Question 38: What measurements and criteria do you use to decide when to change your gas and liquid chloride absorber material? How do you determine the selection of absorber material?
John Clower (Chevron)
For both gas and liquid service, Chevron monitors the inlet HCL/Total Chloride and replaces the adsorbent/molecular sieve based on material balance loading of chloride on the adsorber media. Chevron does monitor adsorbent outlet HCL/Total Chlorides, but as a best practice will change the adsorbent material before vendor maximum loading if breakthrough has not occurred. Spent adsorbent will become acidic and pass chloride as organic chloride to the downstream processes. Organic chlorides are difficult to detect by conventional tubes in gas service and will form HCL in downstream processing units.
This performance-based approach is not without problems, e.g., the accuracy of both chloride measurements and represented adsorbent capacity, and therefore requires a trial-and-error
approach.
Represented capacity of any chloride trap material will have been set the vendor to minimize high acidity conditions that lead to organic chloride and polymer (red/green oil) production. Commercially there are four main types of chloride adsorbent material available:
•Alumina
•Modified/Promoted Alumina
•Molecular Sieve
•Metal Oxide
Each of these materials is used in Chevron Refineries and joint ventures. Each adsorbent type will have various properties that can be used in making a decision on application:
•Total chloride capacity (HCL and Organic)
•Reactivity – potential for organic chloride and red/green oil formation
•Interferences (e.g., Sulfur)
•Cost per pound of chloride removed
Also, the design of the vessel used is important (L/D for adequate flow distribution, contact time) and can result in shorten life versus predicted breakthrough. Selection of adsorbent versus service will usually be made on a cost per pound of chloride removed.
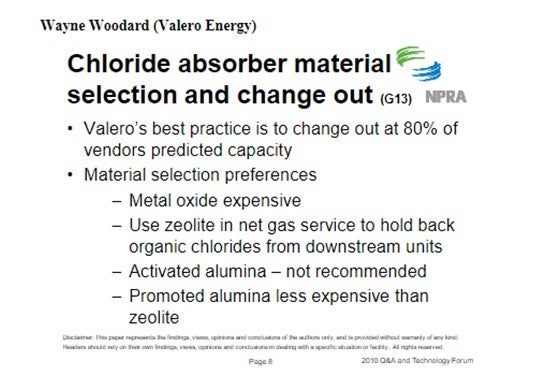
Janel Ruby (Johnson Matthey Catalysts)
Chloride can be removed from streams using various products. These chloride guard products can differ in the way they are manufactured and in the way they work in certain applications, so it is important to choose the right one for your needs. The most common products are chemical absorbents or promoted alumina adsorbents. Chemical absorbents remove chlorides by irreversible chemical reaction, meaning that the chloride is chemically bound within the absorbent. Chloride removal in promoted alumina is accomplished mainly by adsorption in which hydrogen chloride is adsorbed onto the alumina surface. Both types of beds are non-regenerable and require change-out at chloride breakthrough.
When determining which product is right for a particular service, it is important to evaluate the operating parameters of the chloride guard bed. The location of the bed in the reforming flow sheet, the operating temperature of the bed, and the normal and maximum inlet chloride levels are important factors to consider when selecting an absorbent type.
Promoted alumina products are available for liquid and gas services. Promoted alumina can work over a range of operating temperatures but chlorides that are adsorbed onto the material may desorb at higher temperatures which will decrease the effectiveness of the product in these regimes. These products also have a lower chloride capacity usually ranging from 12 to 15% wt/wt, and require a high change-out frequency. An area of concern when utilizing promoted alumina materials is the formation of undesirable side products. When the chloride binds to the alumina surface of the guard material, it creates surface acid sites. The acidic surface of the material can catalyze side reactions and lead to the creation of organic chlorides or high-molecular weight hydrocarbons called “green oils.” Green-oils not only foul equipment, but also the guard bed itself, which can cause difficulties in bed discharge (increased purge time) and disposal.
Chemical absorbents are the most favorable option for chloride removal. These products are available for use in liquid and gas services. Chemical absorbents work over a wide range of temperatures. These products have high chloride pick-ups, for example PURASPECJM 2250 is a mixed metal oxide chemical absorbent which can achieve a chloride capacity of 30% wt/wt in non-fouling, gas phase applications. As previously stated, these products remove chloride through an irreversible chemical reaction. The alumina structure present in these types of chemical absorbents acts only as a binder which minimizes the tendency for unwanted side reactions. PURASPECJM 2250 can commonly be employed with the use of just a single guard bed.
There a few other considerations surrounding chloride guard bed materials. It is important to avoid two-phase flow in these beds as this will affect the performance of the chloride guard. Both promoted alumina products and chemical absorbents have a higher pick-up in gas phase, non-fouling and non-wetting applications. In liquid applications, diffusion through the liquid film around the chloride guard particle is the rate limiting step and capacities are generally lower than gas phase duties because of the mass transfer effects. Chemical absorbent products, PURASPECJM 6250 and PURASPECJM 6255 were designed to address this concern. These products have a high capacity and specific pore structure to allow improved removal capacity. They are comprised of the same chemical formulation and micromeritic properties but represent two differing particle sizes; PURASPECJM6255 is manufactured as a smaller sized sphere. The smaller size provides better performance as this minimizes the liquid film through which the HCl must diffuse, reducing the depth of the mass transfer zone and leads to higher average chloride pick at the point of HCl breakthrough.
The presence of HCl or organo-chlorides (RCl) in the exit stream of the chloride guard bed will indicate it is time to change out the material. The life of the guard depends on how the bed(s) is configured and what type of product(s) has been installed. Unless the bed needs to be shut down for inspection or is involved in a larger turnaround plan, chloride breakthrough will be the main reason for a shutdown to replace product. Regular testing for chlorides in the exit stream will help to determine when change out is needed. In applications with longer life cycles (years) testing may only be needed monthly until the bed is getting closer to its expected change-out interval. In applications with shorter life expectancies (months), the frequency of testing should be at least weekly.
Throughout the life of the bed, it is important to measure the HCl and RCl levels both inlet and exit the chloride guard beds. It has been shown that when promoted alumina is used for HCl removal, it catalyses the conversion of HCl to organic chloride species that can then slip from the bed. If the operator is only measuring for HCl then this chloride slip can go undetected until downstream issues occur. Chlorides passing through the bed can cause corrosion of downstream equipment and formation of ammonium chloride that cause fouling and blocking of equipment e.g., stabilizer columns, exchangers and compressors.