Question 4: What are the hydrotreating operating issues when processing shale-derived light, sweet, and highly paraffinic crudes such as Bakken, Eagle Ford, and Utica? What hydrotreating/catalyst strategies can offset any negative effects? What options are available to optimize the distillate hydrotreater(s) with these light, sweet crudes?
OHMES (KBC Advanced Technologies, Inc.)
There is a full P&P session on Wednesday, so my comments here will be brief. There is no way we can cover this topic in five minutes, but I do want to make a few points, particularly in the hydroprocessing arena. First, most people are seeing that not all shale crudes are created equal. There are a lot of different wells within the same generic field (i.e., Eagle Ford, Bakken, etc.) that produce varying qualities of crude over the production cycle. We have heard of people seeing variations of 10 to 20 API in the crude coming into the refinery. Obviously, that has a huge impact on the plant and is probably the biggest one you will see. Some of the characteristics, again, are starting to become familiar. The shale crudes in question are highly paraffinic, low sulfur, low nitrogen, and low in conventional contaminants. However, we do see some trace contaminants coming in from some of the fracking and completion chemicals. These crudes have a low resid content, which impacts the bottom of the barrel.
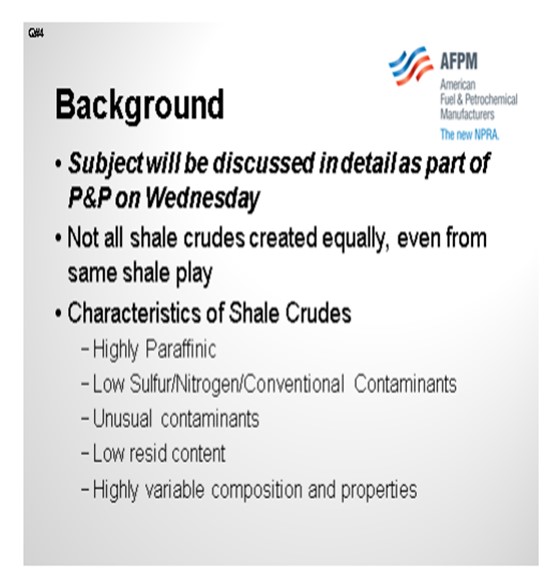
I will make a few points on each of these technologies as we go through the slides. In the naphtha area, you really need to determine if you will be able to process all of the naphtha coming in with crude. Not only does it fit with your facility’s capacity for naphtha; but also, does the market support high naphtha processing rates, particularly if you are in a more diesel-centric market? Look for some of the trace contaminants. Most people are actively managing catalyst activity, but you may want to tighten up on this internal work process. And again, what are you going to do about octane management? Because if you are now filling up your reformers and have a lot of excess octanes, you will want to bypass some blend. Or, is there some low octane blend stock you can bring in to keep yourself in balance and not have any giveaway?
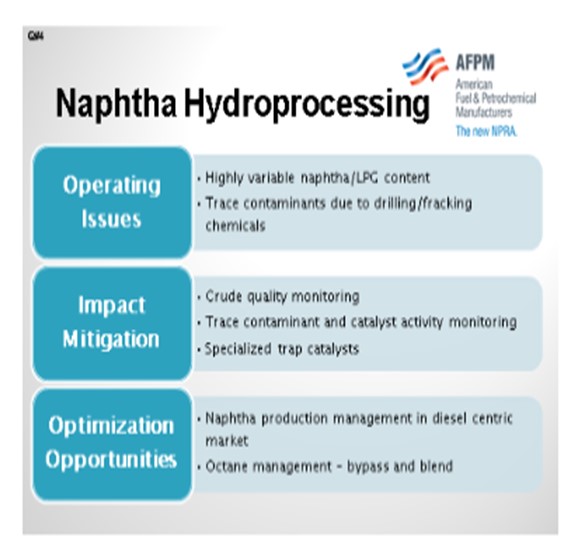
In the distillate area, most people have been able to process this crude without having cold flow property issues because of other streams that are available in the plants and in the blends. The subject of dewaxing catalyst is coming up again as a way to improve cold properties. Because of the highly paraffinic nature, it is great cetane stock; so now you will have some room in your cetane of the diesel pool. You may be able to process a little more cracked stock or some additional purchase streams and do some dumbbell blending around that.
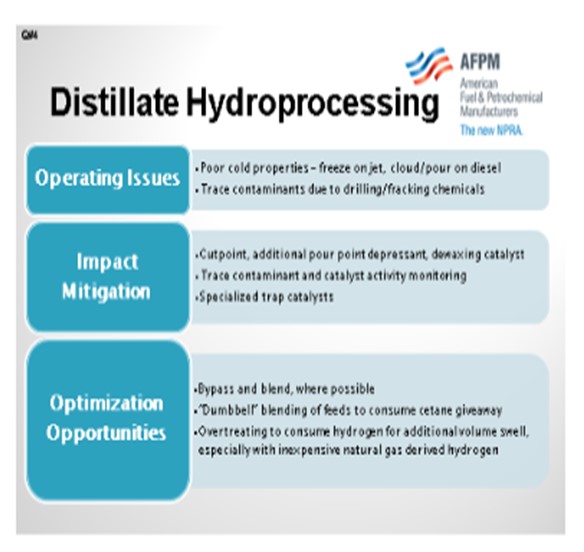
In the gas oil area, the primary focus is on the future impact on the FCC downstream. For your gas oil hydrotreater, you are going to have some nice feed to put in there. What are you going to do with the rest of that capacity? Some people are considering increasing severity to achieve Tier 3 whenever that comes to fruition. This situation may also provide an opportunity to process some of the heavier streams to utilize available capacity.
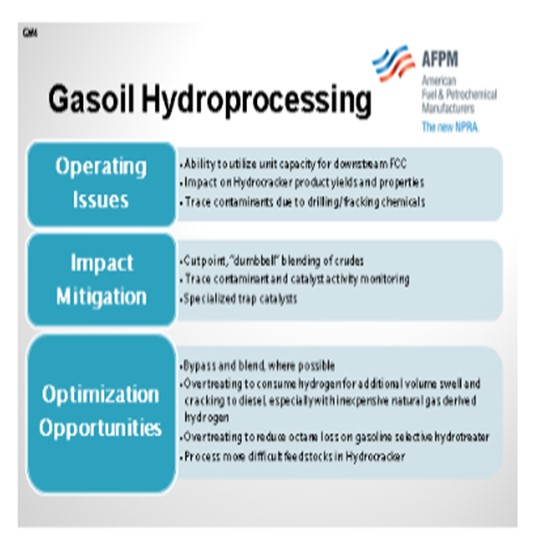
On the hydrocracking front, there is a similar issue of where to get your feeds and how to manage them. You may now have additional catalyst activity available that could cause you to have an entire step change on catalyst cycle length. We would see it as an opportunity to process some more difficult feedstocks. In the resid area, there are only a few folks in the U.S who have resid hydrotreating or bed units. The biggest challenge with the shale crudes is incompatibility when you mix them with some of the other either conventional or unconventional crudes, and that incompatibility would normally present itself in the crude unit or in the coker. But again, if you do have an ebullated bed unit or some type of fixed bed hydrotreater, then you should monitor steam incompatibility. The biggest impact we see is that people are trying to figure out how to balance all of these light sweet crudes being brought in with the available kit, and then they have to do some dramatic dumbbell blending of their crudes and bring in some heavy materials to utilize the plant’s capabilities.
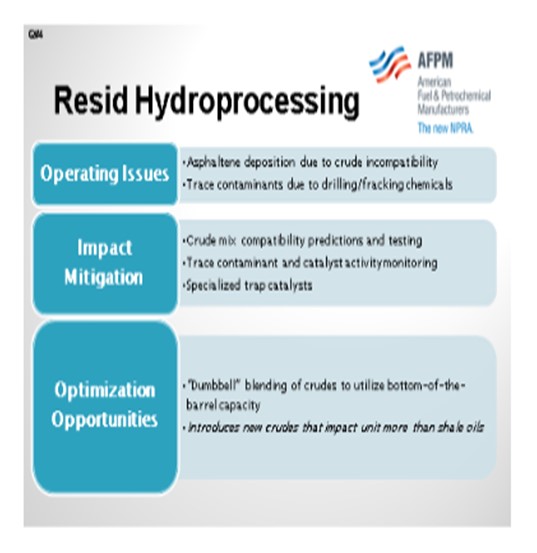
CARLSON (Criterion Catalysts & Technologies)
Before I get into my answers, I would like to acknowledge the support I received from my colleagues at Criterion, Shell Global Solutions, and our operating sites. The great answers, I attribute to them. For the mediocre answers, I will take full credit. The subject of processing these crudes was covered very well by Robert. To add a little, when considering the processing of these lighter, sweeter, but highly paraffinic crudes, Criterion would review the impact of compatibility issues, as well as the operational considerations.
Most refiners are processing relatively small percentages of these “bottom-less” crudes with their typical refinery feed slate (less than 25%). The high paraffinicity can result in compatibility issues with the balance of the feeds potentially resulting in asphaltene, precipitation, and fouling occurring in the facility.
In addition to this precipitation fouling, we have seen instances where increased levels of Fe (iron) and BS&W (bulk sediment and water) have been arriving with these feeds, again adding to any potential fouling or pressure drop build-ups.
As far as actual hydroprocessing operational impacts, these feeds are low in heteroatom contaminants; therefore, the operational impact is often longer cycle life capabilities, due to lower deactivation rates, which everyone likes. However, the low contaminant levels can strain units that relied on higher exotherms for heat integration, potentially limiting EOR capabilities as well. In hydrocracker operations, the low levels of nitrogen in the feeds can result in “controllability” issues in the cracking beds due to low nitrogen slips. However, adjusting pretreat operations can aid heat integration, which can come into play again.
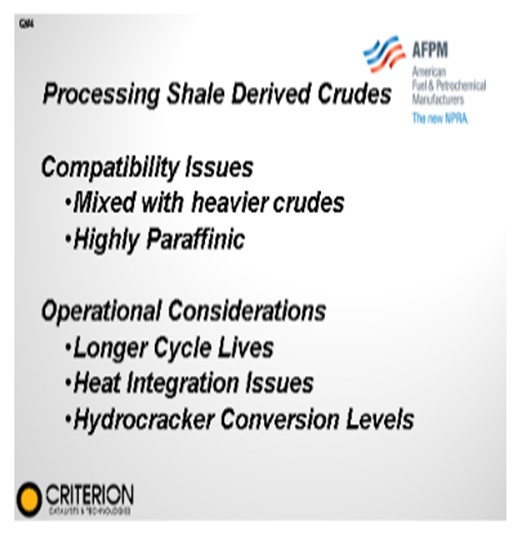
DAN WEBB (Western Refining)
I have seen that when some people are processing dumbbell-type crude blends, the total sulfur going to the unit does not decrease and the amount of higher molecular weight sulfur compounds increases. Does this result in more difficult sulfur compounds going to your unit, while moving towards a catalyst’s activity limits? The feed may contain a higher concentration of sterically hindered compounds even though the total sulfur may be lower or the same.
CARLSON (Criterion Catalysts & Technologies)
It would depend on the individual site and how they are blending their crudes. In general, these lighter paraffinic crudes are easier to process in the hydrotreaters, so it would only be a potential issue if they compensated by bringing in alternate difficult crudes. Many refiners are bringing in lower percentages of these easier feeds and displacing the more difficult feeds. The “dumbbell” impact is often more of an issue where we blend our crude API to a target and end up with more bottoms and diluents without getting the expected distillates or gas oil yields.
BODOLUS (CVR Energy)
This particular slide was aimed at shale-derived crudes. The other kind, of course, is the mined crudes or the tar sands-type crudes. Actually, the next question addresses that particular issue.
AHMAD AL-JEMAZ (Kuwait National Petroleum Company)
How do you see the future of resid hydroprocessing with the bed? Is it moving toward or away from the fixed bed? What is the success of the moving beds in the hydroprocessing of tough residues?
LEICHTY (Chevron USA, Inc.)
Chevron Lummus Global (CLG) has both fixed-bed and ebullating-bed resid processing technology. The decision as to which technology to apply in a particular situation depends on the feed quality, products desired, and other site-specific factors. Both technologies have been, and continue to be, applied successfully within the industry.
OHMES (KBC Advanced Technologies, Inc.)
We are getting questions from clients on both ebullated technology and fixed beds. We say that it is still a robust technology which should be considered, particularly with MARPOL coming in a few years and the reduction in sulfur and fuel oils. People are going to have to do something to manage that issue. There are some questions later that address a couple of the points on ebullated bed.
OHMES (KBC Advanced Technologies, Inc.)
As part of the 2012 Q&A, an entire P&P (Practices and Principles) session is devoted to the impacts of shale oil on refineries. Also, this subject is quite broad, so that a complete answer cannot be given within the space of the Answer Book. However, the following points are made to provide some context and information on the subject.
Though it may sound cliché, not all shale oils are created equal. Even those produced within a given field or region can have drastically different properties and boiling range material content at any given time. Shale oil quality vary to a larger degree and more frequently that refiners may be used to, even those facilities processing opportunity crudes or with variable crude slates. Therefore, one of the first aspects that refiners and hydroprocessing units must account for is how the facility will manage these quality shifts on a daily basis.
The most common property generalities of the shale crudes, when compared to other benchmark crudes, are:
•highly paraffinic in nature,
•poor cold flow properties,
•low sulfur, nitrogen, and conventional contaminants,
•low resid (1000°F+) content and high naphtha (300°F-) content, and
•high levels of unusual and non-conventional contaminants.
Given the broad impact of shale oil in a refinery, the following sections are broken down by process area, and operating issues, impact mitigation options, and optimization opportunities are highlighted.
Naphtha Hydrotreating
Operating Issues: As highlighted above, shale crudes contain a high content of naphtha range material. In addition, if the production fields are recovering light ends (methane through butanes) and retaining them in the crudes, the refinery will see increased production of fuel gas and LPG (liquefied petroleum gas) from the crude units. In addition, many of the chemicals used for shale oil production can contain significant levels of unconventional contaminants, such as phosphorous, titanium, and silica. Depending on the boiling point of these chemicals, many of the associated contaminants are found in naphtha range material.
Impact Mitigation: Several options are available to manage these operating issues. First, the refiner should more frequently monitor shale oil quality to understand how given shipments are varying in quality, and to adjust how the shale crude is fed to the refinery as part of the larger crude basket. In addition, the resultant naphtha streams from the crude unit should be monitored regularly for conventional and unconventional contaminants. Finally, naphtha hydrotreater catalyst loading and catalyst grading should be reviewed to understand if the catalyst can handle the new contaminant levels.
Optimization Opportunities: The primary optimization opportunity is trying to balance the high naphtha content of shale oil against the capacity of the naphtha hydrotreating and reforming sections and the market demand for gasoline or downstream chemicals. As the most facilities will run shale crude as part of a larger crude basket, processing shale crude allows the refiner to “dumbbell” blend the crude slate with a much heavier crude slate to achieve the overall facility’s operating targets. Linear Programs (LPs) and detailed refinery-wide simulations models (such as KBC’s Petro-SIM®) can assist in that optimization. Finally, many U.S. refiners are working to balance an operation where the facility is long octane barrels, primarily driven by the gradual shift to a distillate-centric market. Therefore, shale crude can exacerbate this situation. If the refiner is not able to mitigate the overall naphtha and gasoline balance through crude slate and cutpoint between naphtha and distillates, then the refiner may need to examine options to avoid octane giveaway. Some options include hydrotreating and bypassing naphtha around the reformer as an octane soak or selling naphtha.
Distillate Hydrotreating
Operating Issues: In addition to the trace contaminants discussed in the naphtha section, other issues impacting the distillate pool when processing shale crude are the cold properties (freeze, cloud, and pour) and low sulfur and nitrogen content. Essentially, these issues become challenges around product blending and treatment, as well as highlight areas for optimization.
Impact Mitigation: Given the shale oil derived distillate is easier to hydrotreat due to the lower sulfur and nitrogen levels, the downstream diesel hydrotreaters should have “spare” catalyst activity. However, the amount of spare activity will be driven by the overall facility crude slate. These recommendations provided on contaminant management in naphtha hydrotreating apply to distillate hydrotreating as well.
To manage the cold property issues, the refiner has several options. In the Kerosene region, the crude unit cutpoint will require adjustment to maintain the product specification on freeze point. Therefore, some cutpoint kerosene material will end up in the diesel pool. To manage the diesel cloud and pour point limits, several options exist.
1. Adjust crude unit cutpoint.
2. Utilize additional pour point depressant, for pour point management.
3. Blend whole kerosene into the diesel pool for cloud and pour point management, either in diesel hydrotreater feed or as part of final product blending
4. Evaluate a partial bed of dewaxing catalyst to achieve slight reductions in cold properties.
This last point may be a more realistic option than in the past due to the “spare” catalyst activity that may be available, meaning the refiner can reduce the loading of conventional hydrotreating catalyst and create room for the dewaxing catalyst. The yield and unit performance aspects must be reviewed on a detailed basis.
Optimization Opportunities: If the diesel hydrotreater units do, indeed, have additional catalyst activity or cycle length available, several optimization opportunities are available.
1. Increase processing of cracked stock up to cetane limits (also helps cold properties).
2. Increase severity to increase hydrogen addition and volume gain.
3. Adjust cutpoints on heavier and hard-to-hydrotreat streams.
4. Load regenerated catalyst.
Depending on the overall facility balance, many of these options require additional hydrogen. However, given the relatively lower hydrogen requirement for shale oil distillate, the overall hydrogen balance impact will depend on the facility crude slate and optimization options selected.
Gasoil Hydrotreating
Operating Issues: Similar to the discussions above, contaminants can be a problem for the gas oil units and require the same mitigation approach. The other operating issue involves capacity utilization, both in gas oil hydrotreaters producing feed for FCC and gas oilhydrocrackers. Otherwise, given the qualities of the gas oil compared to other conventional sources, these units should have catalytic capacity. Obviously, the hydrocracker yields and product qualities will be impacted, especially given the paraffinic nature of the gas oil feed. For example, hydrocracker naphtha will have a lower N+A or N+2A value, thereby impacting the reformer and gasoline blender.
Impact Mitigation: As highlighted previously, processing shale crude opens up opportunities to rebalance the overall crude slate. Given that the gas oil processing units are integral to high margin units such as the coker or FCC or are highly profitable in their own right, in the case of the hydrocracker, keeping these units fully utilized is important for refinery profitability. Therefore, if the gas oil units are not full and if the economics support operating these units near maximum capacity, then several mitigation options are available.
1. Alter overall crude slate.
2. Process purchased gas oils or sell virgin or hydrotreated gas oils.
3. Adjust upstream cutpoints in vacuum units, crude units, and coker fractionator. In many instances, these options tie directly to optimization opportunities.
Optimization Opportunities: Several optimization opportunities are available for the FCC feed hydrotreater.
1. Bypass gas oil around the hydrotreater and blend to required overall feed qualities.
2. Increase unit severity to 1) reduce octane loss across gasoline selective hydrotreater, 2) improve FCC LCO properties, and 3) increase volume gain and conversion.
3. Process alternate feedstocks, such as LCO or opportunity feeds.
4. Consider block operation in an alternate service (diesel production).
5. Increase facility diesel selectivity by installing mild hydrocracking catalyst.
These options are strongly impacted by the overall strategy of the FCC, refinery marginal economics, and gasoline blending. Therefore, technical and economic analysis is required to define the best options.
On the hydrocracker, several optimization options exist, as the unit will likely have spare catalytic capacity.
1. Process opportunity feeds, such as additional cracked stocks, purchased feeds, and deeper cutpoint feeds.
2. Depending on unit configuration and catalyst loading, the conversion per pass targets may be adjusted to fine tune yield selectivity.
3. If a catalyst changeout is imminent, the catalyst loading may be adjusted to replace hydrotreating catalyst with additional cracking catalyst or even change catalyst activity profile, thereby improving selectivity.
4. Depending on the limiting quality, the product cutpoints targets may need to be adjusted to meet required specifications or adjusted to shift unit selectivity.
5. Alternate modes of operation may now be possible or profitable. Processing shale crude derived gas oils in the hydrocracker opens up several optimization opportunities.
Resid Hydrotreating
Operating Issues: As with the other hydroprocessing units covered above, contaminant levels and types are particularly problematic for resid hydroprocessing units, both fixed and ebullated bed types. Therefore, careful tracking and management of these contaminants becomes especially critical in these services. One of the biggest challenges with processing shale crudes is how the resultant refinery crude slate will be varied to meet overall product slate and profitability targets. Given the highly paraffinic nature of the shale crudes, some refiners are seeing crude compatibility problems, which lead to asphaltene deposition, coking, and fouling. Normally, these compatibility problems show up in the crude, vacuum, and coking units, but they can also be found in downstream resid hydroprocessing units.
Impact Mitigation: Several options are available to identify potential crude blends that lead to incompatibility including:
1. practical experience, especially in tracking actual crude blends and impact on equipment fouling
2. laboratory testing,
3. anecdotal guidelines
4. predictive models
For many years, KBC has been active in trying to understand and estimate crude incompatibility. The techniques and tools started around understanding maximum conversion and compatibility issues associated with Visbreaker technology and have evolved into estimating incompatible blends for crude and vacuum units, as well as resid hydroprocessing units. These tools and techniques are now being further enhanced by the recent acquisition of Infochem Computer Services Limited, which has proprietary techniques that are used in the upstream oil and gas industries for understanding how reservoirs and production fluids will behave.
Optimization Opportunities: As highlighted above, the primary optimization opportunity in the area of resid hydroprocessing is the ability of the refinery to bring in alternate crudes to help balance the low resid content shale crude. The use of “dumbbell” blending of the crudes can be highly profitable, but only if the facility is able to understand, predict, and manage potential crude compatibility problems. In fact, refiners will likely find that the biggest impact to their operation is not the shale crudes directly, but rather how the new crudes or crude slates affect the ability to maintain reliable and profitable operation.
KEVIN CARLSON and GEOFF WIERSEMA (Criterion Catalysts & Technologies)
Processing of light, sweet and highly paraffinic shale-derived crude oils can present unusual challenges to the refiner. One of the most significant problems is with compatibility with other crude oils. Due to the light nature of the shale-derived crude oils, there is little “bottoms” material in the shale-derived crude oils and these crudes are often mixed with other, much heavier crude oils to provide the proper amount of bottoms material to enable the refinery to operate the units effectively. However due to the highly paraffinic nature of the shale-derived crudes, blending with these heavier, more aromatic crudes can result in “incompatibility” and the precipitation of asphaltenes.
Together with a higher paraffinicity, shale-derived crudes often have much lower nitrogen, sulfur, Conradson carbon levels but can vary in contaminant metals. In particular, the Eagle Ford shale oil, while quite high in Fe content, is very low in CCR and Ni+V (nickel plus vanadium) content relative to typical crude oils. The lower nitrogen, sulfur, and metals concentrations result in reduced severity of reactor operation which can lead to longer cycle lengths; however, the contaminant Fe can result in fouling to occur necessitating good filtration and top-bed grading augmentation. Also associated with these lower aromatic and heteroatom containing feeds are reduced heat integration effectiveness (due to reduced reactor exotherms), and reduced hydrogen consumption and its associated volume swell can be observed.
In hydrocracking applications, the low levels of nitrogen can lead to higher conversion levels and larger reactor exotherms if the temperature cannot be controlled adequately due to the low NH3 (ammonia) concentration and changes in the yield slate due to the paraffinic nature of the feed.
GREG ROSINSKI, BRIAN WATKINS, and BRIAN SLEMP (Advanced Refining Technologies)
The processing of highly paraffinic crudes can pose difficulties with various product grades meeting specifications such as cloud and pour point, as well as cold filter plugging point. In cases where the refiner’s market demands meeting a more stringent specification, changes to the hydrotreating operation may require the combined system of a catalytic dewax catalyst inULSD/jet/kero hydrotreating, or some form of mild hydrocracking in heavier applications, in order to limit the longer paraffinic chains.
In refineries designed with higher hydrogen pressures and low space velocities for dealing with more refractory feedstocks, the introduction or switching to lighter paraffinic crudes can experience incremental light end generation. The high horsepower of these hydrotreaters can cause the undesirable reaction of eliminating some of the paraffin chains once the remaining reactions have gone to near completion.
Some crudes from these areas have been known to contain higher quantities of iron than what are found in typical crudes. Processing the heavier fractions will require the use of adequate feed filtration in order to prevent fouling and plugging in equipment. The use of additional top-bed particulate trapping materials is also recommended in order to avoid an unexpected skim or turnaround.
The processing of light, sweet crudes can have benefits to a refinery as well, as the demand on hydrotreating performance can be lessened at similar processing rates. It can also allow for additional upgrading barrels by increasing throughput or if the process conditions warrant, the ability to place additional hydrogen into the feed making for higher distillate yields at the current processing rates.