Question 39: In terms of hydrocracking, what different definitions of conversion do you use?
PEDERSEN (UOP LLC, A Honeywell Company)
Fundamentally, conversion is probably the most common operating target used for hydrocracking units. Conversion provides us with a measure of the amount of reaction or the amount of work that is accomplished in the unit. The simplest definition for conversion is typically this equation for gross conversion: a hundred times the fresh feed minus the unconverted oil, divided by the fresh feed; unconverted oil being the recovered fractionator bottoms.
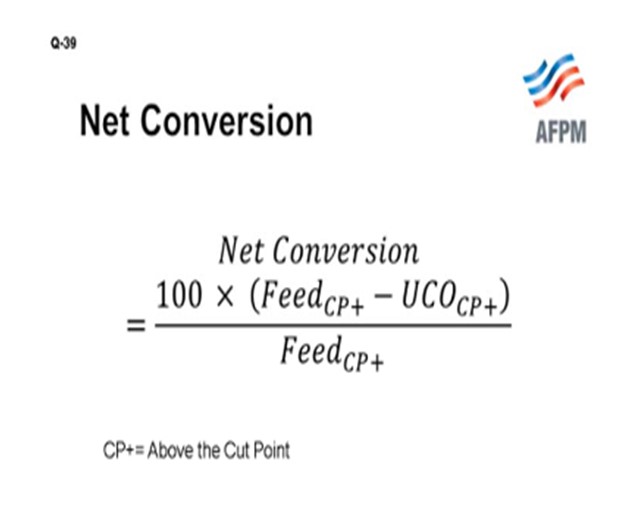
A conversion value only has meaning when it is defined relative to a specific cutpoint. If you do not define the cutpoint, you do not really have a usable conversion value. The cutpoint is the temperature dividing the converted products from the unconverted oil. At the cutpoint, the amount of product in the unconverted oil will exactly equal the amount or volume of unconverted material that turns up in the products.
Gross conversion, as we indicated, provides a measure of how much product is produced. However, in many cases we are interested in identifying how much work is really involved. Some feedstocks are more difficult than others. Particularly if we already have product in the feed, we do not have to convert that material. And when we take out the effect of product in the feed, we get the net conversion definition, which is similar to the gross conversion in form. Net conversion only considers the amount of feed and all the amounts of product or unconverted oil that are residing in the cutpoint plus boiling range.
The chart shows time onstream versus conversion. The blue data points indicate gross conversion. The red data points indicate net conversion. So we can see that in some cases, there is not very much product in feed and that the net conversion almost matches the gross conversion. In other cases, we get a disparity.
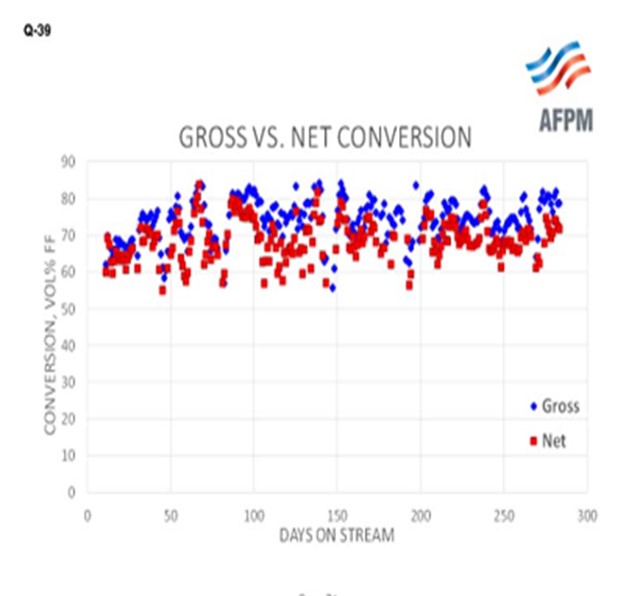
For hydrocracking units with recycle operation, we have an interest not only in the overall conversion, but also in how much conversion occurs on each pass through the recycle operation. So we look at conversion per pass. The definition is similar to the equation on the following slide: total conversion times fresh feed, divided by fresh feed plus recycled oil or sometimes cast otherwise as fresh feed, minus unconverted oil, divided by fresh feed plus recycled oil.
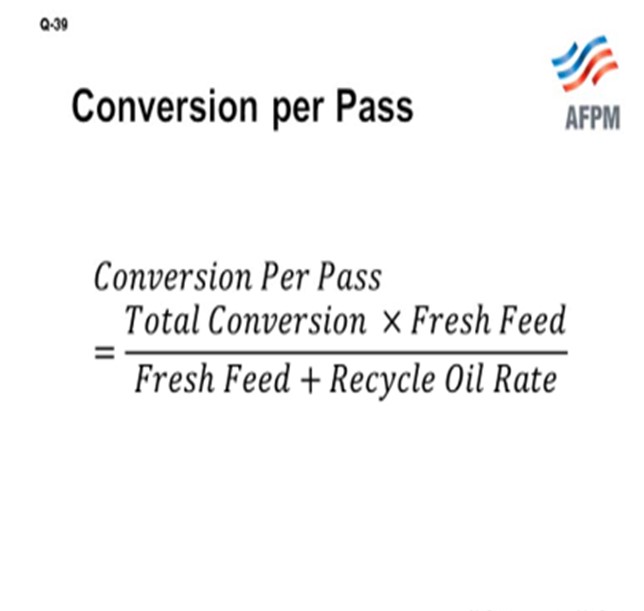
Total conversion versus conversion per pass are compared in this chart where, again, the blue points indicate gross conversion and the red points, conversion per pass. In this particular operation, the amount of conversion achieved on each pass was relatively much lower and less severe than the overall conversion. If we are looking at high conversion operation, it will be beneficial for us to recycle and take the conversion a portion at a time. In summary, when calculating conversion, the necessary information is volume of streams and distillation of fresh feed and product streams, if calculating volume conversion. Conversion on a mass basis also requires stream density information.
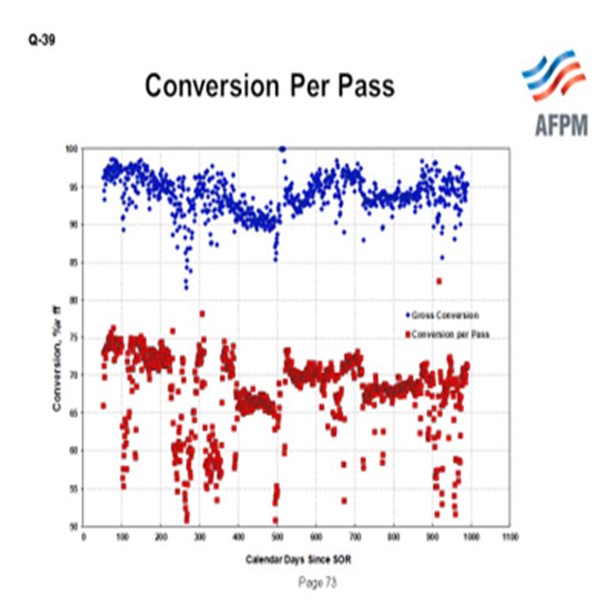
MORELAND (Valero Energy Corporation)
Across the Valero circuit, when we were setting up our unit monitoring systems at corporate, we took a look at all of the different conversion terms being used at each of our 14 plants. The slide lists some of the terms we were using. So depending on the licensor and who set up the initial system, we had apparent, gross, raw, corrected, kinetic, net, and true conversion. We have decided to try to narrow down this list a little, so we put the definitions into two categories: apparent conversion, which would really include the first three, and then what we would call the corrected conversion, which would really include the bottom four. These terms could all have similar meanings, the same meaning, or different meanings depending on how they are defined and the actual cutpoints.
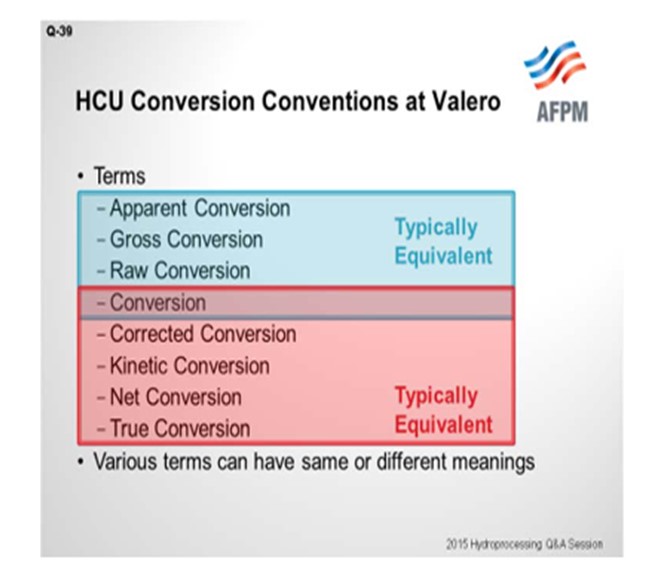
The next slide shows the two conversion definitions that we use most commonly now in our system. The first is the apparent conversion, which Mike covered in more detail. I think my equations are equivalent to his mathematically; they are just written up a little differently. This first is the feed minus bleed calculation. So, feed flow and UCO product flow are the only key performance indicators. The reason we use this one is because no laboratory data is needed. We do have issues with laboratory distillations. You can get a bad data point in your lab system that throws off your monitoring system, which then generates flags where flags do not need to be generated.
The second is the corrected conversion. This one is calculated daily, but we only track when the feed changes significantly or on a monthly review basis. This calculation not only requires the feed flow, but also the unconverted oil flow and flow of whichever is the next lightest product; typically, diesel and all the distillations. So in correct conversion, it is the cutpoint that is corrected. Typically, apparent conversion is done on a volume basis, which is how we sell the products, and then corrected conversion is performed on a weight basis.
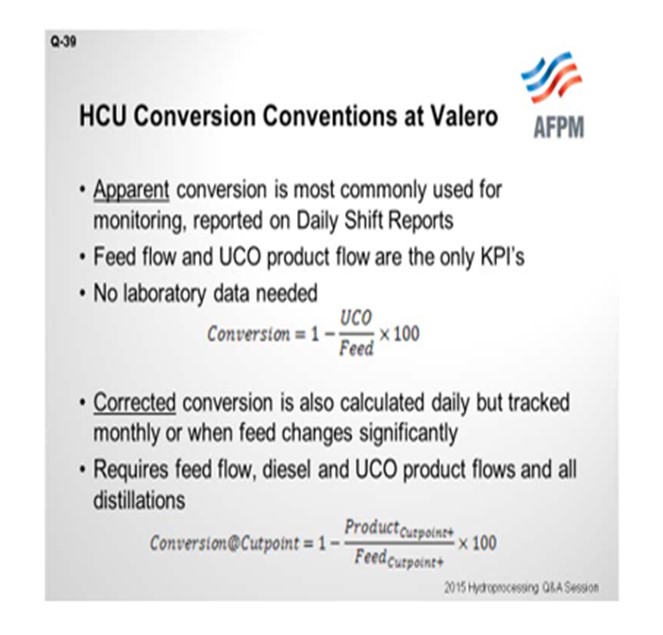
McARTHUR (Phillips 66)
I do not have a lot to add. We do very similar calculations as those that Andy just discussed. We do our corrected conversion calculations about once a week when we get a good mass balance across the unit. And then on our two-stage hydrocrackers, we will sometimes look at our per-pass conversion for various reasons.
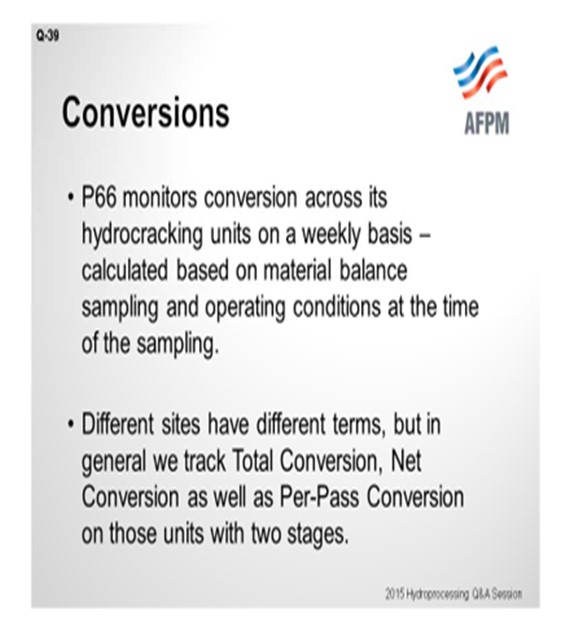
DAVID VANNAUKER (Haldor Topsoe, Inc.)
We have observed differences from refiner to refiner, and even within a refiner, from site to site. We always check to ensure that we are speaking the same language. The following definitions for conversion to 370°C are standard within the Haldor Topsoe, Inc. technology:
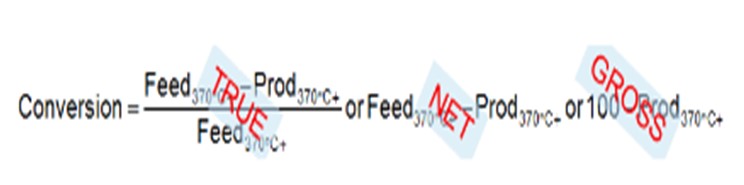
Note: If the conversion is in percentage, then each of the definitions must be multiplied by 100. In addition, you also need to clarify if it is weight percent conversion or volume percent conversion.
JOE FLORES (Criterion Catalysts & Technologies / Zeolyst International)
In general, all definitions of conversion need to be defined by a cutpoint, usually designated as the recycle cutpoint (RCP). The recycle cutpoint is defined as the effective cutpoint between the heaviest product and the main fractionator bottoms. Everything lower in boiling point than the RCP is designated as product, and everything higher in boiling point than the RCP is designated as feed. Therefore, all of the oil with a higher boiling point than the RCP is considered feed or recycle.
Within the definition of conversion, we normally distinguish between gross and net conversion, which can be calculated on a volume or weight basis and is reported as a percentage. Gross conversion does not consider the amount of material in the feed that boils lower than the RCP, while net conversion does. So, in general, net conversion is a more accurate representation of the severity of the hydrocracking catalyst system.
The definition of gross conversion is:
[(Feed flow - Product flow)/Product flow] x 100
Net conversion is defined as:
[(RCP+ in feed) - (RCP+ in product)] / (RCP+ in feed) x 100
Conversion can be calculated across the entire unit or, in the case of a two-stage unit, can be calculated across individual stages.