Question 39: How can we improve temperature control in steam methane reformer tubes? What monitoring practices do you recommend to avoid overheating the furnace tubes?
Ken Chlapik (Johnson Matthey Process Technologies)
Regular visual inspection of the reformer tubes is still an important practical way of monitoring the condition of the steam methane reformer especially during transients when online analytical, or instrumentation may be out of calibration or range for the conditions being seen. Historically, the most severe tube failures in SMR’s have occurred during transients, in particular start-ups. Most operators use pyrometry techniques on a shift or daily basis to measure peak temperatures at the bottom peep doors of the SMR. The operators are typically guided to highlight tube temperatures that are within 25-30°F of the tube metallurgy’s 100,000hr life temperature.
For decades, Johnson Matthey has provided steam methane reformer services to assist in highlighting areas of concern with the SMR, its current and projected performance at future conditions, and in particular balancing of the SMR tube wall temperatures (TWTs). JM uses a proprietary background correction methodology to correct for background radiation that is being seen with pyrometry techniques so that as close to true tube wall temperatures can be understood. This technique can then guide the operator on true hot or cold areas within the SMR as well as the ability to operate closer to the 100,000hr tube life temperature maximizing the production of the SMR.
Recently JM has developed with LAND, one of the leaders in SMR TWT pyrometry, the Reformer Imager which provides much more efficient and complete monitoring of the SMR. The Reformer Imager overcomes many of the limitations that exist with pyrometry techniques. Fitted on a probe of 2.2” diameter as shown below, the borescope lens captures HD videos, which typically ranges from 15 to 30 fps operating effectively in a temperature range of 1100°F to 3300°F. Each frame captures ~324,000 temperature data points in high-definition mode. The wide-angle field of view allows users to be able to identify areas that are challenging to locate by the human eye during visual inspection, as it provides sight of almost the entire lane from the peep door. The HD capabilities of the borescope provide focus along the width of the furnace. Operating near infra-red, i.e., at 1μm, the Reformer Imager is able to accurately measure temperature, with a stated tested accuracy of 1% of the measurement. The probe can be inserted into the furnace for multiple seconds of exposure to ensure completeness of readings from a peep door.
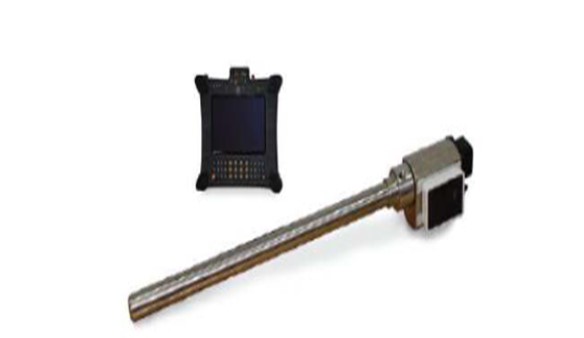
The aability to look at an image from all angles allows users to collectively pinpoint and dissect certain areas within the frozen frame image providing full SMR TWT inspections in about a third of the time. Because of the completeness of the data acquisition and accuracy, challenges of existing pyrometry techniques such as visibility, location, vibration, field of depth (visibility), operator variance are removed. The images below show how the data can be highlighted to look at TWT’s along a level of the row of tubes, profile along the length of a particular tube, or spot temperatures within the frozen frame image making a step change in the ability to effectively monitor SMR tubes.
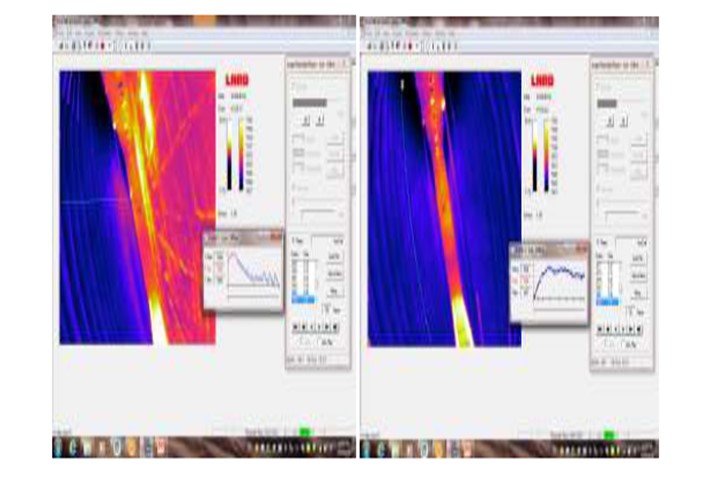
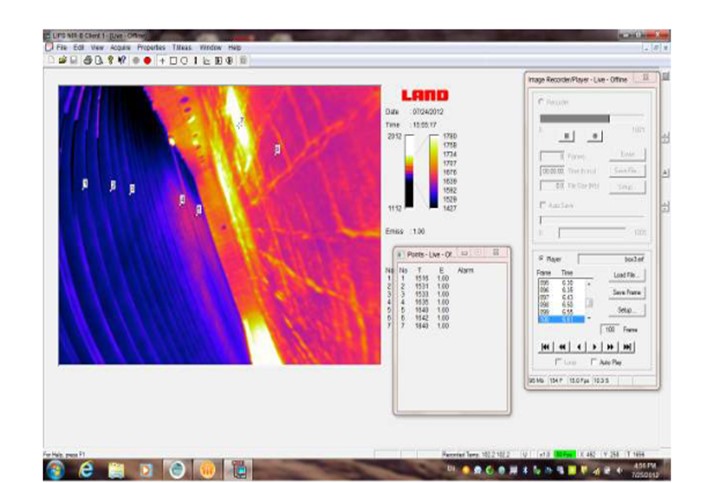
Separate from TWT measurement and monitoring from the furnace side of the reformer, JM has developed, with Daily Thermetrics Corporation, the SMRCatTracker®. (CatTracker® is a registered trademark of Daily Instruments the parent company of Daily Thermetrics Corporation.) The SMR CatTracker® allows an operator to measure on-line process side temperatures within the reformer tube. The SMR CatTracker® is a 1/4” probe with 11 sensing points that is inserted into select reformer tubesalong with the reforming catalyst. Every sensor is designed and manufactured to +/- 0.8°C @ 427°C to provide excellent accuracy at SMR process temperatures. The SMR CatTracker® is connected into the plants DCS system to provide online process gas measurement down the SMR tube.
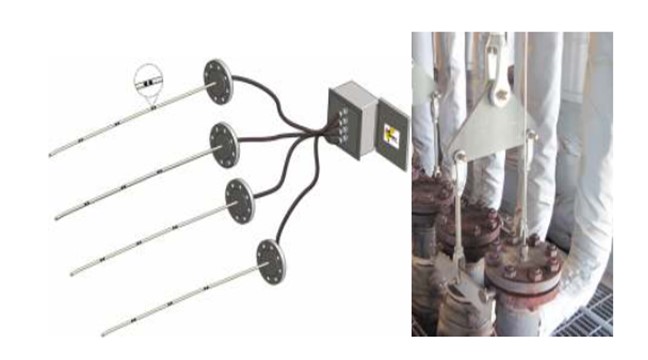
As described above, SMR TWT measurements are used to indicate mal performance of the steam methane reforming reaction within the SMR tubes and SMR tubes are most vulnerable during transients when much of the instrumentation is challenged to provide accurate measurements. As shown in the graphic below, the SMR CatTracker® accuracy provides very responsive measurement of process gas temperatures even during transients. This allows operators to respond quickly to undesirable changes in operation that lead to mal performance and potential overheating of SMR tubes. The SMR CatTracker® is one of the best ways to provide SMR operators the ability to see online and quickly respond to what is occurring inside the SMR tubes.
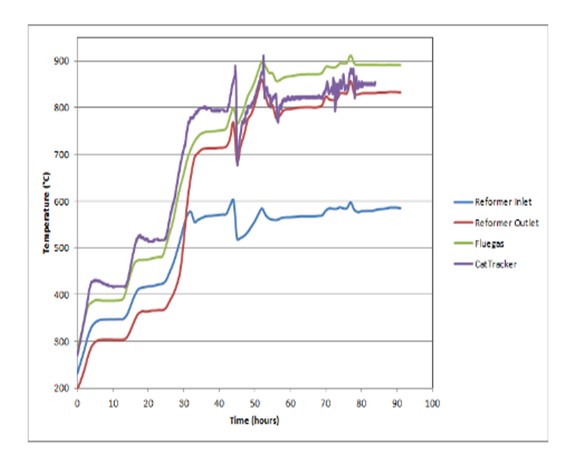
Gopi Sivasubramanian (Foster Wheeler USA Corporation)
Normally the reformer firing control is based on outlet manifold temperature and or bridge wall temperature.
Foster Wheeler’s Terrace Wall reformers have an inherent design advantage of providing stable temperature profiles for the catalyst tubes that prevents overheating of the catalyst tubes.
Pat Bernhagen (Foster Wheeler USA Corporation- Fired Heater Division)
Proper control of TMT (tube metal temperatures) comes from proper process flow distribution and proper burner flame shapes. It is desirable to operate near the normal design process flow rates to maintain the internal heat transfer coefficient and back pressure related flow distribution to the various cat tubes. This means at turndown especially high turndowns that the S/C ratio be increased to maintain enough back pressure to distribute the flow evenly into the cat tubes. The increased steam will increase the coefficient and lower the TMT. On the burner side, flame shape and stability is critical to keep the flames from impinging on the tubes. Burners should be operated at fuel pressures and compositions that the burner was shop tested and verified. The tips must be maintained and clear of debris/deposits. The design draft at the burner must be maintained. All burners should be on and with proper air register settings. Reformer designs that use a stabilizing wall for the flames are inherently better maintaining the flame shape and stability. Burners not fired against a bluff body, especially firing downward, have a greater need of monitoring of draft, air, fuel and register settings. Thermocouples in the outlet manifold at various points allow monitoring of outlet temperature variations indicating different heat transfer in certain tubes. Banding of the tubes – hot then cooler section along the cat tube usually near the top- indicate a poor AFPM 2014 Q&A Answer Book 35 catalyst load or catalyst poisoning in the hot region. There are new in tube catalyst thermocouple devices on the market to have an online monitoring of the process temperatures. Also, there are some TSTC (tube skin thermocouple) devices that claim to stand up to the high temperatures that these cat tubes run. In any fixed monitoring case (TSTC or in-tube TC) a pyrometer scan on a regular basis is recommended. This scan sees all the tube length and should cover any area where a TC is to verify its reading.