Question 36: What are your primary indicators that a coker furnace spall is complete? What steps do you take to optimize the efficiency of spalling?
GAMBOA-ARIZPE (CITGO Refining & Chemicals, L.P.)
A cautionary foreword: Online spalling of furnace heater tubes is not suitable for every heater design. It is necessary to consult with your furnace licensor or manufacturer to determine if online spalling practices are compatible with the heater designs installed in your respective facilities. There will be a more complete answer in the final transcript, including a more detailed discussion on the practice of delayed coker furnace spalling and the factors used to determine when the decoking operation of the furnace is needed. The verbal answer will only address the descriptive metrics currently being employed to determine when a furnace spall is considered ‘complete’. Technically, however, the primary question here is a difficult one to answer, because the completeness of a spall can only be determined post-spall with the furnace back online and after tube wall temperatures are measured; and to a lesser degree, after the heater pass pressure drop on normal oil flow has also been measured. Fortunately, the completeness of a spall can also be based on previous experience with a particular furnace and can be managed procedurally. That is the basis on which I will attempt to answer this question.
CITGO Petroleum Corporation operates four delayed coker units amongst its three U.S.-based refineries. Three out of the four units incorporate routine spalls for their respective coker furnaces as part of a broader operating strategy to optimize effectiveness of their overall furnace operation. The fourth delayed coker unit relies primarily on ‘piggings’. The benefits of online spalls versus steam/air decokes versus piggings will vary depending on the logistics of a facility, as well as on the heater’s mechanical configuration and its design. The decoking effectiveness of the three methods is also different. All methods, however, fundamentally aim to remove as much of the fouling coke layer that builds up along the interior surface of the furnace tubes as is possible during the operation.
The buildup of coke within coker furnace tubes is intrinsic to the delayed coking process due to the nature of vacuum residue material once it becomes exposed to the relatively high temperatures that are required by the process (greater than 850°F). While the buildup of coke cannot be totally averted, the rate of this buildup can be managed, depending on the heater design and other factors. The thickness of the accumulated coke layer can be generally inferred by monitoring and trending the furnace tube wall temperatures. Higher tube wall temperatures are indicative of thicker coke buildup because the deposited coke layer has lower thermal conductivity than the metal substrate of the furnace tubes. In effect, the coke layer acts as an insulating barrier that restricts the transfer of heat from the fire box into the process stream, which then allows the metal temperature of the tubes to increase.
Over time, the tube wall temperatures increase as the coke layer thickens. The sections of the heater that begin to experience faster coke buildup also shift with time as more and more tubes begin to experience lower heat transfer. This dynamic is caused by the need to keep the target coil outlet temperature (COT) relatively constant to maintain viable C5+ liquid yields and because the total heat flux across the heater [for a fixed surface area and a known dT (delta T; ∆T; temperature differential)] is also relatively constant. In other words, the gradual reduction in heat transfer efficiency across some of the process tubes forces the furnace to be fired at increasingly higher rates. This firing shift increases the localized heat fluxes in other sections of the heater to meet the specific COT that is dictated by the operation.
Removal of the coke layer at some routine maintenance interval improves the furnace’s overall heat transfer efficiency because it eliminates the insulative barrier that prevents the heater from meeting those COT targets at lower firing rates. Because of this dynamic, the tube wall temperatures tend to increase logarithmically over the course of a run until the coke layer is again removed. The run-length of this recurring operation must be optimized to maximize the refinery’s profits while ensuring that the long-term reliability of the equipment is not compromised.
Ultimately, the delayed coker furnace is decoked on an as-needed basis to prevent operation that could produce tube wall temperatures above the limiting design metal temperature of the respective alloy of the furnace tubes [as defined by API 530 (Table 5) or an equivalent table (ANSI, ASME, etc.); see my second slide entitled “Table of Limiting Design Metal Temperatures for Various Heater-Tube Alloys”]. The timing of a decoking operation is, therefore, dictated by the need to manage the reliability of the equipment, particularly to avoid encroaching the mechanical limits of the furnace tubes themselves; especially, long-term operation at the elevated temperatures. Equally important, an alloy’s critical temperature should generally never be exceeded as this could result in changes to the alloy’s microstructure. Note: Per API 530, “Other considerations can require lower operating temperature limits, such as oxidation, graphitization, carburization, and hydrogen attack.”
The API 530 limiting design metal temperature is not necessarily the strict driver for the end-of-run (EOR) tube metal temperature, although one could say it is good practice not to exceed it. The real driver for the EOR temperature is an economic optimization question: If a refiner chooses too high of an EOR temperature, then he or she will have to retube the heater excessively/ often; and if the refiner chooses too low of an EOR temperature, then he will have to decoke excessively/frequently. The short-term mechanical integrity limit for a typical coker furnace tube is appreciably higher than the typical EOR temperature. The tube geometry is a factor as well. For a thick-walled tube, the stresses are lower so higher temperatures can be tolerated. At CITGO, the online spalling operation was introduced as a viable decoking practice as early as 2001, with conceptual preparation going as far back as 1999. The written procedures themselves have been optimized at each respective facility via post-spall performance-based evaluations. Trial-and-error adjustments, both to the duration of the overall spalling and to the variable knobs of key procedural steps, have also been modified and incorporated over the years to produce the current procedures being employed today. There is some procedural rigidity for certain steps, but experience has also resulted in producing procedures which allow for some flexibility in other steps. The success of the online spalling operation depends on the combination of various factors. But in a broader sense, four gates must be cleared for the spalls to adequately remove sufficient coke buildup and restore heater performance.
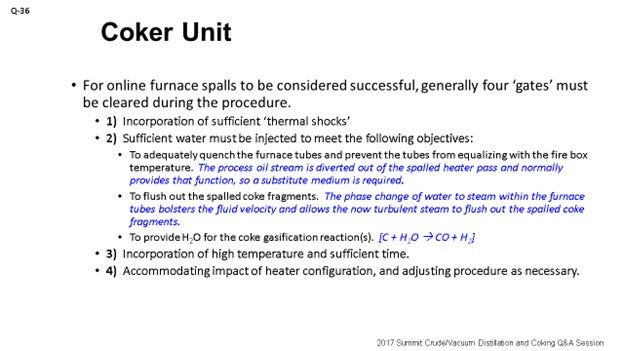
In a general sense, the term ‘spall’ describes the physical action in which chips or fragments are splintered and broken off of a larger solid body. There are several mechanisms that can produce a spall. In the context of the delayed coking process, however, the aim of furnace spalls is to break the coke layer off of the interior walls of the furnace tubes. This dynamic is produced by heating and contracting the furnace tubes in an alternating fashion over a relatively short time span to thermally shock and alter the fixed volume in the tubes themselves. Since the coefficients of thermal expansion of the metal substrate and the fouling coke layer are significantly dissimilar, the two layers grow and contract at different rates, which causes the physical detachment of the coke layer from the metal surface. The objective of thermal shock is to physically break the coke layer by using the force that is produced by thermal stresses to fracture the foulant layer. The first gate that must be satisfied in the spall, therefore, is to ensure that sufficient thermal shocks are incorporated during the procedure. Some are incorporated on the frontend of the spalling procedure, while others are incorporated on the backend of the spall.
During the spalls, boiler feedwater is lined up to the spalled heater pass, usually upstream of the convection section. Water addition serves three purposes, and I have them listed under the second bullet point in the slide. The three purposes are to:
-
Adequately quench the furnace tubes and prevent the tubes from equalizing with the fire box temperature. The process oil stream is diverted out of the spalled heater pass and normally provides that function, so a substitute medium is required.
-
Flush out the spalled coke fragments. The phase change of water to steam within the furnace tubes bolsters the fluid velocity and allows the now turbulent steam to flush out the spalled coke fragments.
-
Provide H2O for the coke gasification reactions.
The second gate that must be cleared is that sufficient water must be injected into the spalled heater pass to provide these three necessary functions. Water addition should be ratably controlled to target specific zones along the spalled heater pass and can be done by monitoring the progression of two wall temperatures in those specific sections over the course of the spall. Note: Boiler feed water or condensate is typically used as the source water because it needs to be free of inorganics/minerals (calcium, magnesium, sodium, etc.).
A combination of high temperature and time is needed to clear the third gate. The optimum value for both of these parameters must be determined through local experience while remaining within the temperature limits of the affected tube alloys. Procedurally, the time factor – or ‘length of hold’ step – should not be too rigid, given the fact that effective spalls can be performed to varying hold step lengths and dependent upon the morphology of the foulant coke, which can change and also be dependent on the feed slate. The combination of high temperatures and high steam velocities is required to micro-spall the coke layer via erosion and gasification reactions (where the steam can directly react with the coke to produce H2 and CO). The time factor simply provides a window for these two mechanisms to occur. The bulk of the coke removal during a spall operation may actually occur from micro-erosion and coke gasification, given the gradual change in tube skin temperatures that is typically observed during spalls.
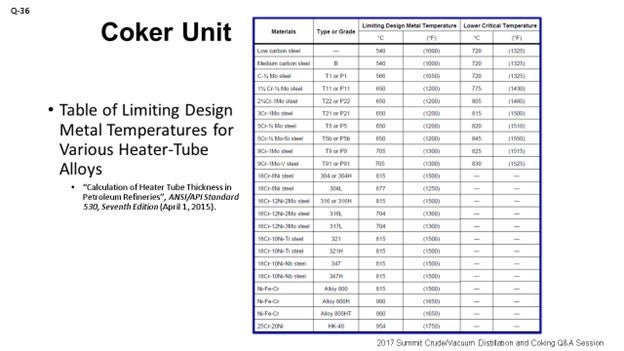
The fourth and final gate is more or less dependent on the heater design. Typically, a heater pass is spalled individually while other the heater passes remain on oil. This approach creates the possibility that the spalled heater pass may be affected by a neighboring sister pass. The fourth gate simply acknowledges the impact that a sister pass can have on the spalled heater pass and accounts for its heat input. Simply stated, a sister pass may need to have its respective coil outlet temperature target lowered prior to the introduction of oil into the spalled heater pass so that the combined firebox heat fluxes do not adversely affect the spalled heater pass in an acute fashion. Experience has taught CITGO that as much as half of the spalling benefit can be squandered from the onset if the effect of the sister passes is not taken into account. Along the same vein, another consideration to preserve the benefits of a spall prior to the conclusion of the spalling operation – and once oil is reintroduced into the pass – is to ensure that the core outlet temperature targets for the spalled heater pass be ramped up slowly. This precaution is needed to prevent higher flux conditions during the period when the oil flow in the spalled pass is not yet sufficiently high to properly quench the tubes.
It should be noted that spalling operations are not as effective on the process convection tubes, because even the minimum water addition requirements may over-quench and prevent the convection tubes from getting hot enough for the spalling mechanisms to work as effectively. Fortunately, the process convection tubes generally do not coke up as severely or as rapidly as the furnace’s radiant tubes. Eventually, however, the loss of heat transfer along the process convection section can become limiting enough and impose a higher duty load on the radiant section (leading to more accelerated heater pass coking rates in that section). Because of this ‘diminishing return’ dynamic, a heater that is normally decoked with online spalls will also need to incorporate a steam/air decoke or a pigging operation – roughly after every three or four spalls – to better restore the performance of the convection section.
In summary, sometimes short spalls are successful; sometimes they are not. Sometimes spalls with less water injection are successful; sometimes they are not. Sometimes spalls at higher temperatures are successful; sometimes not. Generally, however, if furnace tube wall temperatures can be uniformly reduced by 150 to 200°F post-spall, then the spalling operation can be deemed successful. This result will typically occur if all four gates discussed above are satisfied. Of course, there are a myriad of other factors one must consider with the spalling operation, such as effects on coke morphology, the coke cutting operation, some additional reliability considerations, and effects on the heater pass outlet manifold. These other factors usually do not affect the performance of the spall itself; they just need to be considered.
LÉGARÉ (Andeavor Martinez Refinery)
I will try to fill in some of the very few gaps that Héctor had in his talk. So, why is spalling efficiency important? If you are looking at a refinery where you are coker-limited, then coker spalling is essentially slowing down your whole refinery. It is really important that your Coker Operations team and your coker unit engineers are keeping a close eye on spalling to make sure that it is as efficient as it needs to be because it is really integrated into your planning process.
We will not go into why you do spalls, as that was already covered. Spalls really should be coordinated with the Planning Department. As I said, it is built into your plan, which is really managed by Operations because they will be the ones who will go through the procedural steps. Then, the unit engineer will be tracking the actual performance or the efficiency of the spall, which will be tracked as part of the unit health monitoring reports. As Héctor said, you cannot really tell how effective your spall was until it is done; so, online effectiveness is really just a myth and something that you should tell your manager that you cannot do. The effectiveness is really measured as a function of the delta T (∆T; temperature differential). That delta T is defined as the temperature difference between the post-spall start-of-run tube skin temperatures as compared to a baseline, which would be coming out of a turnaround or a physical pig. You really want to start to look at minimizing that delta T post spall because that will be the sign of true efficiency and effectiveness of the spall.
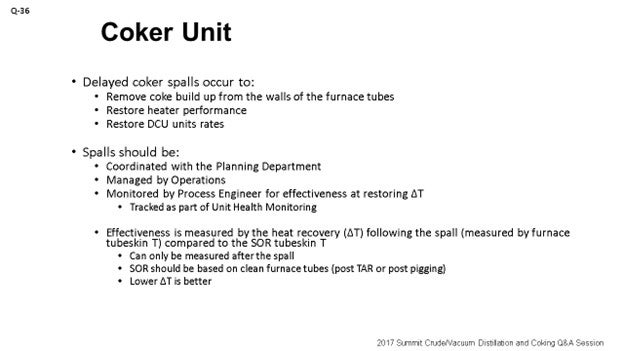
What can drive the efficiency of the spall? Héctor covered some of them factors. Obviously, one is the duration of the spall. Again, when you are in a planning situation and coker-limited, you will get a lot of pressure to minimize the spall duration. However, sometimes you will need to perform a longer spall. So, it is really important to keep that conversation fresh, and be upfront with the Planning Department.
The quantity and quality of the velocity steam you are using: Andeavor uses velocity steam, not boiler feedwater.
The next point is using a shock or continuous spall. The temperature of the spall will be temperature-dependent. So, with the shock spall, you will see temperature gradients playing a greater role as a continuous spall is more about velocity steam and constant temperatures.
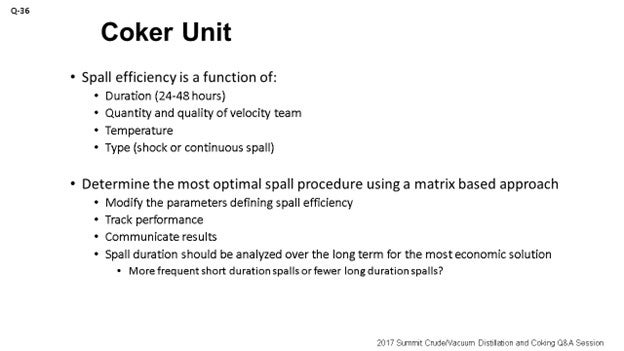
What can you do to optimize the spall approach? We came up with a chart, which you can see on the slide. The chart uses colors to measure performance. What do the colors tell us? Well, green means go; red means stop. The more green you see, the more delta T is being minimized and getting closer to zero. Red on the chart indicates that the spall did not go well. The point I want to make is that when a spall does not go well, you want to get with Planning right away and try to schedule another spall in that same pass as soon as you can. Because if you do not go after that pass right away, you may end up in a pigging situation. Like I said, green means it is directionally where we want to go. You can see there are different colors on the fonts, too. As we change the type of spall, we change the color of the font we use to represent the different spall durations utilized for the spall. So, the green and the red are the measures of the true effectiveness of the spall.
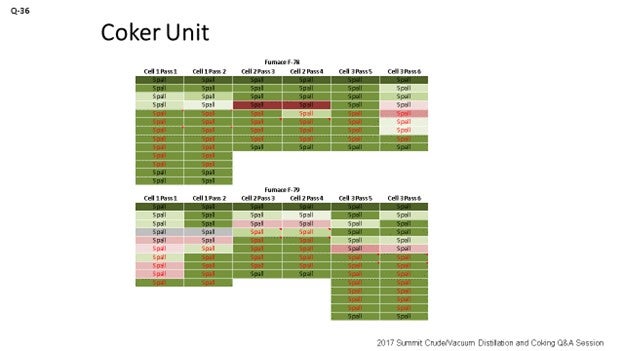
Some final thoughts: Optimized spalls are obviously going to help reduce lost profit opportunity; because when the efficient spalls are planned properly, they will be effective in getting the furnace performance back where it needs to be. Opportunity spalls are something that a refiner should really have in the forefront when looking at coker operations. ‘Opportunity spalls’ are the term we came up with when an opportunity essentially presents itself. For instance, you have some other upset in your refinery that has slowed down your coker. You have room on the coker rate, so you can go after a free spall essentially as long as you have the steam available to do that. Get your heater performance back up on track so that when you are able to push the coker again, you will not have to worry about that spall that was scheduled a week or two out.
I will tell you that the opportunity spall is something which needs to be ingrained in your culture; because as I have seen changes in the Operations team over time, they have lost sight of that opportunity. As a result, we have gone through an LPO (Lost Profit Opportunity) situation where we have had to cut back on crude runs only to come out and start the coker rates up again. And then within a week after raising coker rates, we had to slow down crude and coker rates again to spall. So, obviously, you want to try to avoid that type of coker slowdown. The last point is that the poor spalls really need to be addressed quickly. If you are not effective with a spall, you run the risk of going into a pig and having a shutdown.
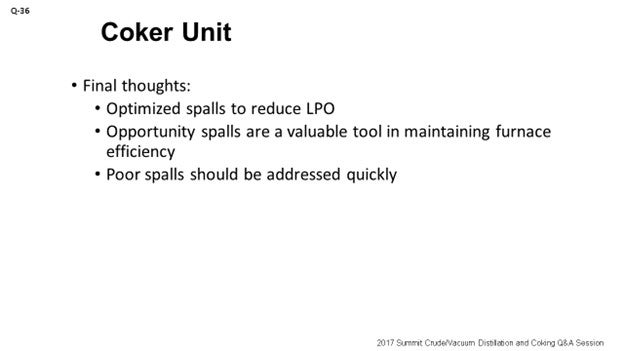
LOGEROT (Prosys Inc.)
You have heard the first two guys talk about trying to develop what might be considered an optimum procedure for the spalling. Héctor spent a lot of time on the four gates. So, I am going to introduce the concept from process control. Once you have decided on your optimum procedure, how will you be sure that you will follow that optimal procedure every time? There is a mechanism that, in the process control world, we call ‘procedure automation’. You can leverage your automation tools. They will allow you to automate your spalling procedure. So, ultimately, you get to a point where the operator just presses a button and says, “Spall this pass,” and the control system goes back doing all the spalling.
Now what I heard these guys say, too, is that some of the steps are rigid and that you want it to be on exactly this flow rate for this time and that temperature. Some of them are more flexible. You can build the flexibility into your procedure automation system by allowing the operator ranges of set points or controls for a particular part or step of the operation. So, basically, if you can write down your procedures in a stepwise fashion and provide the operating conditions that you want in each step, then it can be automated. When you automate it, you basically ensure that your “Best Operator” is on board all the time. Your “Best Operator” is really that control system which is controlling it and telling you exactly which steps you want and in what order, as well as which control settings to use each time.
ROGER METZLER (Baker Hughes, a GE Company)
When you are performing repetitive spalls, do you see a point at which you begin consistently getting diminishing returns and you just know you are only going to be able to perform so many spalls before you will have to set up a pigging or a decoke?
GAMBOA-ARIZPE (CITGO Refining & Chemicals, L.P.)
After several decoking operations, the refiner gets to the point where the spalls are no longer as effective. Usually, the convection section of the coker furnace becomes limiting because the spall is not as effective at cleaning the convection section. So, over the course of three or four spalls, you may have to come back and do either a steam/air decoke or a pigging operation to restore the performance of the convection section. Fortunately, the convection section does not foul as severely. It fouls a bit slower. But because of the general inability to get the right temperatures in the convection section tubes during spalls, the spalls are not as effective in that section.
One of the other points I want to make is that if you do have a spalled pass that did not perform as well post-spall – say you have a heater with four passes and one of them did not do so well – and if you do not do what Eric said and go at it again and reestablish a better spall, then you will end up with an imbalance on the heater. That imbalance is what will drive the heater to foul up more severely during the next run.
TARIQ MALIK (CITGO Petroleum Corporation)
I heard various times for the online spall. Darwin had it at 16 to 24 hours, and I think Eric said 24 to 36 hours?
LÉGARÉ (Andeavor Martinez Refinery)
Forty-eight.
TARIQ MALIK (CITGO Petroleum Corporation)
Forty-eight. So, what tells you that you are done? I would like to be done in 16 hours, but I can never complete a spall in 16 hours.
LÉGARÉ (Andeavor Martinez Refinery)
The range I gave will be in the Answer Book section of the transcript. We were basing it on a 48-hour spall because that was what we needed to get the performance we targeted. What happened was that we did not have the right information from our Inspection Department. As far as the temperature limits, we could see limits on the heater and the outlet piping temperatures. So, once we established a higher allowable outlet temperature on the furnace outlet piping, we were able to spall at a higher temperature and get the performance we needed in 24 hours instead of 48.
TARIQ MALIK (CITGO Petroleum Corporation)
May I ask at what temperature?
LÉGARÉ (Andeavor Martinez Refinery)
The revised temperature was 1300°F.
TARIQ MALIK (CITGO Petroleum Corporation)
For the next question, I want to poll the panel. At what tube-metal temperatures do you trigger the decoke, spall, or pigging of the heater? Do you go to 1300, 1400, or 1275°F? What is that number you reach where you say, “This is the limiting temperature; now decoke the heater tube”?
GAMBOA-ARIZPE (CITGO Refining & Chemicals, L.P.)
I think ours is between 1300°F and 1350°F.
TARIQ MALIK (CITGO Petroleum Corporation)
Is that 9-chrome tubes or stainless?
LÉGARÉ (Andeavor Martinez Refinery)
We are in the same range of 1300°F.
TARIQ MALIK (CITGO Petroleum Corporation)
Thirteen hundred? I do have one more question for Jeremy on that heater that does 12°F fouling a day.
THEISS (Marathon Petroleum Corporation)
I said 6 to 12°F.
TARIQ MALIK (CITGO Petroleum Corporation)
Okay: 6 to 12°F. I just took the upper number. You said that there are three cells. How many passes per cell?
THEISS (Marathon Petroleum Corporation)
Two.
TARIQ MALIK (CITGO Petroleum Corporation)
Okay. Thank you.
ERIC LÉGARÉ (Andeavor Martinez Refinery)
Delayed coker furnace spalls are performed to remove the buildup of coke on the inner walls of the furnace tubes in order to improve furnace heat transfer and maintain unit throughput and efficiency. As furnace spalls require coker and sometimes refinery crude rate reductions, they should be planned and communicated effectively to the refinery’s Planning Department to ensure that crude and product inventories are managed appropriately. Effectiveness of the spall cannot be measured during the spall, so it is only after completion of the spall that effectiveness can be determined. The Coker Operations Team will manage the spalling procedure and communicate spalling results for each planned spall. Spall effectiveness should be captured as part of the unit’s health monitoring report and tracked on an ongoing basis.
Spall effectiveness is monitored by the process engineer – after the spall is complete – by comparing the furnace tube skins’ start-of-run (SOR) temperature after the spall with a post-pigging or post-turnaround SOR furnace tube skin temperature. If post-spall SOR temperatures do not meet expectations, the details of the last spall should be investigated as changes may be required to the spall procedure and/or duration and will need to be communicated to Planning. A poor spall can introduce an unplanned event in the refinery’s monthly plan to recover coker furnace performance before the coke may prove too difficult to remove in a spall and pigging becomes the only solution. Note that the Coker Operations Team should always be looking for a window for an “opportunity” spall to regain heater performance when little or no refinery impact would be incurred.
Spall efficiency is optimized by maximizing spall temperature, which is measured as the furnace pass outlet temperature. Work with your Inspection Department to determine the true limits of your furnace tubes and/or furnace outlet piping. One Andeavor site worked with a lower furnace outlet limit for a couple of years. This resulted in longer spalling durations as effectiveness was impacted by the temperature limitations. The Inspection Department reviewed the piping metallurgy and provided relief on the historical spalling temperature limits.
Quantity and quality of velocity steam (high pressure, dry) is important when determining the optimal spall conditions. Determining the type of spall technique – shock spall or continuous spall – will also affect the efficiency of the spall. Shock spalls will utilize a cycling of spall temperatures to try to break off the coke using a mix of hotter and cooler temperatures in the tube passes. Continuous spalls will use constant temperature and velocity steam to help spall the coke off the tubes.
Spall duration can be seen as a tradeoff between the number and duration of spalls per year. If your spalling effectiveness is not meeting the expectations of your Refinery Leadership Team, it is recommended that a plan be developed using a test matrix to determine the most effective spall method for your unit. Higher spall temperatures within established limits and longer spall durations are preferred, but optimization to minimize durations will always be requested by your Planning Department.
Below is an example of a test matrix which can be used to develop an optimized spalling technique. An Andeavor site created a table that utilized conditional formatting to compare spall effectiveness and spall technique to generate a visual tool to demonstrate overall spall effectiveness. Darker green means spall effectiveness closer to baseline, with dark reds indicating a poor spall. Font color is used to explain the duration of each specific spall. Parameters that were changed included duration and furnace outlet temperature. Changes led to a new spall procedure that takes 24 hours to achieve the same performance that spalls of 48 hours did a year ago. This modification reduces the LPO associated with planned spalls by up to half.