Question 37: How does the increased processing of tight oil (Eagle Ford, Bakken, etc.) affect hydroprocessing operations? With lighter feeds and less sulfur, how can the hydroprocessing reactors and catalyst systems be tailored to optimize performance? What other factors in economics replace volume gain when processing these lighter feeds (i.e., impact on FCC yields, gasoline blending, minimizing cetane giveaway, etc.)?
SHARPE (Flint Hills Resources, LP)
Tight oil crudes have impacted our hydrotreater operations in several ways. Catalyst lifecycles are extending due to the low severity required for treating low-sulfur feed. Low reactor severities have caused emulsion problems due to our not hydrogenating our surface-active compounds in the feed. We have had to set minimum reactor temperature limits on several of our hydrotreaters: every service from jet all the way through gas oil hydrotreating.
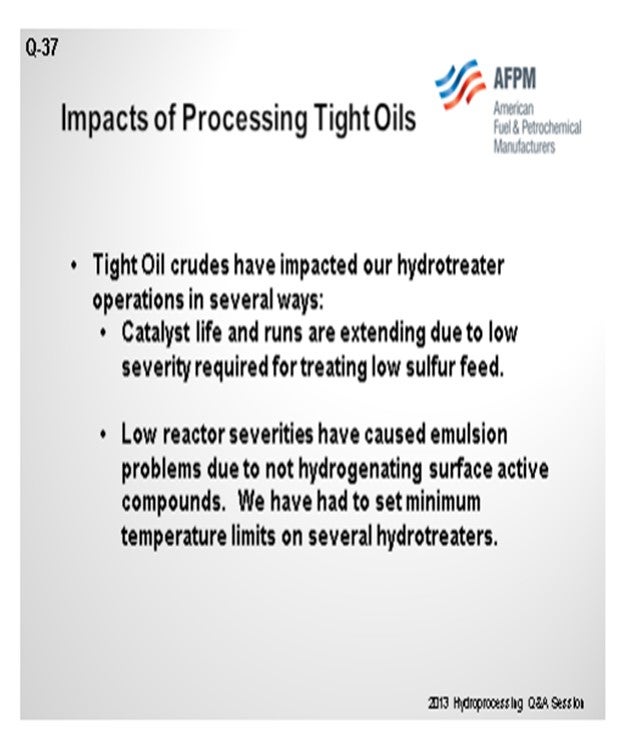
The colder hydrotreating temperatures can also result in downstream equipment running too cold. We had salt deposition in places we did not want it, as well as water condensing in unanticipated locations. So with the colder reactor temperatures, you end up having to pay more attention to cold and corrosion issues. Future hydrotreating catalyst evaluations will be considering the benefits of adding dewaxing catalysts. Several papers were presented on this at this past spring’s AFPM meetings.
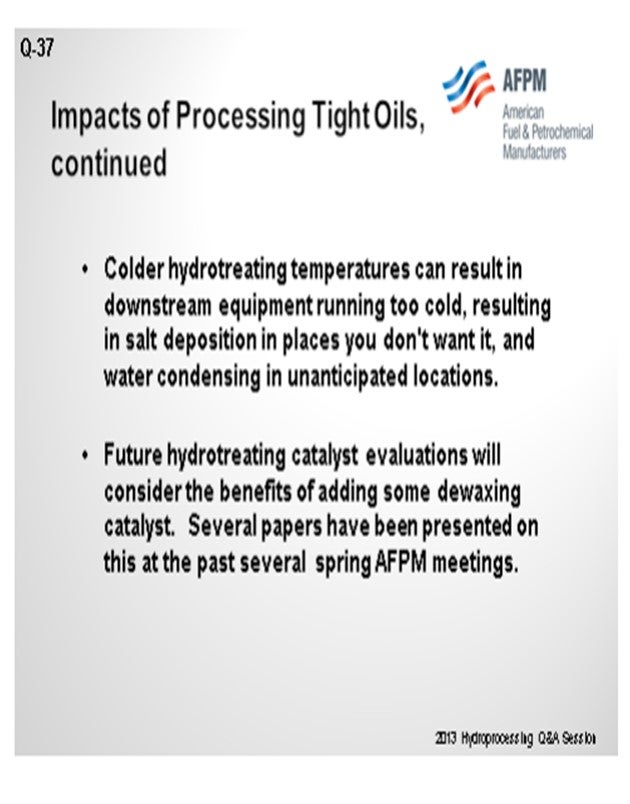
WATKINS [Advanced Refining Technologies (ART)]
We have not seen any negative impact on the actual hydrotreating process itself. Much like Danna said, running these feeds has made the process significantly easier for the refiner. ON reason is that it gives you the ability to consider processing other opportunity streams, as well as more of those easier streams, in order to gain additional barrels of feed through your hydrotreater. You can also maintain volume swell, since that is what is important, so that more aromatic feeds can be used. Consider, though, that since it is highly paraffinic, you should use some type of dewaxing catalyst in your hydrotreater if you have an issue of selling your products while there is a cold flow property problem.
If your refinery is gearing towards running these lighter sweeter crudes in the long-term, consider changing your hydrocracking catalyst to a more distillate-selective material to actually maintain the diesel yields that you are used to or those you are looking to gain. As a side note, since speed quality varies quite a bit day-to-day, even across the same wells from where you may be pulling, we still recommend using demets or other trapping guard materials at the top of your hydrotreater to make sure that there are no other adverse effects through the poisoning.
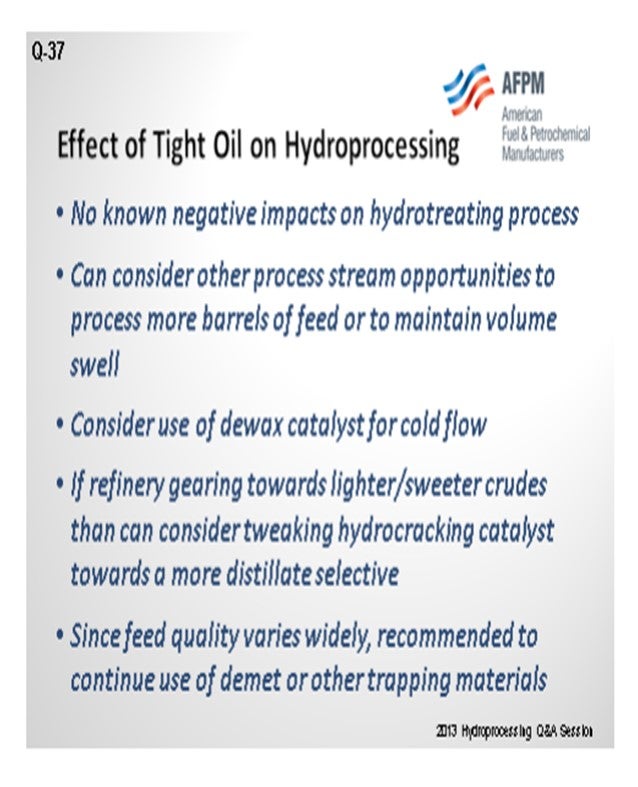
VICHAILAK (Marathon Petroleum Corporation)
We operate similarly and have not seen any adverse impacts on our hydroprocessing units. Because the feeds are lighter and sweet, we have the opportunity to raise space velocity or process heavier crude coming into the refineries. As a result, you will start having lower catalyst life and/or lower hydrogen consumption; so it is possible that you might have to burn away hydrogen. However, easier feeds also provide the opportunity to reuse catalysts with extended cycle lengths in order to reduce operating costs. Cold flow properties are definitely a concern, as was mentioned by both Brian and Danna.
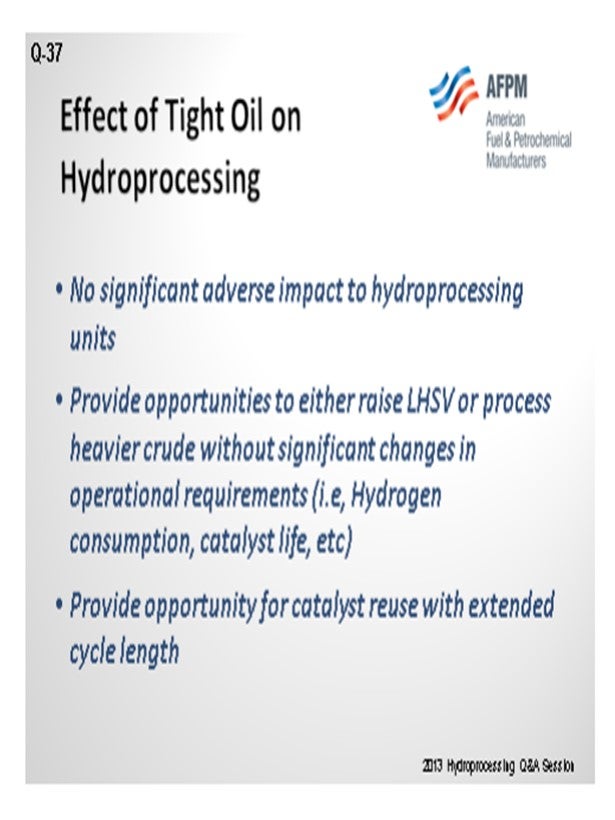
MUKESH PATEL (Reliance Industries Ltd.)
Actually, when we say tight oil does not have any impact on hydroprocessing, we are talking about how much time you have to process in the refinery. So, my questions are: How much time do you process, and how many months or years do we process until now?
SHARPE (Flint Hills Resources, LP)
We are increasing our run-lengths by 50 to 100%. That is the impact we typically see.
MUKESH PATEL (Reliance Industries Ltd.)
It is a combination of other fuel and tight oil, right? When we say 50%, we mean 50% tight oil and 50% the other fuel?
SHARPE (Flint Hills Resources, LP)
The percentage of tight oil varies at our two plant sites. But generally, it is a mix of products from tight oil and some of our foreign crudes. That is a complicated answer because of the way our feed systems are set up, so I cannot really give you the answer on that. Depending on which product stream you are observing, it could be diesel, jet, or gas oil. We have two plant sites, and the interconnections between the different units are rather complex.
STEPHEN PERRY (Motiva Enterprises LLC)
Does anyone have any experience with noble metal catalysts? If there is a little sulfur in the light tight oil, could you actually get a noble metal to work and increase hydrogen consumption and volume gain?
SHARPE (Flint Hills Resources, LP)
We do not.
VICHAILAK (Marathon Petroleum Corporation)
We cannot get to that level yet.
UNIDENTIFIED SPEAKER
Including the patent.
ROBERTSON (AFPM)
You better run out the door now. Wait. The government is closed. You cannot go to the Patent Office. If they get caught working, they will be arrested!
SHARPE (Flint Hills Resources, LP)
Keep your day job, Gordon.
ROBERTSON (AFPM)
If you live in Washington, you understand.
BRIAN WATKINS [Advanced Refining Technologies (ART)]
While tight oil trades at a discount compared to other sources, refineries with ready access to tight oil will be able to shift toward more hydrotreating, including demetallization and dewaxing, and away from a hydrocracking focus. This is still primarily limited to U.S. mid-continent due to transportation limitations. If a refinery is gearing towards structurally processing sweeter crudes, then there is also an incentive to tweak the hydrocracking catalysts toward the milder, more distillate selective part of ART’s hydrocracking catalyst portfolio. Since tight oil quality varies widely (even within the same area), it is advisable to continue to add additional demet and dewaxing capacity and continue to use advanced hydrotreating catalysts.
Looking at comparing a more naphthenic feed slate to one that is more paraffinic and understanding the impact on the various hydroprocessing units in the refinery is important. The use of these tight-oil more paraffinic type crudes (Bakken and Eagle Ford) will lower the required severity on the average U.S. ULSD hydrotreater. Understanding how these changes will directionally affect the various processes is important in order to provide some planning, as there are both positive and negative effects with this change. The lower severity will reduce the required hydrotreating catalyst volume needed in order to achieve the same sulfur specification thereby creating some additional catalyst volume which can be utilized to address some of the product property deficiencies resulting from these types of crudes. The use of tight oil crudes may also reduce the use and expense of using cetane improver to achieve the required cetane as, by nature, paraffins have higher cetane numbers (see Table 1). More paraffinic feedstocks will decrease the hydrogen consumption of a hydroprocessing unit as well.
In general, a feedstock that is more naphthenic will have a higher hydrogen consumption per barrel due to the increased concentration of aromatic compounds. With this increased aromatic concentration, the likeliness that the sulfur or nitrogen is bound up in one of these molecules is greater, making it more difficult to process in the hydrotreater. These feedstocks would require more aromatic ring saturation in order to remove the sulfur and nitrogen, hence increasing the hydrogen consumed. The increased aromatic content of these feeds also can influence the product cetane in ULSD (Table 1).
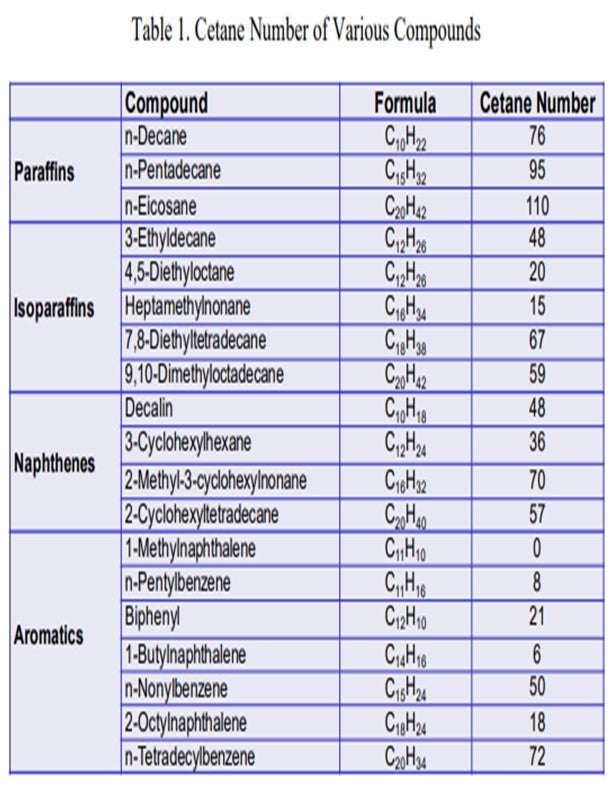
With higher aromatic concentration, however, there is a much greater potential for increased volume swell (Figure 1). Additional detail on volume swell with aromatic saturation can be found in the AFPM paper, “Understanding Catalyst Systems for Higher Yields of Diesel” AM 13-10.
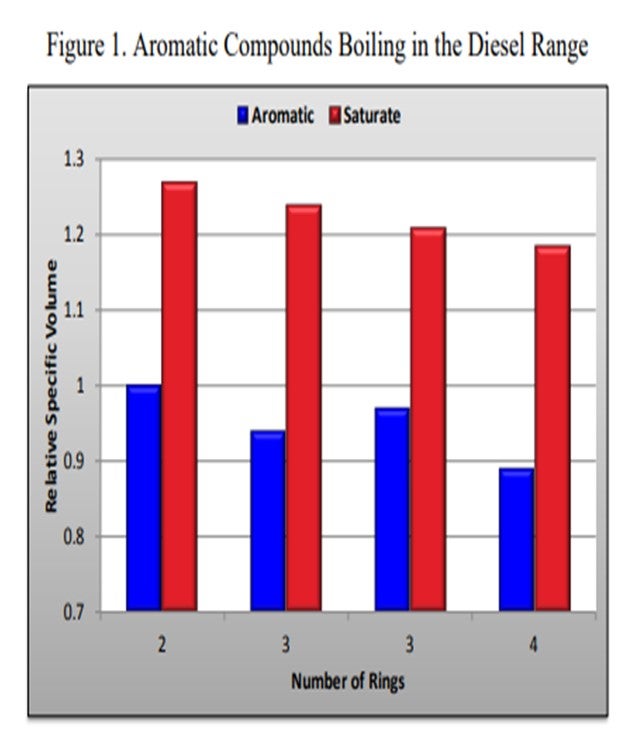
Those feedstocks that are more paraffinic in nature, Bakken and Eagle Ford, are much easier on the hydrotreating operations in the refinery. The sulfur and nitrogen molecules in these feedstocks are not as likely to be bound inside an aromatic ring and can be removed via direct abstraction, which is significantly faster than having to complete a saturation step, as well as the sulfur or nitrogen removal. This will provide either additional cycle time, as the required temperatures assuming equal feed sulfur will be lower, or there will be opportunity to process additional barrels per day in order to make up the loss in product yields.
These feedstocks also indicate an increase in light gas make as well. With higher paraffin content comes less aromatic saturation opportunity, which will produce less volume swell per barrel than what is seen with a naphthenic feedstock. This also reduces the burden on the hydrogen system due to lower consumption. The high paraffin content of these feedstocks can also influence the cold flow properties requiring additional processing such as catalytic dewaxing or the blending of other valuable streams in order to meet these requirements. Another positive with the processing of a more paraffinic feed is that for ULSD service, an increase in paraffins will provide a much better cetane value than aromatic species of similar carbon content, as shown in Table 1.
MONTRI VICHAILAK (Marathon Petroleum Corporation)
We have not seen any adverse impact of increased processing of tight oil in our hydroprocessing operations. As mentioned earlier, tight oil crude is light sweet and easy to process. This gives refiners opportunities to either raise LHSV or process heavier crude without significant changes in operational requirements (i.e., hydrogen consumption, catalyst life, etc.). Minimally, processing tight oil gives an opportunity for catalyst reuse with extended cycle length.
HENRIK RASMUSSEN (Haldor Topsøe, Inc.)
Catalyst cycle lengths have gotten longer due to the lighter feeds and lower sulfur in the tight oils. Catalyst systems need to be tailored to match the cycle length with potential pressure drop issues due to longer cycle lengths. Also, refiners now have the option of processing more barrels or blending with even worse fossil crude and still maintaining the same hydrogen consumption and SRU capacity while meeting the minimum cycle length.
Challenges are that there will be more light products produced from a hydrotreater and the fractionation overhead section may not be able to handle higher rates. This would then limit the unit throughput which could mean a reduction in the feed rate.
The tight oils are also more paraffinic in nature and as such will reduce the possible volume swell compared to most fossil crudes. The paraffins will also contribute to worse cold flow properties of the diesel fraction but it will result in a higher cetane.