Question 32: What is your suggested minimum temperature required to achieve adequate metals removal in the demetalization (demet) catalyst to protect primary treating catalyst in FCC and hydrocracker pretreaters?
TEMME (Albemarle Corporation)
The suggested minimum reactor temperature required for adequate metals removal is going to be metals specific. For silicon, the temperature is definitely greater than 570°F; and for nickel and vanadium, we suggest greater than 600°F. Now higher reactor temperatures may be required for adequate removal, depending on the space velocity through the metal-strapping catalyst and whether or not there may be a tolerance issue with the primary treating catalyst. It can also be very feed specific. If it is a very aromatic feed, such as a highly asphaltenic feed with high levels of porphyrin molecules, higher reactor temperatures may be needed to enable saturation of a ring(s) of the porphyrin structure to allow for the metal compound removal.
With very aromatic feed, close attention should be given to an optimal pore size of the metal-strapping catalyst with a larger pore-sized catalyst generally being needed. High nickel and vanadium content feeds require such a catalyst to avoid a premature form of plugging due to the metal deposition.
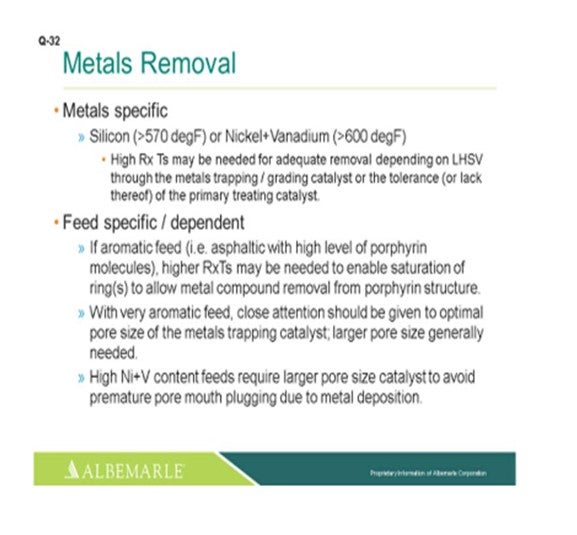
For hydrocracker pretreating's and other gas oil-types of processing applications, especially when processing heavy feedstocks, not only is nickel and vanadium problematic, but also the porphyrins and the asphaltenes. These molecules can deactivate the catalyst via a condensation reaction forming coke that is going to plug up pore mouths and block access to active sites. So proper protection of main bed catalysts for not only nickel and vanadium, but also for asphaltene contamination, is critical in heavy feedstock applications.
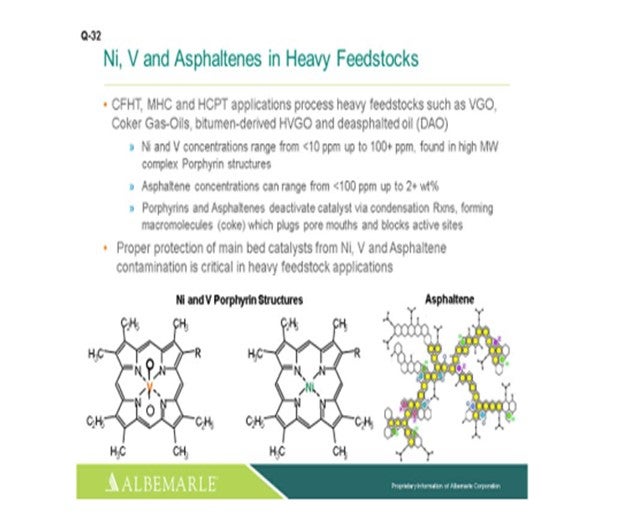
The left corner of this slide shows a comparison, in terms of large pore-sized catalysts versus small pore-sized catalysts, with the Y-axis showing the relative activity of the fresh catalyst as nickel and vanadium as deposited on the catalyst, which is the X-axis. You can see that the falloff and activity with the small-pore high activity catalyst can be much greater than that of the large-pore high activity catalyst. The graphic to the right really depicts this type of phenomenon where the larger pore catalyst allows for a fuller deposition of metal throughout the catalyst particle; whereas with the small pore-sized catalysts, there is pore-mouth plugging which restricts access to the active site. So, a good metal-tolerant catalyst is definitely needed for this full deposition of the metals through the catalyst particles. Now yes, there is usually some tradeoff in terms of a little lower activity; so, you definitely must have a good balance between your demet (demetallization) catalyst and your active catalyst to make sure that you have enough demet catalyst to protect your active catalyst.
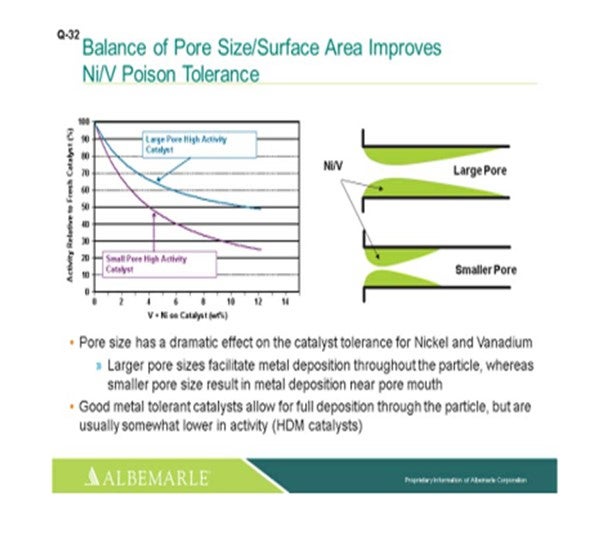
Just one other slide relating to asphaltene porphyrin condensation potential. The hydrogen partial pressure unit is below 1600 psig. A large-pore monomodal architecture type of catalyst, a conventional catalyst, is probably just fine for activity, as well as metals coke capacity. But for higher hydrogen partial pressure greater than 1600 where the condensation rates become higher, bimodal architecture specialized catalysts can be very helpful in terms of increasing the metals- and coke-loading capacity.
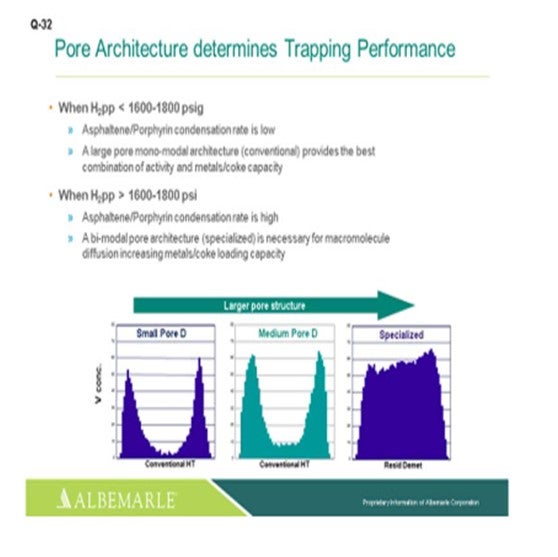
MORELAND (Valero Energy Corporation)
Thanks, Paul. That was a good summary. I told the guys at lunch today that we get a lot of the basics in this Q&A, and I think Paul covered really, really well the basic mechanisms in nickel vanadium plugging. So I will just bring a question to the audience describing a scenario I have seen while helping support our units within Valero. Some recommendations from our catalyst partners are a little different. We have two cat feed hydrotreaters – and this is for you experts in the room – that have two different recommended minimum temperatures for demetallization. Basically, this question asked about cat feed hydrotreaters and hydrocracker pretreats. Unit A is a cat feed hydrotreater for which our vendor recommended the demet temperature should stay below 650°F at start-of-run. I have a very similar unit in another one of our refineries. A different catalyst vendor recommended the start-of-run demetallization temperature be greater than 690°F. So, in one case, they say less than 650°F; and in the other, greater than 690°F. As I reviewed this issue more in-depth, I looked into the catalyst properties themselves. What we have found was that in Unit A, the catalyst itself that they were using in the demet beds was 2% nickel, 8% moly, and an expected 50 to 60 wt% (weight percent) metals pickup. So, my theory – and correct me if I am wrong – is that our goal here is to maximize the capacity of this demet catalyst. We are not really worried about the percent of nickel-vanadium removal. The second unit: You can see that the metals here were basically about half of what they were in the other. We are looking for almost twice the weight percent metals pickup. This is the one they recommended 690°F as the minimum operating temperature. The idea here is to try to maximize the nickel-vanadium removal and protect the downstream catalyst so that the capacity really would not be an issue. So, at the end of the day, when they asked me this question, I said, “Go back to your licensor or catalyst vendor and do what they say.” [Laughter]
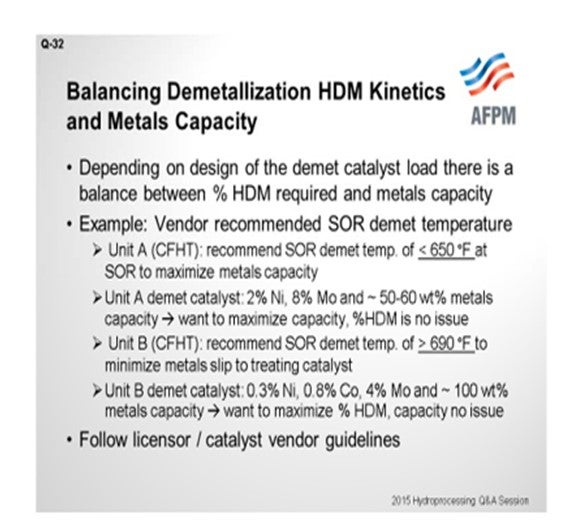
EPSTEIN [Flint Hills Resources, LP (FHR)]
A tough act to follow. Flint Hills Resources Pine Bend Refinery has typically used around 500 to 550°F as a minimum temperature for treating. The minimum temperature required for metals removal depends on the metals that are present in the feedstock. Arsenic removal follows a kinetic reaction (chemically bonding to the catalyst) and therefore may require a higher temperature to maximize pickup than other metals, such as nickel, vanadium, and silicon. For specific poisons and catalysts, FHR would usually defer to the supplier. The people who provide the catalyst-supplier guidance are in this room. I am not going to name names, right? [Laughter]
RAMÓN LOUREIRO (KBC Advanced Technologies, Inc.)
Is the loaded density the same in both cases?
MORELAND (Valero Energy Corporation)
No, I do not believe it is. I think the demet catalyst in Unit B with the lower metals is about half of the loading density.
RAMÓN LOUREIRO (KBC Advanced Technologies, Inc.)
If one is half of the other – that is, 50 units per volume – and the other one is 100 units per volume, then you will end up with the same result, given that one loads twice the metals on a weight percent basis, right? Then it is independent of space available in the reactor to load the catalyst.
MORELAND (Valero Energy Corporation) You would end up with them, yes.
RAMÓN LOUREIRO (KBC Advanced Technologies, Inc.)
And it does not matter how much space you have to put in the catalyst?
MORELAND (Valero Energy Corporation)
That is true. I do not think it is a 2:1 ratio, but there is a density difference between the two.
PAT GRIPKA (Criterion Catalysts & Technologies)
Our recommendation, if you want to maximize the metals uptake, is to operate at a lower temperature and minimize pore mouth plugging, especially at the beginning. If you want to maximize removal of HDM (hydrodemetallization), you will want to operate at a higher temperature to increase the percent HDM. But your overall capacity through the whole cycle will be less because you will have increase pore mouth plugging, which was shown quite well by the first slide. So there are competing reactions and competing objectives, but we can work with either and design a system properly for either one.
MICHAEL SCHMIDT (Haldor Topsoe, Inc.)
The metal capacity of a hydrotreating catalyst is mainly determined by the catalyst’s porosity and thus not dictated by the temperature. However, the rate of metal removal is a catalytic reaction and is therefore very much dependent on the reactor temperature, as well as catalyst activity and residence time (LHSV). Based on experience, it is advisable to have reactor temperatures above 600°F to ensure that the rate of demetallization is high and the demet capacity of the catalyst is properly utilized. A higher metal content in the feed will results in higher metals pick up capacity for the catalyst.
DORIAN RAUSCHNING (Criterion Catalysts & Technologies)
The rate of feed metals removal and a catalyst’s capacity to trap metals, such as Ni and V (vanadium), in FCC PT (pretreat) feeds depends on temperature, pressure, feed metals concentration, catalyst pore structure, and catalyst size. In general, the higher the temperature, the higher the rate of HDM, but a minimum temperature of about 600°F should be maintained. Criterion’s demet catalysts contain moderate hydrogenation activity that generates exotherms and provides some additional driving force for the HDM reactions to occur, even with a suboptimum reactor inlet temperature. Other feed metals – such as Si, As, or Fe (silicon, arsenic, or iron) – can also be present and be removed from the feed by selective trap catalysts in this temperature range. Criterion offers a wide range of selective Ni, V, As, Si, and Fe trap catalyst whose depth, sizes, and properties can be optimized to remove metals from feed and protect the primary conversion catalyst.