Question 38: What are your concerns with processing FCC heavy cycle oil or slurry in a hydrocracker unit?
PEDERSEN (UOP LLC, A Honeywell Company)
In most of our experiences, I think that FCC heavy cycle oil and slurry oil are just nasty. [Laughter] Basically, the heavy cycle oils are known to be very challenging when run in a hydrocracker due to the high concentrations of coke and HPNA (heavy polynuclear aromatics) precursors. These contaminants lead to high reactor temperature requirement and high deactivation rates, as well as poorer yields; and actually, relatively poor product quality as well.
I want to step through an example that compares properties of different streams and explain why I just made the comments I did. This chart shows compositions of several typical feedstocks for a specific unit: straight-run gas oil, coker gas oil, light cycle oil, and heavy cycle oil. In looking at these different streams, we can see that the light cycle oil and the heavy cycle oil stand out by the predominant amount of aromatics content, and in the case of the heavy cycle oil, the really high concentration of the aromatic heteroatom materials. In this chart, the yellow bar represents the aromatics content, and the heteroatom compound concentration is the dark blue bar on the right-hand side.
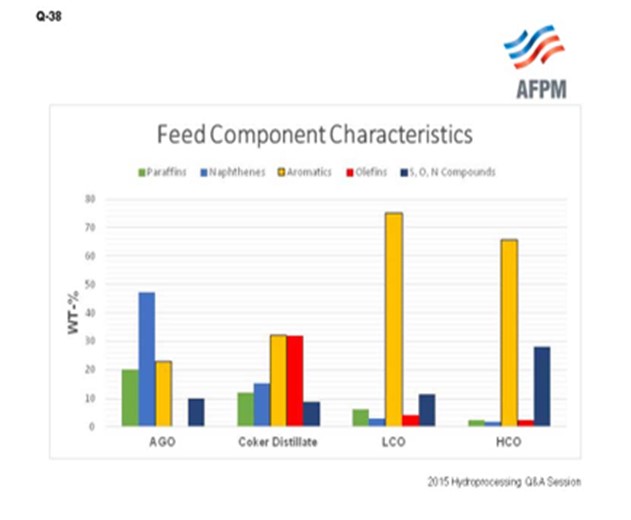
The next chart drills down to a finer characterization of light cycle oil versus heavy cycle oil. Light cycle oil is a favorite hydrocracker feed in many operating units. We can see that the type of aromatics in light cycle oil is skewed to the one- and two-ring compounds. In some cases, particularly high conversion FCC operations will give a larger contribution from the three-ring compounds. Typical LCO does not have any of the four- and five-ring compounds (the red and dark blue bars) found in the heavy cycle oil, which are the compounds that become problematic when processing heavy cycle oils.
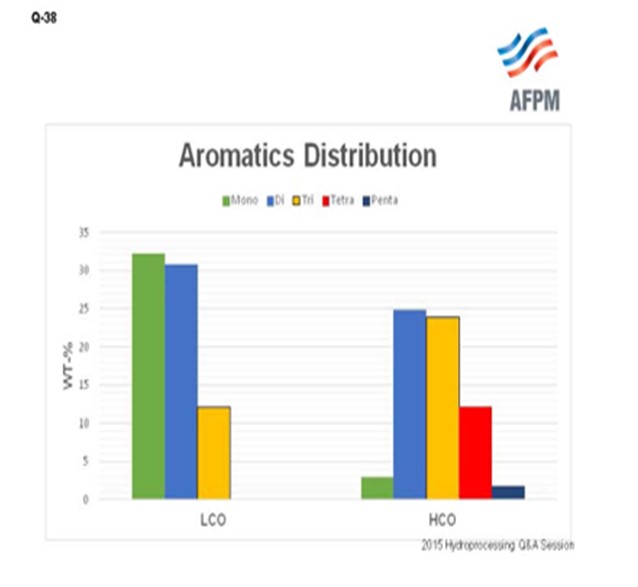
A series of hydrocracking pilot plant tests were run on a combination of the analyzed feed streams, which included processing increasing amounts of heavy cycle oil while backing out straight-run stock. We found that even with small amounts of heavy cycle oil, there was a significant impact on temperature requirement. In the next chart, we see that for each approximately 5% increment of heavy cycle oil, there is an increase in pretreat temperature requirement of about 5°F per 5% increment of heavy cycle oil: whereas with the hydrocracking catalyst, 5% incremental HCO increased temperature requirement 11 to 12°F. The increases in temperature requirements are directly related to the four- and five-ring aromatics in the feed blend. These compounds are, as I said earlier, difficult to convert and condense to form HPNAs, leading to higher reactor temperatures.

The response in the prior chart showing increasing temperature requirement with increasing percentage of HCO (heavy coker oil) in the feed blend correlates directly with the amount of four- and five-ring aromatics compounds in the feed. In addition to the higher temperature requirement, because of the aromatic nature of the material, hydrogen consumption also increases dramatically with HCO content. In the case of 20% HCO in the feed, we saw a 30% increase in hydrogen consumption. Despite the increase in hydrogen consumption, the quality of the distillate products was still very poor.
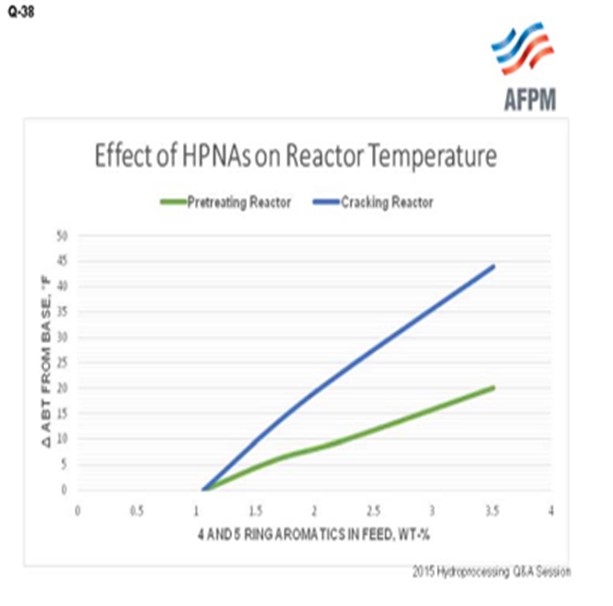
In conclusion, I think we would like to generally steer away from heavy cycle oil in hydrocracker operations. There are not a lot of FCC units that pull a separate HCO product; but if a refiner chooses to process heavy cycle oil, it should really be in a high pressure hydrocracker unit to experience success.
MORELAND (Valero Energy Corporation)
We are getting asked this question every now and then, generally from some of our internal folks who look at the lowest value stream in the refinery and one of the highest and say, “Why can’t you do this?” So these are some of the guidelines that we put up and some of the concerns about processing slurry oil as hydrocracker feed. The first concern is solids handling. Fines from catalyst or particulates, as well as some of the contaminants that Mike mentioned – nickel, vanadium, and antimony – could be a concern from catalyst additives. Other contaminants from heavy feed – for example, Conradson carbon residue or asphaltenes – could also be an issue. I think Mike hit on the hydrogen availability or high hydrogen consumption, as well as concerns with the diesel properties and the high concentration of aromatic nitrogen species calling for increased temperature requirements for pretreating and cracking. I do want to put in a plug. Valero, at one point in the past, operated an FCC slurry hydrotreater for low-sulfur fuel oil production. So, I was made aware of that as I was preparing these slides. It was at the Alma Refinery, which we no longer operate.
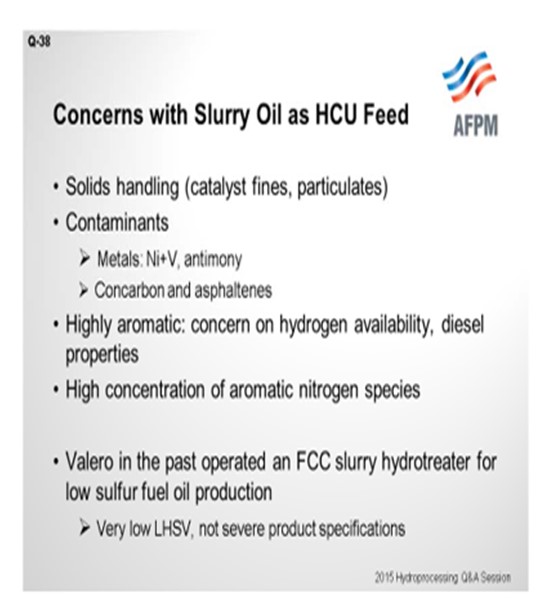
However, Mike also talked about heavy cycle oil. We do operate five LCO (light cycle oil) hydrocrackers that have quite high feed endpoints. I often get asked, “What is the limit on the endpoint for these feedstocks.” It typically falls into one of these three categories: either finished diesel properties; the T90 specification of 640°F, which is a typical number; or pretreat catalyst activity for sulfur removal in these units’ bottom stream. We are trying to make ultra-low-sulfur diesel – meaning, a 10- to 15-ppm sulfur requirement – and then, finished diesel cold flow properties. So, if you look at our five LCO hydrocrackers operating today, the endpoints here – other than Memphis, which is limited somewhat by cloud point – are pushing 800°F on the LCO endpoint. The specifications we set are either the diesel pool T90 or T95. You can see our economic models run those right up to the maximum limit that we can process in those units.
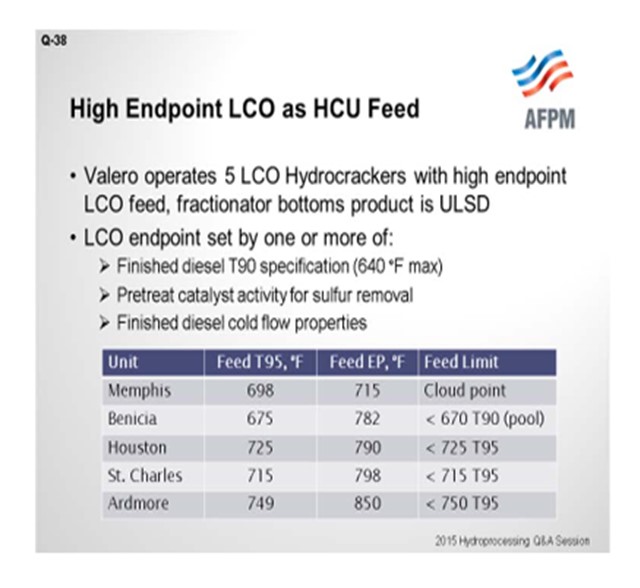
GEORGE HOEKSTRA (Hoekstra Trading LLC) Andrew and Mike, you both mentioned heteroatoms in the heavy aromatics as a factor. Do you think that it is the aromaticity itself that governs the difficulty of the feed, or is it like nitrogen content where the heteroatoms themselves have a separate effect?
MORELAND (Valero Energy Corporation) I will take a stab at it. Looking at the nitrogen content, I think we see that as the molecular weight of those nitrogen compounds increases, it becomes increasingly difficult to do the required HDN (hydrodenitrification) reactions. So, 1,000 ppm of nitrogen weighted towards the lighter end of the stream is not near as inhibiting as 1,000 ppm of nitrogen towards the heavy end.
PEDERSEN (UOP LLC, A Honeywell Company)
Thanks, Andy. George, I will follow up on Andy’s comments. Basically, your access to the contaminant that you want to remove, typically nitrogen, is much more difficult and more sterically challenging with the larger aromatic compounds. The process needs to go through much more of saturation – in some cases, cracking of peripheral rings – before actually addressing the nitrogen atom that is buried in the material. So, what I am getting at is that those two issues are intertwined.
ROGER LANOUETTE (Monroe Energy, LLC)
A quick question for clarification: The 800°F that you mentioned, is that SimDist (simulated distillation)?
ROGER LANOUETTE (Monroe Energy, LLC)
A quick question for clarification: The 800°F that you mentioned, is that SimDist (simulated distillation)? MORELAND (Valero Energy Corporation) I believe these are SimDist D2887s.
UNIDENTIFIED SPEAKER I want to add one more comment about this highly aromatic component: the secondary refinery streams. I believe we are all talking about fuels, but the hydrocrackers are also used for making lubricant-based oils. In fact, for certain Group II applications, especially for heavy Group II lubricants, we are seeing that there is an incremental requirement, not of VI (viscosity index), which comes from higher hydrocracking and better-quality feed, but rather the KV (kinematic viscosity) target of 40, which defines and improves the yield of those Group II heavy oils.
So, we have developed certain applications of these secondary highly aromatic streams, like aromatic extracts and heavy cycle oil from FCC. We have also come up with a particular reactor or design where we use certain tri-metallic, self-supported, hydrotreating catalyst and try to avoid too much hydrocracking of these molecules. However, we try to improve the overall naphthenic content of the unconverted oil for this Group II heavy oil. So, there is a huge application now and another area we are working on.
TARIQ MALIK (CITGO Petroleum Corporation)
You mentioned the light cycle oil or its endpoint, but the question really addressed heavy cycle oil. So, if you are drawing a limit on the endpoint of heavy cycle oil, where would you draw the limit, Andrew?
MORELAND (Valero Energy Corporation)
We have said that the limit here is based on the size of the reactor size. At the end of the day, it is making sulfur specification for ULSD (ultra-low-sulfur diesel). We run out of pretreat, and that is what sets the limit. So as we go deeper in the LCO, we end up reaching the limit on making ULSD. If we went to a heavy cycle oil processing, we would need a lot higher conversion here to make sure our bottoms product hits the ULSD’s specifications.
TARIQ MALIK (CITGO Petroleum Corporation)
At our Lake Charles refinery, we regularly feed FCC heavy cycle oil to the hydrocracker. It has an endpoint specification of 880°F. We typically hit the less than 860°F endpoint on purchased light cycle oil fed to a hydrocracker without too much of an issue. But on a lower pressure ULSD unit with light cycle oil in the feed blend, you will have to draw a lower endpoint limit because this is a refractory compound and aromatic saturation is much lower here.
MORELAND (Valero Energy Corporation)
Are you making ULSD with the bottoms?
TARIQ MALIK (CITGO Petroleum Corporation)
Yes. Well, it is, at least when the catalyst is fresh.
MORELAND (Valero Energy Corporation)
Okay. [Laughter]
TARIQ MALIK (CITGO Petroleum Corporation)
But you can blend that purge/bleed stream into a larger ULSD product pool without violating the sulfur specs on ULSD product.
MORELAND (Valero Energy Corporation)
At the St. Charles unit in particular, there have been times when we had excursions on endpoint that have put us off spec for diesel sulfur. So, when we exceed this, we do see that we will make a 20+ ppm sulfur product.
TARIQ MALIK (CITGO Petroleum Corporation)
You are talking from the viewpoint of the ULSD owner?
MORELAND (Valero Energy Corporation)
Yes. Well, from this LCO hydrocracker.
MEL LARSON (KBC Advanced Technologies, Inc.)
Just one comment that we are throwing around here. Do not forget that hydrogen partial pressure makes a big difference. We are talking about 1,000 or 2,000 pounds, which can make all the difference in the world as to whether you can process more or heavier hydrocrack material.
MORELAND (Valero Energy Corporation)
Absolutely.
WENDY WILDENBERG [Flint Hills Resources, LP (FHR)]
I have a question for Andy or Mike. We talked about nitrogen inhibiting sulfur removal in these difficult high endpoint heavy cycle oils. We also talked about sterically hindered sulfur molecules. How much does the polarity of a four-plus ring aromatic have to do with the difficulty of removing sulfur versus a non-polar molecule (one-, two-, or three-ring aromatic)?
UNIDENTIFIED SPEAKER
Basic nitrogen?
WENDY WILDENBERG [Flint Hills Resources, LP (FHR)]
Yes. How much does basic nitrogen or other polar aromatics (four+-ring molecules) have to do with how difficult that particular stream is to remove difficult sulfur?
PEDERSEN (UOP LLC, A Honeywell Company)
I do not know an exact answer, Wendy. But generally speaking, there is a lot of interaction of more complex oxygen-containing and nitrogen-containing compounds with key catalyst sites. All have a polar characteristic, so there is a correlation between the two functions.
MORELAND (Valero Energy Corporation)
Just from a catalytic perspective, those four-ring larger molecules are going to adsorb on the catalyst surface a lot stronger, which is good for removal but also bad, from a catalyst inhibition perspective.
DAVID VANNAUKER (Haldor Topsoe, Inc.)
Heavy cycle oil and slurry contains fines, particulates and heavy complex aromatics. The fines and particulates require filtration to ensure stable operations. Some sites plan on performing skims. The value uplift can be enough that the expected downtimes required for skims can be justified. The heavy complex aromatics contribute to heat release and catalyst coking rates. The units need to have sufficient hydrogen and compressor capacity to handle the additional hydrogen consumption and heat release. These heavy molecules are also coke precursors. Recycle operations can experience increased coking rates and shorter cycle lengths due to the HPNAs. Increases in hydrotreating and hydrocracking activities for heavy aromatics can alleviate these issues.
JOE FLORES (Criterion Catalysts & Technologies / Zeolyst International)
FCC heavy cycle oil, and especially slurry oil, will have solids that need to be removed before processing in a hydrocracker, or rapid increase in pressure drop of the first reactor bed will result, which will either restrict unit rate or require a shutdown for a catalyst skim. In addition:
1. These streams contain nitrogen and sulfur species, which are very difficult to treat, and which will have a negative impact on the pretreat and cracking ROT (reactor operating temperature). Pretreat WABT (weighted average bed temperature) will usually need to be increased, which will reduce the cycle length of the catalyst.
2. If the nitrogen compounds are not removed, they will have a negative impact on the cracking catalyst, which can result in reduced cycle length and reduced selectivity.
3. The increased feed sulfur to the unit can result in high sulfur levels in the HCU products.
4. The FCC heavy cycle oil and slurry are also highly aromatic, which will increase hydrogen consumption.
5. To process these streams, the gas-to-oil ratio and makeup hydrogen need to be sufficient.
6. Another consideration is the disposition of the unconverted oil from the hydrocracker. If this unconverted oil is sent to the FCC and the resultant FCC HGO (heavy gas oil) and slurry oil are sent back to the hydrocracker, a long recycle loop can be created. In this scenario, if the bleed off of the hydrocracker is insufficient, a buildup of PCAs (polycyclic aromatics) can result, which could foul the equipment in the hydrocracker and lead to rapid catalyst deactivation.