Question 34: What is your best practice for minimizing octane losses based on unit operating parameters and/or catalyst types in FCC gasoline post-treat units?
Olivier Le-Coz (Axens)
Minimizing octane loss while hydro desulfurizing FCC gasoline implies minimizing olefins saturation with hydrogen. This is all about selecting the right operating conditions (temperature, pressure and H2/HC) so that the hydrodesulfurization reactions are fast enough, but the kinetics of the olefin's saturation reactions remain low.
One also mostly need a highly active but selective catalyst in those conditions. Axens has developed a series of non-noble metal-based catalysts which are extremely well responding to those objectives.
Another challenge is to meet cycle length in sync with the FCCU and therefore identify and eliminate contaminants that would affect the catalysts, such as arsenic. Unlike conventional hydrotreaters (DHT, CFHT) which may also experience arsenic contamination, arsenic removal must be achieved without olefin saturation to minimize octane loss. Such catalysts have been developed and are successfully operating in many Prime-G+ units.
Process scheme optimization is very important to minimize octane loss. Axens’ PrimeG+ addresses this problem. It has many references worldwide and in the US. PrimeG+ scheme is customized for each feed’s quality, it usually involves a selective pre-treatment reactor to remove diolefins and then a selective hydrodesulfurization reactor. Pre-treatment is performed at low H2/HC and low temperature, HDS at higher H2/HC and temperature.
Depending on the distillation range of the FCC gasoline to treat, the scheme may involve differentiated treatments on split cuts. PrimeG+ can desulfurize the full range FCC gasoline down to 10 wppm Sulfur while minimizing octane loss and achieving extremely long cycle lengths (more than five years).
Over-desulfurization should be avoided to minimize octane loss. Several refiners have successfully used a combination of inferential developed by Axens along with APC to achieve this goal and also to minimize utility consumption.
Ujjal Roy (Indian Oil Corporation)
In our refineries, FCC gasoline is treated for sulphur removal targeting minimum octane loss. Our target gasoline sulphur is 50 ppm and 350 ppm in two grades. We process normally high sulphur crudes. The general configuration adopted in our refineries is first FCC gasoline with sulphur varying from 300 to 500 ppm and RON of about 92 goes for selective hydrogenation for di-olefins conversion to olefins and for conversion of light sulphur species to heavier ones. The outlet from selective hydrogenation unit is split in three cuts (a) LCN i.e. IBP-65°C with low sulphur content sent directly to gasoline pool, (b) MCN i.e. 65-85°C with sulphur content of less than 100 ppm is either taken to Isom unit or directly routed to gasoline pool depending upon margin available in benzene and sulphur limit, (c) the heavy cut i.e. HCN (85°C – FBP) with high sulphur content goes for hydro-desulphurization. Some typical balance across selective hydrogenation is given in table below:
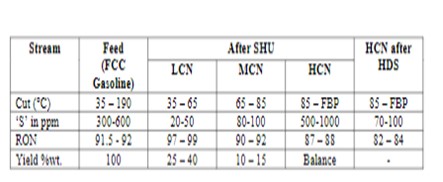
Selective hydrogenation inlet temperatures are maintained at about 120°C with temperature rise of about 16-18°C. The pressure is maintained at about 16-18 kg/cm2 with H2/HC ratio of 7-9 Nm3/M3. With loss in catalyst activity, temperature can be increased up to about 150°C. SHU catalyst is Ni-Mo based. HDS is operated at a pressure of about 17-18 kg/cm2 and at inlet temperature of 230-250°C. HDS catalyst is Co-Mo. Depending upon the feedstock quality and by adjusting operating conditions, we are able to contain RON loss between 0.8 to 2.0 across SHU and HDS (FCC Gasoline post treat block). In case of higher severity operation, RON loss can go as high as 3.0.
Minimizing RON loss in FCC gasoline post-treat units, in our configuration, depends on how good we are splitting the gasoline after SHU and adjusting blending proportion in finished gasoline pool. We try to operate SHU at minimum possible severity to minimize RON loss. The RON loss across SHU is nominal when operated at optimum just to convert di-olefins and light sulphur species. Depending upon the sulphur content in HCN, HDS severity needs adjustment. The loss of RON across HDS can be as high as 5-6 units. However, through appropriate splitting after SHU, stream properties can be optimized to ensure minimum RON loss. In one of our units, we have discontinued MCN draw as benzene content in gasoline pool is in control. After discontinuation of MCN, the split between LCN and HCN was 46 : 54 wt. ratio initially. At this split, the RON loss in HCN across HDS was 3.0 units. We reduced HCN draw to 50 wt.%. This reduced the space velocity across HDS reactors, and we could reduce RIT by about 15°C. The RON loss came down by about 1.5 units after these adjustments due to shift of lighter olefins to LCN thereby reducing hydrogenation potential in HDS. But such adjustment is again limited by olefin specification in finished gasoline. Currently, we are implementing APC in one of our FCC gasoline post treat units to minimize RON loss.
Brad Palmer (ConocoPhillips)
ConocoPhillips has almost all of the available technologies for FCC naphtha post-treating in service within our system. The technologies we apply include Prime G, Scanfining, CDTech, S-Zorb, and conventional hydrotreating at mild conditions. Most of these processes use proprietary catalysts operated at relatively mild conditions to avoid olefin saturation while still removing residual sulfur. We follow licensor guidelines for the operating conditions. In some of our refineries, we actually pretreat the FCC feed sufficiently to avoid post-treatment. This avoids the whole octane loss issue, but is expensive. The severe treatment is driven by other factors. As we are considering moving to < 10 ppm sulfur in gasoline, we will be able to modify some of these systems to meet the new spec fairly easily, while others will probably not be capable of meeting the 10 ppm spec without major work. In all cases, additional octane loss is unavoidable. Fortunately, most of our refineries are not short octane.