Question 32: How does catalyst activity, run length, H2 uptake, volume swell, reactor temperatures, price of the catalyst and product quality impact optimizing the business case for a catalyst selection? Compare a regen catalyst, moderate activity and next generation catalysts in a cheap H2 available market.
Mike Rogers (Criterion Catalyst and Technologies)
Refinery Process Engineers are often confronted with a complex and time-consuming process when it comes to choosing a catalyst for their hydrotreating units. The “Business Case” for a catalyst decision must take into account not only the catalyst costs and projected run lengths but also refinery margin and often a long list of other less obvious factors such as catalyst delivery and availability, technical support, and spent catalyst value to either cascade to other units or send to reclamation. A systematic approach starts by creating a decision matrix, listing all of the potential priorities that need to be taken into consideration, then for each discrete catalyst option, applying a score to each entry. The overall business decision is based on an aggregate of the scores, allowing consideration of many factors. The factors mentioned in the question focus on catalyst performance and cost:
1.Catalyst activity – This is often considered the most important attribute for a catalyst, since it typically has a direct impact on many of the other priorities. Higher catalyst activity means that the catalyst will do the same job at lower temperature, which in most cases is good. To estimate how the impact of catalyst activity on the business case, it is necessary to figure out how activity affects those other factors more directly tied to the refinery margin such as unit constraints or the catalyst cycle length. Sometimes catalyst activity can directly affect refinery margin by improving volume swell or improving a product property such as cetane or density.
2.Run Length – The run length between unit turnarounds (catalyst change outs) is most often defined by the catalyst, which starts life with a high activity enabling low temperatures. Over time, the activity declines and temperatures must be increased. The end of the catalyst cycle occurs when it is no longer possible to meet the production targets – either the product is not meeting specifications, or the unit throughput cannot be maintained. There is no “ideal” cycle length for all units. Each unit has its own particular circumstance that would define what the best catalyst cycle for it is. For example, many refineries are highly integrated, so that a shutdown of one unit will cause several others to stop or slow down. In those cases, catalyst cycles need to be synchronized to the turnaround schedules of all the other integrated units.
3.H2 Uptake – Assuming a case with cheap supply of H2 and a unit capable of supplying the required H2 makeup, economics typically support maximizing H2 uptake. The cost of cheap H2 is less than the value realized in the final product barrels from the associated volume swell in the hydrotreater.
4.Volume Swell – Volume swell has a direct impact on refinery margin, since increased “swell” results in more saleable product for the refinery. The HDS and HDN reactions in a hydrotreater generate some of the volume swell, but the majority comes from olefin and aromatic saturation reactions, which lower the product density. Criterion’s newest generation CENTERA catalysts are capable of significantly boosting volume swell compared to older generation catalysts. Criterion has a full line of NiMo catalysts (DN-3636 for ULSD, DN-3621 for HCPT and DN-3651 for FCCPT) designed to deliver significantly improved HDS, HDN and aromatic saturation activity to provide maximum benefit for refiners that target volume swell. Depending on unit capabilities, additional catalysts can be incorporated into the reactor to utilize Mild Hydrocracking or Ring Opening to further increase volume swell.
5.Reactor temperatures – Reactor temperatures are set by the operator to achieve the refiner’s processing objective for the unit. The catalyst activity directly affects the required operating temperature, and in that way, activity will have a direct impact on many operational factors. In many cases, catalyst deactivation will raise the temperature requirement over time, until an equipment limitation is reached. That condition will define the “end of cycle” for the catalyst. The reactor temperature also may also have an influence on the energy consumption in the unit. Energy will have a directly quantifiable cost which can be a factor in the business case.
6.Price of the Catalyst - The cost of catalyst replacement represents the easiest identifiable proportion of the overall unit operating cost of a hydrotreater. To justify the large expense of changing the catalyst, the cost should be balanced against the expected benefits that the catalyst load will bring and include any “recovered” value which might be gained at end of run, such as the value of the regenerated catalyst, or the reclaimed metals. The actual catalyst cost can be small compared to the potential benefits to be realized.
7.Product quality – Hydrotreaters are typically operated with a primary objective of achieving a certain product quality. Producing ULSD or Tier-3 gasoline requires tight sulfur control. Other quality objectives that should be considered when selecting a catalyst might include diesel cetane or product color. Newer generation catalysts have demonstrated significant gains on their ability to address a wider span of fuel quality issues.
Catalyst Selection Matrix
A simplified example of the catalyst selection matrix for a ULSD unit is presented as follows. We used a typical medium pressure ULSD unit operating with a typical feedslate of SR and some (~10-20%) cracked stocks at 0.8-1.0 LHSV as our basis as this is the most likely scenario in which regen catalyst would be considered. Higher pressure units or units processing significant amounts of cracked stock should not even be considering using regen catalyst. For the max volume swell case, a variety of options can exist depending on the unit capabilities, revamp opportunities and feedstock characteristics and hence will have to be evaluated on a case-by-case basis.
As can be seen in the improved performance of latest generation and advanced catalysts system and as indicated by the potential value generated, there is significant value that can be realized by using latest generation catalysts. Units operating at different conditions (pressure, LHSV) and with more cracked stocks can provide even more value with utilization of latest generation catalysts and technologies. Each situation will have to be evaluated individually to determine the most economical solution. In addition to the value generated through volume gain, the other criteria (delivery, technical support and spent catalyst value) are also more attractive for the latest generation catalyst systems.
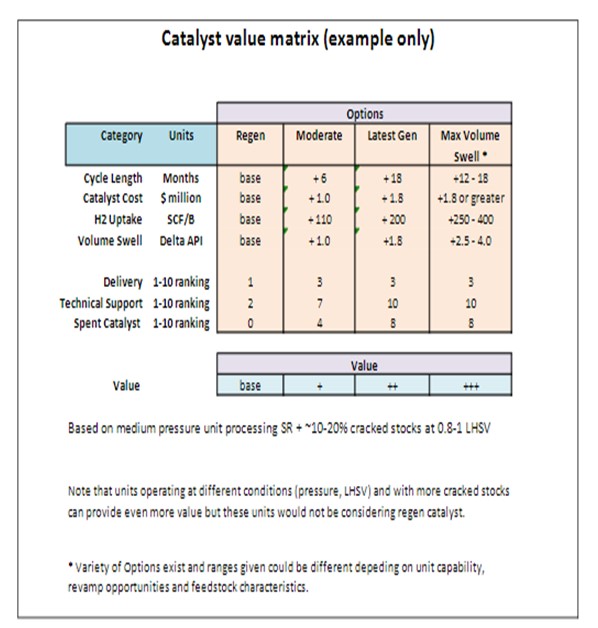