Question 36: What are the best practices for maximizing catalyst run length in NHT units that are limited by reactor pressure drop?
Wayne Woodard (Valero Energy)
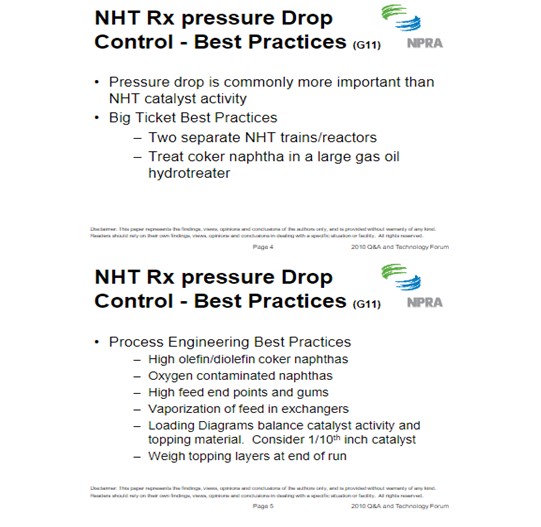
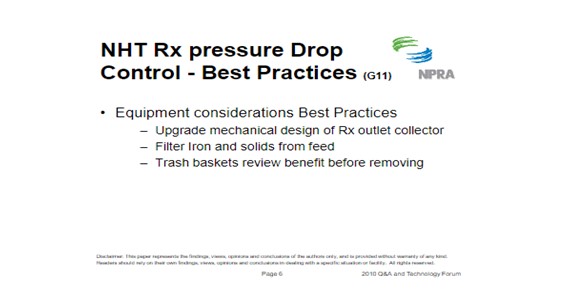
Greg Harbison (Marathon Petroleum)
Marathon’s experience with NHT fouling has been primarily corrosion products from upstream units and oxygen related polymerization of the naphtha. The use of feed filters can help minimize the effects of corrosion products. Oxygen related polymerization has impacted our NHT units from air leakage across intermediate naphtha storage tank seals and in purchased naphtha. Nitrogen blanketing intermediate tanks can be an option if these projects are shown to be economical. Antioxidants are used to treat purchased naphtha, but this only reduces the impact of oxygen related fouling. It is important to apply the antioxidant treatments prior to naphtha contacting oxygen. We are currently considering a test run using an antioxidant treatment of naphtha prior to intermediate storage in one of our plants. We have also tried oxygen stripping in units that process purchased naphtha. We have seen some success in improving run length. Our experience is the longer the oxygen has a chance to react with the naphtha, the less effective oxygen stripping becomes. The best solution to avoid oxygen contamination of the NHT feed is to bypass intermediate tankage altogether.
We also have specifications for olefins and di-olefins for our purchased naphtha. For plants processing transmix material, olefinic material may be present and end up in NHT unit. In these unique cases, we try to maximize the hydrogen to hydrocarbon ratio in an attempt to saturate the olefinic material and not let it polymerize to coke. Limiting this olefinic material is a key to controlling reactor pressure drop.
In a lot of cases, the oxygen polymerization is formed in the feed exchangers and deposited on the heater tubes. Over time the material will eventually migrate to the reactor. Unit upsets and shutdowns can have a significant impact. Thermally cycling a unit can dislodge solids from the exchangers, and heater to a lesser extent, causing reactor pressure drop. We have not found a solution to this other than maintaining reliable unit operation, and generous cooldown/warmup temperature ramp rates of the order of 50-75 degrees per hour. In some of our units, we periodically take unit outages to clean the feed exchangers and de-scale the reactor heater tubes to remove fouling material from the unit.
Historically, trash baskets were widely used to catch scale to improve NHT reactor run lengths. Marathon has moved away from this technology and shifted to traditional grading. We are now starting to use modern wafer style gradings that offer higher void space in the top layers of the NHT reactor bed. We have tried a couple of these different gradings and seen improvements in the reactor run length. Most of our NHT’s have migrated away from being pressure drop limited and currently are silicon limited.
Processing untreated coker naphtha in the NHT is a definite source of fouling in the unit in general and can shorten the reactor run length. Several of the ideas presented above also apply here. We try to run this material directly to the unit, avoiding tankage and possible oxygen contamination. If routed through tankage, our experience is to nitrogen blanket the tank. We have also maximized our hydrogen/hydrocarbon ratio to ensure as much hydrogen as possible is available to react with olefins and di-olefins.
John Clower (Chevron)
There are various means by which the reactor loop and catalyst bed fouling occurs in NHT service:
•Deposition of particulates in the feed
•Feed soluble metals •Reactor loop corrosion
•Feed oxidation and polymerization products
•Heavy ends carried in feed
•Catalyst or support material breaks up during loading or operation
•Rapid heating of fresh catalyst
•Reactor internals problems
Fouling mitigations include:
•Feed filtration to remove particulates (at least 25 microns)
•Make sure internals are assembled properly and remain clean during loading
•Minimize exposure of feedstocks to air in tankage, especially cracked stocks
•Minimize temperature cycling
•Use graded catalyst loading for the top bed (Fig. 1)
•Ensure “Dry Point” is reached before the furnace (heater tube fouling)
•Reduce hydrogen flow or recycle (increased deactivation)
•Ensure inlet device breaks momentum of feed •Increase operating pressure of unit
•Mechanical bed movement, such as flow disruptions
•Chemical injection to disperse foulant
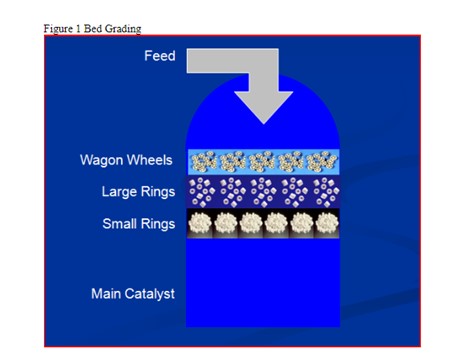
Dean Edgar – Criterion Catalysts & Technologies)
Post cycle deposit analysis can greatly aid in identifying the fouling mechanism, helping in determining the mitigation efforts. However a number of best practices can be followed to reduce the potential of polymerization and particulate related fouling in the system:
•Run cracked stocks directly from their processing unit to the hydrotreater without intermediate storage.
•If required to use intermediate storage, tank should be inert gas blanketed and floating roof.
•Minimize mixing cracked feeds with straight run feeds taken from storage where they may have entrained oxygen.
•Utilize feed filters for cracked feeds containing particulates, e.g. delayed coker naphtha.
•Use materials at the top of the reactor to grade for both size and catalytic activity. Use the minimum reactor inlet temperature required to meet product specifications.
Gregg McAteer (Nalco Company)
We apply a chemistry to the top of the reactor bed that is designed to open up spaces in the fouling crust that has formed on top of the catalyst bed. We have found more than 80% of the time we get a sufficient decrease in pressure drop to allow the refiner to hold charge until the scheduled run length. Some reactors show good improvement in the first day, others don’t show improvement until after the first 24hours of the cleaning. Below Is an example of the nearly 70 psi pressure recovered in the first 24 hours of an NHT reactor cleaning:
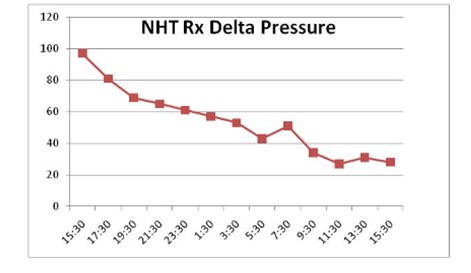
Sam Lordo (Nalco Company)
One approach of minimizing one of the potential reactor bed foulants, FeS, is to control the transfer of FeS from upstream units. This is done by addressing corrosion in those upstream units, or installation of feed filters (as small as 1-5 micron). Once fouled the reactor bed pressure drop can be reduced with the use of reactor bed FeS dispersants, such as what Nalco supplies. Below is a pressure drop improvement from the use of Nalco’s dispersant.
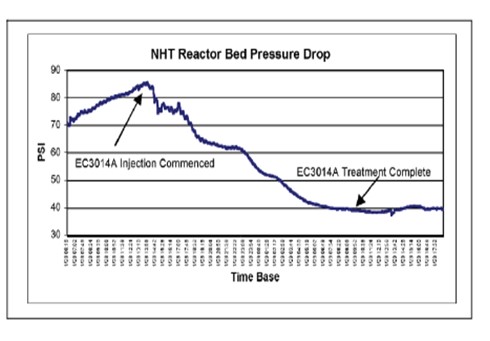