Question 4: How reliable are the dry gas seals on hydroprocessing recycle gas compressors? What are the system components put in place to enhance the reliability?
Shankar Vaidyanathan (Flour)
Dry gas seals have been used for compressors for many years. The feedback was mixed in its infancy, and there were teething problems. External factors such as the contamination of the sealing gas, insufficient sealing gas pressure and process gas leak onto the seal ring surfaces have been the main reasons for seal degradation. Wetness, particulates, and heavier hydrocarbons cause seal reliability issues. The quality of seal gas and buffer gas, dryness level, pretreatment, liquid separation and filtering are the keys to reliable operation. Experience has shown that seals can last a long time in a clean environment and many existing plants have switched over to gas seals. Tandem self-acting dry gas seal with internal labyrinths has been selected in many recent projects.
Please see the attached sketch for external components of the dry gas seal system.
1. Depending on pressure balance, the sealing gas may be pure makeup hydrogen (if the makeup compressor is located within the same plot) or recycle compressor discharge gas. Chlorides in makeup hydrogen and amine aerosols in recycle hydrogen are potential contaminants.
2. Nitrogen is used as the buffer gas.
3. Filters for seal gas and buffer gas should be duplex, one operating and one standby, 3-micron stainless steel coalescing filters equipped with high differential pressure alarm. Avoid three-way valves for filter switching.
4. Consider additional pre-filter for sealing gas if experience has shown that coalescing filters are inadequate. Consider additional demister filter for buffer gas if necessary.
5. Minimum 1” size stainless steel piping is preferred. Additional notes for piping layout include minimizing runs, avoiding pockets, heat tracing and winterizing as necessary.
6. The seal gas injection is on automatic pressure control.
7. Primary vent is routed to flare; secondary vent is routed to safe atmospheric location.
8. Primary seal vent flow is monitored with high flow and high-pressure alarms.
9. Pressure in the secondary vent line must be limited such that the maximum seal backpressure should not exceed 5 psig.
10. Consider differential pressure alarm between the buffer gas and secondary vent.
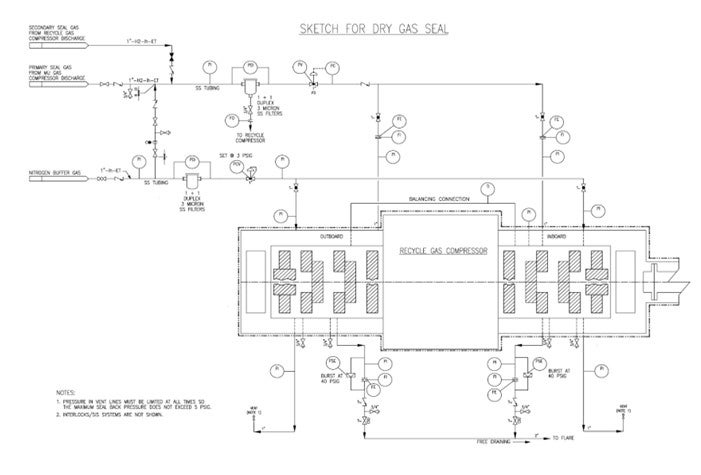
Minh Dimas (CITGO)
Dry gas seals are more reliable than oil seals provided the seal gas conditioning system is properly designed, and the seal gas is very clean and dry. That said, the filtration and liquid removal system must be very reliable and have spare equipment to maintain its reliability. Tandem dry gas seals require a source of very clean, dry seal gas at startup.