Question 37: What are some of your strategies for managing as oil streams during outages of conversion units for refiners with vacuum gas oil hydrocracking and FCC units?
MORELAND (Valero Energy Corporation)
Obviously, the answer to this question is very site-specific depending on different options available based on refinery location and configuration. There are a couple of general options, and I will give one example. If you have an outage of a VGO processing unit in your refinery, one option would be internal processing. So you store and reprocess the stream or route it to another VGO consumer in the refinery with their multiple options there. You can sell intermediate streams. Many refiners, such as Valero, purchase intermediate streams to process if spare capacity is available. Another option is to reduce production of VGO. This could be a very expensive option, but you could try to reduce or shut down VGO production. And then, another potentially expensive option is to blend fuel oil.
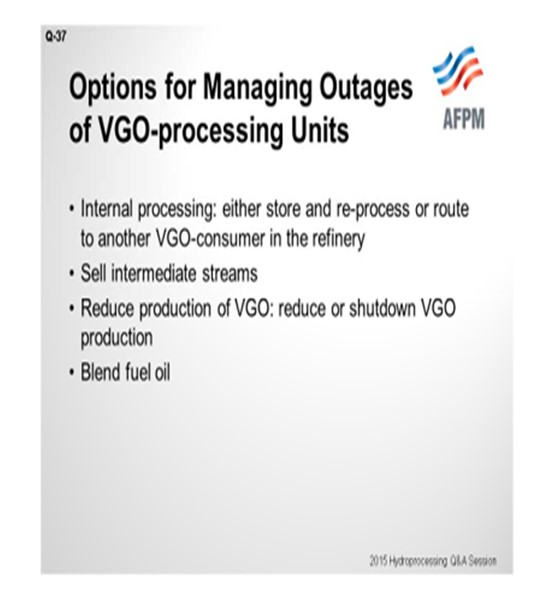
I am going to give one example of what we do to manage gas oil streams at one of our large Gulf Coast refineries. This refinery has three VGO consuming units: a GOHT FCC (gas oil hydrotreater fluid catalytic cracking) alkylation complex and two gas oil hydrocrackers. We have to use multiple strategies to manage catalyst changeouts, turnarounds, and unplanned outages.
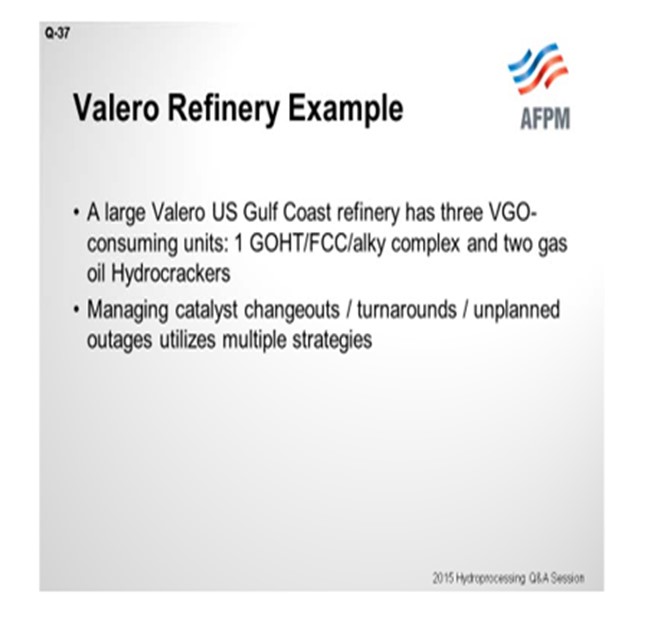
I will walk through the slide explaining the configuration. The first complex in the diagram, the GOHT/FCC complex, processes atmospheric gas oil and light vacuum gas oil. Hydrocracker Unit #1 processes a blend of HVGO (heavy vacuum gas oil) and heavy coker gas oil. It is a partial-conversion hydrocracker targeting 70% conversion, making primarily jet and diesel, and the unconverted oil is fed to the FCC. And then finally, HCU (hydrocracker unit) #2 processes HVGO plus purchased HVGO, making primarily diesel at high conversion.
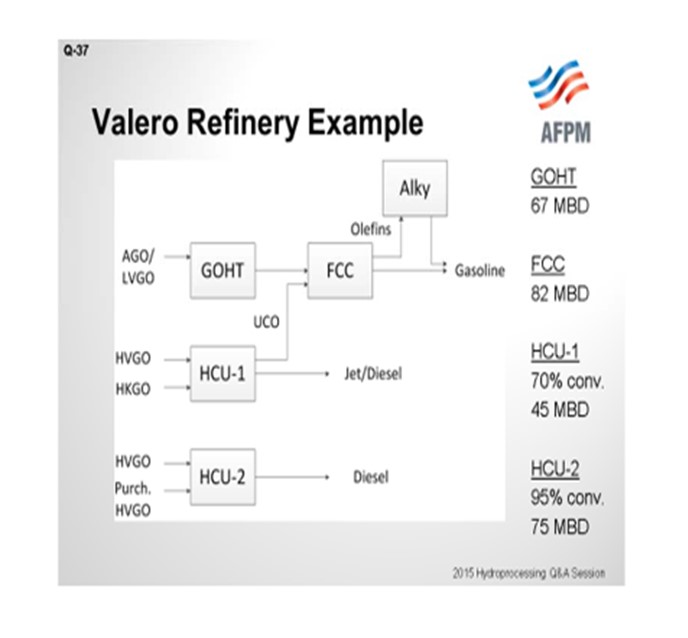
So let’s go through outage scenarios starting at the bottom when HCU#2 is down, for example, for a catalyst turnaround. Our first option, as you would probably imagine, is to stop purchasing HVGO and process as much of the HVGO as we can into HCU#1. Then we typically would sell HVGO either to another Valero refinery or other refinery on the Gulf Coast. Occasionally, we would process the HVGO in the GOHT FCC, but we prefer to keep the really heavy streams out of that gas oil hydrotreaterbecause it runs at fairly low severity.
Going on to the next scenario, when HCU#1 is down. We have plenty of room to utilize the HVGO to displace purchases for HCU#2. We would then transfer the heavy coker gas oil to another Valero refinery with that capability to process as we do not process any heavy coker in either the GOHT or the HCU#2 due to the catalyst cycle life debit.
Finally, when the GOHT is down, we will try to purchase low-sulfur VGO for the FCC, if economic; though in many cases, we end up buying sour gas oils and running slightly lowered hydrocracker conversion. In those cases, we are sometimes also able to store the AGO (atmospheric gas oil) and LVGO (light vacuum gas oil) and reprocess it later. If the FCC is down, we will typically shut down this whole complex, as you could imagine.
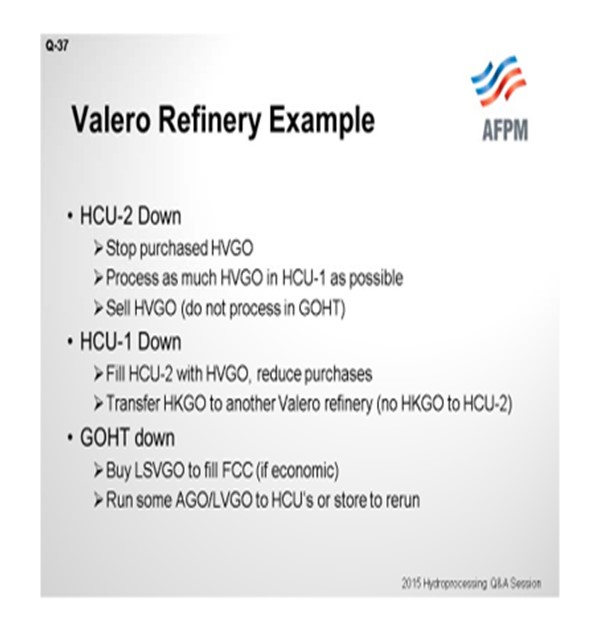
Finally, the last slide covers concerns and considerations when managing outages of units. The units will have varying tolerances for contaminants – such as silicon, phosphorous, metals, and Conradson carbon residue – and different unit capabilities. The amount of hydrotreating severity they can offer – in terms of pressure, hydrogen availability, or space velocity – also varies. So really, you have to take all of the costs into consideration. Licensor guidelines for co-processing crack stocks, its effect on catalyst life, and, in many cases, some of our newer units still have cycle length guarantees that could potentially be violated if we ran the wrong feedstock. So it is all governed by economics. We are in this business to make money. With the different yield slates, look at the margins across each of the different units and try to optimize to the best of your ability.
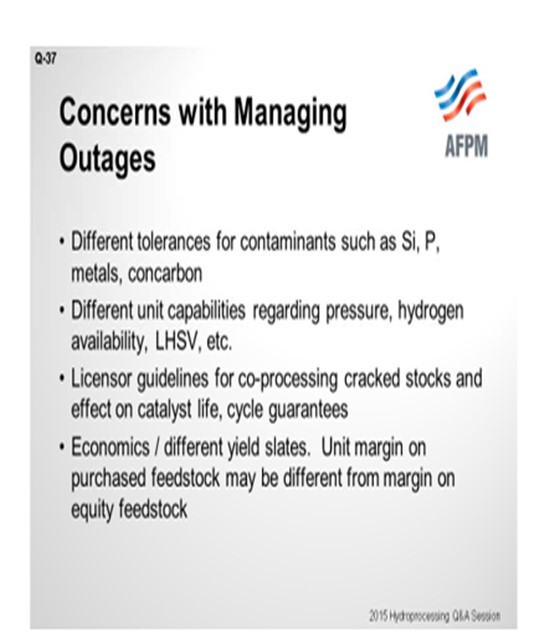
McARTHUR (Phillips 66)
I totally agree with Andy that dealing with this problem is very site-specific. My answers are fairly general, though. We will begin with pre-planning and feedstock storage well ahead of an outage, which may include getting creative with tank management options. Oftentimes, we have used alternative crudes and might have a little lighter crude slate. These are just small moves that can be made here to help incrementally reduce the amount of gas oil that we will have to process or store. Also, we will sell intermediate feedstocks, although we do not like to do that. And then lastly, we just cut back on the crude group to actually reduce gas oil production that way. That is obviously a last resort.
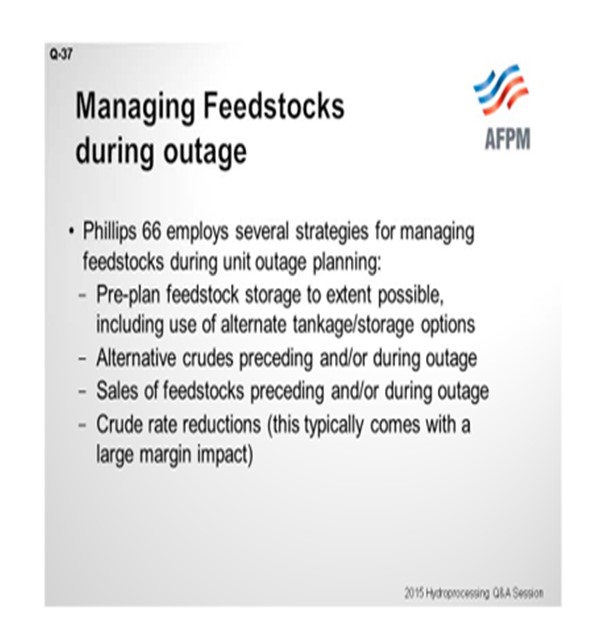
RATHINA SABAPATHI [Kuwait National Petroleum Company (KNPC)] We have a two-stage hydrocracker. Can we run both stages with the fresh feed if the catalyst is suitable? Has anyone processed fresh (treated light vacuum/heavy vacuum gas oil) in the second stage instead of unconverted oil from the first stage?
MORELAND (Valero Energy Corporation) We have not done that. We do not have any catalyst or pretreat capability in our second stage. I do not think that would be possible for our system.
SUBHASIS BHATTACHARYA (Chevron Lummus Global LLC)
In fact, in KNPC, a similar catalyst system is employed in the Shuaiba refinery. It has two separate units: the first-stage hydrocracker, Unit 68, and the second-stage hydrocracker, Unit 08. Both reactors have a pretreat capability. The first-stage reactor has a lower cycle length of two years compared to the second-stage cycle length of almost four years. So when the first stage is under turnaround for catalyst replacement, say, for a period of four to five weeks, the second-stage reactor can be run on fresh feed.
DAVID GATES (Motiva Enterprises LLC) I am going to put in my shameless plug for Wednesday morning’s “Fostering Profitability” P&P. [Laughter] I think there will be some conversation around optimization, and I think that some of the comments from Andrew are spot-on.
MORELAND (Valero Energy Corporation) I think James Kleiss is on the panel from Valero. Another shameless plug. I think he is actually going to talk about this example a little more as well.
DAVID VANNAUKER (Haldor Topsoe, Inc.)
The options reflect that standard dispositions and economics lead to the preferred route. Options include selling gas oils. For FCC Down:
1. Maximize virgin diesel endpoint.
2. If required, exit jet business and perform wide-cut blending of jet and diesel to manage cold flow properties and endpoint specifications.
3. Run light feed to the hydrocracker and maximize rates.
4. Run heavy feed to the hydrocracker and maximize volume swell and API gains.
5. For once-through hydrocracker with unconverted oil feeding the FCC, the refiner should maximize conversion in the hydrocracker For HDC (hydrocracker) Down:
6. Maximize virgin diesel endpoint.
7. If required, exit jet business and perform wide-cut blending of jet and diesel to manage cold flow properties and endpoint specifications.
8. Maximize FCC fresh feed rates. Purchased FCC feed may need to be reduced.
9. If the diesel pool cetane is marginal, the FCC may need to be run in maximum naphtha mode.
10. Crude slate may need to be more paraffinic to keep the FCC in heat balance.
JOE FLORES (Criterion Catalysts & Technologies / Zeolyst International)
When a refiner has a hydrocracker processing vacuum gas oil and an FCC unit, he can balance the production of VGO off the crude unit against the capacities of his FCC and VGO HCU. When the HCU is down, VGO can be stored to be processed later or sold on the open market, if VGO production and conversion unit capacity is balanced. In the case where VGO is purchased to keep the conversion units full, the refinery can reduce VGO purchases during times when the conversion units are down. In the end, unit economics will dictate the strategy employed at the time of the outage.