Question 39: There is a drive to target the highest endpoint possible on all distillate feed streams when maximizing overall diesel production. Are there feed streams that should be targeted first, considering operational impacts of such optimization, impacts to catalyst performance and life cycle, as well as cutpoint optimization between distillate units and the FCC?
VICHAILAK (Marathon Petroleum Corporation)
For maximum diesel, in general, we prefer getting the distillate out of the FCC. I think we had a discussion last year in the FCC forum during which we said that keeping some distillate in the FCC feed is a benefit. We still say that if you want to maximize the diesel, heavy-out the straight-run distillate of virgin gas oil because it will be the easiest to treat compared to the other two, which are coker distillate and LCO. Coker distillate is the second target because it has high sulfur and nitrogen. Light cycle oil streams are the last on which you want to increase the endpoint because most of the sulfur in there is very difficult to treat. Because if you are heavy on that part, you will probably have to back out a different easy stream to make room for it, keeping in mind that you must make the product spec.
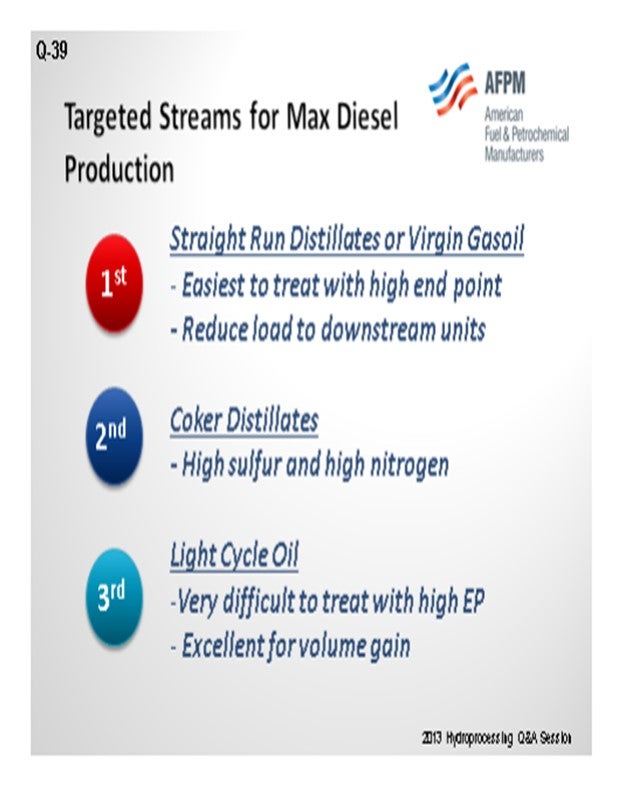
Endpoint maximization depends on the capability of distillate hydrotreaters. Most of the time, if the easy stream (like light straight-run diesel) normally goes to one of the low-pressure hydrotreaters, while most of the cracked stock will then go to the high-pressure units as per design. Hydrogen availability at the site also dictates how you are going to maximize endpoints. You can upgrade low-quality diesel feeds like LCO and coker distillate, but the cetane of that cracked stock pool will normally be low. High paraffin content in crude may limit virgin feeds because you need a bit more aromatics in there. But for any cracked stock that you add to a unit, you will probably have to back out some of the easy stream. If you treat them together, our rule of thumb is: One barrel of coker distillate will replace three barrels of virgin feed.
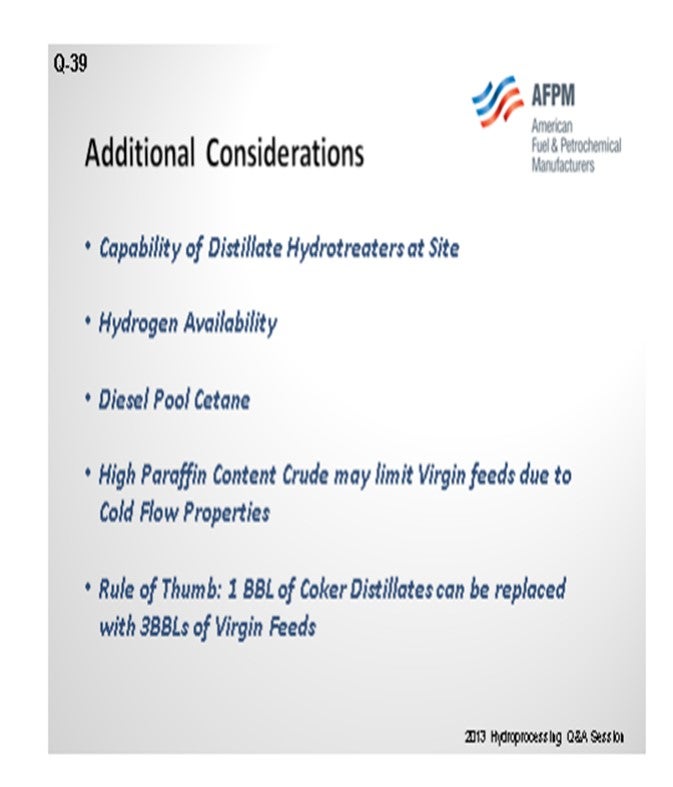
WATKINS [Advanced Refining Technologies (ART)]
If you are looking for what you will consider for max diesel production, there are a couple options to consider. One is to get more barrels into your ULSD hydrotreater. The other is simply trying to get more barrels on the backend of your diesel hydrotreater. So, one is volume swell, and one is just putting in more barrels. This chart examines the initial understanding of increasing endpoint might do in terms of how much sulfur is coming into the unit. It is evaluating LCOs, coker gas oils, and straight-runs. So, if we want to just change up the endpoint of our feed regardless of feed stream, we will actually start increasing the amount of hard sulfur coming into the hydrotreater. So, we will want to pay attention if we have a hydrotreater that used to have a 650°F or a 750°F 90% point because we will now go to around 750°F to 780°F, which will have a serious impact in the terms of actually processing for your hydrotreater.
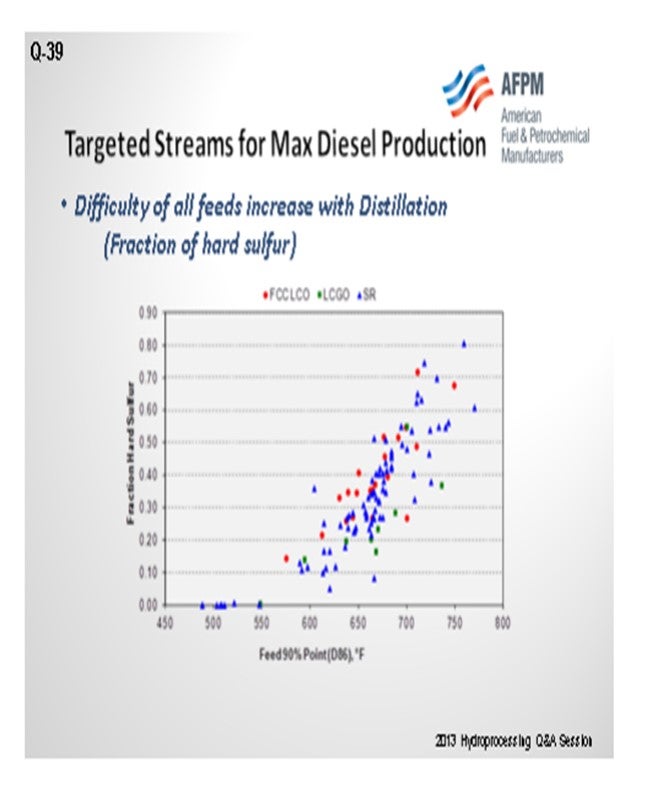
Virgin (SR) Feedstocks: If you are going to then want to think about what you will get from max diesel, if you can get more barrels into your units and are not constrained in that sense, then certainly bringing in a virgin feed stock is good. It will have minimal impact and will not change your hydrotreater cycle dramatically; so, the activation rate will not go up as much, nor will it consume as much hydrogen as your other two streams might; so, it is the easiest on your general operation.
Coker Distillates: It is kind of a one and a half choice. It is clearly a second, but it is almost interchangeable. It does have higher sulfur and nitrogen than a virgin feedstock, assuming the same distillation. As you mentioned, it has higher olefins so it will have more hydrogen consumption. If that is the feed stream on which you want to consider increasing endpoint, then make sure you have enough hydrogen in your system to handle that consumption because it will also require a higher weighted average bed temperature in order to get to the same ULSD targets.
FCC Light Cycle Oil: This feed would be your third choice. It will definitely have higher aromatics, PNAs (polynuclear aromatics), than a virgin feedstock of the same boiling range, a much lower API. Sulfur and nitrogen concentration will depend on your pre-treater or a lack of a pre-treater in front of the FCC. It could be very high sulfur or very low sulfur and nitrogen, depending on how that process is operated. This will definitely require higher temperature in your hydrotreater, so it will shorten your cycle length the most. It will also consume quite a bit more hydrogen in order to achieve that same level of product qualities you are used to.
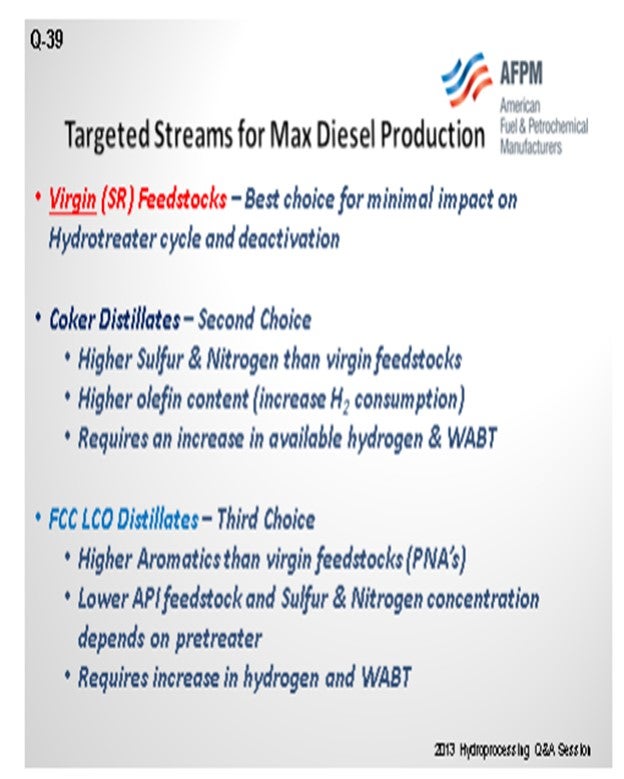
My next slide shows that it could actually be your first choice, if you are looking for volume swell. That was the other piece of our puzzle. Is it more barrels in the front or more barrels in the back? If you have high enough pressure, you will have the incremental hydrogen to add to your process to avoid being limited. It could actually provide you with the maximum volume expansion or the actual largest cetane increase that you could see over any other feedstock. The chart compares the results when a refiner went from 100% light cycle oil to 100% straight-run during its process. You can see that the biggest cetane increase results from the inclusion of the most LCO. But obviously, it comes with the caveat that you're starting cetane is significantly lower if you run 100% light cycle oil. So, consider that you may not meet a 45- cetane specification because you started at 20.
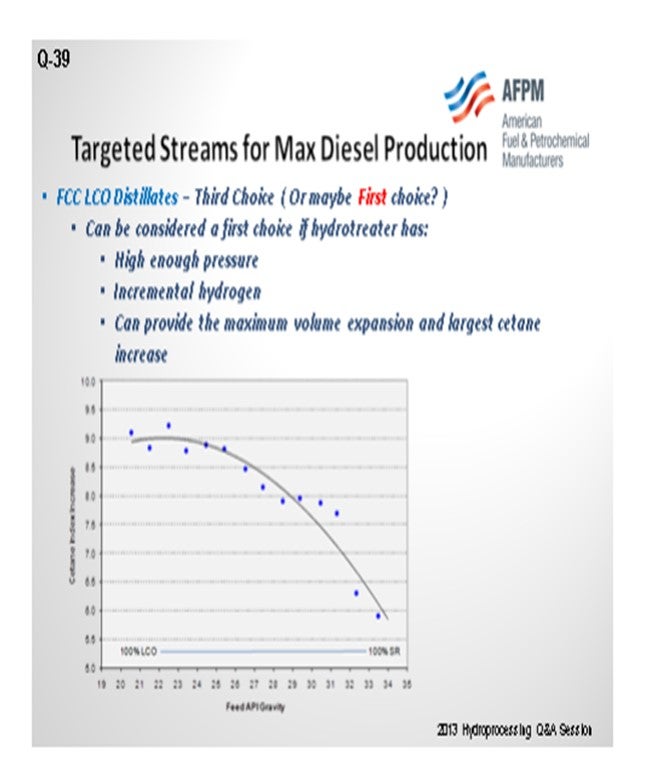
KEVIN PROOPS (Solomon Associates)
Those were all good comments. I want to particularly talk about Brian’s slide that showed the amount of hard sulfur in the streams as a function of TBP (true boiling point). To the panelists, if we are going to put more hard sulfur in the unit and start challenging the unit operation, does it make sense to start taking out some of the light material if you have a unit with that has a capacity constraint and in which space velocity is getting tough? Should we be taking the light cracked distillates in the front end of the light cycle oil or the front of the coker distillate out of the unit and putting them somewhere in a lower-severity unit, keeping the higher-boiling molecules in the unit that is better equipped to deal with them?
WATKINS [Advanced Refining Technologies (ART)]
Feed selection would really depend on the hydrotreating capabilities at your refinery. If you have another unit out of which you can pull those light barrels and continue to process, then it would make sense to do so in order to then pull that heavier diesel into your diesel hydrotreater. You will want some of that light material in your hydrotreater feed in order to give you some extra heat of reaction. It will easily be processed in your ULSD hydrotreater because that unit probably has more horsepower than if you had to try and bring it into your kerosene unit or some other light processing unit. It will really depend on the horsepower of your ULSD unit. If you want to take it out, it may just be going for the ride.
GEORGE HOEKSTRA (Hoekstra Trading LLC)
Every year in the industry, there are many cycles that are much shorter than expected. Sometimes that is certainly caused by pushing too hard on your feed. Other times, it is caused by the catalyst or by bad flow distribution, for example. So, I have a multiple-choice question: Do the panelists have any thoughts on which one of those three is the most likely cause of a short cycle in a diesel unit? Is it the feed, the catalyst, or the flow distribution?
VICHAILAK (Marathon Petroleum Corporation)
Before putting the catalyst in the reactor, you should evaluate what you plan to do for that cycle and try to protect it and preserve activity. Do you have a budget of how much temperature you will allow? If you have enough activity, then you can just heavy-up the feed and go further. That catalyst side is planned, but flow distribution of coke in the bottom of the reactor is not planned and could happen. So I would pick the last one to be the main reason. It will be your call to heavy-up the feed when you know, for certain, that there is not enough activity.
LIOLIOS (DuPont Clean Technologies)
One of our famous consultants told us, “A catalyst does not deactivate. It is always murdered.”
WATKINS [Advanced Refining Technologies (ART)]
I agree, because we see deactivation as being feed-driven. You start your cycle with one feed, and you end it with something completely different. Management is giving you opportunities every day, and you have to fight through it. Feed quality tends to be a lot of what shortens your cycle.
SHARPE (Flint Hills Resources, LP)
Yes: thinking, planning, and economics
SERGIO ROBLEDO (Haldor Topsøe, Inc.)
I have a general comment. With regard to diesel hydrotreating, most people look at D86 distillation. Often, fractionation is not that great. We have seen people who do SimDists (simulated distillations) where the tail is 100°F different from what you gain on D86. So, it is a good idea to look at D86 and your SimDist when changing your endpoints on a D86 basis.
SHARPE (Flint Hills Resources, LP)
When you increase your endpoint, you also increase nitrogen in the feed. The ULSD catalyst can be very sensitive to nitrogen, which forces you to raise your reactor temperatures to meet your sulfur targets. That can lead to more rapid deactivation. So, when you start working on high endpoints, you need to watch your nitrogen as closely as your sulfur compounds.
GATES (Motiva Enterprises LLC)
I will put the same caution on SimDist: You should always double-check to confirm you are looking at the final distillation quantity actually being reported. There may be a hidden tail that could get you, even on a SimDist, above and beyond the D86.
MONTRI VICHAILAK (Marathon Petroleum Corporation)
Straight-run diesel or atmospheric gas oil streams should be targeted first because they contain less sulfur and nitrogen and are the easiest streams to treat, compared with other cracked material with the same EP (endpoint). Maximizing the straight-run diesel endpoint also helps to debottleneck the heavy end processing units as well. Cracked distillates normally contain high sulfur and nitrogen. If the operating condition of ULSD processing is already limited, increasing the cracked material endpoint may require reducing throughput of the unit in order to meet ULSD product spec. Our approximation for tradeoff barrels between coker distillates and straight-run diesel on EP is a factor of 3.
Increasing light cycle oil endpoint increases the number of aromatics and heavy sulfur to the unit. For medium to high-pressure ULSD units with tight treat gas ratios, the concern will be significant increases in hydrogen consumption, which will reduce hydrogen partial pressure of the bottom beds. Also, the sulfur species in the heavy ends will be much more difficult to be treated, necessitating higher operating temperature. The combination of conditions required to meet product sulfur spec can lead to significantly higher deactivation rate due to coking.
BRIAN WATKINS [Advanced Refining Technologies (ART)]
There are several basic impacts that need to be understood when considering increasing the final boiling point of a particular feed stream in the refinery. With elevations in the final boiling point of the feed, the total sulfur and nitrogen, the concentration of hard sulfur, and aromatics content all increase. This is independent of the source of feedstock (Figure 1). In order to maintain the same product specifications, this will need to be compensated for by increasing the reactor temperature. Examining your available hydrotreaters and their processing capabilities, as well as the availability for an increased demand for hydrogen in one area or another in the refinery, is important to avoid unexpected turnarounds.
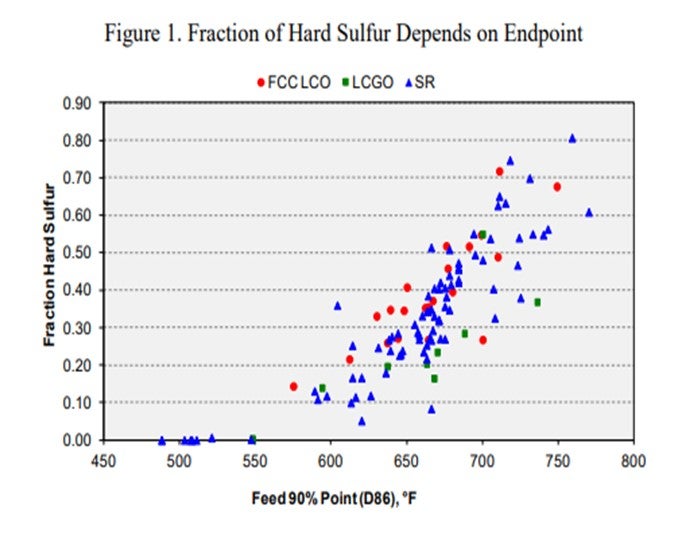
In order to rank which feed source to consider for increasing the FBP (final boiling point), a good understanding of the current situation in the refinery and the ultimate impact of the change is important. In general, cracked stocks (cokers and LCOs) are more challenging to hydrotreat and require a higher weighted average bed temperature (WABT) compared to a straight-run (SR) material at the same product targets. Coker stocks normally have higher sulfur and nitrogen content based on the nature of the feed to the coker and the coking process. These feeds also have a much higher olefin content (or Bromine number) than SR feeds. The higher concentration of sulfur, nitrogen, and olefins will produce a higher heat release when operating to the same product targets, giving rise to an increase in hydrogen consumption. When increasing overall diesel production by increasing feedstock endpoint coker stocks are probably the second-best option for catalyst longevity behind straight-run feeds.
Feeds from the fluid catalytic cracker (FCC) are much higher in aromatics than their SR counter parts and are especially concentrated in the polyaromatic content. This also gives these feeds a much lower API gravity relative to SR or coker stocks. The concentration of sulfur and nitrogen in these feeds is dependent on the presence of a pre-treater upstream of the FCC which can help in lowering the total sulfur or nitrogen content. However, the sulfur and nitrogen compounds in FCC are usually the more difficult refractory species requiring a much higher required WABT to achieve the same product specification (Figure 2).
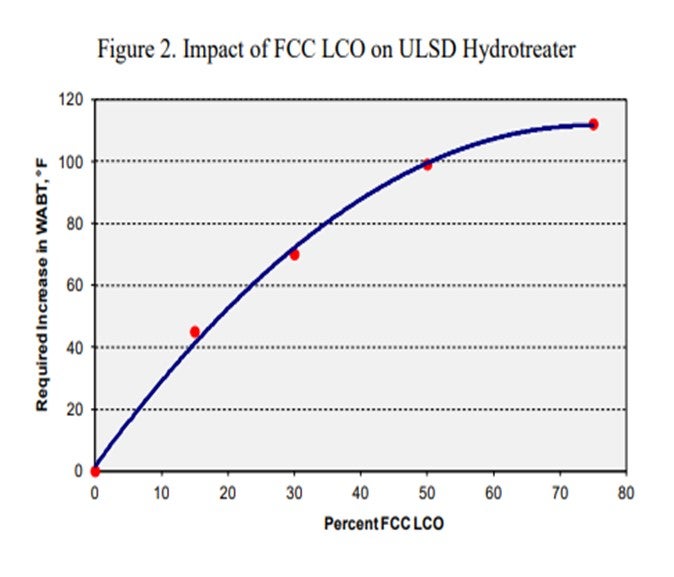
Not all feedstocks provide equal economic benefit. If your distillate hydrotreater has incremental hydrogen available and operates at high enough pressure, LCO may be the first choice for maximum economic return. LCO normally contains the highest amount of aromatics and therefore will provide the maximum volumetric expansion from hydrotreating. LCO will also undergo the largest increase in cetane across the hydrotreater as shown in Figure 3 below.
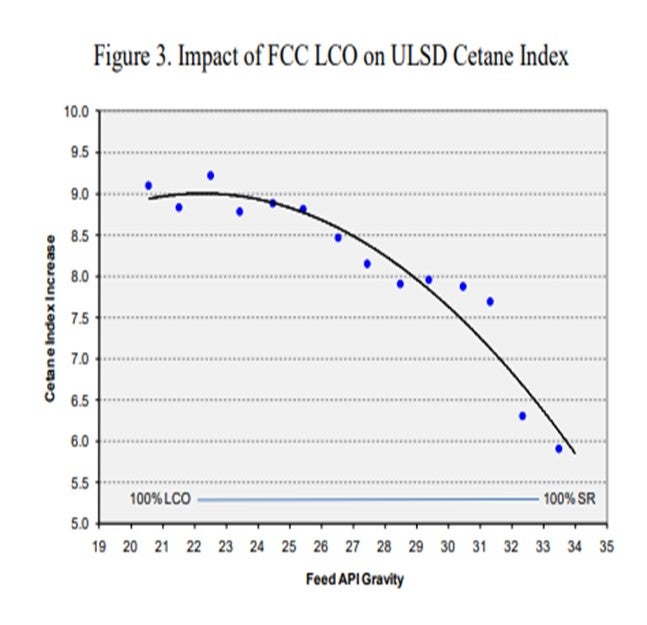
As always, ART is prepared to discuss these options and assist in making the best choice with the catalyst system already in use. We are also able to help you prepare for the next catalyst load in order to take advantage of these various paths.
DAVID VANNAUKER (Haldor Topsøe, Inc.)
The realized diesel feed endpoints depend upon the crude slate and overall refinery operations. From the hydroprocessing operational ease perspective, the virgin feeds should be maximized first, followed by the coker and then the FCC streams. In an economic environment favoring diesel production, keeping virgin and coker diesel boiling range molecules out of the FCC will maximize site diesel production and profits. There are additional considerations that impact the final realized feed endpoints. With waxy high paraffin content crudes, the virgin feeds may be limited by cold flow properties. The light coker gas oil typically has the same endpoint as the virgin feed, but sites typically have a lower endpoint for light coker gas oil due to coker drum cycles and the resultant coker fractionator instability. The LCO endpoint will be limited by unit operating pressure, hydrogen availability, and diesel pool cetane. In addition to very active distillate hydrotreating catalyst, Topsøe also makes distillate dewaxing catalyst, TK-932, which is added at the bottom bed of the reactor to isomerize the long normal chain waxy molecules to improve cold flow properties.
LARRY KRAUS (Criterion Catalysts & Technologies)
Stream value economics are refinery specific. In general, increasing DHT feed endpoint can increase DHT unit throughput and provide additional material for the diesel pool; however, feed endpoint has a critical impact on feed processing difficulty. Increasing the endpoint increases the multi-ring aromatic content along with the concentration and complexity of sulfur and nitrogen species.
Increasing feed endpoint makes achieving ULSD product specifications more challenging. Higher SOR temperature requirements, higher deactivation rates, and shorter cycle lengths are expected when increasing the feed endpoint. The benefit of increased feed endpoint is determined from the incremental value between the additional feed throughput and the cost of additional H2 consumption, the negative impact on product properties, and the reduction in cycle length. In general, the ability to increase feed endpoint is ultimately limited by the product T-90 specification.
Increasing the endpoint of cracked distillate streams, such as coker light gas oil and FCCU light cycle oil, typically offers the highest upgrading margin in the absence of a hydrocracker but the most processing difficulty in the hydrotreater. These highly aromatic streams contain sulfur and nitrogen species which require a high hydrogenation environment to meet ultra-low sulfur and cetane targets. Elevated hydrogen consumption and operating temperatures combined with additional coke precursors will shorten the hydrotreater cycle life. Maximizing the endpoint of the coker light gas oil and FCCU light cycle oil is an optimization between economic value and hydrotreater capability. Lower hydrogen partial pressure and higher space velocity units will be less capable of processing these streams having a higher feed endpoint.
Increasing the EP of straight-run distillate typically has less margin of improvement than for cracked stocks but increases available throughput. As a less aromatic stream, the endpoint is limited more by the T-90 specification than by the complexity of the sulfur and nitrogen species or cetane. Hydrotreater cycle life will be reduced due to higher required temperatures.