Question 4: How will increased production of naphtha from light tight oil (LTO) and Tier 3 regulations affect the economics for alkylate and reformate production? Are there other options for processing light naphtha streams?
KEADY (Technip USA)
That was a great Keynote address this morning because it talked about the LTOs, and Ramón Loureiro described them in detail. A couple of other options are to take the light naphtha through an isomerization unit and separate out the C5s and C6s to possibly get the benzene precursor removed from the reformer. That is one advantage. Also, you will have more butanes, which will be available for alkylation and for the FCC. You can recycle the light olefins from the FCC gasoline back to the FCC unit to produce more C3s and C4s that would then be available for alkylation use of the butanes to make more alkylate. With BenzOUT™ technology, if you separate out your benzenes, you can react them with the refinery-grade propylene to make a light reformate.
I did a quick study of one of the refineries that I worked on in the U.K. when I was on assignment there. Shown in the table are the gasoline-blending components from the grassroots refinery. You can see that there are different characteristics. Because I am a process design engineer, I am always thinking about how to push a unit just a little more than your 10% overdesign margins. So I said, “Okay, this is our base gasoline (as shown in the table) that we are making, which has around a RON (research octane number) of 95. And if we have an additional light naphtha that would be going through the hydrotreater, what would this do to the quality of the blend?” You can see that the RON goes down; the MON (motor octane number) goes down; and also, the olefins and aromatics go down. If you were to take 10% through the isomerization unit and the reformer unit, all of these qualities would go up. Of course, then the benzene will go up, the olefins will go down, and the aromatics will go up.
In Case 3, I said, “Okay, let us make 10% more alkylate and blend that.” All of the qualities go up: RON and then the olefins, and the aromatics go down. I put a dollar value because that is what the first part of the question was requesting. So in Case 1, if you had 10% additional naphtha, it would be a little neutral; but if you were able to produce 10% more in your isomerization unit reformer, you would get an increase in value. Of course, the higher value would be if you could produce more alkylate as part of your gasoline blend.
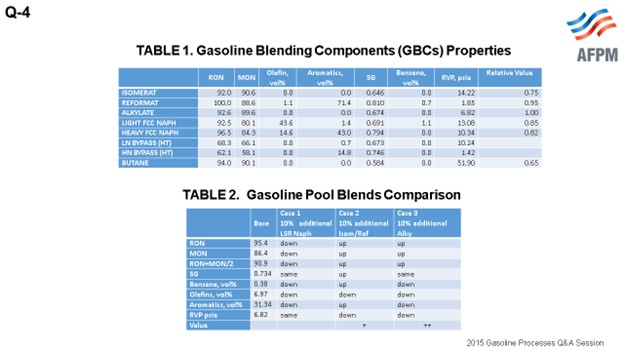
LAMBIE (KBC Advanced Technologies, Inc.)
Alkylate is the premium gasoline blendstock, both in an LTO environment and even more so in a Tier 3 environment, as FCC naphtha sulfur and octane will decrease. The key properties of alkylate are its octane and Reid vapor pressure (RVP). Alkylate’s high octane allows for lower reformer severity, which provides a liquid yield benefit. Alkylate’s low RVP allows for upgrading high RVP light naphtha or isomerate to the gasoline pool. In some locations, alkylate can yield about 20 to $30 per barrel above regular unleaded gasoline. Increasing alkylate production, however, may be difficult as most locations have full alkylation units; but if you can make more alkylate, you should.
Reformate is also a valuable gasoline blendstock; however, it contains benzene and aromatics which may impact gasoline blending specifications in some locations. In an LTO processing world, reformer feeds are leaner and yield loss is higher, assuming a constant octane. This results in less gasoline and increased quantities of lower value gas and LPG (liquefied petroleum gas). The increased yield loss makes reformate less valuable than alkylate. When it comes to Tier 3 and supplementing the reduction in FCC naphtha octane, the reformer is the likely knob to turn. Again, increased reformer severity will increase benzene and aromatics, and these must be managed in the gasoline pool.
One light naphtha processing option is to blend directly to the gasoline pool. Another option, as Ginger mentioned, is isomerization of light naphtha. For this option, one must consider RVP blending limitations. Some locations have the ability to sell light naphtha – for example, to Canada – for use as bitumen diluent or to blend into low octane gasoline for export. Light naphtha can also be used as cracker feedstock for ethylene production, but it may not be as economical as more readily available lighter feedstocks, such as ethane and natural gas liquids (NGLs).
ERIC YE (DuPont Clean Technologies)
At first glance, the increasing supply of light naphtha, LTOs, and natural gas liquids (NGLs) would seem to improve the economics for alkylate and reformate production as the increasing supply of cost-advantaged feedstocks results in depressed prices and, therefore, improves the upgrading margins for these unit operations. However, when one considers the PNA (paraffin, naphtha, aromatic) characteristics of the naphtha produced from LTOs, the impact on the economics of reformate and alkylate production becomes considerably different.
Naphtha from LTOs or associated NGL production is predominantly paraffinic which results in a lower N+2A (volume of naphthenes + two times the volume of the aromatics) content. The result is that for the same severity, reformer C5+ yield and hydrogen production is lower and fuel gas and LPG (liquefied petroleum gas) production increases. Even with the LPG and fuel gas yields increase, burgeoning supplies of natural gas and NGLs (due to the success of hydraulic fracking in North America) has depressed both fuel gas and LPG prices to the point that economics to process naphtha produced from LTO or NGL production in a catalytic reformer is challenged at best, even with historically high premiums for high octane reformate. Low natural gas prices have resulted in on-purpose production of hydrogen being competitive with byproduct hydrogen production from reformers, further handicapping reformer economics. With challenged economics, the supply of reformate as source of high-octane gasoline blendstocks has been limited. As a result, the price of an octane barrel has increased.
Alkylation is one of the few LPG processing technologies that has the ability to convert a paraffin to a heavier hydrocarbon molecule without first converting the paraffin to a more reactive compound such as an olefin or alcohol. The increasing production of butane is driven by the same market factors that are driving the increased production of naphtha LTOs: the growing use of hydraulic fracturing in North America. The resultant surplus of butanes in North America has resulted in butane prices that are heavily discounted when compared to gasoline. As illustrated in Figures 1 and 2, the ability of alkylation to convert heavily discounted butane into a high octane/low RVP gasoline blendstock has resulted in record high alkylation margins despite the sharp decline in absolute gasoline prices. With reformer economics often being challenged, alkylate offers refiners the most economically attractive option to produce additional high octane blendstocks. With limited alternative uses for NGLs such as butane and isobutene, and a growing demand for gasoline, this trend is expected to continue for the foreseeable future.
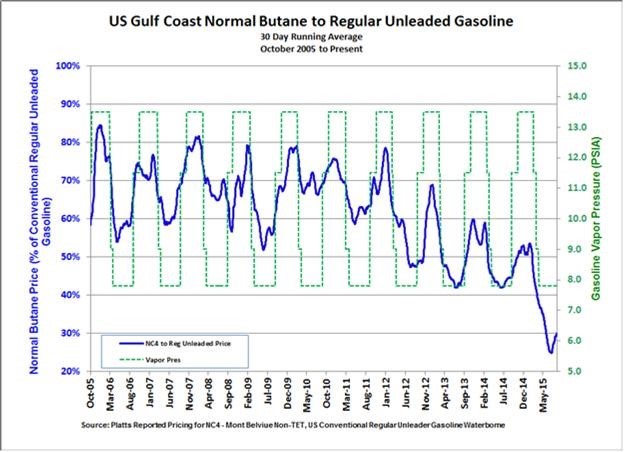
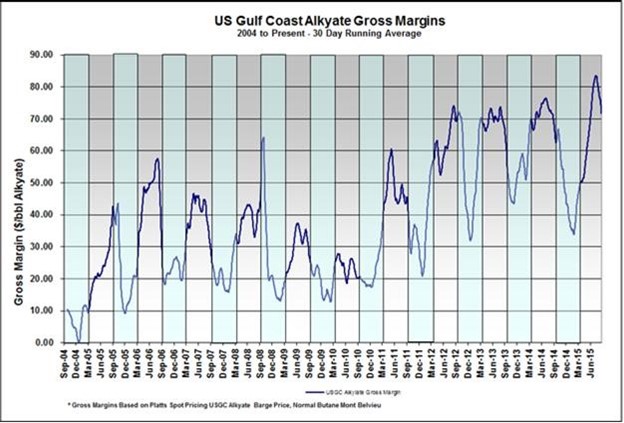
Tier 3 regulations, which require a reduction in gasoline sulfur content from the existing 35 ppm average to 10 ppm, will increase the need for additional octane barrels. This is due to the fact that the sulfur current contained in the gasoline pool is mostly due to FCC naphtha, which will need to be hydrotreated more deeply than it currently is in order to achieve the new sulfur specifications. More severe hydrotreating will hydrogenate some of the high-octane aromatics and olefins contained in the FCC naphtha to their corresponding lower octane naphthenes and paraffins, thus lowering the octane of this blendstock.
While it is speculative at this point in time, the EPA (Environmental Protection Agency) is considering modifications to the current Tier 3 regulations that would increase the minimum octane rating from its current 87 road octane rating to 89 road octanes, in addition to the elimination of the 1 psi waiver for ethanol gasoline blends. The former change will further EPA’s goals of increasing automobile CAFÉ targets as it will allow auto manufactures to produce gasoline engines with turbo chargers and higher compression ratios, both of which improve vehicle fuel efficiency. As such the demand for high octane blendstocks, such as alkylate and reformate, will only increase.
While light paraffinic naphtha (C5/C6) can be isomerized to improve the naphtha octane rating by 10 to 15 points, with few exceptions the product will normally be below the blending octane ratings (80 to 85). In addition, a modest percentage of the naphtha (2 to 4%) will be converted to fuel gas and LPG, reducing the economics of this conversion process. Further, isomerate has a high vapor pressure [15 to 20 psia (pounds per square inch absolute)]. This limits the ability to blend this material into the gasoline pool.
Alternatively, light naphtha can crack in an FCC to produce light olefins for subsequent upgrading into alkylate. However, the economics can vary considerably based on a refiner’s available FCC and alkylation capacity, fuel gas balance, and FCC configuration, to name a few.
Clearly, in the current environment for the refiner with an available light olefin supply (C3 to C5 olefins), alkylation provides the most economically attractive means of addressing the current and potential future Tier 3 gasoline regulations.
SCOTT LAMBIE (KBC Advanced Technologies, Inc.)
The quantity of light and heavy naphtha typically present in light tight oils (LTOs) presents a challenge for some refiners. The ethanol blending mandate, while adding significant octane to the gasoline pool, has added to the difficulty of blending to RVP specifications, thereby limiting additional LTO processing in some locations. However, most refiners have managed to modify the operations of their plants to address these challenges and have done so in a number of ways: blending more LSR (light straight-run) instead of isomerizing; blending heavy naphtha instead of reforming, depending on the octane balance; and, lowering reformer operating severities. Some coastal refiners are exporting low-octane gasoline, while others are exporting light naphtha to Canada where it is used as diluent for crude transport.
Depending on the overall balances resulting from increased LTO processing, the quantity of gasoline may increase or decrease; that is, the increased naphtha from the feeds may be offset by reductions in total FCC naphtha and alkylate. In either case, alkylate is, and will continue to be, highly profitable and the ideal blendstock due to its low sulfur, lack of benzene or aromatics, relatively low RVP, and high octane. Incremental reformate is profitable to produce, but only up to the point where the gasoline pool octane is in balance.
The impact of Tier 3 gasoline regulations will require FCC naphtha treatment to obtain roughly 10 to 25 ppm product sulfur to meet the pool sulfur requirement of less than 10 ppm (7 to 10 ppm within the refinery gate). The increased hydrotreatment will likely result in lower FCC naphtha octane, which will require changes to operating conditions within the plant to balance octane in the gasoline pool.
Incremental alkylate is the desired route to compensate for reduced FCC naphtha octane. In some locations, alkylate is yielding greater than 15 to $30 per barrel above RUL. However, most refineries are already adjusting FCC operations to provide the maximum feed rate alkylation units can handle. Modifications to FCC operations and catalyst formulations may help provide an octane boost to native FCC naphtha while maintaining alkylation units at maximum throughput, thereby reducing its octane loss.
In order to compensate for the expected reduction in octane from the FCC combined naphtha stream, it is possible for some refiners to increase the feed rate to the reforming unit by reducing the amount of heavy naphtha sent directly to the gasoline pool, if applicable. Alternatively, refiners can increase the reforming unit severity to balance the gasoline pool octane. The increased throughput and/or severity will result in the production of lower value LPG and fuel gas, which is a debit for reforming economics, but which may be necessary, depending on the alternatives. In either case, the feed rate and/or severity should be minimized to maximize liquid yield. Some refiners may be constrained on benzene in the gasoline pool and should take precautions before raising reformer severity. Maximum removal of benzene precursors from the reformer feed is a prudent adjustment in this scenario.
Incremental isomerate is profitable versus blending light straight-run material provided the gasoline pool can accommodate the higher RVP blendstock. Blending light naphtha to the gasoline pool may be profitable but may require additional octane from other sources to accommodate the blendstock.
GINGER KEADY (Technip)
LTOs are composed of 40 to 60 vol% (volume percent) naphthas, which are generally paraffinic with low sulfur content and low octane. Therefore, lighter straight run naphthas (LSR), as well as LPG, are available for processing and blending.
The LSR naphtha is sent to a C5/C6 isomerization unit. The C5/C6 isomerate can contribute high octane isomers converted from normal paraffins without olefins or aromatics but has high RVP.
The benzene precursors, methycyclopentane (MCP) and cyclohexane (CH), are removed from the reformer feed.
Butanes are available for alkylation. Alkylates are the primary component for high-octane gasoline with low sulfur and very small amounts of olefins, benzene, and aromatics. The alkylation of amylenes can be considered with some RON loss and an improvement in gasoline pool RVP. The alkylation of benzene with the ethylene in the FCC off gas can also be considered.
In BenzOUT™, technology reacts a benzene rich stream with a light olefins stream, such as refinery grade propylene stream, to produce a light reformate with a reduced RVP.
Light/heavy FCC naphthas contribute to the olefins, benzene, and aromatics content of the gasoline pool. If C6/C10 olefins in the gasoline boiling range are recycled and overcracked in the FCC, propylene is produced preferentially with an increase in C4 olefins as well.
Assessment: To assess the impact of LTOs on the naphtha processing units in a refinery, gasoline blending components (GBCs) from a grassroots refinery are used. The GBCs are produced in the following licensed technologies and shown in Table 1:
-
Naphtha hydrotreating,
-
C5/C6 isomerization,
-
Reforming,
-
Alkylation (C3 and C4),
-
C4 isomerization, and
-
FCCU.
TABLE 1. Gasoline Blending Components’ (GBCs’) Properties
|
RON |
MON |
Olefin, vol% |
Aromatics, vol% |
Specific Gravity SG |
Benzene, vol% |
RVP, psia |
Relative Value |
Isomerate |
92.0 |
90.6 |
0.0 |
0.0 |
0.646 |
0.0 |
14.22 |
0.75 |
Reformate |
100.0 |
88.6 |
1.1 |
71.4 |
0.810 |
0.7 |
1.85 |
0.95 |
Alkylate |
92.6 |
89.6 |
0.0 |
0.0 |
0.674 |
0.0 |
6.82 |
1.00 |
Light FCC |
92.5 |
80.1 |
43.6 |
1.4 |
0.691 |
1.1 |
13.08 |
0.85 |
Heavy FCC |
96.5 |
84.3 |
14.6 |
43.0 |
0.794 |
0.0 |
10.34 |
0.82 |
Light Naphtha (LN) Bypass (Ht) |
68.3 |
66.1 |
0.0 |
0.7 |
0.673 |
0.0 |
10.24 |
|
Heavy Naphtha (HN) Bypass (Ht) |
62.1 |
58.1 |
0.0 |
14.8 |
0.746 |
0.0 |
1.42 |
|
Butane |
94.0 |
90.1 |
0.0 |
0.0 |
0.584 |
0.0 |
51.90 |
0.65 |
All effluent streams are from either hydrotreaters or hydrocracker; therefore, all GBCs achieve the blended gasoline spec of 10 ppm sulfur.
An evaluation assumes an additional 10% of LSR to gasoline blending for Case 1, additional 10% feed to ISOM/Ref for Case 2, and additional 10% of alky for Case 3 for the impact on the gasoline pool. The comparison is shown in Table 2.
TABLE 2. Gasoline Pool Blends Comparison
|
Base |
Case 1 10% additional LSR Naphtha |
Case 2 10% additional Isom/Ref |
Case 3 10% additional Alky |
RON |
95.4 |
down |
up |
up |
MON |
86.4 |
down |
up |
up |
RON+MON/2 |
90.9 |
down |
up |
up |
SG |
0.734 |
same |
up |
same |
Benzene, vol% |
0.38 |
down |
up |
down |
Olefins, vol% |
6.97 |
down |
down |
down |
Aromatics, vol% |
31.34 |
down |
up |
down |
RVP psia |
6.82 |
same |
down |
down |
Value |
|
|
+ |
++ |