Question 33: Phosphorus-based chemicals are used to neutralize naphthenic acids. Drilling and completion fluids also can contain phosphorus, so it may be in crude oil. What are your Best Practices to protect active hydrotreating catalyst from phosphorus poisoning?
MORELAND (Valero Energy Corporation)
I am going to give a little background on phosphorous poisoning and then share one specific example we have seen in one of our refinery units. First of all, phosphorus is a strong catalyst poison. In our course materials, we say that 1% phosphorous on catalyst will reduce the activity by 50%. So, it is a significant poison. There have been examples of up to 3% phosphorous completely destroying the exotherm from a bed going down to almost nil. The deactivation mechanism is pore mouth plugging through surface deposition similar to nickel or vanadium. The common sources are crudes, drilling fluids, phosphorous-based corrosion inhibitors, and flow improvers. In particular, we have had more and more experience with phosphorous-based corrosion inhibitors, and the example I am going to discuss deals with that.
We have seen, in this example, the spent catalyst from the skim indicated up to 20% phosphorous on top-bed grading; so, significant amounts of phosphorous. And in this cycle, after seeing the exotherm decline, when we reloaded, we switched from the phosphorous-based naphthenic acid corrosion inhibitor to a sulfur-based inhibitor and saw the DT (differential temperature) decline halt or be held.
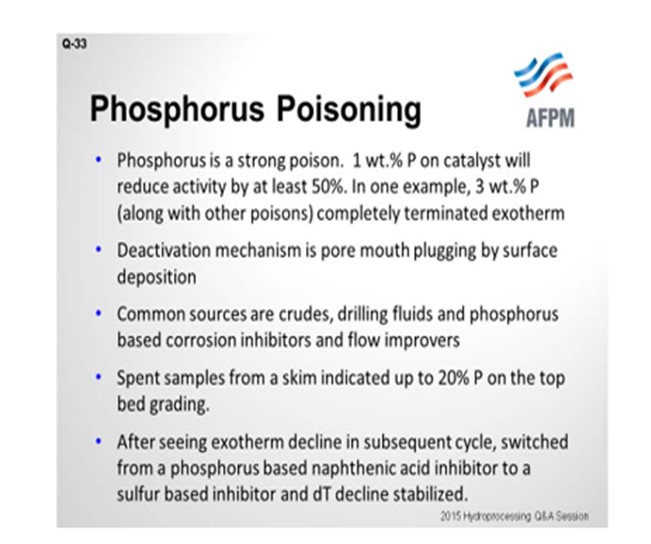
On the next slide is an example of the first cycle. The unit in question contains two reactors in series with two beds each; so the beds are delineated as Bed 1, Bed 2, Bed 3, and Bed 4. You can see that through the beginning of the 2013 cycle, the ΔTs (delta Ts; DTs; temperature differentials) were stable. The y-axis shows how the total temperature rise is distributed amongst the four beds. The vertical pink line marks the time when the phosphorous-based corrosion inhibitor was started. You can see that Bed 1’s temperature rise starts to decline. We actually tried to increase inlet temperatures to recover the ΔT, but it was not successful; the ΔT continued to decline. And as you would expect from plug flow and metals deposition, Bed 1 declines and Bed 2, which is the blue line, picks up the ΔT as it begins to decline. Bed 2 is the green. Bed 3 picks it up in the blue. And finally, when Bed 3 starts to decline, Bed 4 picks it up. We ended up changing the catalyst out in the cycle ahead of schedule.
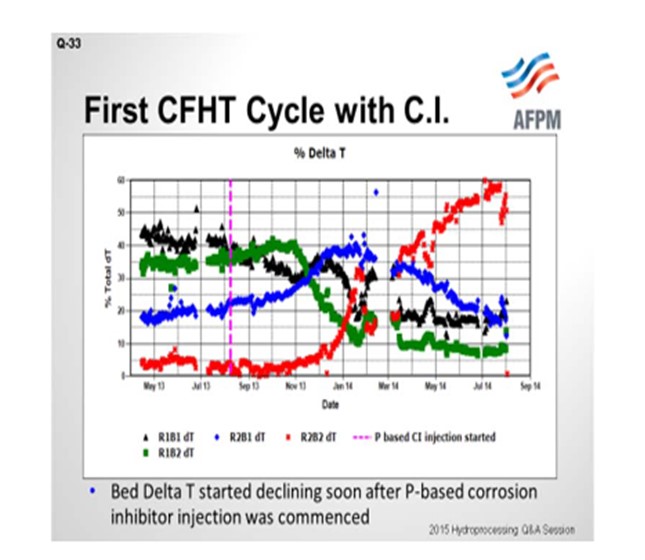
So when the catalyst samples were pulled out from the spent catalyst load, you can see that the Bed 1 samples were exceeding 20% phosphorous. If our threshold is 1% phosphorous or a 50% activity decline, even Bed 2 was above that and showed significant activity decline. We did have lower levels of phosphorous in Beds 3 and 4, and that is where the bulk of the HDS catalyst was located.
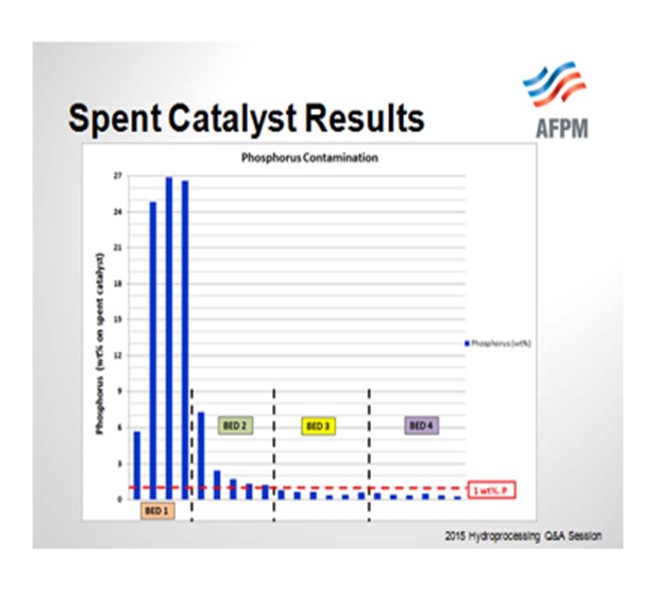
For the next cycle that started up after this, you can see the temperature rise response in the four beds, Bed 1, Bed 2, Bed 3, and Bed 4. The ΔT decline continued. You may ask, “Oh, did you guys at Valero not learn anything?” This delay at the start of cycle is the time it took us to get the spent catalyst sample results. When we unload the catalyst and send it to our supplier, we do not get those results back for several months. So it reinforces that having good technical service and timely return of spent catalyst samples can really help us make a change. As soon as we saw the high levels of phosphorous, we had a discussion and the refinery switched to a sulfur-based corrosion inhibitor. We worked with our chemical supplier. You can see that when we switched to that sulfur-based corrosion inhibitor, the ΔT stabilized. There was still some decline, as you would expect from metals poisoning throughout. However, the rapid decline that we observed in the previous cycle was not repeated.
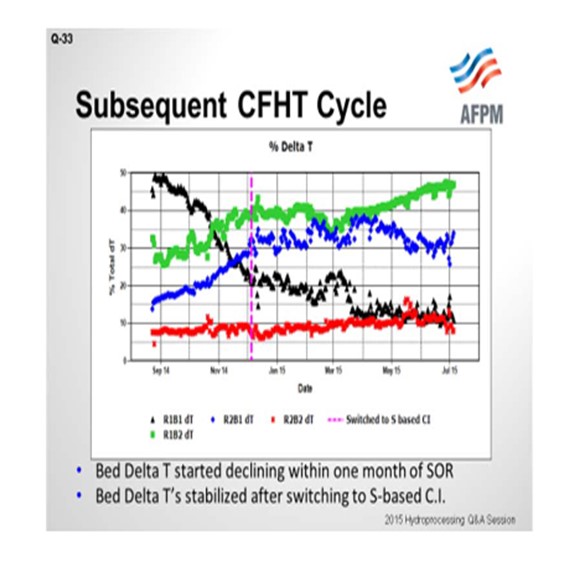
So in summary, our Best Practice for phosphorous poisoning is to minimize the source of phosphorous poisoning. We do still use phosphorous-based corrosion inhibitors. They are very effective for naphthenic acid corrosion inhibition. However, it has to be an economic justification between the use for protecting the VGO (vacuum gas oil) circuits and any deactivation that may occur in a VGO hydroprocessing unit. There are demetallization catalysts that would be used for nickel and vanadium; they are also effective for trapping phosphorous. But still, a small amount of phosphorus goes a long way in terms of catalyst deactivation.
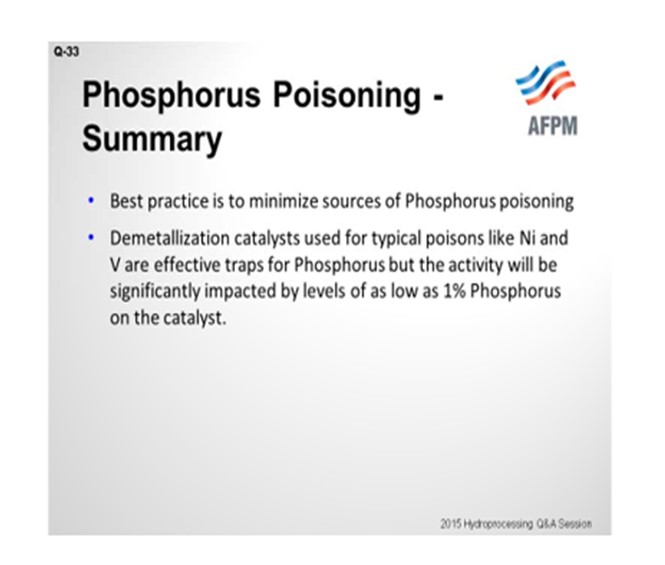
TEMME (Albemarle Corporation)
I agree with what Andy said. That is a really powerful example. Phosphorous is definitely becoming more problematic, especially with high TAN (total acid number) crude treatment programs. Andy has already mentioned the sources.
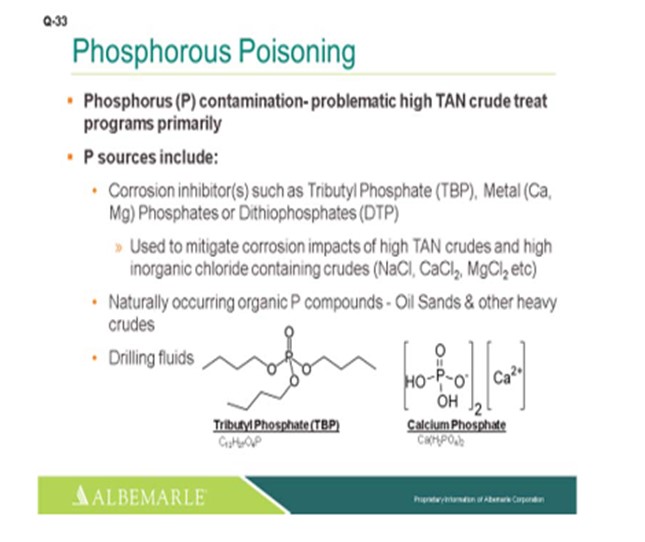
Phosphorous will cause pore mouth plugging leading to diffusion limitations. The mechanism is more pronounced with high temperature/high-pressure operations. And with that, the pore mouth plugging will have a greater impact on small pore size, smaller median pore distribution-sized catalysts. We have seen that phosphorous deposition of 2 wt% can result in a 50% loss of catalyst activity.
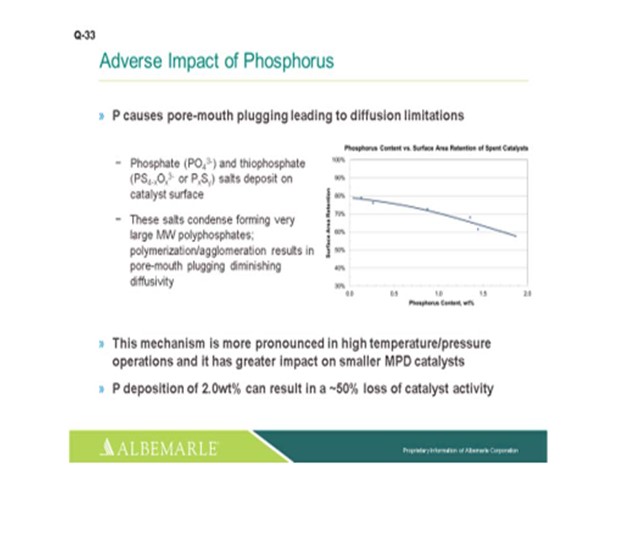
In terms of assessing and dealing with phosphorous trapping, as Andy indicated, getting good spent catalyst samples are essential for assessment. There are catalyst-handling companies that have core sample machines which work very well for getting a good axial core bed sample. Instead of having to try and vacuum off or pick samples out of flow bins, we want to make sure to get enough samples to define the extent of the problem. It does not hurt to get some third-party testing done, especially if they can do it in a quicker turnaround and get a baseline of the phosphorous and the catalyst substrate from the vendor to ensure that you have good accounting. And yes, phosphates can be removed using guard catalysts. They are designed for iron, nickel, and vanadium pickup, especially catalysts with the pore architecture that will minimize pore mouth plugging. We feel that catalysts with minimal diffusion limitations will deal best with phosphorous trapping.
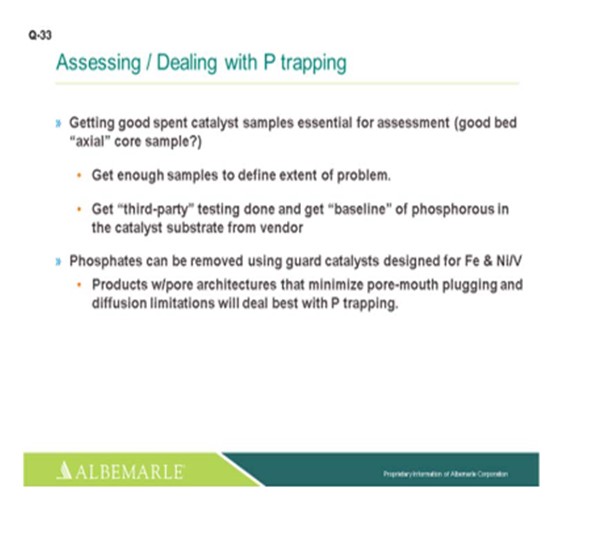
PEDERSEN (UOP LLC, A Honeywell Company)
I will add that it is important not only to identify the concentration of phosphorus contaminant, but also the type of material with which this phosphorus is associated. Basically, the more acidic the phosphorus compound, the more lethal it is to your catalyst.
JEFF JOHNS (Chevron USA, Inc.)
I am curious about comments from the panel about protection from phosphorus in crude. Is there is any monitoring program or other procedures you have instituted to be able to prevent that poisoning? As an example, just so people are aware that that is a real problem, we had a diesel hydrotreater that completely went through a cycle in about six weeks due to phosphorus from crude poisoning. So, what have you done?
McARTHUR (Phillips 66)
I will say that we do not have a unit that has really had a significant phosphorus poisoning problem yet. So I do not think we have installed what I would call a top-of-the-line phosphorus monitoring program.
MORELAND (Valero Energy Corporation) All I want to say, Jeff, is that we would have been caught by something like that, too. We do not typically monitor for phosphorus in diesel streams. We have seen some phosphorus in some kerosene (kero) streams at one of our plants and some phosphorus-based fouling in the crude tower in the kero circuit. So maybe it is a similar case, but it did not seem to affect operations. In that refinery, the jet is not hydrotreated; so we would not have seen it in the hydrotreater. We have monitored it in VGO; but in diesel, we do not look for phosphorus very often.
NAGASHYAM APPALLA (Reliance Industries Limited) I have two specific questions. First, is there any industry-wide accepted limit of phosphorus in the gas oil stream going to the hydrotreater? Does anyone monitor this, and is there any permissible limit for the phosphorus levels? Secondly, in the presentation, it was mentioned that the customer switched from phosphorus-based chemistry to sulfur-based chemistry. Phosphorus-based chemistry is known to provide a better protection against the attack of naphthenic acid attack by forming a more stable Fe-S-P scale. Only sulfur-based inhibitors are not found to provide that level of protection. Also, as per experimental studies, the sulfur-based inhibitors need to be dosed in a higher proportion than the phosphorus-based to get the same level of protection. So, my question is: How did the customer ensure the same level of protection against corrosion from the naphthenic acid by switching to sulfur-based chemistry?
MORELAND (Valero Energy Corporation) I can answer the second question; I do not know about the first one. So in answer to the second part, we understood that switching to the sulfur-based inhibitor would be less effective for protecting against naphthenic acid corrosion. So the higher dosing went into the economic equation of how much high TAN crude we process at this particular facility. We have two different plants at which we are using the phosphorus-based corrosion inhibitor. One stayed with it and even dealt with the penalty on the hydrotreater downstream. The other, the example I showed, switched away from the phosphorus-based to the sulfur-based and then reduced the runs of high TAN crudes. As far as acceptable levels, I do not really have a number.
McARTHUR (Phillips 66)
The only time we review feedstock for phosphorus is if we have an opportunity feedstock come in, and then we would be looking for elevated phosphorus levels. We would steer away from something that had any appreciable amount of phosphorus, but I do not the number off the top of my head.
JAMES PROROK (Husky Energy Inc.)
About fouling in the crude tower, at the Lima Refinery, we experienced that phosphorus fouling there in a light gas oil cooler. We also experienced it then in the “water white” kerosene cooler – another air cooler – that basically plugged up with the same material, which shortened the life of the diesel hydrotreater catalyst.
MORELAND (Valero Energy Corporation)
We saw it in deposits in the crude tower. I do not know if we knew it ahead of time; because when we analyzed those deposits, that is when we saw phosphorus in those deposits. Is that a similar experience?
JAMES PROROK (Husky Energy Inc.)
After the pressure dropped in the kerosene section of the crude tower, we then got a sample where we could. We got a sample of the solids that were caught in a strainer on a pump, had them analyzed, and found out that there was phosphorus in that circuit. Then, we saw phosphorus in the heat exchangers downstream of that, on the way to the DHT (distillate hydrotreater).
MAUREEN PRICE (Fluor Corporation)
There is a question on this in the Crude Q&A tomorrow morning that covers phosphorous deposits in the crude unit equipment that may provide additional insight.
SALVATORE TORRISI, JR. (Criterion Catalysts & Technologies)
The panel talked about solids in the crude tower, and the focus of the question was activity on the catalyst. Can anyone on the panel comment about any impacts on pressure drop related to phosphorus?
McARTHUR (Phillips 66)
I do not have any experience with it, but my understanding is that there will be a pressure drop problem with phosphorus fouling on a catalyst, especially if you have a very low void space area where it is collecting. But again, we have not had that problem yet.
SALVATORE TORRISI, JR. (Criterion Catalysts & Technologies)
The experience I have seen has been more with regard to accelerated fouling in the feed preheat exchangers rather than in the catalyst bed itself.
MORELAND (Valero Energy Corporation)
Sal, you are probably as familiar with the unit as I am, so all I will add is that when you lose the activity this fast from phosphorus, the time onstream is not sufficient for development of a significant pressure drop issue. However, we have seen pressure drop start to increase. We ended up doing reactor skims before it really became a run limiter.
SALVATORE TORRISI, JR. (Criterion Catalysts & Technologies)
Okay, thanks. I was wondering about that because what happens is you use a corrosion inhibitor to neutralize the acids; and if you are not consistently neutralizing, organic iron can form as a result of the reaction of the acids with the equipment. We have observed some organic iron being converted back to solid iron sulfide by reaction with H2S in the reactor at the same time we observed the phosphorus being deposited in the catalyst bed. That is a secondary indicator that you may have a phosphorus issue because you are just starting to see some iron sulfide formation due to conversion of iron naphthenates. They can go hand-to-hand with phosphorus.
MICHAEL SCHMIDT (Haldor Topsoe, Inc.)
Phosphorus species are rarely found in typical crudes; however, some opportunity crudes – and in particular, renewable feeds – may contain significant amounts of phosphorus. Furthermore, phosphorus containing anticorrosion additives can be found in the diesel and VGO fractions. The phosphorus compounds are decomposed in the hydrotreater, and the phosphates react with the alumina support, forming very stable alumina phosphates. Accumulated amounts of phosphates will reduce the accessibility to the active sites of hydrotreating catalysts and lower the activity accordingly. Handling of organic phosphorus compounds in the VGO feed to FCC pretreaters or hydrocracker pretreaters is a major challenge in some refineries. The phosphorus deactivates the conventional catalyst fast and reduces cycle length dramatically. Often the phosphorus is co-present with silicon and calcium in the feed, and this combination makes the impact worse. The strategy for handling phosphorus is to capture it upstream the main high-active HDS catalyst. This is achieved by installing guard catalysts with improved porosity which allow the phosphorus to deposit in high amounts, thus protecting the main catalyst to a much higher degree. These guard catalysts, with proprietary properties and composition, will be able to prolong the cycle length of the unit.
Topsoe has a specialty product, TK-31, with a very high capacity for phosphorus (P). We recommend installing this phosphorus trap if the feed level is higher than 2 ppm P for protecting the downstream bulk catalyst from contamination and subsequent increased deactivation.
RALPH WAGNER (Dorf Ketal)
High temperature corrosion inhibitors used to control naphthenic acid corrosion are another source of phosphorus to be considered. A Best Practice is to use an inhibitor that is thermally stable and oil-soluble to control corrosion at the lowest possible phosphorus level. Many phosphate esters used for this purpose are vulnerable to thermal degradation. A thermally stable phosphate ester can reduce the level of phosphorus required to control corrosion by up to 80%, reducing exposure to the hydrotreater catalyst.
DORIAN RAUSCHNING (Criterion Catalysts & Technologies)
Phosphorus is increasingly being reported in a wide range of feedstocks including shale tight oils and recycle oils. The phosphorus is, in part, a result of different chemical additives. It may also be indigenous to some crude oils. Regardless of its source, phosphorous contributes to catalyst deactivation by depositing on the exterior surface area of a catalyst pellet and restricting hydrocarbon access to the catalyst pellet’s interior active metal sites. It has been detected on conventional hydrotreating catalysts with concentrations of 2 to 3 wt% and exhibits significant loss of activity. While narrower pore catalysts have limited phosphorous tolerance and deactivate quickly, wider pore demet catalysts can be effective in absorbing feed phosphorus and protect the lower bed primary conversion catalysts from phosphorous poisoning. Criterion offers a range of wider pore demet catalysts that facilitate greater interior pellet pore utilization for phosphorus deposition. These demet catalysts also provide some moderate hydrodesulfurization/hydrodenitrification (HDS/HDN) conversion activity while simultaneously trapping other feed contaminants such as Ni, V, Si, and As. One version of our MaxTrap demet catalyst demonstrated 10 wt% phosphorus pickup.