Question 33: What is the philosophy or criteria for optimizing catalyst bed grading material to prevent high reactor pressure drop from feed containing significant amounts of Fe (iron)?
LIOLIOS (DuPont Clean Technologies)
Certainly, identifying the sources of the iron coming in – whether organic, iron oxides, iron sulfides, or just scale from tanks – is very critical to understanding your best strategy for mitigating pressure drop. Ultimately, when you form iron sulfide, it creates deposits on the bed and coke deposition, and certainly leads to reduced catalyst life.
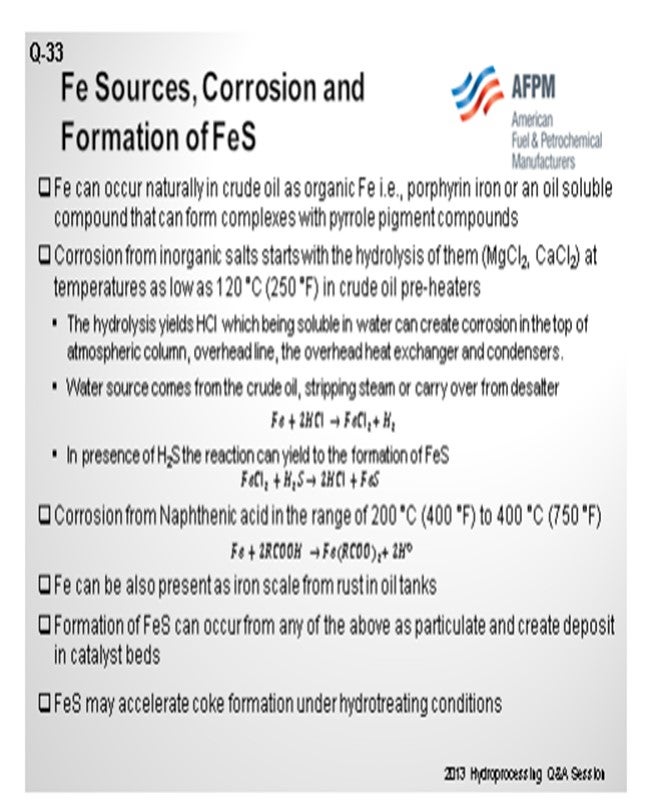
The next slide shows the analysis of the scale that was collected from a guard bed in a VGO hydrotreater. The graph on the left is the first pass on the analyzed scale. About 40% of it was under 25 micron. The analysts took that same sample and re-circulated it. I cannot get into it, but basically 80% of the sample after recirculation was under 25 microns. Also, the small particles will come into your bed under hydrotreating conditions. They will grow and increase in pressure drop, and they will take off on you. Understanding why iron sulfide is coming in and how it is coming in is very important to setting up a strategy, which is shown on the next slide. So, identifying the root cause is important.
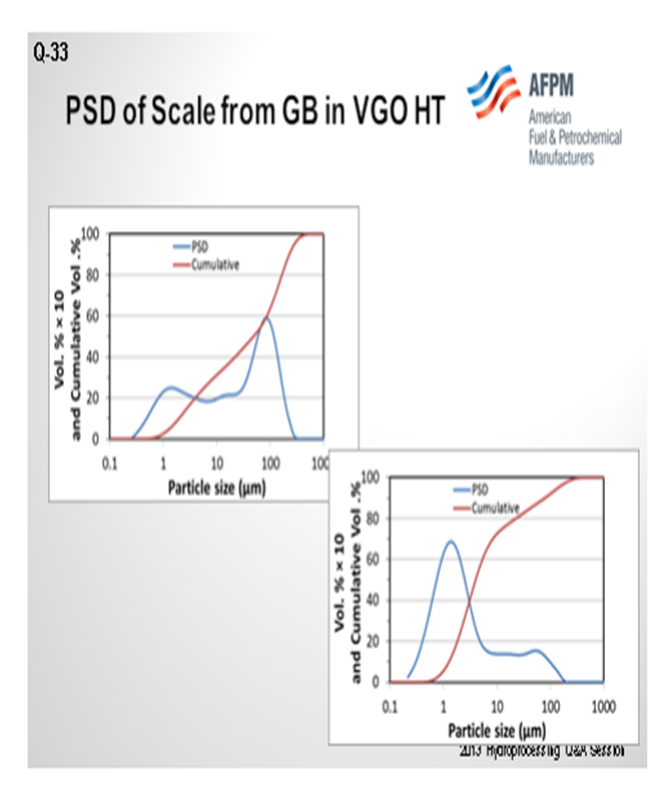
The first phase of the reduction strategy should be feed filtration. Either cartridge or backwash-type filters are most commonly used down to about a 25-micron size. Next, look at size grading, which is a high-void area, in order to capture this material in the void area. Crystaphase CatTrap® or other specialized topping materials are very effective at capturing some of these iron materials then some active grading because some of the iron content will actually form iron sulfide at these conditions. So, after the active grading, you will need additional trapping material with large pore structures in order to capture the iron.
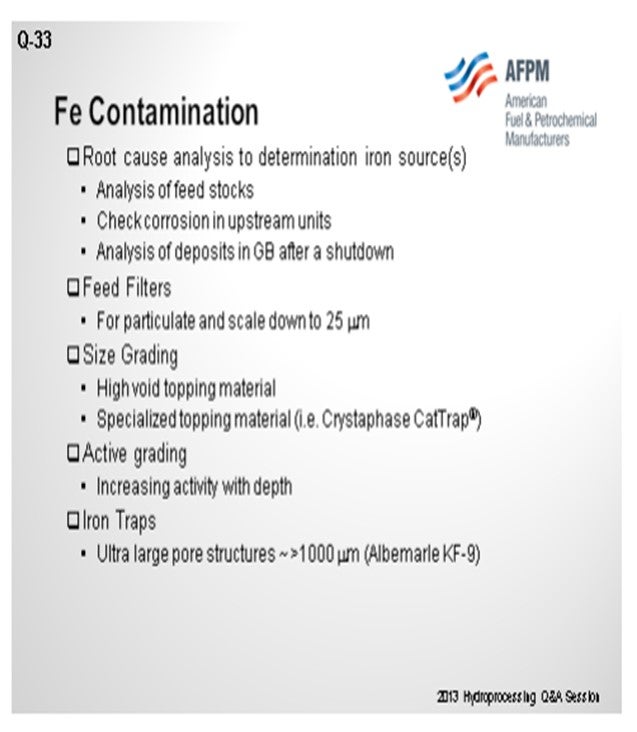
WATKINS [Advanced Refining Technologies (ART)]
I basically agree with a lot of what Glenn just said. The goal is to identify the origin of your iron and determine if there is a way to handle or stop it. If it is corrosion, we can certainly take care of it elsewhere. Characterization is the key. The bottom three pictures on the slide simply show iron and how it is sitting in the reactor or on various places in exchangers or furnaces or on the catalyst. Some can be filtered out; for others, you must use a catalytic mechanism. The one on the left is absorbed iron on catalyst.
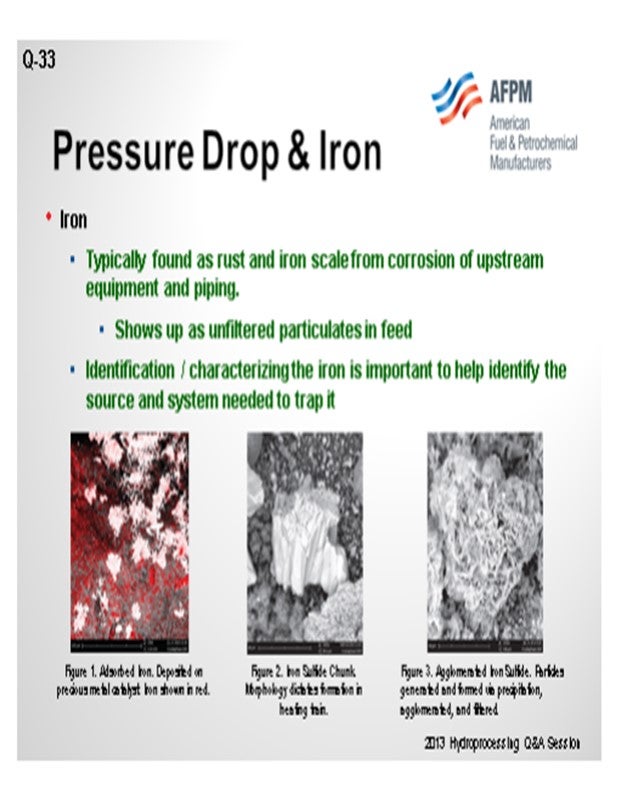
Again, 25 microns is the target range for iron-particulate scale and other contaminates that are going to come into the hydrotreater using a grated bed system to mitigate any pressure drop. The goal is to dramatically increase the actual void fraction so you have somewhere to put this incoming iron. Top-bed materials with high internal void space are important. Sock loading: If you know that a prior cycle had a problem, the goal next time may be to change the diameter of your catalysts. Sock-load a portion of the bed so that you have some space, and do not shut down on pressure drop. If you have enough void space in your reactor, the contaminates can sometimes actually pass through. This will not really be a problem in your catalyst beds if you have too much void space.
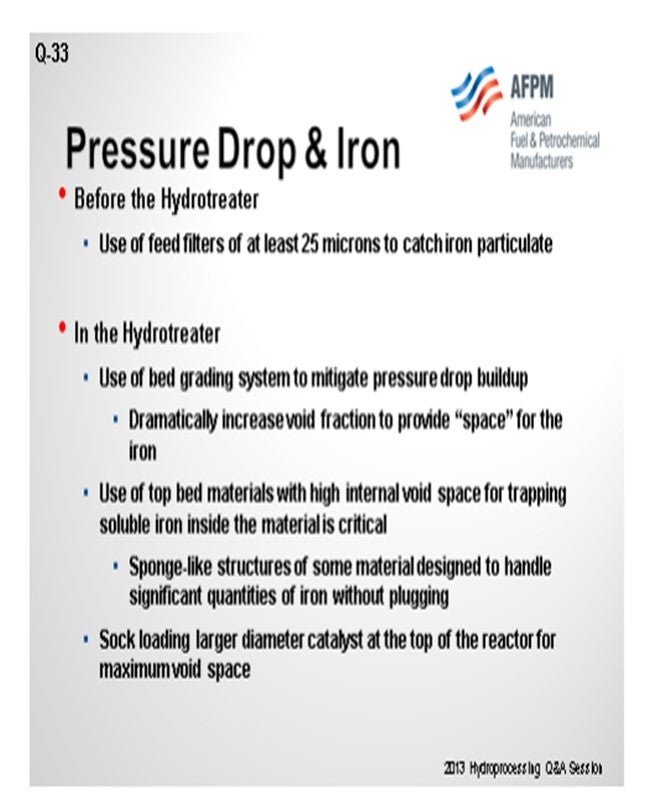
The third slide shows an example you may have already seen. On the top left is a Crystaphase disk, which we can see has a very large void space. You can actually fill up quite a bit of that with iron and other particulates. A similar example is using a ring molecule at the bottom comparing fresh and spent samples so you can pick up coke, iron, and other contaminates. So, it is all about creating a void space.
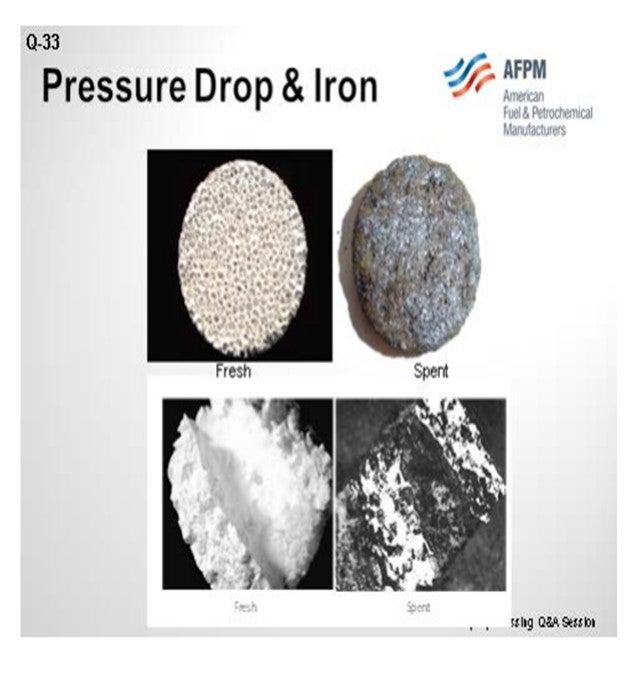
MUKESH PATEL (Reliance Industries Ltd.)
What is understood from some literature is that soluble and insoluble Fe, of course by filter and cat (catalytic) trap, can capture the particles and also that some of the iron is emitted by heightened crude processing. Is there any temperature correlation for Fe falling?
SALVATORE TORRISI, JR. (Criterion Catalysts & Technologies)
I think the answer is: Yes, there is a temperature correlation. In general, when you have organic iron, as soon as it sees an H2S environment, it will start to recreate the iron sulfide. Typically, many of the hydrotreaters do not have H2S coming in until you first begin to desulfurize. It is very important to activity-grade to generate H2S in very small quantities as a start so that you do not deposit all of your iron at once. You tend to want to go through a very long activity grading, as well as a size grading on top of the activity, to try to disperse and deposit that iron in a large amount of pore volume. Of course, there is a temperature component to that, but perhaps the more important component is controlling the activity during that deposition.
I have a follow-up from the first question about arsenic. Mukesh, I think you asked that as well. I received a question for the panel after that about whether it is possible to put in a scavenger. You can soak up arsenic, which is the scavenger. That, of course, takes up space, but maybe not necessarily activity. Over the years, we have begun to put include multiple functionalities. You are not only picking up arsenic, but you also lose activity with arsenic because it will kill your ∆T. If you have a unit that is ∆T-limited, particularly at end-of-run, you become furnace-limited. I think the industry has begun to develop more catalysts, as opposed to traps, in an effort to accommodate the arsenic and compress it into as small a space as possible. That is a late response to Question 1.
Back to the panelists: More along the lines of Questions 1, 2, and 3. When you have multiple contaminants together, what is your philosophy on how to handle it? I do not think you have nickel, arsenic, or iron just by themselves. Does anyone want to comment on handling trapping systems? It seems to be a relevant enough topic to have made the top three questions about when you get into multiple contaminants.
WATKINS [Advanced Refining Technologies (ART)]
Generally, it will be dependent on the type of service: a gas oil hydrotreater, FCC pre-treat, or hydrocracker pre-treat, for example. Your major contaminants are nickel plus vanadium, so you will start putting more demet-related products at the top of your reactor. The convenience of using an HDM guard catalyst is that it generally contains nickel, so you do get that combined benefit of picking up arsenic plus a little nickel and vanadium (Ni+V). If your process has more arsenic than Ni+V, you will generally work on your larger molecules first because you need space to put contaminates. If you put in guard material that is designed for arsenic and naphtha up at the top, it will get plugged-up rather quickly with nickel, vanadium, and contaminates like that.
In diesel hydrotreating, the use of guard material really depends on the concentration of your limiting factor. Most of the time, it will be silica, arsenic, or maybe phosphorus. We often have a combined trap, which really is defined by your concentration. We are not worrying about nickel or vanadium in diesel and naphtha products.
GLENN LIOLIOS (DuPont Clean Technologies)
Literature shows that a mixed iron sulfide and coke deposits are common in higher temperature equipment which processes sour crudes and its processed components1. Hence, more information may be obtained from the 2011 study by Wang and Watkinson who determined that iron sulfide and coke formation were the two main culprits of fouling in HP catalyst beds. Catalyst bed grading targets the capture of particles, iron scale, and other contaminants that may cause fouling. Use of proper guard catalysts that can capture iron should be part of the solution supplementing catalyst bed grading. A more detailed explanation may be found below.
Preventing reactor pressure drop with feeds containing significant amounts of Fe typically involves a multi-faceted strategy including feed filters, bed grading, and the use of iron traps. Depending on the form of the iron (organic, iron oxide, or iron sulfide, etc.), it may also include a strategy for converting the iron to the form most readily trapped. Iron present as iron sulfide (FeS) in the feedstock, due to corrosion in upstream units, may be too small to be trapped in feed filters. To this end, guard bed material with ultra large pore structure iron traps can be used to trap iron sulfide inside the guard element. If the iron is particulate in nature, the particle size distribution will also impact the strategy.
Postmortem analysis of a hydrotreater scale includes a particle size distribution (PSD) analysis as one of the multiple tools used to troubleshoot iron contamination. In the diagram shown in Figure 1, at least 30% of the scale was FeS in nature from chemical analyses. The initial PSD plot shows multimodal particles centered at about 2 µm (micrograms), 20 µm, and 80 µm with bigger particulates being agglomerates of smaller ones. On this initial plot, one can also notice that particles under 25 µm account for 40% of the total. However, upon recirculation to allow some of the agglomerates to breakdown in primary particles, the most predominant particle size is around 2 µm with some particles up to 150 µm. In this case, particles under 25 µm account for more than 80% of the total particles. This is a very simplified analysis but shows the complexity of the problem to address not only the nature of the particles, but also their size distribution.
Feed filters, cartridge, or backwash type are usually used as initial mitigation for iron scale down to 25 µm particulates. Then size grading, along with activity grading, is used to mitigate iron source foulants depending on their type. It is also advisable that refiners identify the source of the iron and consider root cause analysis to potentially eliminate that source. For example, if the iron is a result of serious upstream corrosion, this may be managed through corrosion mitigation measures. However, if iron is naturally present in the feed (such as in naphthenic crudes), a combination of guard grading, shape, and activity is to be taken into consideration for mitigation of pressure drop strategy. In short, a combination of feed filters, graded size, and active material with iron traps can mitigate the onset of a rapid pressure drop increase; however, it should be tailored taking into account the nature and/origin of the iron contamination in the hydrotreater feedstock.
Finally, in situations when iron deposits have accumulated and resulted in significant pressure drop, the use of iron dispersants (such as provided by Baker Hughes) has resulted in varying degrees of success in partially mitigating the problem.
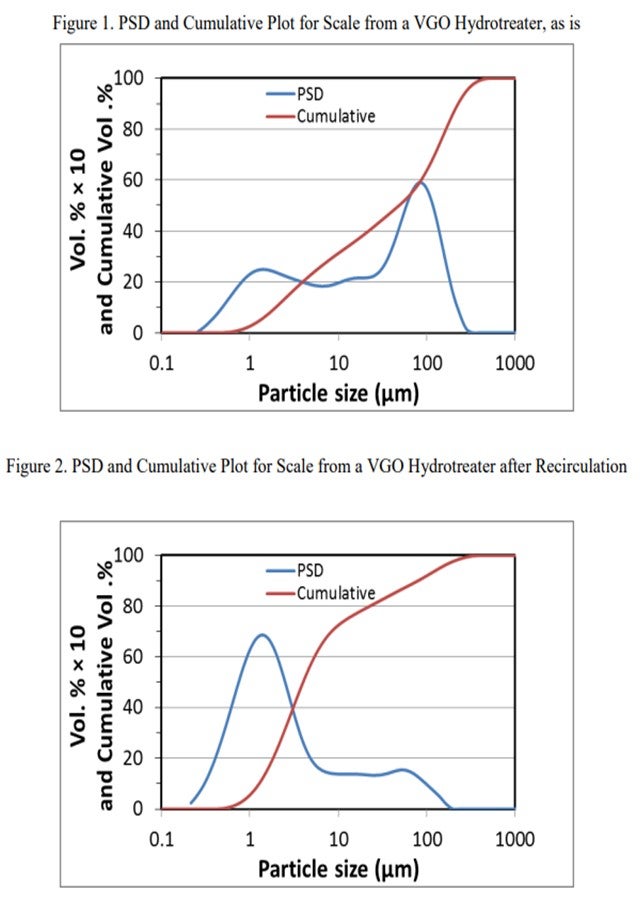
BRIAN WATKINS [Advanced Refining Technologies (ART)]
Iron works its way into hydrotreater feed as rust and iron scale from corrosion of upstream equipment and piping, as well as unfiltered particulates present in the feed. Iron naphthenates can form from piping corrosion due to naphthenic acid in the feed, and the iron readily precipitates out in the presence of heat and H2S. These iron particulates fill the interstitial spaces in the catalyst bed which will result in a higher than expected pressure drop. To help mitigate the pressure drop associated with iron, ART uses a series of grading materials which have high void space to accumulate and ‘store’ these particulates. Use of a specialized iron trapping material (GSK-9)
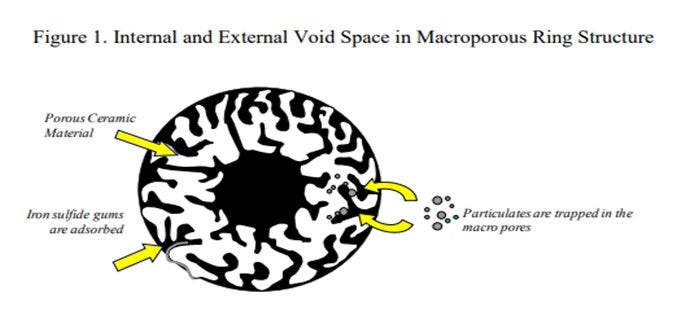
If iron is known to be the cause of the pressure drop issues, then changes to larger diameter catalysts can also be used in an effort to allow for additional void space in the reactor. Sock loading a large portion of the top of the reactor will also greatly increase the effective void space allowing the smaller iron particles to move through the reactor.
Another option is to use materials that are specially designed to dramatically increase the void fraction in the top bed of the reactor and which are very good at trapping iron, as well as using other particulates and scale. These measures are helpful for delaying pressure drop buildup, but they do not prevent eventual pressure drop buildup. Effective feed filtration to remove particulates (at least 25 microns) provides a longer lasting solution in helping mitigate pressure drop buildup from these sources, as well as providing a way to identify the sources of iron that are present in the process.
CHRIS CLAESEN (Nalco Champion Energy Services)
With regard to the Fe content of the feed, you can often control it by looking at the upstream process. Possible treatments are iron removal in the desalter and corrosion inhibitors for the upstream equipment or the installation of feed filters. In some cases, the catalyst bed pressure can be reduced with a reactor bed cleaner.
SERGIO ROBLEDO (Haldor Topsøe, Inc.)
Fouling of a catalyst bed can be caused by a number of different factors or sequences of event in the refinery; however, in most cases, one of the most commonly encountered contaminants is iron. Organic iron can be present in refinery feedstocks; but more often than not, the iron originates from corrosion within the refinery itself. This is especially true for refineries using naphthenic type crudes. Processing these high TAN (total acid number) crude types accelerates corrosion in plant piping, tankage, etc., due to the presence of naphthenic acids. This iron can have a wide range of particle size distribution ranging from sub-micron up to flakes or lumps that can be one-quarter to one-half inch, or even larger.
When grading for iron, the graded bed must be able to handle the iron in all of its size possibilities. Haldor Topsøe’s TK-25 TopTrap™ is designed to load with an interstitial void of 61% and holds an additional 25% void in the pore system, for a total void volume greater than 85%. This gives TK-25 TopTrap™ the ability to trap not only larger quantities of deposits, but also the ability to trap the smaller particles of less than 10 micron size. Larger-sized material deposits in the interstices between the individual quadralobes. Fines or smaller-sized materials enter the TK-25 TopTrap™ pore system and are trapped within the structure of the particle itself. Not all grading is created equal, and it is not just a question of creating a high interstitial void fraction. Porosity and surface area are very important functionalities for graded bed material for FeS, as well as other inorganic or organic contaminants. TK-25TopTrap™ has proven to be very effective for trapping the small micron-sized inorganic contaminants in the pore size, thus, minimizing the buildup.
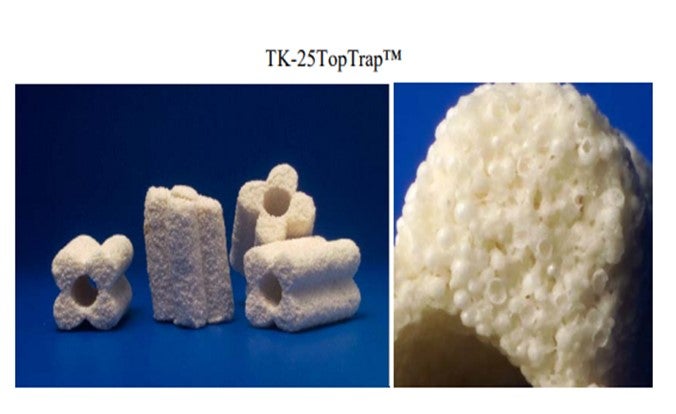
This specialty trap would be loaded right under the high-void, high-density topping layer, such as TK-10 or TK-15. This is because when grading for iron, the objective is to keep the material near the top of the vessel where you have the highest amount of void. If iron migrates through the graded bed and gets to the main bed catalyst, it will hit the pinch point where interstitial void is at its lowest. This would then result in the pressure drop building quickly.
AUSTIN SCHNEIDER (Crystaphase Products, Inc.)
Iron is a ubiquitous foulant across all refining service types and is commonly the primary element involved in compound formation, which causes pressure drop. Delta P issues caused by iron tend to persist even after heating train lines have been pigged and upstream feed filter elements have been put in place. Although iron contamination comes in many forms, including both solids and solutes, when considering pressure drop, iron contamination should primarily be examined as a solid. In this form, it is most commonly encountered as the compound iron sulfide.
Upstream feed filters remove a very large portion of solids moving into the heating train and reactor system. A common action taken to reduce reactor fouling is to implement a filter with a tighter mesh, increasing the particle size range it can capture. This usually results in more frequent filter changes/washes, which operators do not enjoy doing at increasing intervals, with the end result being that the fouling rate is rarely impacted.
Pigging removes any residual iron sulfide crust that may have formed during the previous cycle. While this procedure removes fouling buildup and improves the fluid characteristics and heat transfer capabilities across the heating train, it does not do much to change the fouling rate. In fact, pigging can serve to increase fouling generation initially as removing the corrosion products from the inner piping exposes fresh steel to corrosion pathways.
Although necessary, neither of these proactive maintenance processes serve to keep dissolved iron from passing through the feed filters, nor do they prevent corrosion reactions from occurring on the hot skin surfaces of the heat exchanger or furnace tubes.
Much of the dissolved iron will contribute to catalyst deactivation, and there are catalysts in the industry specifically designed to trap these types of organometallics to protect the main bed catalyst. An example of this is shown in Figure 1, which is a SEM (scanning electron microscopy) image of a precious metal catalyst extrudate that has been poisoned by incoming iron contamination, which is identified in red. This limits the catalyst life but has little effect on the pressure drop.
Solid iron typically takes the form of iron sulfide as it enters the reactor via feed filter bypass, scale/corrosion generation in the heating train (Figure 2), or in-situ particle precipitation followed by agglomeration (Figure 3). Assuming the feed filters are run responsibly and continually, we can focus on the latter two: corrosion and precipitation. This is the material responsible for crust formation in the catalyst bed or ring grading layers, resulting in pressure drop.
Incoming iron of this nature is a direct result of energy input on the way to the reactor driving the reactions for corrosion and precipitation. The only option left for the engineer is to deal with the filtration issue raised by iron sulfide generation and to work with top bed technology suppliers to improve the filtration capabilities of the reactor. The volume for particle storage should be increased to improve the resistance to pressure drop. There are materials available that can greatly expand the reactor’s filtration capacity while minimizing the ∆P. These materials work in a uniquely different manner than standard grading and are able to filter without forming a pressure drop. They are differentiated by their sponge-like structure made up of individualized elements. These types of systems can be designed to handle the equivalent volume of several crust layers.
Additionally, characterizing the foulant is also of high value. It can help identify the source of the foulant and the type of filtration or catalyst system needed to trap the iron. Tools to help with characterization include Total Suspended Solids, Particle Size Analysis, Digital and Electron Microscopy (SEM, which is shown below), and some form of elemental analysis. Engineers should consider using all of these tools to separate iron foulant from catalyst fines and other significant particle sources to resolve problems both inside and outside of the reactor.
PAUL CECCATO (Criterion Catalysts & Technologies)
Iron is introduced to a reactor as either solid particulates from scaling or soluble iron from corrosion, which precipitates as solid iron sulfide in the presence hydrogen sulfide. In both cases, a reactor bed grading system distributes the particulates over a volume of catalyst to prevent surface caking and a rapid pressure drop increase upon restriction of the hydraulic channel. Installing layers of grading materials from high void fraction to lower void fraction above the main catalyst bed creates the desired distribution and filtering effect.
For solid iron particulates, large-shaped materials are utilized at the top of the grading package to prevent accumulation and crusting at the inlet of the reactor. For soluble iron, adjusting the activity of the grading materials from very low at the top of the bed to moderate above the main catalyst slows the generation of hydrogen sulfide to allow precipitation of iron sulfide over the full depth of the grading materials. To assist with control over iron sulfide precipitation, Criterion manufactures OptiTrap[MacroRing] 8.0 mm hollow cylinders. The mild activity and macro sized pores of the OptiTrap[MacroRing] allow for precipitation and retention within the substrate for an overall increase in iron capacity of the grading system.