Question 35: What important parameters do you consider in designing a post-treat bed for a hydrocracker? What are the advantages and disadvantages between Type I and Type II catalyst when used as a post-treat bed in a hydrocracker?
McARTHUR (Phillips 66)
The post-treat bed is generally positioned at the bottom of the reactor in a hydrocracking reactor, and its main purpose is to remove sulfur compounds that have recombined with the organic compounds coming out of the reactor. Usually, it is a function of olefins that are generated in a hydrocracking catalyst. In our experience, designing the post-treat bed should be a little dependent on the type of cracking catalyst it supports. Now we have had some dewaxing catalyst post-treat beds that have performed poorly, and we think it was just because they were undersized. General space velocity recommendations, as we have heard, range from 12 to 15 hr1 (inverse hours). In our experience, I was just talking about how that was not enough and that we needed even a lower space velocity.
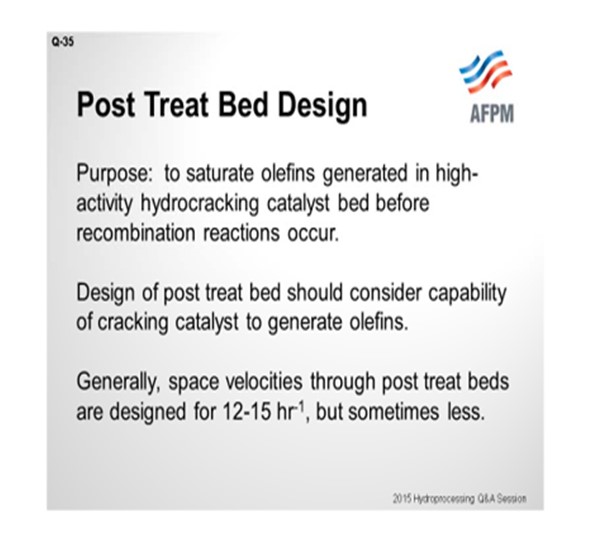
End-of-run post-treat bed temperature is also a consideration. The higher the temperature at the bottom of the bed, the more prone those recombination reactions are to occurring. But as far as Type I and Type II catalysts, olefin saturation and sulfur removal reactions are not especially difficult reactions. So, in theory, we do not really think there would be a need for a Type II catalyst in a post-treat bed. We do have some pretty good experience with both. I am going to put up a couple of slides and walk you through them.
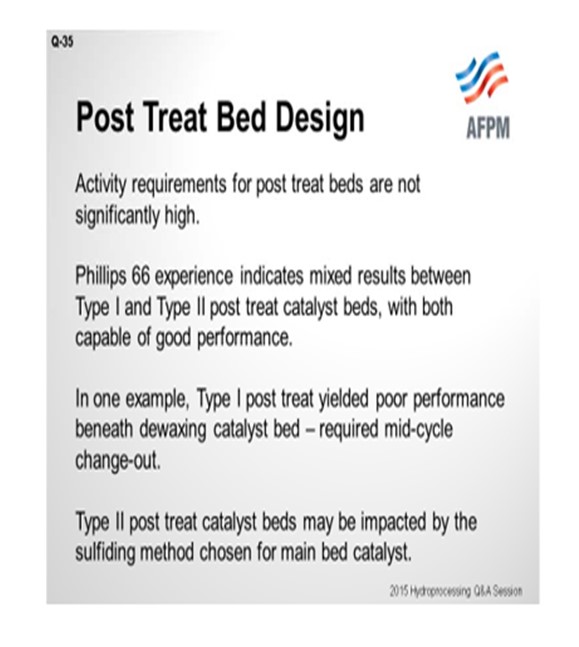
This first example is on a hydrocracker in one of our refineries: two different cycles with very similar cycles, as far as feed and operating conditions. They may not be exactly apples to apples, but we think they are pretty close. One initial run had a Type II post-treat bed, as shown in blue. It had a pretty good performance throughout the cycle with mercaptan sulfur in the light hydrocracking stream. A subsequent cycle, as shown in red, had a significantly worse performance. This subsequent cycle was with the Type I post-treat catalyst.
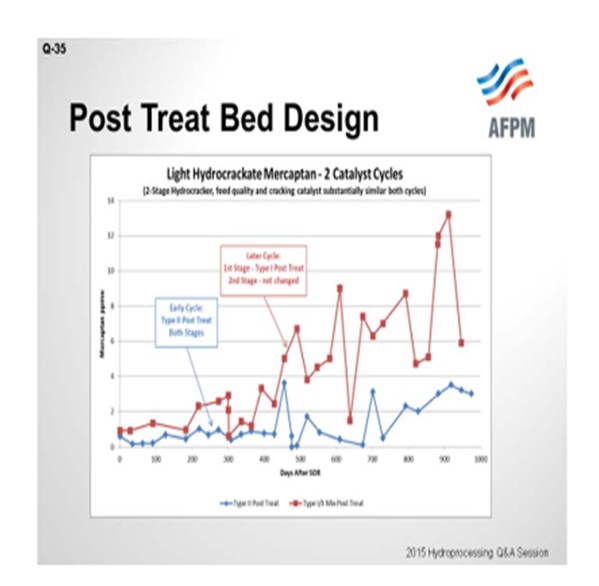
The second slide shows another unit at a different refinery. I actually have two cycles plus part of a third cycle. As you can see, Cycle A (in blue) was the Type I post-treat. It actually did pretty well through most of the cycle. The second cycle, in red, was a Type II post-treat bed, which had enough sulfur recombination in it that it was causing some blending issues by the end of the run. This third cycle, again, was a Type II post-treat. The sulfiding methods were different between the two Type II catalysts. The gas-phase sulfiding was not recommended by the catalyst providers, so we might have shot ourselves in the foot there.
If I have been coherent with my descriptions here, you will see that our data conflicts and that we do not really have a clear picture on which one is better: Type I or Type II. That is where we stand.
PEDERSEN (UOP LLC, A Honeywell Company)
The interest in post-treat catalyst, and the associated issue with mercaptans formation, primarily relates to the naphtha fractions. As shown in this example, higher sulfur and higher mercaptans content are typically found in the lighter fraction. In this chart, sulfur content is shown on the Y-axis and time onstream on the X-axis, where red symbols represent the light naphtha data and green shows the heavy naphtha measurements.
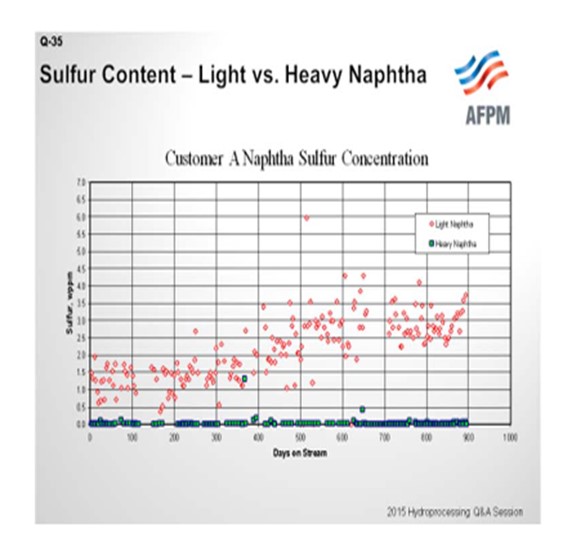
There are two factors that contribute to this type of result. First, the formation of light mercaptans is much more thermodynamically favored than the formation of heavy mercaptans. The second is, as we have all experienced, that the selectivity for heavy naphtha in a hydrocracking operation is much higher than for light naphtha; so we have a much bigger dilution effect in the heavy naphtha fraction.
As Scott already indicated, our purpose in looking at installing a post-treat catalyst is to saturate olefins, which are precursors to mercaptans formation downstream. Type I catalysts typically have more than adequate activity to accomplish the goal of saturating olefins. If this is the situation in which we find ourselves, Type II catalysts may actually be detrimental in that Type II catalysts are often formulated with a higher level of acid function. More acid function may result in slightly higher olefins content coming out of the reactor. If conversion of organic sulfur compounds is really the objective, then it can be important to use a higher activity catalyst like, perhaps, a Type II catalyst. And as Scott indicated, it may be necessary to drop the space velocity considerably in order to achieve this goal. Just one more comment: We very commonly install post-treat catalyst in hydrocracker operations. If sulfur in the naphtha fractions is not an issue, either due to blending specifications or the fact that the material will be treated again downstream, the space used for post-treat catalyst may be more optimally loaded with hydrocracking catalyst.
SUBHASIS BHATTACHARYA (Chevron Lummus Global LLC) I would like to add that the difference between Type I and Type II is mostly evident during the startup. Type II catalyst uses a particular reagent to get a better dispersion of the metals during startup. So as long as you are using a hydrotreating catalyst, whether it is Type I or Type II, if it does not have any acid/cracking function, it will not introduce more mercaptans. So if you have a Type II hydrotreating catalyst as your main hydrotreating bed, then you can continue with the same as your mercaptan control layer or the post-treat. As Scott showed with some of the results from his testing, it is very clear that Type II, with better metal dispersion, showed much better mercaptan control in those layers. So I would like to say that you do not have to go for Type II specifically for post-treat. You can continue with the same catalyst system you already have for your primary hydrotreating function.
DAVID VANNAUKER (Haldor Topsoe, Inc.)
The first question to answer is the purpose of the post-treat bed. Is it to handle mercaptans or to provide additional desulfurization of the partially cracked and easier to treat molecules? The traditional purpose is to saturate olefins to prevent mercaptan reversion that is most prevalent in the naphtha fractions. Other refineries require additional volumes of hydrotreating catalyst to provide additional desulfurization. Many units have been expanded and today are running with twice the original feed rate. In some of these units, the cracking catalyst volume is on the edge of the required amount, and the partial conversion of molecules occurs. In addition to mercaptans, thiophenes are sometimes found in the naphtha and diesel fractions. For these units, additional post-treat catalyst may be warranted and justified to improve the desulfurization. For naphtha streams, the costs of additional processing or sulfur traps can be avoided; and for diesel, the lower product sulfur can provide additional blending flexibility in the refinery.
The main advantage for Type II catalysts is the activity. Type II catalysts have higher activity. Therefore, a smaller volume of post-treat catalyst can be employed. However, Type I and Type II catalysts can both provide good performance. Startup procedures are another key consideration. Please check with your vendor to ensure that the startup procedures are compatible with the catalyst. Since Haldor Topsoe, Inc. Type II catalysts are manufactured to enable the standard startup, the traditional startup procedures can be employed.
JOE FLORES (Criterion Catalysts & Technologies / Zeolyst International)
Space velocity is an important factor to consider when designing the height of the post-treat layer, and the post-treat bed is typically designed with a LHSV in the 12 to 25 range. More severe operations tend to require more catalyst, and the amount of H2S in the recycle gas also has a bearing on amount of catalyst required. Prior experience in a typical service is helpful. Since post-treat beds are only needed for easy-to-treat sulfur species formed by recombination (i.e., mercaptans), Type II catalysts are typically not needed as their higher activity is not utilized. Since the post-treat catalysts tend to operate at high temperature at the bottom of the cracking catalyst bed, catalyst robustness is also a key consideration. Type I catalysts are usually all that are required.