Question 4: In your experience, what options are available to debottleneck existing hydrogen systems and increase hydrogen production? Is hydrogen recovery from refinery off gas an economical option?
Praveen Gunaseelan (Vantage Point Energy Consulting)
To focus the question, let us consider a refinery setup where the main hydrogen (H2) sources are the catalytic (naphtha) reformer off gas and an on-purpose steam methane reformer (SMR) for the supplemental H2. It is assumed that pipeline H2 is unavailable. (When pipeline H2 is readily available, it is typically one of the lower cost options to meet incremental H2 demand).
Traditionally, refiners could potentially increase the severity of their catalytic reformers to boost H2 production. However, due to tighter restrictions on aromatics content in gasoline, refiners have had to decrease their catalytic reformer severity, so it is unlikely that the approach will be a viable option going forward.
Existing Steam Methane Reformers (SMR):
There are several approaches to debottleneck existing SMRs to boost H2 production. The optimal approach will extremely plant-specific and depend on the plant's design history, current condition, operating regime, etc. As plant designs are proprietary, it is important to consult with the technology provider or recommended engineering contractors to evaluate your facility and identify the optimal debottlenecking approach. Possible debottlenecking approaches for SMRs include:
•Addition of a pre-reformer
•Replacing the SMR tubes with larger diameter tubes
•Replacing catalyst with higher activity catalyst
•Addition of a secondary reformer downstream
H2 Recovery from Off gas:
There are numerous factors that dictate whether H2 recovery from refinery off gas can be economically competitive, and the decision is ultimately site-specific.
•Market factors can include the price of natural gas (that affects the relative competitiveness of SMR H2), market value of recoverable liquids, etc.
•Technical considerations include the quantity of H2 in the off gas, gas pressure, type of separation technology considered, etc.
•High-pressure gas streams containing H2, such as purge gas from high-pressure hydrotreaters, are generally good candidates for H2 recovery as they require less compression and are richer in H2. For better economics, such off gas sources should not be commingled with lower quality off gas prior to recovery.
•Either membrane systems or adsorption beds are typically used for H2 recovery from H2-rich off gas.
·When high-purity H2 is desired, adsorption is the preferred recovery method.
·Membrane units consume less energy than adsorption beds, and are suitable for lower capacity applications that do not require high H2 purity.
Brian Moyse (Haldor Topsoe)
Typical hydrogen revamp options include addition of a prereformer, (which will allow the use of broader range of feedstocks and a reduction in S/C ratio). With the addition of the prereformer, more of the fired duty in the steam reformer will be used to make H2 and less for steam export. The prereformer can typically increase the H2 production by 10-15%. Another option is to add a Heat Exchange Reformer in parallel with the existing SMR and using some of the WHB heat as heat source for the new Heat Exchange Reformer (may increase capacity by up to 25% and reduce export steam).
Hydrogen recovery from refinery off-gases may be an economical alternative, but one needs to keep in mind that the amount of the PSA purge gas may exceed the need for fuel gas in the refinery. The alternative would be to use the refinery off-gas as feed for the hydrogen plant. The hydrocarbons in the refinery off-gas will then be steam reformed to additional hydrogen. This option may require a prereforming unit or at least a special naphtha type steam reforming catalyst in the steam reforming furnace.
Revamping “Old design” Hydrogen Plants
For revamping hydrogen plants of older design, without a PSA unit, to higher capacity and/or improved energy efficiency, numerous traditional revamp options exist. These options include:
•Upgrading of feed purification and desulfurization section
•Installation of feed saturator •Upgrading of mixed feed preheater to increase reformer inlet temperature
•Reduction of the steam to carbon ratio in the reformer, taking advantage of new high-activity reforming catalysts
•Change of reformer catalyst tubes with thinner wall tubes made from new, stronger alloys
•Introduction of combustion air preheat
•Installation of adiabatic prereformer
•Introduction of new high-activity shift catalysts and re-configuration of shift section
The choice between the options must of course be made on the basis of a careful analysis of the specific situation including the condition of the existing equipment. Typically, a capacity increase of 10-20% can be achieved.
When significant capacity increase (>20%) is desired, this can be achieved by adding a compact convection reformer in parallel with the existing reformer, either a Topsøe HTCR or a HTER convection reformer. HTCR and HTER reformers are very energy efficient and compact reformers that require only a minimum of additional plot area. In order to determine the feasibility of a revamp Topsøe will perform a feasibility study to provide the client with the optimal solution. The study will take into account the status of the existing unit, the various requirements of the client as well as prevailing conditions such as availability and price of feedstock, plot plan, available downtime for revamp etc.
Figure 1 shows a diagram of how an HTER can be incorporated into an existing H2 plant.
Figure 2 is showing a heat exchange reformer being installed in an existing Syngas plant.
Figure 1
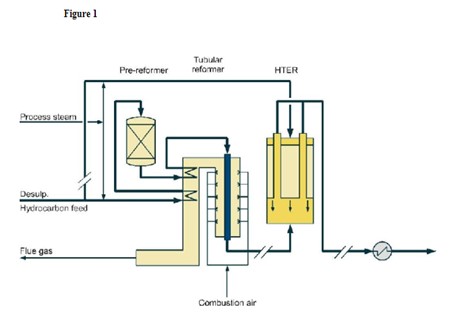
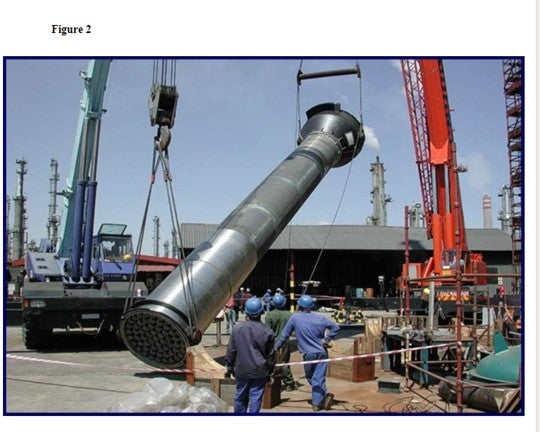
Diane Dierking (Johnson Matthey Catalysts)
There are several revamp options available for debottlenecking an existing hydrogen plant to increase hydrogen production. We will address these individually.
One of the simplest ways to increase production is by enhancing the efficiency of the plant. This might include optimizing performance of all reactors in the flow sheet (steam-to-carbon, operating temperature, etc.) over the life of the catalysts, improving combustion in the steam methane reformer (SMR) such as reduced excess oxygen, balanced firing, etc., and minimizing pressure drop by catalyst selection or optimally shaped supports, such as Johnson Matthey’s STREAMLINE™ products. These types of changes can result in incremental gains in production, on the order of 3 to 5%.
Another method of increasing hydrogen production is to re-tube the SMR with tubes having a larger inner diameter. This will be most beneficial to plants that currently have lower alloy tubes installed. By switching to a higher alloy, such as a micro alloy, the tube wall thickness can be reduced. Maintaining the outer diameter of the tubes while increasing the inner diameter achieves an increase in capacity while minimizing any other changes needed to accommodate the new tubes. Note that the spring hangers or other supports will have to be considered, as will any other hydraulic limitations in the flow sheet. This option can provide a larger incremental gain in production, generally 5 to15% with the larger percentage occurring on older plants that have had little or no upgrades in tube metallurgy over the life of the plant.
Installing an additional reactor into the flow sheet can also increase hydrogen production. The most common reactor additions are to add a low temperature shift bed, a pre-reformer or a post-reformer.
For plant configurations that have only a high temperature shift (HTS) bed, a low temperature shift (LTS) bed can be added to provide greater CO conversion in the plant and will likely also provide additional hydrogen recovery in the PSA. The addition of an LTS bed can allow an increase in total hydrogen production of 3 to 5%.
A pre-reformer can be installed downstream of where steam flow is introduced and upstream of the SMR. The benefits of a pre-reformer are additional feedstock flexibility and greater capacity through the steam methane reformer with minimal to no increase in heat duty. Depending on the feed type, modifications to the existing feed pre-heat coil may be required. To get the maximum benefit from a pre-reformer an effluent pre-heat coil will need to be installed in the convection section to heat SMR feed. The amount of production increase is dependent on operating conditions and the available feedstock but can be from 8 to 15% with the greater increase in production coming from heavier feedstocks.
A post-reformer can be installed parallel to the reformer. Some of the combined feed is diverted to the post-reformer, or gas heated reformer (GHR). The reformer process effluent is used to heat the GHR and drive the reaction, which reduces make-up fuel usage and potentially reduces NOx formation. Depending on plant design, this option can increase plant production 10% to 30%.
With respect to refinery off gases, many of Johnson Matthey’s customers feed refinery off-gas streams to the hydrogen plant. Also, many are beginning to evaluate how refinery off gases might be used instead of natural gas to increase the overall hydrogen availability in the plant. Processing refinery off gas in an SMR is most economical for streams that are not hydrogen rich. On an equal molar feed basis, heavier hydrocarbons will provide more moles of hydrogen product than natural gas; this assumes that the off-gas stream is not hydrogen rich. Also, the heat duty to reform C3+ hydrocarbons is less than natural gas, creating the opportunity to reform more of the refinery off gas. If the refinery off gas is too rich in hydrogen, it is possible that hydraulic limitations might become an issue. For refinery off gases which have more than 35 to 45% hydrogen, the economics for recovering that hydrogen with a membrane or PSA become much more favorable. The residual hydrocarbon/off gas from these systems can then become a more easily reformed feedstock for the SMR.