Question 36: Has the increased use of tight oil crudes and western Canadian crude been correlated with increased metals and solids in diesel, gas oil or vacuum resid?
SHARPE (Flint Hills Resources, LP)
The FHR CC (Corpus Christi) refinery has not seen an increase in raw crude filterable solids. With the increased domestic crude rates, we typically run about 20 to 50 pounds per thousand barrels with these occasional spikes to 100. We have recently started monitoring the filtrate from the 0.45 micron test with 0.1 micron paper. We see loadings in a similar range, but we do not have much historical data for comparison.
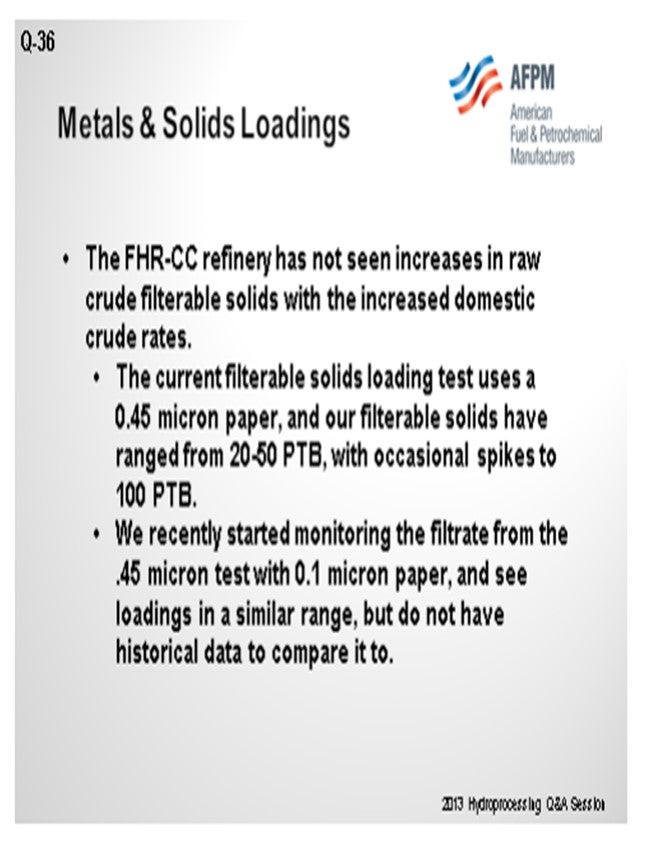
We have seen an increase in copper and barium on the FCC catalyst. Vanadium and nickel were decreased by about 50% in the ARC (atmospheric residue) from our tight oil crude unit. The crude units we have been running, with a mix of domestic and some foreign crudes, have not shown substantially decreased metals.
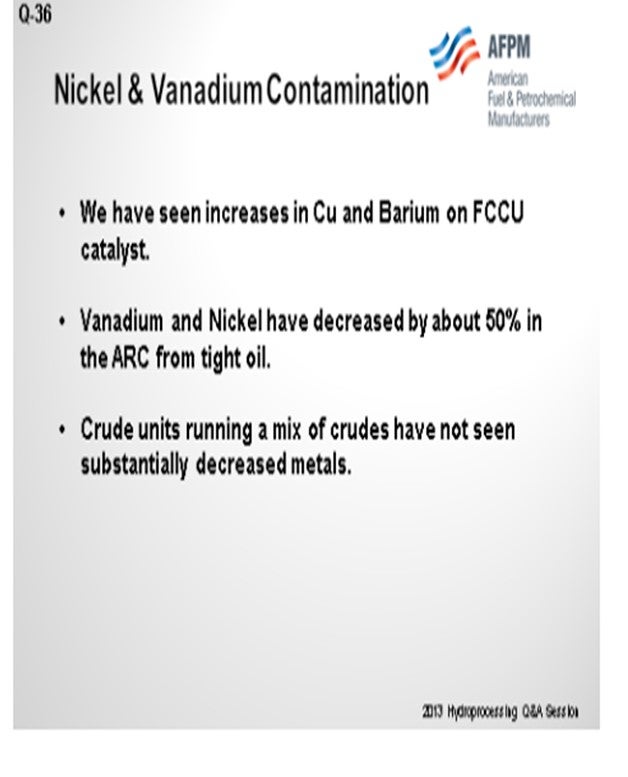
The slide of our atmospheric resid shows that the vanadium and nickel have come down substantially since we started running a lot of domestic.
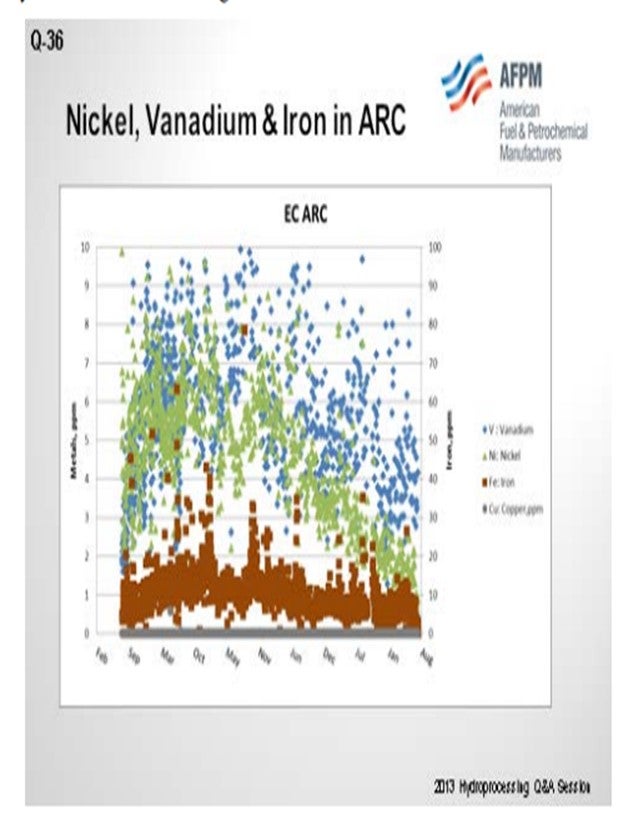
VICHAILAK (Marathon Petroleum Corporation)
The question is about tight oil and Western Canadian crudes. The two types of crude are on totally opposite sides of the pole. Tight oil is normally light sweet, low in metals, and paraffinic in nature. The prevalent areas where you get this type of oil are Bakken, Eagle Ford, Permian Basin, Niobrara, and Utica, Ohio.
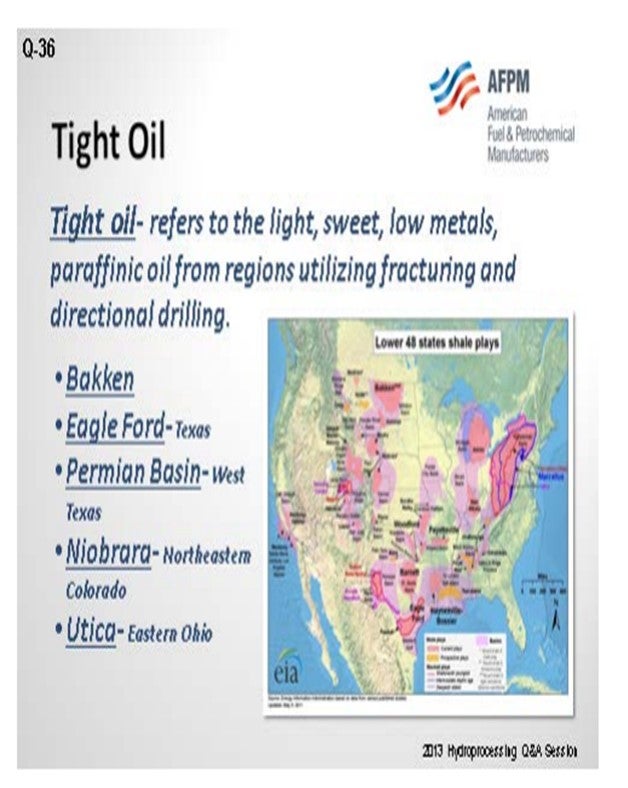
Because tight oils are very low in metals and do not impact the hydrotreaters very much, I learned from my queries that the industry has not seen any increase in the metals from tight oil crude. Nickel and vanadium are usually low and may contain phosphorus, but that is due to the general fracturing agent they add in artificially, not from the crude itself. As I said, we do not see any impact on the processing of tight oil. We have seen barium in one of our reactors that processes Eagle Ford crude, but the barium is mixed in and hard to separate. Phosphorus can be a potential problem, both in foulings and deactivation. I think Brian discussed this a while ago.
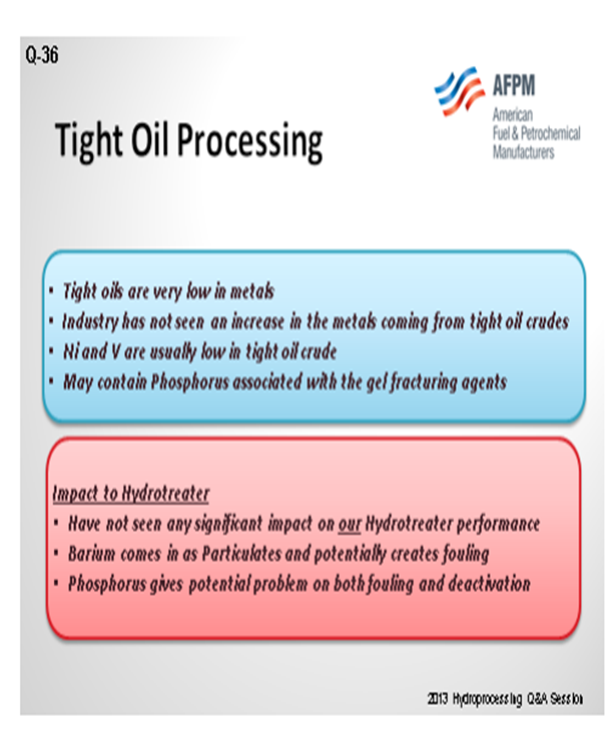
Now I will talk about Western Canadian crudes. These are heavy asphaltic diluent bitumen blends. The bitumen portion has very high metals and will contain solids. It depends on how it was processed: either having been mined or produced by SAGD (steam-assisted gravity drainage). This type of crude contains high nickel-vanadium, so the gas oil and Bakken reserve will have very high nickel-vanadium as well.
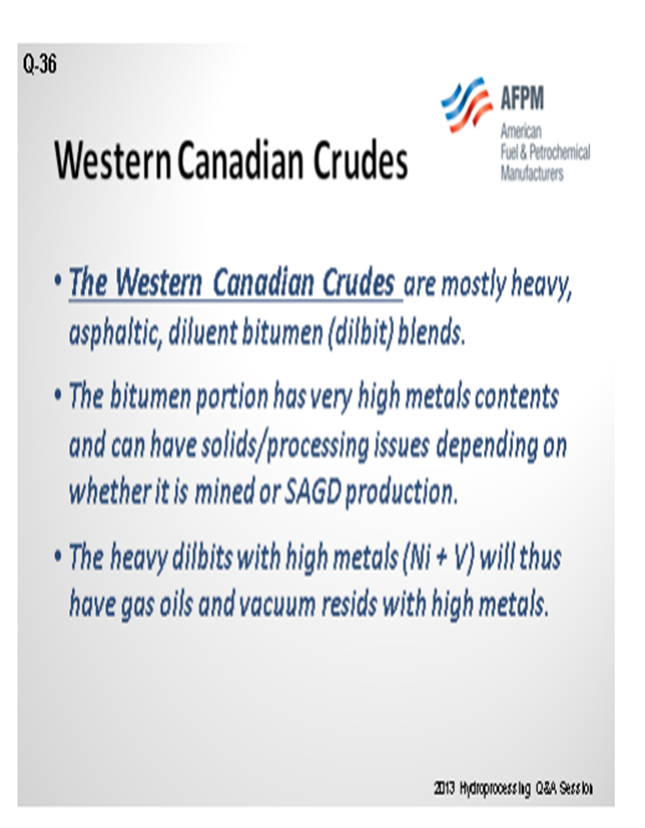
Marathon has experienced asphaltene precipitation in the pre-heat circuit of our crude unit, but nothing downstream of it. We have not had any issues linked to precipitation in a downstream unit besides the pre-heat exchangers. However, our refinery that processes this type of crude separately has one train treating process only for tight oil and another for heavy crude. The product from the crude unit then gets mixed in between and goes to the same hydrotreater, for example. We can see the potential for issues when this happens. But as far as asphaltene precipitate, we normally do not put asphaltene to fixed bed hydrotreaters anyway. We try to prevent having asphaltene going in, so we do not really see any problems processing these feed streams.
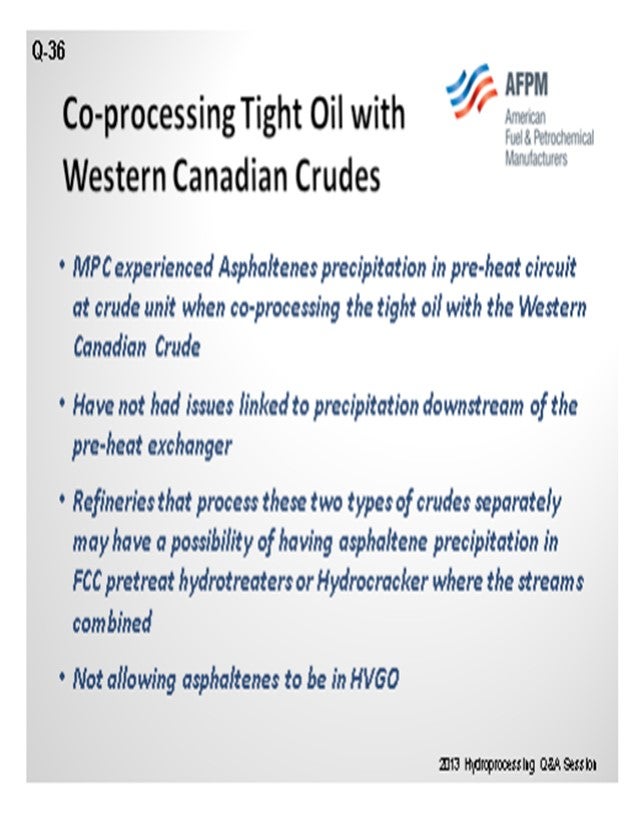
MONTRI VICHAILAK (Marathon Petroleum Corporation)
Tight oil and Western Canadian crude are very different in nature. Tight oil refers to the light, sweet, low metals paraffinic oil from regions utilizing fracturing and directional drilling. The most prolific tight oil regions are:
• Bakken: primarily North Dakota, tremendous growth, two-thirds of Bakken now being railed out due to economics and pipeline constraints;
• Eagle Ford: Texas;
• Permian Basin: West Texas, combined into the WTI (West Texas Intermediate) stream;
• Niobrara: northeastern Colorado, White Cliffs condensate; and,
• Utica: eastern Ohio, volumes very low, mostly >50 API (American Petroleum Institute) condensate
These oils are very low in metals. Except for the phosphorus associated with the phosphorus-based gel fracturing agents.
\Marathon’s experiences from processing Eagle Ford crude are fouling in the lower section of crude tower where the foulant has been identified as barium that had come from drilling mud. We also see a significant amount of barium in fines retrieved from the distributor tray coming from the lead beds of FCC pre-treat hydrotreater. So far, we have not had much problem with processing tight oil in hydrotreaters.
The Western Canadian crudes are mostly heavy, asphaltic, diluent bitumen (dilbit) blends. The bitumen portion has very high metals contents and can have solids/processing issues depending on whether it is mined or SAGD produced. The heavy dilbits with high metals (Ni+V) will thus have gas oils and vacuum resids with high metals.
Marathon did experience asphaltenes precipitation in pre-heat circuit at crude unit when co-processing the tight oil with the Western Canadian crude. As the two opposite types of crude are mixed, the asphaltenes’ solvency reduced, causing it to precipitate out. We have not had issues linked to precipitation downstream of the pre-heat exchange.
For the refineries that have multiple crude units processing tight oil and the Western Canadian crude separately and where the heavy vacuum gas oil from both crude units is sent to a gas oil hydrotreater, there is a possibility that the asphaltene precipitation can occur in the hydrotreater. This problem may be manageable by optimizing crude/vacuum tower operation as initially, there should not be any appreciable amount of asphaltenes in the heavy vacuum gas oil.
GREG SAVAGE (Nalco Champion Energy Services)
High solids content in tight oil, typically iron and calcium salts, concentrate in the residual oil streams. Removal of the solids at the desalter, through optimization and solids removal agents, can minimize the amount of solids in the vacuum residual oil. Calcium and iron have been successfully reduced at the desalter using metals removal additives.