Question 38: Does the panel have experience with mercury contamination of feedstocks to gasoline processing units? What are the typical crude sources that can potentially contain mercury? What units are likely to be most impacted, and how?
DUBIN (Axens North America)
Mercury is an ever-increasing problem that we see. It is coming in higher quantities and in more various crudes. Crudes from the East Asia region have historically been known to contain quite a bit of mercury. We have experience with a Thai crude that contained 3,000 [weight parts per billion (wppb) of mercury. However, a neighboring country has crude with only 10 wppb of mercury. The crudes of the Americas and Venezuela have been seen with mercury contents of up to 4,000 wppb. This variation tells us that the mercury impact on your refinery is going to be very site-specific and will depend on your particular blend and the source of your crude. At the same time, gas condensate streams, which are becoming a larger picture of the refinery feed, have been sampled with up to 2,000 wppb of mercury.
Where does the mercury go in the refinery? It can be found everywhere downstream of crude fractionation. Predominantly, it concentrates in the straight-run naphtha portion of the refinery; however, the most volatile species end up in the LPG (liquefied petroleum gas) and light ends. This leads to contamination in the light ends units, such as steam crackers, gas plants, and gasoline processes. For the gasoline processes, the major units in question are reforming,
isomerization, etherification, and hydrogenation.
The impacts from mercury contamination could be consolidated into three main groups: process impacts, finish stock impacts, and effluent impacts. Process-wise, we have seen aluminum heat exchangers in LPG plants that have been severely corroded due to mercury. For
the gasoline units, poisoning of catalyst is the major concern. Anywhere from 10 wppb to 20 wppb of mercury has been known to kill various precious metal catalysts. Therefore, it may not take much mercury in your crude to bring down a unit and short cycle it.
Finished products: If any mercury makes it into your finished products, say, a feedstock for a downstream user that is using your product as a steam cracker feed, then contamination by mercury may devalue that feedstock or make it unsellable, based on that user’s requirements, thereby creating a massive financial impact.
On the effluents, emission of mercury to the air or to the ground through purges is a concern, as is refinery personnel. Maintenance on any equipment that handles mercury then becomes an issue during turnarounds.
It must be kept in mind that hydrotreating mercury-containing feedstocks do not remove mercury; it only changes the mercury from its organic state to its elemental state. You will still need a guard bed downstream of the hydrotreater to remove the mercury and protect your downstream processes. Axens can provide sampling systems to determine exactly what species of mercury you have present. And through our RAM II process, we can design a guard bed
system to remove mercury down to the detectable limit of 1 wppb.
KOONTZ (HollyFrontier)
I do not have too much to add. At HollyFrontier’s refineries, primarily due to where we get our crude – which is from Canada and the Mid-Continent, we have not experienced mercury problems in any of our catalyst waste. We have not noticed any problems that we would attributeto mercury.
DAVID SMITH (UOP, A Honeywell Company)
I agree with all of Geoff’s comments, which were quite thorough. I have found that it is quite common for refineries in Southeast Asia to have mercury contamination in many of their hydrocarbon streams. Where they typically remove the elemental mercury is out of the naphtha stream downstream of the hydrotreater, as Geoff indicated. That appears to be the optimum location and the easiest way to remove the mercury with a non-regenerative mercury adsorbent, such as GB-346S.
PATRICK BULLEN (UOP, A Honeywell Company)
In units that do not have the guard bed technology, we have noticed that the typical stripper receiver and stabilizer receiver in the isomerization unit are places where mercury will accumulate. It becomes HSE issues when you do inspections at turnarounds. There is a little pool of mercury in the receiver, and there are typically no boots on the stabilizer receivers in the isomerization units to drain out the mercury; so that makes it more difficult, from an HS&E
perspective.
DUBIN (Axens North America)
Axens has significant experience in assisting refiners who have found mercury in their feedstocks. The quantity of mercury found in crudes can quite significantly depending on the region, and even the source of crude within a region with levels from as little as 1 wppb up to4,000 wppb of mercury being observed. Crudes from the East Asia region have been known to contain mercury. Axens has experience with Thai crude with 3,000 wppb of mercury. Yet,
crudes from nearby countries may have as little as 10 wppb of mercury. Closer to the U.S., Venezuelan crudes have been observed with up to 4,000 wppb of mercury. But mercury contamination is not limited to just crudes. Gas condensate streams with levels of mercury in the 2,000 wppb range have also been found.
A wide range of mercury species can be found downstream of the crude units, but significant amounts mercury is often found in the straight-run gasoline portion of the crude. At the same time, the most volatile mercury species are usually found in the light ends/LPG portion of the crude. This leads to mercury contamination issues predominately in light ends/LPG units (gas plants, steam crackers, etc.) and gasoline processing sections (isomerization, reforming, and etherification). The impacts on these units can be essentially grouped into three main categories, process impacts, effluent impacts, and finished product impacts.
Process impact wise, catalyst poisoning is the most common. Impurities in the wppb level have been known to cause cycle life degradation in gasoline hydrogenation units. But catalyst poisoning is not the only concern with mercury contamination. Severe corrosion of aluminum plate heat exchangers, in both LNG (liquefied natural gas) facilities and ethylene plants, has been observed and traced back to mercury.
The effluent impacts are harder to both identify and quantify, but they are still quite serious. The potential exists for the emission of mercury through effluent streams to both the air and to the ground. Protecting refinery employees from mercury contamination is also a key consideration. During their daily rounds, refinery personnel can be exposed to mercury in both normal operation and during maintenance of any equipment that handles mercury-contaminated
feedstocks.
The other major concern with mercury contamination is in the pollution of finished materials. Should mercury find its way into a finished stock, if that finished stock has to be sold as a contaminated one, the value of the material could drop drastically. And depending on the service for which the finished stock is being sold, it may not take much mercury at all to be deemed contaminated.
KOONTZ (HollyFrontier Corporation)
HollyFrontier processes crude primarily from Texas, Canada, and the Mid-Continent. HF also processes some natural gasoline from the Mid-Continent. I was unable to find any data regarding mercury in the crudes or natural gasoline that we process. We routinely do metals analyses on catalyst and other process samples, but mercury is not in the normal list, and we do not ask for a special analysis looking for it. We also send catalyst and other wastes out for metal
reclamation and/or disposal and we have never experienced environmental concerns due to mercury contamination.
ILYA ARANOVICH (GTC Technology)
Mercury is a poison for all of the isomerization catalysts as it has properties to be able to replace the metals that form the framework of the catalyst and also substitute the protons in the acid sites. Both of these phenomena lead to a decrease in the amount of active catalytic sites (acid and metal) and lead to faster catalyst deactivation. For the SI-2TM catalyst the recommended level of mercury is 20 wppb for normal operation to meet the guaranteed values on performance. A light naphtha pre-hydrotreatment block significantly decreases the amount of metal impurities that hit the downstream isomerization reactor. We have not seen problems in any of our 10 operating units with maintaining this level of mercury with a pre-HDT (pre-hydrotreatment) block. We highly recommend using this approach and properly preparing the isomerization feed.
ANDREA FOSTER and JAMIE CHISAMORE (Johnson Matthey Catalysts)
Mercury is found in an ever-increasing number of hydrocarbons worldwide. The level of mercury can vary significantly depending on location. Data published by the Environmental Protection Agency (EPA) show reported levels of mercury in various crudes. Some of these are listed in Table 1. Published levels of mercury found in refinery product streams are shown in Table 2.
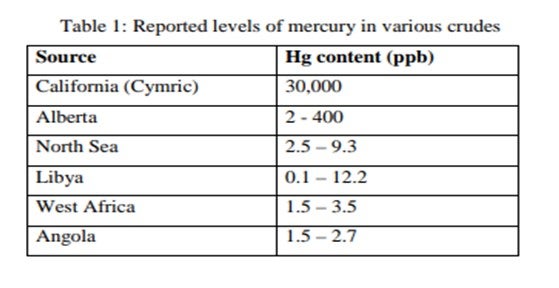
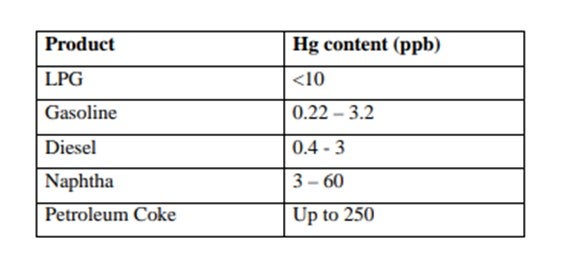
Although the levels of mercury recorded are low, the tonnages of liquid hydrocarbons handled are enormous, so downstream processing equipment is exposed to a substantial amount of mercury. The main worries are corrosion, poisoning of catalysts and health and safety. These can involve serious financial losses.
Precious metal catalysts such as platinum and palladium are particularly prone to poisoning by mercury. They react to form a 1:1 amalgam, i.e., platinum-mercury (PtHg) or palladium-mercury (PdHg) that is stable at low temperatures. With low metal loadings very low levels of mercury can have a significant impact on performance. The mercury can be driven off by heating above 300°F to 400°F, but this accelerates sintering and hence loss of active surface
area.
Johnson Matthey has many Refinery and Petrochemical customers that have installed mercury guard beds upstream of units using precious metal catalysts. The use of PURASPECJMTM* fixed-bed mercury removal absorbents has resulted in significant increases in catalyst life and also provides environmental protection, removing mercury from the lighter product streams.
*PURASPEC is a trademark of the Johnson Matthey Group of Companies.
AREIN LAZONDER – Albemarle Corporation
Mercury is a very effective poison for platinum promoted, chlorinated alumina catalyst. As can be seen in the graph below, the isomerization activity decreases very fast with mercury being deposited on the catalyst.
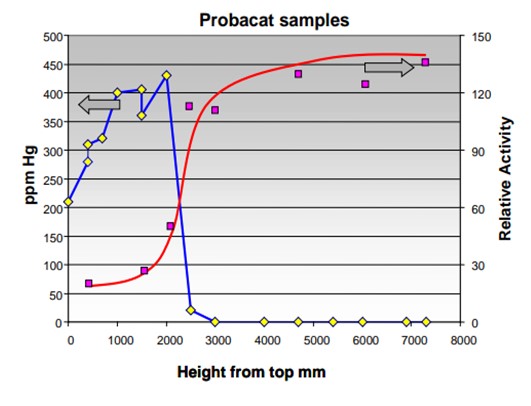