Question 34: What are your current protocols, practices, and concerns for using wireless communication between field instruments and the control room? Would wireless communication be acceptable for monitoring only, or is control allowed as well?
LOGEROT (Prosys Inc.)
The question asked about the protocols. But rather than naming the protocols, I think it would just be best to describe what the installation looks like. With wireless transmitters that are in use, you are usually installing a mesh network and you have a Modbus gateway connected to the DCS. You have a separate wireless gateway that is connected to that as well, and the wireless gateway connects to all the transmitters. Each one of the transmitters can actually act as a hub and is able to receive and transmit data with the other transmitters. That way, transmitters can find other transmitters close by and multiple pass-backs to the gateways. So, if a transmitter is out of service for any reason, the other transmitters will basically find pathways around it to get communication back to the wireless hubs.
Note that in this kind of arrangement, you need to have a robust gateway; because basically, the wireless gateway represents a single point of failure. Therefore, most installations use redundancy there, sometimes triple redundancy, to make sure that communication stays open.
Where are the main uses of wireless in refineries today? In our experience, they are usually remote areas of the refinery where a signal and power wiring are not easily run out. The big advantages, obviously, are cost savings, conduit wiring, and cable trays. Inside the battery limits of, say, a crude unit, wireless is not as common. Where used, it is usually for auxiliary type of measurements such as corrosion monitors, vibration monitors, additional temperatures, and pressures that are not central to the process. You might also consider wireless technology, as sometimes we have outside operators who have handheld devices that are wirelessly connected back to the control room. For that one-ring device, there will also be a network of gateways available for the wireless device to communicate back to the control room.
What are the concerns associated with wireless technology? The first real concern is cybersecurity. I mean, everyone is concerned about security these days. Basically, every wireless device and transmitter in your plant represents a potential entry point for intruders. So, you have to be very careful to put in strong security protocols to make sure that intruders will not get into your network. What can happen from an attacker? An attacker can jam your signals. You could lose proprietary data, and – worst of all – an attacker could end up gaining control over part of your process. You really do not want that to happen, which is why security is a big concern when using wireless. Second is overall reliability. Basically, we have been using hardwired signals for decades. Wireless signals are just not as robust in today’s technology as are the hardwired signals. For example, how often do you have to go reset the Wi-Fi in your house? That is an example of when wireless is not as reliable as it could be.
The last part of the question had to do with whether wireless is acceptable for control or if it is just for monitoring purposes. When I say ‘control’, I am talking about closed-loop control where you have a wireless transmitter communicating to the control room and there is a control action. They then signal out to the final element, usually a valve. It is probably also wireless, but it might be hardwired; but there is at least some component in that closed-loop control that is wireless. Our typical answer is that it is just not used very often for closed-loop control, and it is usually not recommended. One of the problems is battery life, because the transmitters you are using in the field are battery-operated. If you have a very high refresh rate – like, typically, a five-second refresh rate, then your batteries will die too quickly. That is one reason why you would not want to be using wireless for controls. So, generally speaking, it is not recommended or used. However, that is not to say that wireless control will not, sometime in the future, be relatively common.
THEISS (Marathon Petroleum Corporation)
The chart on the slide is really the internal guidance we use at Marathon. You can see that for what we call Class 0 and Class 1, we do not allow wireless communication, which basically inputs to an SIS (safety instrumented system) or some control point that is detrimental to the process. An example of a detrimental control point would be an FCC (fluid catalytic cracking) reactor/regenerator pressure differential transmitter for which we would not allow wireless control.
There are a couple of applications in which we allow control. I do not think they are widely used within Marathon; but with some corporate guidance and corporate technologist approval, we can use them wireless for control. These would be considered Class 2. An example would be a tray tower control for a temperature.
As you move further down the chart to Class 3, you can see an example of where you have the overhead water boot. You have a remote signal that goes into the board, but it relies on the operator to go out and make the move to drain that water boot and start to pump or open up a valve. Class 4 and Class 5 are really for informational purposes. My example for a Class 4 would be a secondary alarm on a tank where you have a primary alarm that is hardwired in and a secondary level or a backup level that could be used remotely. Class 5 would be temperature indication on heat exchangers just to gather data for fouling.
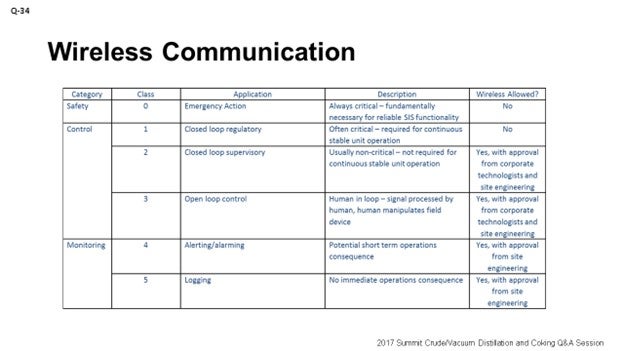
JEREMY THEISS (Marathon Petroleum Corporation)
Technology continues to progress in this field. Since 2011, we have had guidance that allows some usage of wireless instrumentation, but this technology is limited based on application. The table below identifies our stance on certain applications.
CATEGORY |
CLASS |
APPLICATION |
DESCRIPTION |
WIRELESS ALLOWED? |
Safety |
0 |
Emergency Action |
Always Critical: fundamentally necessary for reliable SIS functionality |
No |
Control |
1 |
Closed-loop regulatory |
Often Critical: required for continuous stable unit operation |
No |
2 |
Closed-loop supervisory |
Usually Non-Critical: not required for continuous stable unit operation |
Yes, with approval from corporate technologists and site engineering |
|
3 |
Open-loop control |
Human in Loop: Signal processed by human, human manipulates field device |
Yes, with approval from corporate technologists and site engineering |
|
Monitoring |
4 |
Alerting/alarming |
Potential short-term operations consequence |
Yes, with approval from site engineering |
5 |
Logging |
No immediate operations consequence |
Yes, with approval from site engineering |
Examples:
Class 0: Inputs to a Safety Instrumented System
Class 1: FCC Reactor/Regenerator pressure differential transmitter (used to manipulate flue gas stack valve)
Class 2: Tower tray temperature
Class 3: Water boot high/low level where control or field operator starts/stops a pump or opens/closes valve
Class 4: Storage tank secondary level alarm
In most of the approved applications, redundant wireless gateways are required to minimize disruptions to a failed gateway. Other points to consider for determining if wireless is acceptable include the required scan rate of the application, wireless distance limitations, and potential for wireless interference. Guidelines should be made to ensure battery life or alternate power to the wireless device is sustained and has monitoring capabilities.
DARWIN LOGEROT (ProSys Inc.)
Wireless Protocols
Rather than naming the protocols in use, it is probably better to describe the installation. Where wireless transmitters are in use, they are often installed in a mesh network similar to cellular towers or a Wi-Fi network with multiple hubs. A Modbus gateway is connected to the DCS and to the wireless gateway that is connected to all the transmitters. Each wireless transmitter acts as an individual hub and is able to receive and transmit data with others. This way, a transmitter can find other transmitters close by and have multiple paths to the wireless gateway. If one or two transmitters are out of service, the remainder will adjust to provide continuous communication.
In this arrangement, a robust wireless gateway is important. If only one wireless gateway is provided, it can represent a single point of failure, potentially losing view of all instruments using that path to the DCS. Users will typically install redundant gateways to mitigate this.
So, where are the main uses of wireless technologies in refineries today? The locations are usually remote where the signal and power wiring are not readily available. The big advantage is cost (savings in conduit, wiring, cable trays, power distribution, etc.) and the ability to monitor remote data, such as in a large, spread-out tank farm.
Inside a refinery process battery limit, use of wireless is not so common. Where it is used, some of the more common wireless applications are in corrosion monitors, vibration monitors, and additional temperature and pressure monitoring on vessels and exchangers (auxiliary to the hardwired temperatures and pressures).
Another use of wireless technology is for hand-held devices used by field operators. With this arrangement, another mesh network is employed to connect the wandering device to the DCS. The field operator can use the device to monitor operating conditions, execute periodic rounds, and take notes regarding observations. Major DCS manufacturers are offering this technology as an extension of the control system, but the control itself is done with hardwiring; only monitoring and setpoint adjustment are done through wireless.
What are the concerns associated with wireless technology?
First and foremost is cyber security. Every wireless device represents a potential entry point for an intruder. Security protocols are better and stronger now than ever, but many potential users are still reluctant to install extensive wireless devices. Security concerns include the possibility of wireless signals being jammed by an attacker, potential loss of proprietary data, or, worst of all, an outside intruder gaining control of part of a process.
The second concern is reliability. Wireless communication generally is less robust than hard-wired connections.
A third concern is the data refresh rate and its connection to battery life. For example, a one-minute update rate on the transmitters was tied to a life of about 10 years, whereas an update rate of four seconds reduced that life to two years. The relationship between refresh rate and battery life, of course, impacts how wireless can be used for basic control and impacts wireless maintenance costs.
So, is wireless communication acceptable for process control?
Allowing for a slightly wider definition of “wireless control”, it is in widespread use today – the plant radio. For example, the console operator can contact the outside operator: “Hey, go open/close the bypass valve around the control valve that is not working.” But more seriously, purely wireless communication for process control in a refinery is seldom used or recommended, especially in a unit that is tightly connected geographically, such as a crude unit or FCC. Where wireless communication is in use, it is almost exclusively for monitoring only, primarily due the problems outlined above. The closest approach to wireless control is using the handheld devices to adjust setpoints. The control itself is still through hardwire communications from the transmitters to DCS controllers and to the valves.
That said, there is no reason to expect that as technology improves, the current problems will not be overcome, at least in part. Perhaps future refineries will include widespread use of wireless process control.