Question 37: What is the panel's experience in operating chlorided isomerization units, which were not designed specifically for benzene saturation, in a benzene saturation mode? How are operational parameters adjusted for the different operation?
MUEHLBAUER (Valero Energy Corporation – Benicia Refinery)
This is a good question; because as we blend more ethanol into the gasoline pool, a lot of refineries become octane-long and RVP (Reid Vapor Pressure)-long as well. So, the incentives to isomerize are diminishing as you blend more ethanol. Within Valero, we looked at one of our isomerization units and did a project to convert it into a benzene saturation unit but without capital improvements. We accomplished this by operating a unit designed for isomerization in benzene saturation mode. The key component is the cooling of the first reactor effluent. The benzene concentrations are normally maximum 4% to 5% in the isomerization feed. For each percent of benzene in the feed, you get about a 20°F exotherm on the reactor. So, the more you can cool the first reactor effluent, the more favorable the iso-to-normal equilibrium will be in the second reactor.
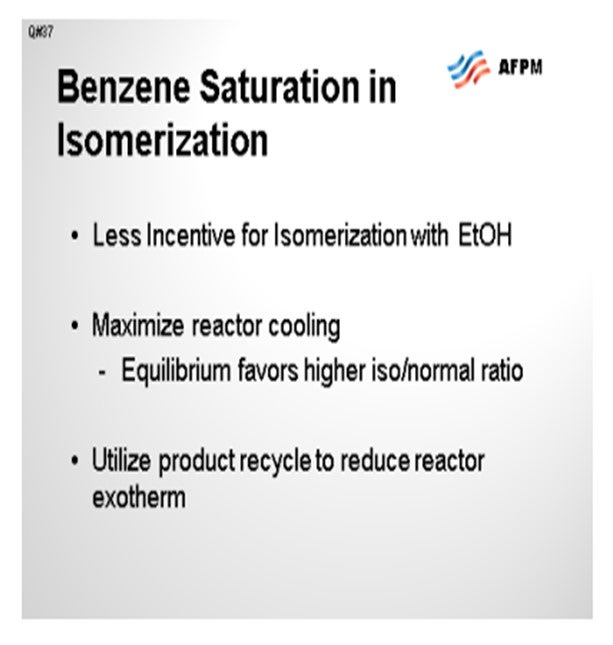
In terms of ways to cool the effluent, increasing unit recycle is one method, assuming there are not any hydraulic or space velocity limitations. Essentially, the benzene in the reactor feed, compared to the unit feed, is much more dilute. The other method would be trying to improve cooling by installing an inner reactor quench. I have heard that some facilities will bypass some of the feed around the first reactor into the second reactor to get exotherm and perhaps a little more cooling that way.
DUBIN (Axens North America)
We have seen that the quantity of benzene in the isomerization feeds has gone up due to the current regulations on benzene in the gasoline pool. For those units that do not have a dedicated benzene saturation reactor, the impact is a little more significant. The rule of thumb that Joe mentioned, 20ºF exotherm for every vol% (volume percent) of benzene, is applicable.
When processing feeds with a benzene content higher than design, we recommend reducing the inlet temperature to your first isomerization reactor to lower than typical. The goal is to have the temperature at the outlet of what we term the benzene saturation zone (that is, the top layer of the first reactor where all of the benzene is hydrogenated) at the ideal isomerization reaction inlet temperature.
Those refiners who are targeting maximum octane improvement, as opposed to just benzene destruction, may still need a higher overall temperature through that first reactor as you are bringing in more naphthene rings that will have to be opened before you can turn them into isoparaffins.
PATRICK BULLEN (UOP, A Honeywell Company)
We have had some licensees who do not have octane as a priority in their Penex unit but who still need to remove the benzene. In several cases, they have cut out their chloride injection in the Penex unit. They still typically see around a five upgrade across the unit, even without the chloride injection. They are able to handle the loss in activity by raising reactor temperatures to around the 400°F range for peak temperature. The system seems to be fairly stable. Of course,
you get the normal deactivation from oxygenates in the feed, for example, that eventual kill the catalyst. But for that type of operation, it seems to work well for them.
Our customers have seen some sulfur upsets in this type of unit operation. Reinstating their chloride injection seems to help recover some of the activity and still allows them to continue getting that minor octane upgrade they wanted. I agree with the other comments that, generally speaking, using the start-up line from the bottom of the stabilizer as a dilution source certainly dilutes the benzene that is in the feed as long as the hydraulics of the unit will allow it. We have some customers who have put in the separate benzene saturation reactor in front to try to minimize the impact on the Penex unit itself as a capital option.
DUBIN (Axens North America)
Axens has a number of units operating in benzene saturation mode even if the original design did not call for the same level of benzene reduction. With increasing benzene content in the isomerization feed, an increasing percentage of the isomerization catalyst in the first reactor is now utilized for benzene saturation. The refiner should lower the inlet temperature to the first reactor so that the temperature at the outlet of the ‘benzene saturation zone’ in the first reactor is
in line with the desired temperature. An increased overall temperature profile in the first isomerization reactor may still be required for ring opening of the additional naphthenes in the system brought about by the increased benzene content in the feed. The typical rule of thumb for liquid phase benzene saturation is a 20°F exotherm for every 1 vol% of benzene saturated.
AREIN LAZONDER (Albemarle Corporation)
Benzene saturation is possible in an isomerization unit loaded with platinum promoted chlorinated alumina catalyst. The bi-functional catalyst only needs the platinum function to saturate benzene. The acid sites on the catalyst have no additional function for the hydrogenation of benzene.
Operating in a benzene only saturation mode with no additional isomerization of the paraffins can be done in one of two ways: (1) by the injection of a chloriding agent to conserve the acid sites to be able to isomerize the paraffins once the benzene saturation mode is over or (2) without the injection of a chloriding agent if the unit will continue operating in a hydrogenation mode. With the latter operation the acid sites will be lost in the course of time and the isomerization activity cannot be fully recovered. Chloride inhibits the hydrogenation activity of platinum partly. For optimum hydrogenation activity, ceasing chloride injection can be considered. In both cases the operating conditions are moderate, at a RIT (reactor inlet temperature) = 120°C/250°F benzene is already hydrogenated. An excess of hydrogen is mandatory to prevent the catalyst from coking. At the reactor outlet the H2/HC (hydrocarbon)ratio should still be 0.1 molar ratio. Benzene saturation is exothermic so, if large amounts of benzene are processed, the heat release can be significant. To prevent temperature excursions, it is recommended to keep the maximum benzene concentration to be processed at less than 7 wt%.