Question 34: Hydroprocessing reactor pressure drop can increase due to feed particulates, corrosion by-products and polymerization reactions. How can bed design and loading method be optimized to avoid pressure drop limiting the cycle length or throughput?
McARTHUR (Phillips 66)
There are a lot of approaches to helping out with pressure drop problems in a reactor, and I will go through them. We use all of these at Phillips 66. I will start at the top. There are particulate catching trays. These are relatively new. We have had limited use with these, although we think they have been fairly successful. We are reviewing potential applications at some of our other units that have some historical issues.
Many of our units have had, and some still do, trash baskets or scale-catching baskets. But in general, we are removing them because they are difficult to load around. Removing them tends to add a lot of time at turnarounds, and they can actually create some maldistribution issues at the top of the bed. That is not always the case. There are some cases where we choose to keep them in the reactor. It is a site-by-site decision.
We think the primary workhorse is with the graded bed at the top of the reactor for two purposes. One is for particulate removal. There are many different kinds of particulates. They can come in with the feed and have several layers of size change. Shape change will spread this catch of particulates out across a large volume of material with a lot of void space and leave a lot of room for the oil to keep going through for longer and longer periods through the cycle.
Likewise, these graded beds can have some amounts of increasing activity built into them. We start with very low activity material to initiate some of those reactions, which helps avoid polymerizing compounds onto the main catalyst bed. The primary reaction here is saturation of the diolefin bonds that would otherwise, when hitting the primary high activity catalyst, polymerize right out. Also, if these polymers are going to foul out, I would rather they foul out in the high void space up in the graded bed rather than in the main bed.
Moving down to the loading method for the main catalyst bed, if there are typically DP (differential pressure) limitations associated with the main bed, then decreasing amounts of dense loading or eliminating dense loading can leave a little room for improvement in pressure drop across the reactor. This generally is not too significant, but it can help. And then actually, the choice of catalyst pellet size can be a factor as well. Smaller catalyst pellets tend to have a little higher pressure drop, so choosing a little larger pellet can have a small impact on DP across the main catalyst bed.
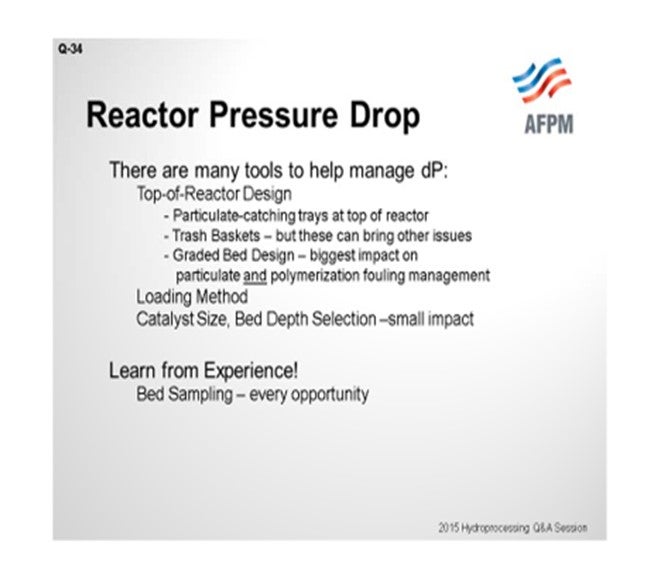
The diagram is what I have walked through. The main takeaway we would like to tell our engineers is that it is very site-specific; and really, the best way to learn the location of your issue is to do sampling at the end of the run, not just dump the catalyst and plan to load it like you loaded it last time because you got a “pretty good” run last time. It is really through sampling that you learn where the problem is in the reactor, what you are catching, and the cause of the problem. And then, you can optimize the bed for future runs after that.
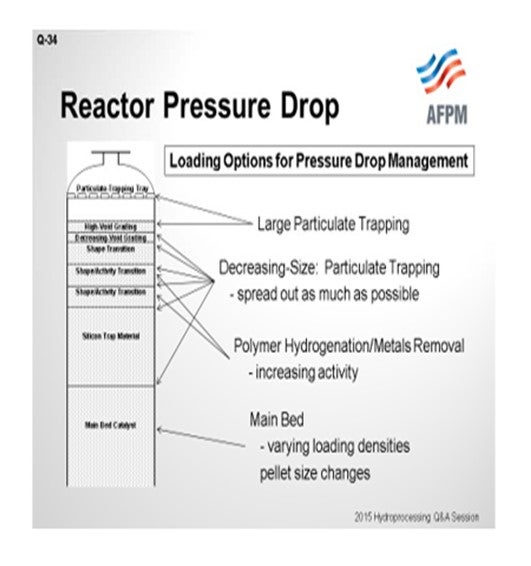
WRIGHT (Hunt Refining Company)
One method we have used to avoid pressure drop is, as Scott mentioned, balancing the amount of filtration material with the demet or graded bed. For example, our diesel hydrotreater was running into a particulate problem that resulted in high ∆P (delta P, pressure differential) on R1 (Reactor 1). So we stole some active catalyst volume and replaced it with filtration material to help us get the second half of the run finished. For our hydrocracker, we had the unusual experience of buying larger than required reactors relative to the design feed. [Laughter] We are on Cycle 2 now. In Cycle 1, we did not use up all of the space. We had some adventures in our feed resulting in some ∆Ps on R1, Bed 1. So during the skim, we filled up the volume that was there with the filtration material, again, to help us make the second half of the cycle. And as Scott mentioned, you can use the activity grading to help you balance pressure drop with activity, as well as employing dense versus sock loading at the appropriate times.
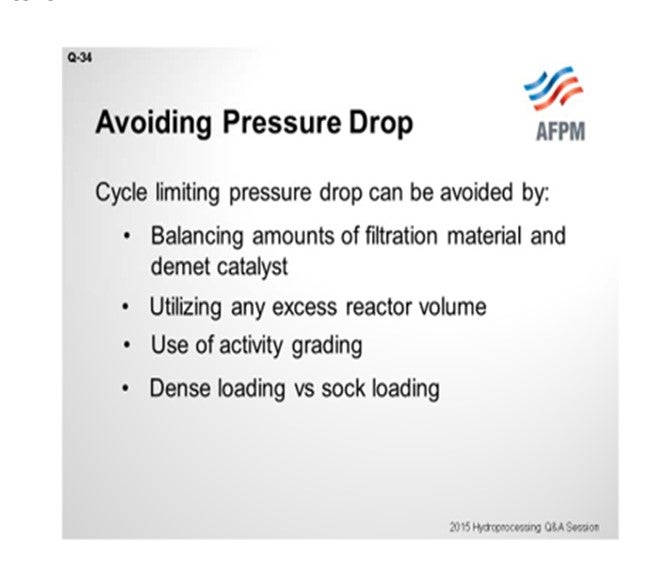
TEMME (Albemarle Corporation)
I agree with what Scott and Samuel just went over. Definitely, it is good to know the past to address the present. If you have something occur on the current cycle, it is hard to address quickly; but hopefully, you have had some past history to give you potential ideas for a path forward. You definitely want to make sure that a comprehensive size- and activity-grading catalyst loading is employed, looking particularly to see whether or not it is a particulates problem, a polymerization problem, or maybe a combination of the two and also whether or not that occurs at the interface of any one particular layer.
You have to check to see if dense loading is feasible. If not, do the unit hydraulics cause pressure drop limitations? In that case, sock loading has to be used. Yes, sock loading does give a lower initial reactor DP, but it can lead to less optimal flow distribution and potentially preferential coking, which then can lead to increased reactor DP if the sock loading is not done well. Another consideration is whether a larger sized catalyst may yield a lower reactor DP, but you must be certain that the loss of catalyst activity can be tolerated by the unit activity demands.
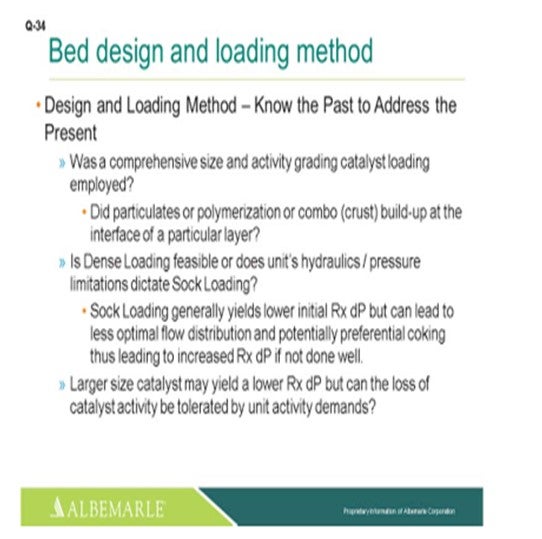
Really, you have to take a look at – I think in terms of a holistic way – the big picture and whether the upstream impacts are significant contributors. What is going on with the feed management? Is cracked feed storage problematic, in terms of nitrogen blanketing? Purchased feeds: Do they seem like a bad actor? Can the cracked feeds be hot-linked to run directly to the unit instead of going out to the storage? Are the purchased feeds properly blended and managed where you will not have purchased feed volume swings from high to low and back to high again, which can cause some issues, in terms of hydrogen consumption variability and potentially DP type of problems?
Upstream, especially at the crude unit: Are there good monitoring and inspection programs? Is there a comprehensive corrosion coupon installation in the crude unit that is monitored regularly? Have feed tanks been running for 10 years? Maybe they have not been inspected or cleaned, and you just have a high level of particulates, iron sulfide, or other solids buildup in the tank that is now working its way over into the unit. Now a lot of people have feed filters, but are they being worked on and maintained properly? And then there is their assessment of the captured materials. Have a particle-size distribution assessment been done to help give you an idea of how you might put your grading system together? So, we feel that all of this can be very helpful in avoiding pressure drop problems.
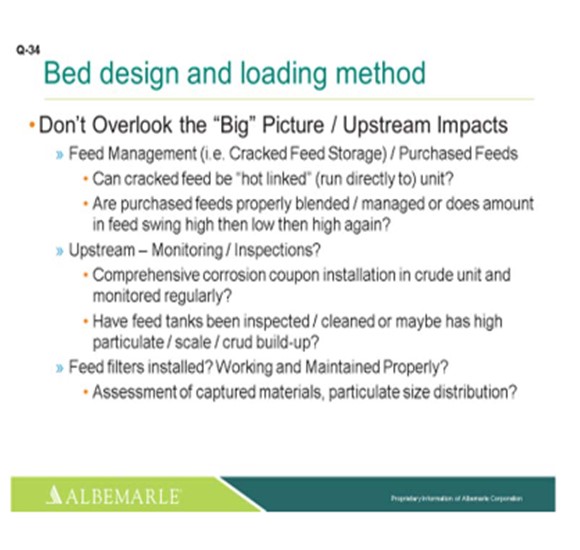
JAMES (TIM) CAMPBELL (Eurecat U.S. Incorporated)
I want to add a comment for those folks who use regenerated catalysts; because many times, there is a concern about pressure drop with regenerated. At Eurecat, we address that. We can test for relative pressure drop of the regenerated catalyst versus its fresh version and give you a factor that you could use in your evaluation.
SHRIKANT MADHAV VAIDYA (Indian Oil Corporation Limited)
I have one observation. The minute we have a recycle gas flow failure, after which the plant gets restarted, we have a step change in the R1, Bed 1∆P. So, could there be any reason for that?
McARTHUR (Phillips 66)
I guess there could be several reasons. If it typically trips your heater when you lose your compressor, the rapid cooling of the tube will sometimes cause coke material to slough off the tubes. And then when you start back up, you will carry that back onto the reactor bed. We have had that problem a few times. Also, any significant period of time where the oil on catalyst is a hot temperature with no hydrogen there, you are going to have some coking issues and fouling with that, too.
WRIGHT (Hunt Refining Company)
We were having recycle gas compressor issues in Cycle 1, so we were getting these nuisance trips. We saw that the fouling material in the CFEs (combined feed exchangers) would then flow to R1, Bed 1. And later on in the cycle, we were having charge heater limitation; so we intentionally pulled out the feed in order to slough the foul end off of the CFEs and onto the filtration material of R1, Bed 1. So we serendipitously observed that phenomenon and used it to our benefit later on.
PANKAJ DESAI [Shell Global Solutions (US) Inc.]
I agree with what the panel has said that having a well-designed graded bed is necessary to mitigate pressure drop issues. However in spite of that, upsets can occur. If you need extra insurance or protection against pressure drop, we offer a couple of devices in our reactor internals portfolio. If it is simply a case of inorganic iron or scale deposits, then we offer a simple scale-catching tray that helps to minimize pressure drop. For more complex feedstock issues with gum precursors or treating cracked feedstocks, we offer a more sophisticated device called a filter tray that helps to minimize pressure drop. Both of these devices sit in the dome of the reactor and do not take away any active space in the reactor from loading active catalyst.
JEFF JOHNS (Chevron USA, Inc.)
We have already invited you to come to the Principles & Practices session tomorrow morning. We have an hour set aside to continue the discussion. I appreciate the good responses from the panel. We hope to continue with more discussion and less advertisements.
SERGIO ROBLEDO (Haldor Topsoe, Inc.)
A properly designed catalyst system can go a long way in mitigating pressure drop issues. A key factor for designing a catalyst load is a properly designed graded bed. A fixed bed catalytic reactor can be graded in a number of ways, depending on the nature of the feedstock. We must differentiate between contaminants entrained in the feed as opposed to compounds, such as diolefins or metals-containing molecules in the feed that react upon entering the reactor environment and have the tendency to produce byproducts [polymer, Fe (iron), Ni (nickel), and V (vanadium) deposits]. In extreme cases, polymerization can manifest itself as a very hard crust which, in some cases, has to be jack-hammered out of the unit. Such agglomeration causes bypassing of catalyst and maldistribution in the catalyst bed.
In other cases, the material is very fine, in terms of particle size (5 to 10 microns); and although not forming a crust, it will also deposit in a small area, resulting in a reduced void fraction which causes the pressure drop across the catalyst bed to increase exponentially. Our experience, since Haldor Topsoe, Inc. invented grading in 1979, shows that the critical point is reached when the available bed void is reduced to approximately 20 to 25%. We therefore prefer to use what we term “useful bed void”. This means the fraction of the reactor void which is available for deposition or storage of contaminants before the critical limit where the pressure drop increases. Please refer to the following table:
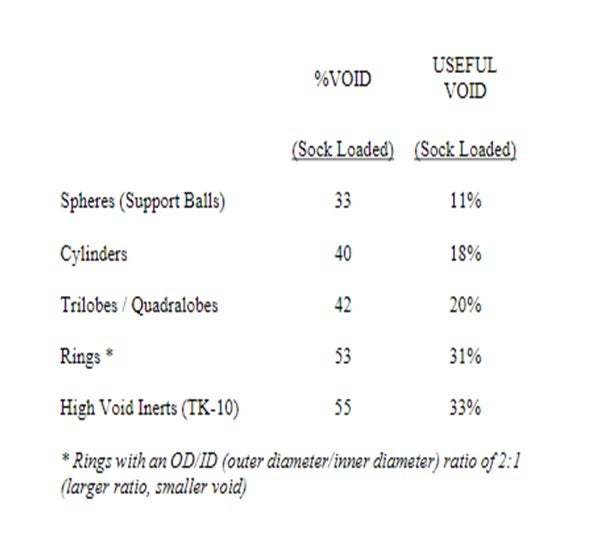
Inorganic material such as iron or polymers can quickly fill up the spaces between particles of a main bed catalyst effectively cementing them together, causing maldistribution and eventually crust formation with a resulting increase in pressure drop. The properly designed graded bed system can extend the cycle length of a main bed before pressure drop becomes an issue.
Fouling of a catalyst bed can be caused by a number of different factors or sequence of events in the refinery; however, in most cases, one of the most commonly encountered contaminants is iron. Organic iron can be present in refinery feedstocks; but more often than not, the iron originates from corrosion within the refinery itself. This is especially true for refineries using naphthenic-type crude. Processing these high TAN crude types accelerates corrosion in plant piping, tankage, etc., due to the presence of naphthenic acids. This iron can have a wide range of particle size distribution ranging from submicron up to large flakes.
When grading for iron, the graded bed system must be able to handle the iron in all its sizes Haldor Topsoe, Inc.’s shape-optimized TK-26 TopTrap™ is the successor of our very successful TK-25 TopTrap™. The optimized shape of TK-26 TopTrap™ provides an improvement in pickup capacity of 21%. TK-26 TopTrap™ is designed to load with an interstitial void of 61% and an additional 25% void in the pore system, for a total void volume greater than 85%. This gives TK-26 TopTrap™ the ability to trap not only larger quantities of deposits but also the ability to trap the smaller sized particulates. Larger-sized material deposits in the interstices between the individual particles. Fines or smaller-sized materials enter the TK-26 TopTrap™ pore system and are trapped within the structure of the particle itself. Not all grading is created equal, and it is not just a question of creating a high interstitial void fraction. Porosity and surface area are also important functionalities for graded bed material designed to trap particulate matter. Please note that the material trapped in the pore system of TK-26 TopTrap™ will not add to the pressure drop. This is the reason why TK-26 TopTrap™ is more effective in mitigating pressure drop issues than other ceramic trap materials in the marketplace.
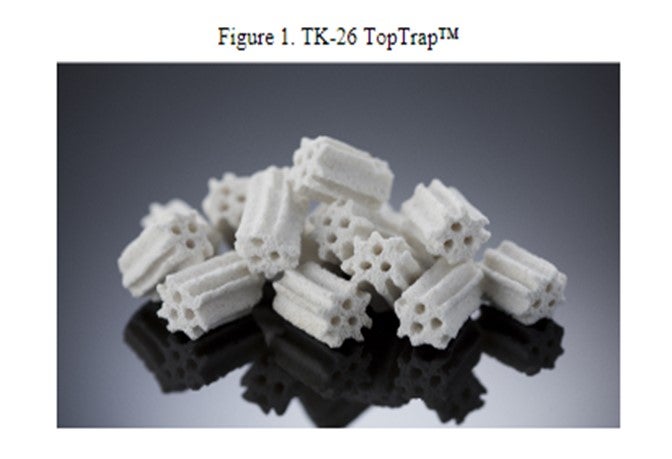
This specialty trap would be loaded right under the high-void, high-density topping layer, such as TK-10 or TK-15. TK-10 or TK-15 act as a hold-down, as well as storage space, for larger size inorganic material.
For units processing a high number of cracked stocks, a high quantity of olefins – which can cause large temperature rises in the reactor – need to be considered when designing a graded bed. In the presence of small amounts of oxygen, or at elevated temperatures above 450°F, these molecules will radically polymerize to form gum that can foul exchangers or reactors causing poor heat transfer, as well as high reactor pressure drop. If the feed blend contains coker naphtha, then we also need to consider the highly reactive diolefins compounds, which are severe coke precursors.
Cracked stocks should preferentially be sent directly from the upstream unit to the hydrotreater to prevent contamination with oxygen. Even straight-run stock that may be part of the feed component must be prevented from being contacted by oxygen by using nitrogen-blanketed storage tanks.
Even without oxygen ingress, the diolefins in the coker naphtha can polymerize at elevated temperatures. With high olefinic and/or cracked stocks, saturation will occur regardless of catalyst activity. However, an option does exist whereby the reaction front is spread out over a large volume, rather than at the top of the bed, or at the reactive interface between the inert topping and active catalyst.
This option is referred to as an “activity gradient”. We use a number of low- to medium-activity Raschig ring-shaped catalysts in 1/8” and 3/16” sizes on top of the main bed catalyst. Furthermore, high void inerts and rings have the advantage of improving the radial distribution and are also recommended to enhance distribution.
Haldor Topsoe, Inc. produces our 1/8” ring catalysts with a very large ID of the hole to allow for maximum feed contaminant capacity without sacrificing the crush strength. The ratio of the OD/ID for our 1/8” rings is 2:1. Furthermore, we manufacture all of our grading material to strict ISO (International Organization for Standardization) specifications from fresh raw material and not from scrap catalyst or regenerated catalyst, which may contain impurities from its prior use.
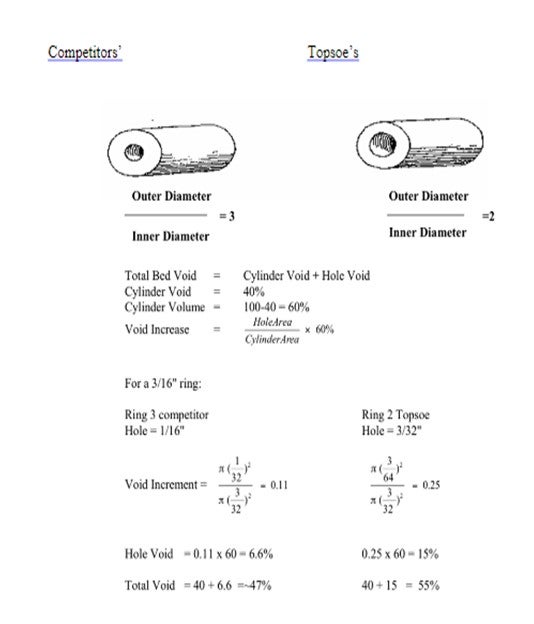
The particle size will definitely impact the SOR (start-of-run) pressure drop of the catalyst bed because each particle has an inherent interstitial void. For comparison, a 1/16” TL (trilobe) will have, on average, about an 80% lower SOR pressure drop than a 1/20” TL. This will have minimal to no impact on the SOR activity of the load but will allow for a larger window between SOR and EOR (end-of-run) pressure drop. This strategy can be further refined in reactors with multiple beds where a larger sized catalyst can be installed in the top bed where pressure drop is a concern, and a smaller sized (i.e., 1/20”) catalyst installed in the lower beds where pressure drop is less of an issue.
The same strategy is also true for loading method. On average, the SOR pressure drop of a dense loaded bed will be twice that of the same bed sock loaded. Therefore, sock loading can be considered when pressure drop is severely limiting cycle length and not activity. However, sock loading will mean that the activity will be about 15% lower than for a dense loaded bed. Again, the same method of titration can be employed in sock versus dense loaded portions of the catalyst bed. In multiple bed reactors, it is sometimes advisable to sock load the top bed and continue dense loading the lower beds. This will minimize the impact on the overall activity of the system but will improve the window for pressure drop build on the top bed where pressure drop is typically an issue. One point to keep in mind is that radial flow profiles in a bed may be impacted when changing to sock loading which could limit the cycle length due to peak operating temperature.
In units with severe pressure drop issues and where activity is not an issue, both a size change and loading method may be a viable solution. These two approaches – size and/or loading method – can also be employed in units with pressure drop issues in lower beds.
Scale Catchers
In addition to an effective graded-bed system, Haldor Topsoe, Inc. also recommends the use of our patented scale-catching trays, which are placed in the top of the reactor. The tray is installed above the tangent line to avoid reducing the catalyst volume. Haldor Topsoe, Inc. has designed scale-catching trays for both mixed-phase and 100% vapor-phase operation.
Clients have seen as much as a doubling of the cycle length after installing our scale catching trays, and we often find two to three inches of material deposited on the tray. This material would have fouled the catalyst bed without the presence of the scale catcher tray. This gas oil hydrotreating unit increased the cycle by 100% after installation of a Topsoe scale catcher.
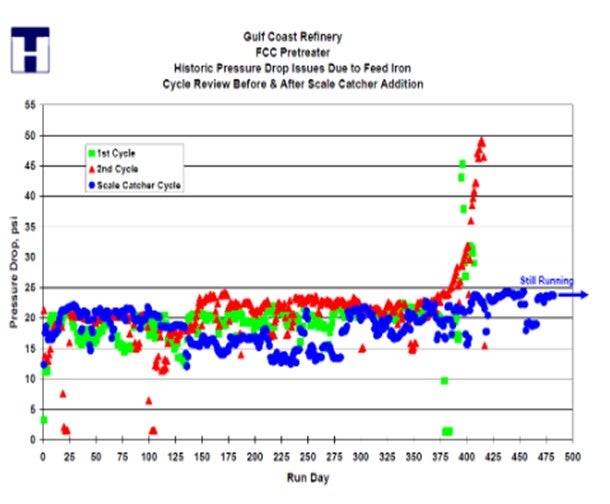
CHRIS STEVES (Norton Engineering)
All catalyst vendors provide hydroprocessing reactor grading design that can help to manage pressure drop during the catalyst cycle in order to keep reactor throughput as desired. It is important to understand the historical sources of pressure drop in the unit, though, so that the proper grading system can be chosen: a system that is designed to handle particulate contaminants may not work as well in a situation where the pressure drop is due to polymerization reactions. Samples from the top of the bed after every run should be used to confirm sources of pressure drop and then taken into account when designing the grading system.
DORIAN RAUSCHNING (Criterion Catalysts & Technologies)
Catalyst bed pressure drop growth mitigation can be achieved by integrating the results of empirical bed unloading observations, spent catalyst fines analysis, and subsequent design of a deep bed filter. While a multi-cycle iterative approach using trial and error can often result in the final development of a deep bed filter system, a more rapid resolution can be obtained by taking the time to gradually remove (vacuum) the top bed catalyst, visually observe the location and quantity of dust/fines/crust and collect intermittent spent catalyst/crust/dust/fines samples for chemical and particle size distribution analysis.
Based on the combined observations and analytical results, a deep-bed filter can be developed which utilizes void fraction grading of specialized grading materials and catalysts that facilitate selective trapping of different sized feed particulates, gums, and/or soluble metal naphthenates. A large diameter and intersticial void catalyst layer is first used to remove large-sized feed particulates while simultaneously still providing sufficient void space to permit the medium/small-sized particulate to penetrate deeper into the reactor and not form a high-density crust. Subsequent ever-smaller diameter and intersticial void fraction grading or catalyst layers are then used to promote further selective feed particulate removal until the primary conversion catalyst is reached. These layers are all sock loaded. The net effect of such deep-bed filters is that the feed particulate is distributed over a greater depth of reactor volume and do not form immediate, high density, narrow layers that restrict feed or treat gas flows.
The deep bed filter should also provide an activity gradient to mitigate the formation of adhesive gums that can form from olefinic polymerization reactions. Feed unsaturates can react to combine longer chain polymers which can act as gums and form coke that bridges catalyst pellets. In addition, these gums interact with feed particulates causing rapid pressure drop growth. To mitigate these reactions, the deep bed filter should be graded for activity as well. The bed’s upper layers should have lower activity catalysts to slow down the rate of polymerization and promote hydrogenation. The deep bed filter’s subsequent catalyst layers’ activity begins to increase as the concentration of polymer-forming compounds decreases.
Criterion’s OptiTrap™ product line is designed to provide a wide range of top-bed grading catalyst products from which a deep-bed filter can be constructed. OptiTrap™ products offer selective particulate removal in combination with an activity gradient. In addition, Criterion has extensive troubleshooting experience in resolving reactor pressure drop growth issues in naphtha, distillate, FCC PT, and hydrocracking applications. Criterion also offers a full range of research and analytical support.