Question 38: How do you monitor coke drum overhead lines to determine when cleaning is required? What cleaning techniques are effective and which are ineffective?
GAMBOA-ARIZPE (CITGO Refining & Chemicals, L.P.)
The relationship between coke drum operating pressures and C5+ liquid yield is fairly well-known across the petroleum refining industry. I have a general relationship that I pulled off of the internet from an issue of Hydrocarbon/Hydroprocessing Magazine. You can actually do a Google search and similar relationships will pop up. Generally, lower coke drum pressures produce higher C5+ liquid yields, which are higher value products; and higher coke drum pressures produce more pet coke (petroleum coke), LPG (liquefied petroleum gas), and off-gas, which are lower value products. This effect is consistent across a diverse array of coker feed slates. Most refiners routinely clean the coke drum overhead vapor outlet header in an attempt to preserve the lowest possible coke drum operating pressure. Usually, this knob is available to Operations. Given the batch nature of the delayed coker process, it equips the unit with a built-in ability to isolate individual coke drums and some of its respective ancillary piping. In other words, the only other readily available pressure reduction opportunity that does not require an extensive outage can be captured by cleaning the coke drum overhead vapor header; although some facilities are also equipped with the ability to clean condensing equipment in the fractionator overhead system online, which would also have the same effect.
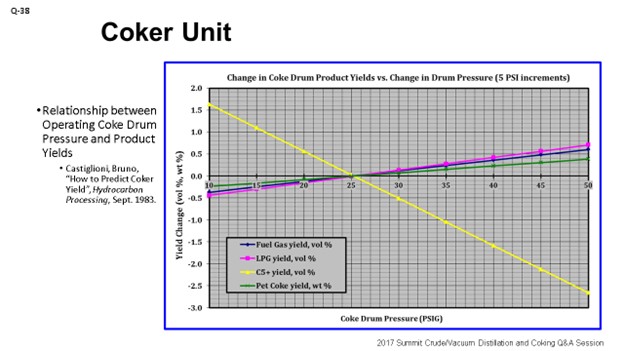
Planned decoking operations of the coker furnace, or even unplanned outages, also provide a sufficiently large enough window to capture this opportunity to eliminate unwanted pressure drop. So, when under a time crunch, the cleaning of just the coke drum overhead vapor and nozzle throat is sufficiently beneficial and can provide an appreciable rate of return (on maintenance investment). In fact, this section of the vapor header should be cleaned more often, because it is upstream with a quench oil injection stream and is more susceptible to coke buildup. The cleaning of the coke drum overhead vapor header can be justified whenever the expected boost in drum yields can cover the cost of the maintenance expense. Removal of sufficient coke within the vapor header – enough to shift the operating drum pressures by, say, 2 psi (pounds per square inch) – may not seem like much, especially because the increase in C5+ liquid volume may be lost in the noise of the product flow indications. However, a yield improvement of 0.20 to 0.25 vol% (volume percent) in higher-value products is an appreciable shift on unit margins.
Many facilities conduct routine, single-gauge pressure surveys of the coke drum overhead vapor header or track pressures with DCS-monitored transmitters to determine when coke buildup along the walls of the header becomes hydraulically restrictive to the vapor flow, thereby imposing a higher backpressure on the coke drums. Other metrics – such as pseudo-normalized pressure drop across a vapor header, usually a dP (delta pressure; ∆P; pressure differential) over MBPD (thousands of barrels per day), or the normalized pressure drop across a vapor header dP over the flow squared – are also monitored to adequately measure the performance gap versus the theoretical clean state. Sometimes field observations alone, such as whistling on the drum top head deck, are associated with higher dP and suggest that the vapor nozzle throat or the affected coke drum needs cleaning.
Because of the mechanisms involved – a combination of both cracking and polymerization reactions, the concrete-like coke layer that is deposited along the coke drum overhead vapor header is generally very hard. Third-party hydroblasting services are usually required to spall off the coke layer along the majority of the line via strategically located cleanup flanges. These maintenance hydroblasts require larger planning windows due to limited accessibility and the need for cranes, as well as to account for the longer length of line cleaning. The coke drum throats, however, can be cleaned more frequently with mechanical chipping or a local hydroblasting lance. Cleaning of the drum throats can usually be squeezed into longer coke drum cycles and should not produce any ‘lost opportunity’ barrels.
In our experience, the most effective third-party cleaning methods involve the use of hydroblasting setups, which can spray tighter jet streams closer to the surface of the wall as opposed to hydroblasting setups that create broader jet streams more than 6 inches away from the coke layer; for example, rotating nozzle tip setups. Setups with alternating blast pressures do appear to be more effective as well. Recently, the coke drum overhead vapor headers were cleaned at one of CITGO’s facilities by the more refined method described above. The task was completed in record time versus the more generic hydroblasting setups that had been used in the past. Erosive discharge pressures over 25,000 psi (pounds per square inch) should probably be avoided.
LÉGARÉ (Andeavor Martinez Refinery)
The Andeavor site where I work went through a multiyear process to address this problem. The coker at our refinery started in 2008; and for the first couple of years, we did not really see this as a problem. It eventually became known to us that this increase in back-pressure was affecting our yields in a measurable way. So, we started to work with our Planning Department and said, “Okay, we want to propose an overhead line cleaning and take one of the drums out of service.” We talked about the benefits that Héctor discussed and agreed that it really looked like noise in our instrumentation. We were able to prove it using process simulations. When we ran the math, we were able to translate it into millions of dollars in appreciable yields over the do-nothing scenario.
The number we were using was a 1 psi increase in the back pressure on the drum. It was going to shift about 0.25 wt% of that feed into coke, not the gasoils that provide greater value to the refinery. We started to trend the data and showed the Planning Department how the system was degrading over time. We managed to convince them that we should go forward with this process, and we eventually came up with the system where we were cleaning each one of our four drums on a quarterly basis. So, it was integrated into our planning process. We took the rate cuts and actually had one of our engineers up there taking a look at the as-found condition so he could deduce what improvements we could be making in coker operations and installation of insulation in the overhead line to see what could be done to reduce that coke make over time. Mechanical cleaning is what we found works best, similar to what Héctor said about using lances and hydroblasting. We wanted to make sure we also had Operations on hand to buy off on the post-cleaning conditions. That way, before things got buttoned up, we had someone from Ops reviewing it to make sure that the mechanics were telling us the truth on how clean it was.
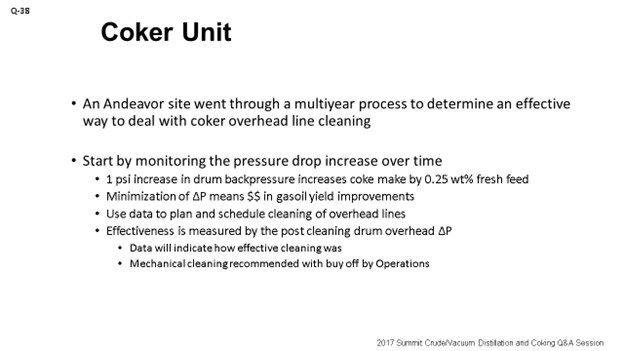
This slide shows the trends our Operations engineers were using to measure the effectiveness of the cleaning process. Again, this is a normalized dP in the overhead systems. So, like Héctor said, you can do this with a single pressure gauge or you can use instruments on the DCS. As our coker is of recent construction, we had pressure indication on the DCS. We would track the dP over time. You can see how each time we took that drum out of service to perform the cleaning, it got back close to zero; then, we would start increasing the backpressure again. Over time, similar to what I said during the spalling conversation earlier, you have opportunities to clean your overhead lines as well. If you are low on rates, you can go after the overhead line cleaning. Then when you are pushing rates again, you will get the full yield benefit right away. So, the opportunities on cokers on a coker-limited refinery go hand-in-hand.
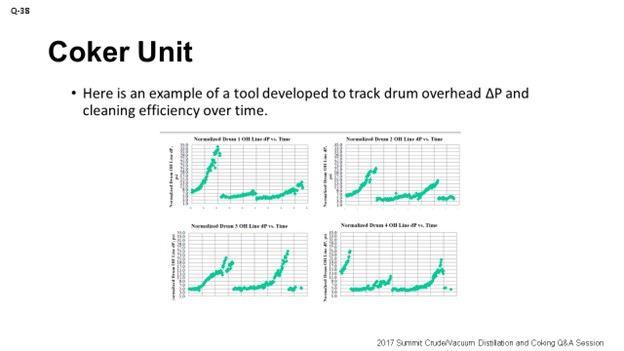
ERIC LÉGARÉ (Andeavor Martinez Refinery)
This question raises an interesting review of the last nine years of coker operation at an Andeavor refinery. It began with monitoring the increase in pressure drop over time in each drum overhead as part of the process engineer’s health monitoring effort. Higher pressure drop reduces gasoil yields in the coker fractionator and profitability for the refinery. Establish graphs that demonstrate the relationship between pressure drop and yield loss and make them visible to the organization.
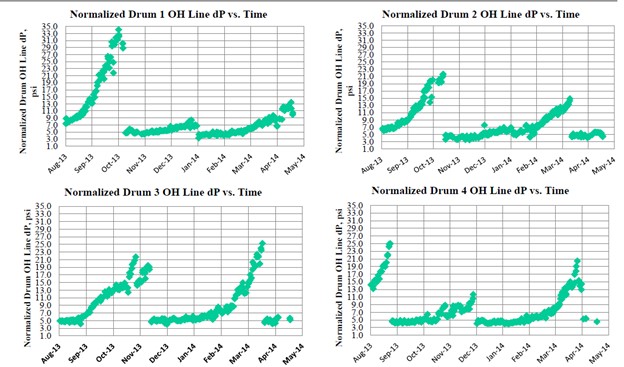
The Coker Operations Team will then work with the Planning Department to plan an overhead line cleaning event to recover yields using improved coker yield economics to justify the work. The refinery then moves towards planning the cleaning as a regular event by working it into the refinery operating plan, similar to online spalling. The coker rate was reduced by 15 to 20% during the 40 hours it took to clean the overhead line, but it was offset by the significant gains in product yields (basis was 1 psi drop in operating backpressure reduced coke make by 0.25 wt% of the fresh feed). Overhead lines were mechanically cleaned every three months based on the economics of yield improvement versus crude rate reductions. Effectiveness of the cleaning method was measured by the post-cleaning operating pressure of the cleaned drum (refer to charts on the slide). Whenever possible, the operating pressure following the overhead line cleaning was compared to the SOR condition following a TAR (turnaround). Operations personnel bought off on the cleanliness of the overhead line after each cleaning via visual inspection prior to it being returned to service. The overhead line cleanings resulted in measurable gains in coker gasoil yields on an annual basis.