Question 36: What has been your experience regarding selectivity and activity when using regenerated hydrocracking catalysts versus fresh catalysts? How do results vary with catalyst type, unit objectives, and conversion targets?
PEDERSEN (UOP LLC, A Honeywell Company)
There are well-established track records for regeneration and the reuse of spent hydrocracking catalysts, depending on service history, catalyst type, and conditions in which the catalyst was recovered. These catalysts can be returned to fresh or near-fresh performance, in most cases, and often come back basically equivalent to fresh. However, to ensure successful hydrocracking catalyst reuse, it is important that the catalyst did not experience extreme temperatures during the operating cycle and that there was no significant amount of metals contamination on the catalyst during the prior cycle. It is also important that during the regeneration of the catalyst, the temperature is carefully controlled and the regeneration is conducted according to the recommended procedures in order to recover catalyst activity.
This chart shows results from a pilot plant comparison of commercially regenerated catalyst that was run through one cycle versus fresh catalyst which was a sample of the material that had been loaded for that cycle. The data show that at the same operating temperature, the same conversion was achieved, implying full recovery of activity. What is shown in this chart is gross conversion on the Y-axis and temperature on the X-axis. Blue represents the fresh catalyst data points; the red data points indicate the regenerated catalyst.
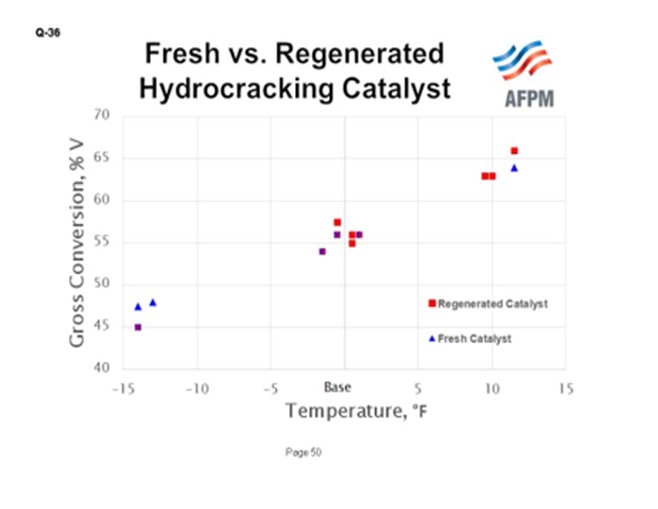
Similarly, in back-to-back commercial operation shown on this chart, we see required temperature for constant conversion versus time onstream. Blue, again, is fresh catalyst, and the data points in red indicate the performance of the regenerated catalyst. In this case, equivalent performance on cracking catalyst activity between the fresh and the regenerated catalyst is observed. The operating data also show very good catalyst stability throughout the cycle for the regenerated catalyst (red data points).
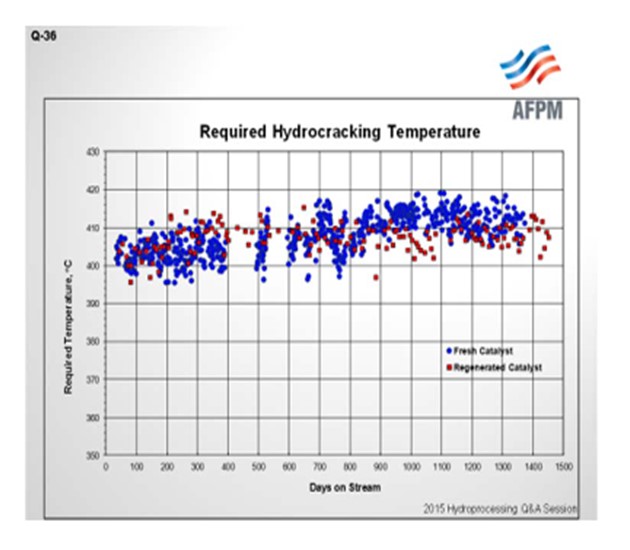
These are two examples of good outcomes. This is not a guarantee that regenerated catalyst performance is always good. I will remind you of my earlier point that it is important to pay attention to how the catalyst is handled in the prior process cycle, in order to ensure success on regeneration. Although regeneration of distillate selective catalyst is most common, catalysts across the activity spectrum have been successfully regenerated, in fact, multiple times in many cases. We tend to see a bigger shift in performance and properties with the max naphtha catalysts versus distillate catalysts, if there is a deviation from fresh catalyst performance. Typically, when we see good results like those indicated in the charts, we are talking about catalyst activity from the standpoint of the cracking function.
However, as we know, hydrocracking catalyst is bifunctional. Regeneration does not always produce equivalent recovery of the hydrogenation function. In those cases, the selectivity might suffer a little relative to the fresh catalyst; although in some cases, the selectivity comes out just as good as fresh.
Generally, if regenerated catalyst is used in low conversion operations, there is a lot less sensitivity to differences in performance. So, there is a lot more flexibility in those cases for selecting regenerated catalyst. In some instances, it may be necessary to install some fresh catalyst to make up for a potential loss of activity or shortage in quantity of the regenerated catalyst. Our recommendation is to load the fresh catalyst (the higher activity cracking catalyst) nearer the reactor inlet, primarily from a temperature control and safety standpoint.
McARTHUR (Phillips 66)
Phillips frequently makes some use of select regenerated cracking catalysts in our bed design. This is catalyst for which we know the operation history, so it is typically catalyst from our own units. Our experience is that a hydrocracking catalyst regenerates fairly well and with only a small loss of initial activity. The yield selectivity tends to be similar to fresh catalyst when run at similar operating temperatures. The yield decline over the run is similar to, or maybe even a little better than, that of fresh catalyst. But in our experience, it is best to bring in the catalyst vendor. It will be worth your decision when you are deciding whether or not or how much of it to load.
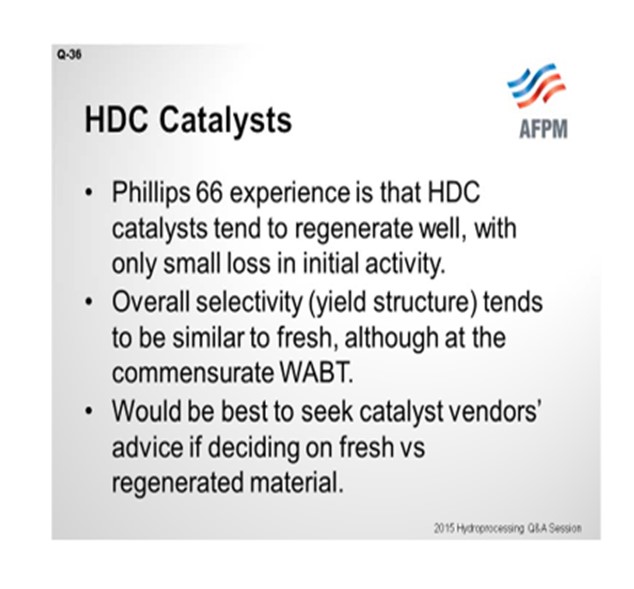
WRIGHT (Hunt Refining Company)
We are on Cycle 2 of our hydrocracker. We have not used regenerated catalyst yet. We plan to use it in Cycle 3 relative to the fresh catalyst though. The pilot plant data shows that the selectivity is higher, but the activity is slightly lower.
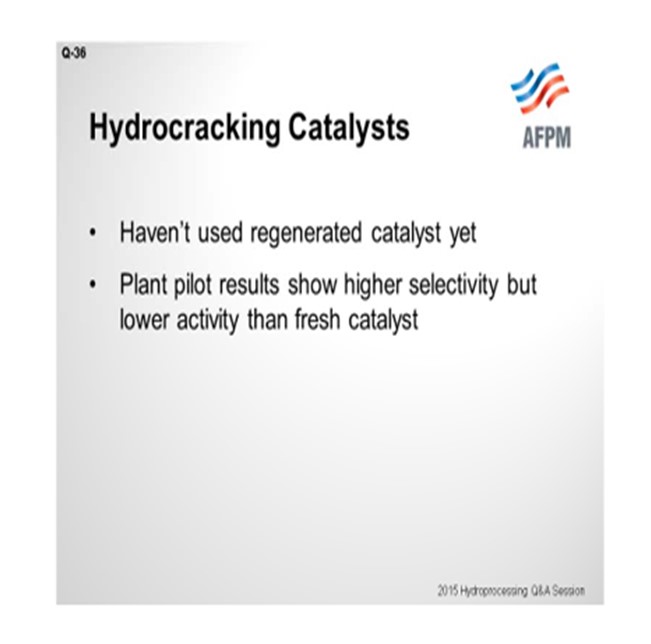
JAMES (TIM) CAMPBELL (Eurecat U.S. Incorporated)
Is there any difference in your comments for nickel tungsten versus nickel moly hydrocracking catalyst? Have you seen any difference of regen versus fresh?
McARTHUR (Phillips 66) I am going back in memory here, which is a little scary; [Laughter] but no, we do not see a lot of difference between the two.
SHRIKANT MADHAV VAIDYA (Indian Oil Corporation Limited)
On the presentation slide that Mr. Pedersen of UOP showed about the regenerated catalyst and fresh catalyst, there was a comparison between fresh and regenerated catalyst activity and selectivity, which showed the regenerated catalyst data for the fresh catalyst as being quite encouraging. But still, invariably the users always go for the new catalyst. That is the general feeling. So why is it not so popular to use the regenerated catalyst if the results are going to be so good? Why is there no confidence among the users? Why, therefore, are they not preferring the use of regenerated catalyst?
PEDERSEN (UOP LLC, A Honeywell Company) That is a good question. Why is there not more use of regenerated catalyst? I think that is somewhat of a company-specific and regional-specific question. Some refiners are a lot more risk-averse than others. As I indicated in my comments, you do, of course, have the potential to recover activity very well through regeneration, but it is not always guaranteed. The second factor is that in a fair number of cases, a refiner will contaminate his catalyst during the cycle, either through temperature excursions or through lack of adequate demetallization pretreat; and in that way, he will diminish the suitability for the catalyst to be regenerated. There are some lower activity amorphous catalyst systems where there is no pretreat, so the contamination with metals is a higher risk in those cases.
MORELAND (Valero Energy Corporation) In Valero, we have not used regenerated hydrocracking catalyst. And in our opinion, when we look at a catalyst selection for a hydrocracker, we are almost always trying to consider the latest, greatest generation just from the yield perspective. So even if there is no activity or selectivity difference between a regenerated catalyst and a fresh catalyst, there is potentially a new grade out from a catalyst supplier – like UOP, Criterion, or Chevron – that has higher yield and better activity than even the fresh catalyst from the previous generation.
PEDERSEN (UOP LLC, A Honeywell Company) There is one more factor that we probably should mention. With the use of regenerated catalyst, it is typically required to keep a spare batch of catalyst. The reason is that turnaround on catalyst regeneration, particularly for refiners who are in a more remote location, does not allow for dumping regeneration and reloading all in one turnaround.
TARIQ MALIK (CITGO Petroleum Corporation) As owner-operators, we are interested in the run-length. When you are primarily focused on run-length, including conversion and yields from your hydrocrackers, you are scared of regenerated catalyst. You do not know what you or the previous owner have done to that catalyst, so you always go for fresh catalyst.
MORELAND (Valero Energy Corporation) Well, I think what you are saying is that the risk is on me, or on us as the SMEs (subject matter experts) if we recommend a regenerated catalyst. It can only go poorly for us. [Laughter]
TARIQ MALIK (CITGO Petroleum Corporation) That could be a career-limiting move.
MORELAND (Valero Energy Corporation) That is correct. [Laughter]
DAVID VANNAUKER (Haldor Topsoe, Inc.)
The catalyst regeneration process exposes the catalyst to high temperatures and steam. The hydrocracking catalyst can lose metals functionality, zeolite functionality, or both. A loss in metals functionality leads to less aromatic saturation and more nonselective cracking. Light gas yields increase. A loss in zeolite functionality can lead to high temperatures for normal operations and an increased sensitivity to nitrogen slip and more difficult feeds. If the unit requires high conversion, the previous conversion level may not be able to be reached. The regeneration quality determines the results. Some units have been able to successfully use regenerated catalyst with minimal impact, while others have seen increases in light gas production and catalyst deactivation rates.
JOE FLORES (Criterion Catalysts & Technologies / Zeolyst International) Typically, regenerated hydrocracking catalysts exhibit reduced activity and selectivity when compared to fresh catalyst. The amount of reduction is usually dependent on the service the catalyst was in its previous life, i.e., how long it was in service, the final severity before the catalyst was taken offline, and whether it was subjected to any temperature excursions. Regenerated catalysts can have a place in a replacement catalyst load as a cost-effective alternative to fresh. Oftentimes, a higher activity catalyst that is regenerated can be used in place of lower activity fresh catalyst. Each individual situation is unique, and the unit objectives of cycle length, desired conversion, and yield selectivity need to be considered when employing regenerated catalyst. Regenerated catalyst can be evaluated in a pilot plant to baseline the remaining activity and yield selectivity before it is recommended in a replacement load.