on fouling. If you are starting to run out of hydrogen and your partial pressure begins to drop, your fouling rate will go up. How low do you want that to go? The other question is: How short would you like your cycle to be? A rule of thumb is that cycle length is proportional to hydrogen to partial pressure, so it is one over that to a power. The range is generally two to three. You can see it has a decent impact, which is determined by reactor pressure at the inlets, total pressure, makeup hydrogen purity, and recycled gas rate. As Glenn asked, “How much can you bleed, and what is the degree of feed vaporization?” If you have a unit that was fairly heavy on the frontend and now you decide to feed co-processed naphtha in your ULSD unit, expect your hydrogen partial pressure to drop; because you have now created quite a bit more gas in your unit, and it will possibly have an impact on your ULSD.
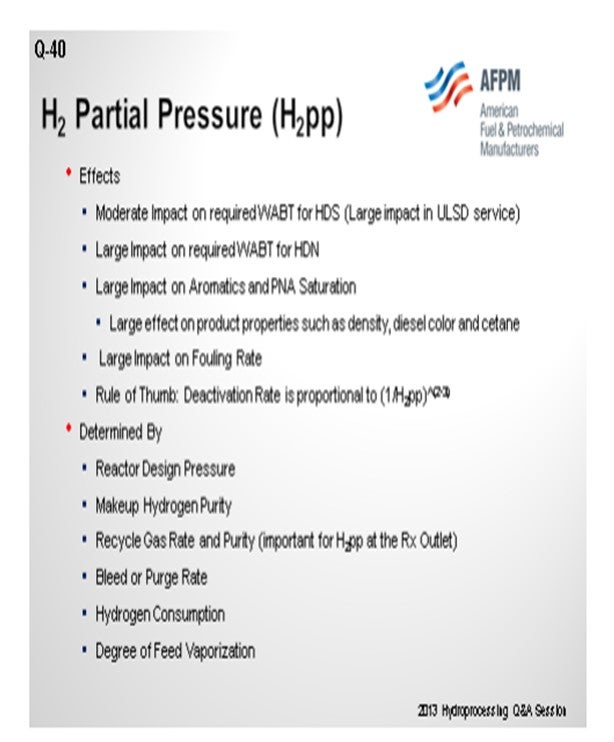
The information on this slide gives you a feel for what the impact may be. First, we try to hold imminent pressure constant, and then we vary makeup purity. If you have a unit that starts at the bottom of the slide with 80% purity on your makeup, you can see that it has a fairly low outlet hydrogen pressure for this unit; so maybe you will expect a two-year cycle. If you can actually get up to using fairly high purity hydrogen, like 95 to 100%, you can see quite a big impact on your process, which might gain you 12 more months. So that might be important. The reason why it is going to do that is that it will give you a much lower start-of-run temperature. So that will extend your cycle length as much lowering your deactivation rate.
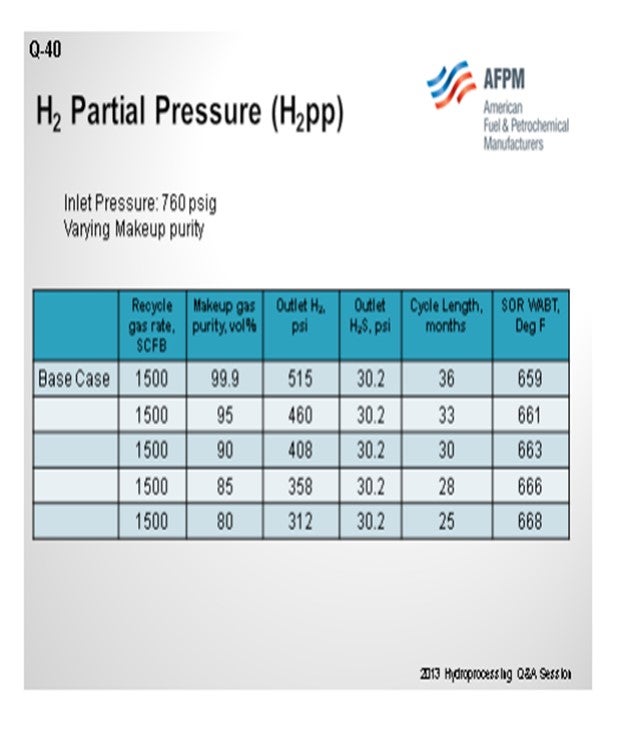
The next chart demonstrates another way to look at that same situation. If you work down the chart, you see that a unit that needs reduction of its recycle rate because of issues with hydraulics going through it. Every time you decrease that recycle rate; you will actually start killing off cycle length. So, you will have to raise the temperature in order to compensate for reduced hydrogen partial pressure, resulting in a higher fouling rate. So, in this case, going from 800 to 1500 scfb (in other words, doubling your recycled gas) will, again, give you your biggest bang for the buck. For this example, your cycle will potentially be 12 to 18 months. There is no true good answer of what is the lowest. It is really what you are willing to sacrifice, in terms of cycle.
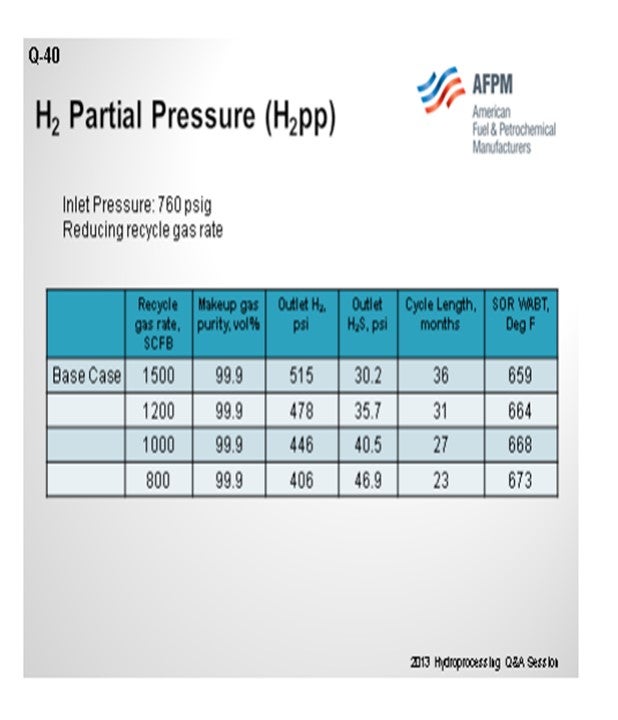
SIVADASAN (UOP LLC, A Honeywell Company)
The hydrogen partial pressure is mainly determined by the total pressure of the reactor system, makeup gas, recycled gas, hydrogen purity, and gas-to-oil ratio. All of these factors have a big effect on the cycle length of the unit. Recommending a minimum hydrogen partial pressure is difficult because it must depend on how much the refinery is going to forego on the cycle length.

MUKESH PATEL (Reliance Industries Ltd.)
What is the revamp scheme that was mentioned? Has anyone has gone for the parallel reactors to reduce that ∆P, split the feed, and then treat the feed?
R.E. “ED” PALMER (Wood Group Mustang, Inc.)
Yes, that has been done. There are some issues, as far as distribution, because you have two-phased flows. Ideally, you like to split the flow between two sets of combined feed exchangers, and maybe split the heater in two to go to two parallel passes or then to the heater; but that has been done.
JEFF JOHNS (Chevron Products Company)
You have all suggested that the choice of hydrogen partial pressure tends to be more of an economic one. Brian said that fouling was proportional to the inverse of the second or third power of the partial pressure ratio. I am interested in whether you have observed that the fouling can fall off a cliff if the partial pressure gets seriously way too low. Could you suggest a methodology on how you might determine that before you fall off that cliff?
SHARPE (Flint Hills Resources, LP)
I keep asking catalyst vendors that question, and they say, “It is complicated.”
JEFF JOHNS (Chevron Products Company)
That is why we are asking you.
SHARPE (Flint Hills Resources, LP)
I am working on it, but I have not yet figured it out. It is one of my current projects.
ALAN KERN (APC Performance, LLC)
I have a very similar question, but maybe once you are above the cliff. The hydrocracker I worked on for several years was maintained with one gas oil ratio for many different feeds. As long as they were above it, the wisdom was that coking would be okay. But based on the statements you have all made, it sounds like there is actually the possibility of a lot of optimization potential that can be seen when looking more closely at that gas oil ratio, depending on what you are trying to monitor, including your feed and cycle length. Would you agree? I would appreciate your feedback.
SIVADASAN (UOP LLC, A Honeywell Company)
I will agree with that rationale because they would assume there are some excess hydrogen numbers that we generally follow, like four or five times the hydrogen consumption. So, if you have more than that, you can optimize your gas oil ratio.
WATKINS [Advanced Refining Technologies (ART)]
I agree with that also. Depending on your gas oil hydrotreater, if it is a really high-pressure unit and you already have 90% hydrogen and a fairly high partial pressure, then maybe going to 95% hydrogen will not give you the economic return. Perhaps it will cost more to do that. Certainly on low-pressure units, such as low-pressure ULSD units, the ability to add more hydrogen will give you incremental benefits, in terms of cycle. That is really where it plays into effect. But usually for your high horsepower units, if you have already met a minimum requirement, adding more hydrogen will not give you any more performance.
ALAN KERN (APC Performance, LLC)
What I am hearing is there is not really a cliff on the high end. There is almost no point at which you have too much excess hydrogen. If it were more, it would not help your cycle length.
WATKINS [Advanced Refining Technologies (ART)]
Yes. On the high end, you may not get any benefit from adding more hydrogen. If you are already at four or five times what you think you will need, then adding six is just extra money that may not result in any benefit. If it is a low-pressure unit, you could probably get some benefit from that. I do not know your specifics.
VICHAILAK (Marathon Petroleum Corporation)
The concern of adding more gas is also with ∆P. If you have too much gas and then ∆P goes too high, that may not be good either. We only recommend a minimum hydrogen availability of 4:1.
GLENN LIOLIOS (DuPont Clean Technologies)
Treating diesel with higher endpoint, cracked feedstocks, or pre-treated feeds can be challenging due to the increased concentrations of refractory sulfur species, organic nitrogen species, polyaromatics, and contaminants such as silica and metals. Refiners generally recognize the need for increased hydrogen partial pressure with difficult feedstocks both to achieve the desired diesel product specifications and maximize catalyst life.
A distillate hydrotreater processing primarily straight-run diesel (SRD) from the crude unit might operate at 600 to 750 psi with a hydrogen recirculation rate of 1000 to 2000 scfb. Comparatively, a unit processing a feedstock with 50% cracked stocks (such as light coker gas oil, light cycle oil, or hydrocracked diesel product) could operate at pressure between at 900 and 1300 psi with a hydrogen recirculation rate of 2500 to 3500 scfb.
Refiners often reference hydrogen requirement as the ratio of hydrogen supply to hydrogen consumed. Hydrogen supply is the sum of the makeup gas, the recycle gas, and the quench gas for each bed, whereas hydrogen consumed is the chemical hydrogen consumption in that bed. When processing feed blends without cracked stocks, a typical target ratio is around 2/1 to 3/1. For high levels of cracked feedstocks, this ratio is increased to a typical 4/1 or higher. This ratio is commonly termed as the hydrogen availability. The required hydrogen availability is very dependent upon the feedstock and the product specifications. For ULSD applications, the minimum ratios are increased to 4.0 and 5.0 or greater for straight-run diesel and mixed feeds with cracked stocks.
Sometimes it is possible to increase the hydrogen availability for existing units – either through using higher purity makeup hydrogen, increasing the makeup gas rate, or increasing the recycle hydrogen rate, all of which result in higher operating costs.
For more severe feedstocks, a unit revamp at higher pressure may be required. A unit revamp could require additional reactor capacity, increased recycle gas compressor head and flow rates, and a new high-pressure amine scrubber. Higher design pressures allow the use of catalyst systems that are more suited to a reaction pathway for removing difficult sulfur species. Often organic nitrogen covers the catalyst sites and has to be removed before the difficult sulfur species can be converted to very low levels.
Nickel molybdenum (NiMo) catalyst typically performs better than cobalt molybdenum (CoMo) for removing organic nitrogen at 1000+ psi. (The use of NiMo catalyst also requires higher hydrogen partial pressure for stability to achieve an acceptable life.) Sometimes the catalyst types are loaded to target certain reactions. After the typical guard/grading catalysts, NiMo is used to reduce the nitrogen to near zero levels. CoMo is then used to convert the difficult substituted sulfur species in subsequent catalyst beds.
Generally, revamping a trickle bed unit involves adding a new trickle bed reactor, a new recycle gas machine, increased hydrogen makeup rates, etc. (See Figure 1).
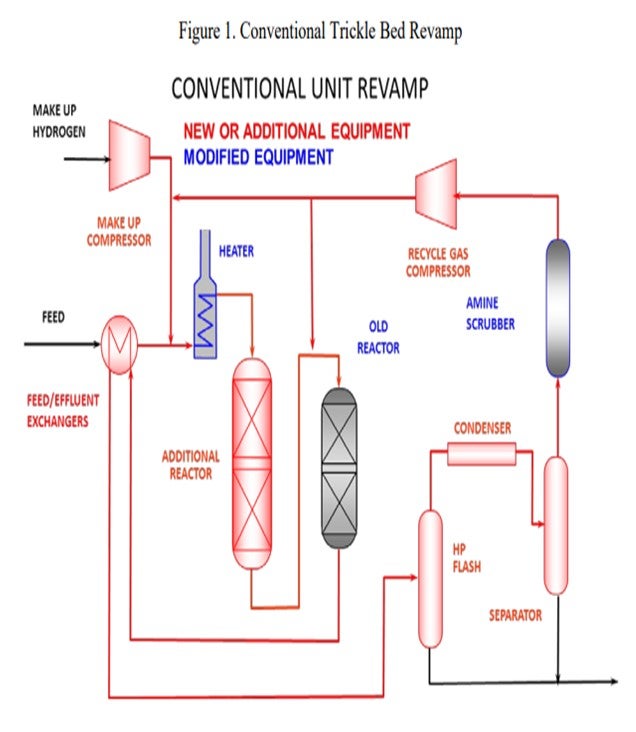
However, there is an alternative. A high-pressure IsoTherming® hydroprocessing reactor licensed by DuPont™ Sustainable Solutions can be installed and does not require a new recycle gas compressor (Figure 2). The IsoTherming® hydrotreating process is a liquid full catalyst system that recycles hydrotreated reactor effluent with absorbed hydrogen. The recycled oil delivers dissolved excess hydrogen to the reactor system by pumping reactor effluent that has been saturated with hydrogen. Hydrogen availability for the IsoTherming® hydroprocessing reactor is determined by the liquid recycle rate, hydrogen solubility in the oil, and the number of beds in the reactor. Makeup hydrogen is injected with the feed and mixed with the effluent from each bed to replenish the hydrogen consumed in the previous bed. This way the faster reactions (i.e., easy sulfur, olefins, polyaromatics, and most of the nitrogen) can be converted in the IsoTherming® hydroprocessing reactor. Adding the IsoTherming® hydroprocessing reactor provides sufficient hydrogen availability and undertakes the additional hydrogen consumption required due to an anticipated change in feedstock. The increased hydrogen consumption is completed in the IsoTherming® hydroprocessing reactor such that the existing trickle bed reactor does not require additional hydrogen recycle rate. This allows the conventional trickle bed reactor to operate at conditions similar to the hydrogen partial pressure enjoyed with the less difficult feedstock. As a result, the reactor product meets the distillate specification, and the reaction system maintains a similar catalyst deactivation rate. Hence, additional hydrogen availability may not be required such that the existing recycle gas compressor has sufficient capacity.
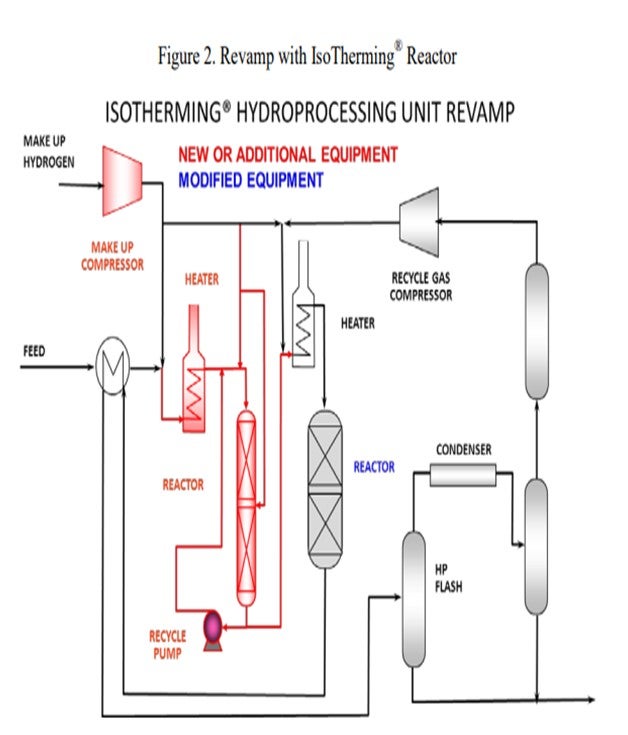
BRIAN WATKINS [Advanced Refining Technologies (ART)]
The question of “What is the minimum allowable H2 partial pressure for a hydrotreater?” has been asked frequently. The general answer is: It depends on how much the refiner is willing to sacrifice in cycle length. As background for this discussion, H2 partial pressure is set by the following parameters:
• Reactor design pressure,
• Makeup hydrogen purity,
• Recycle gas rate and purity,
• Bleed rate,
• Hydrogen consumption, and
• Degree of feed vaporization.
Typically, the reactor is operated at a constant inlet pressure near the design value and with a relatively stable feed quality. The hydrogen consumption and degree of feed vaporization are also essentially constant. Consequently, the variable parameters affecting H2 partial pressure are makeup hydrogen purity, recycle gas rate and purity, and bleed rate. Of these, the independent variables are makeup hydrogen purity and bleed rate which set the recycle purity, and the recycle gas rate. Since many hydrotreaters have amine scrubbers to remove H2S from the recycle gas, a bleed is not necessary and H2 partial pressure is a function of makeup purity and recycle gas rate.
The H2 partial pressure varies throughout the reactor with the highest partial pressure at the inlet and the lowest at the outlet. Since the operating conditions are the most severe at the outlet and strongly influence catalyst activity and stability, we will look at the impact of makeup purity and recycle gas rate on the H2 partial pressure at the reactor outlet.
The following tables show the effect of these parameters on unit performance for a diesel hydrotreater. The base case is:
Inlet pressure:
760 psig (pounds per square inch gauge)
Makeup gas purity:
99.9 vol% (volume percent) Recycle gas rate: 1500 scfb
Table 1 shows the effect of reducing makeup gas purity on reactor outlet conditions, cycle length, and start-of-run (SOR) weighted average bed temperature (WABT).
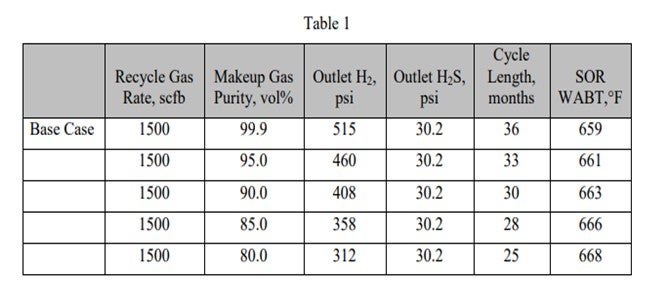
As the makeup gas purity drops, so does the outlet H2 partial pressure. This leads to reduced cycle length and higher required SOR WABT. The impact of reducing makeup gas purity is essentially the same as reducing inlet pressure. Note that as long as the recycle gas rate remains constant, even though the H2 purity is dropping, the outlet H2S partial pressure is constant. In Table 2, the impact of reducing the recycle gas rate is illustrated. Here the effect is more severe because as the outlet H2 partial pressure drops, the outlet H2S partial pressure increases. These further decreases catalyst activity and cycle length. The effect of the outlet H2S partial pressure can be isolated by comparing the 90% makeup gas purity case with the 800 scfb recycle gas rate case. The outlet H2 partial pressure is similar, 408 psi versus 406 psi; however, the cycle length is seven months shorter, and the required WABT is 10°F higher.
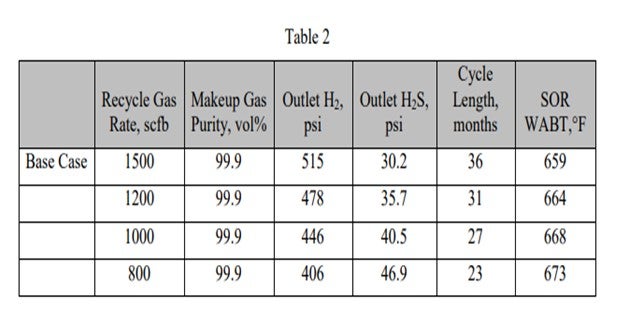
RAJESH SIVADSAN (UOP LLC, A Honeywell Company)
Hydrogen partial pressure has a major impact on cycle length from a catalyst activity standpoint. Cycle length is determined by the catalyst deactivation rate at the design space velocity and hydrogen partial pressure. Increasing hydrogen partial pressure corresponding to reactor inlet pressure decreases the catalyst deactivation rate; and hence, the longer predicted cycle length for a fixed quantity of catalyst. H2 partial pressure is mainly determined by the:
• total pressure,
• H2 purity/recycle/makeup purity, and
• gas/oil ratio.
The operating pressure is probably the most important variable. It directly affects the H2 partial pressure; therefore, the cycle length. Higher pressure drives reactions, especially HDN.
A higher treat gas rate can be used to increase the hydrogen partial pressure, but this is usually limited because of the associated increase in the reactor loop pressure drop and the corresponding maximum operating pressure of the various system components.
Hydrogen purity of makeup gas also impacts the hydrogen partial pressure. Lower purity makeup hydrogen requires higher hydrogen circulation rates to maintain the target hydrogen partial pressure and may even require a purge stream from the cold separator.
It is, therefore, difficult to recommend a guideline for the minimum hydrogen partial pressure as it depends on how much the refinery is willing to forgo on the cycle length.
SERGIO ROBLEDO (Haldor Topsøe, Inc.)
There is no practical minimum hydrogen partial pressure for specific feeds, per se. Temperature, hydrogen partial pressure, and LHSV (liquid hourly space velocity) are the three most important variables that will dictate whether specific product specifications can be met for a given feed. Therefore, the minimum hydrogen partial pressure for a given feedstock is also very dependent on the unit design. If a unit has a low hydrogen partial pressure and also a low LHSV, then it will have a very good chance at removing more difficult species in the cracked or high endpoint feeds. Besides, the unit conditions the activity of the installed catalyst is also an important factor as to whether a specific feed can be hydrotreated to meet the desired product properties. There are plenty of ULSD units loaded with Topsøe’s BRIM™ catalysts that treat cracked stocks at low hydrogen partial pressures of less than 500 psi and a number of units with an inlet hydrogen partial pressure of 200 to 300 psig.
Lower hydrogen partial pressures when treating more difficult streams will mean that a higher reactor temperature will be required to drive the reaction. Topsøe’s BRIM™ catalysts have proven to offer unmatched stability at these low hydrogen partial pressures. Also, cracked feeds and/or higher boiling range material also introduces more coke precursors which will increase the deactivation rate. This is especially significant at lower hydrogen partial pressures. Therefore, the unit will most likely be able to hydrotreat the feedstock, but this will come at a cost of cycle length.
This might still be economically attractive, as the refiner should not necessarily run his unit to meet maximum cycle length but to ensure the highest profitability for the refinery. Of course, if the hydrotreater is tied to another more profitable unit’s turnaround cycle, then meeting the cycle length is important and processing a harder stream might not be viable. It is true that as the feed is being treated deeper into the barrel, more hydrogen partial pressure will typically be required. Below are some general guidelines for operating units based on the service they are in:
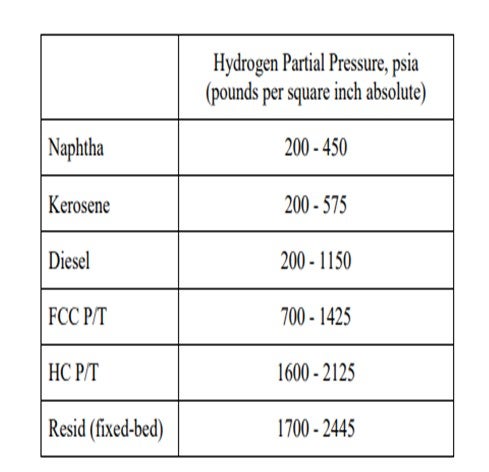