Question 31: What are your current safe practices for sour water monitoring? What are your preferred analytical methods/sampling frequency used to measure NH3/NH4HS (ammonia/ammonium bisulfide)?
McARTHUR (Phillips 66)
The primary concern with sour water sampling is exposing operators to H2S and ammonia, which will evolve off the liquid as it is collected into the sample bottle. Typically, most of our plants would take an approach of ensuring that the operator pulling the sample was in supplied air. This is our most common practice, but it tends to be a little cumbersome. Sometimes it takes some prior planning and operator availability, so it tends to lead to an inconsistent frequency of sampling.
Our preferred approach is to move to engineered sampling stations. This approach would incorporate a closed-loop supply of the sour water. We vent the sample away from the operator. Typically, the liquid sample will be running into the blowdown system. The sample bottles would be sealed with a septum, which is pierced by a sample delivery needle, as part of the sample station. The sample bottle itself is also vented away from the operator through secondary tubing. These bottles do require warehousing, perhaps of something that is not currently in stock at the plant.
Septum covers are also required for the tops of the bottles. Several of our plants are now using some analyzer capability for the sour water. These are plants which typically run against their ammonium bisulfide limits, and we need to keep a closer eye on those concentrations. We are having some good success with these systems.
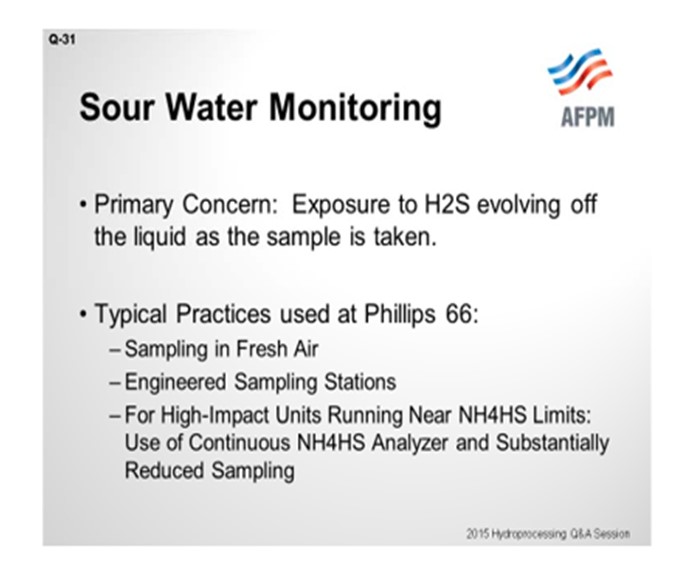
As far as the analytical methods, most refineries either measure total sulfide, total ammonia, or total alkalinity as a lab analysis. We believe that total alkalinity and total ammonia are the more accurate of those methods. Total sulfide tends to be less accurate because of loss of H2S during the sampling event. That leakage can lead to a false sense of security because you are actually reading something a little lower than what it actually is. That inaccuracy can be demonstrated if you do a sulfide comparison against an ammonia test comparison. We find total alkalinity testing to be the most accurate of the lab tests.
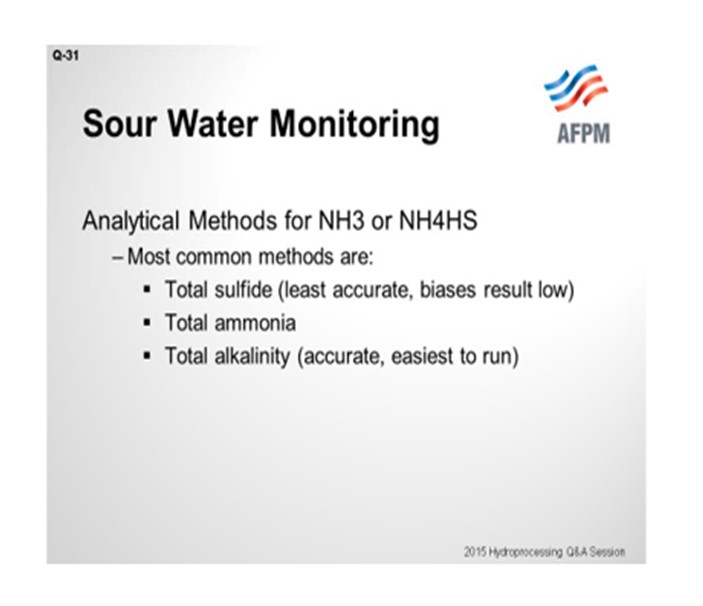
And then on this last slide, I have drawn a fairly simplified schematic of several of our units where we have a closed-loop sampling system off of the foul water system at the bottom of the vessel. Also incorporated around that sample station, which is done with some amount of frequency, is an analyzer loop that will also be a continuous tie-in to our DCS (distributed control system).
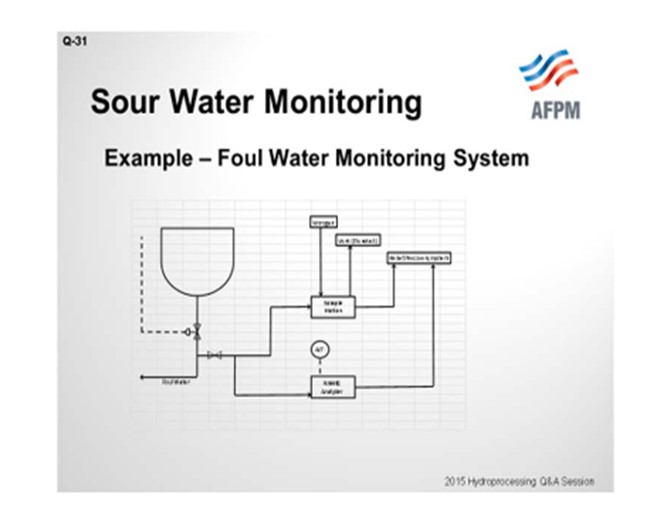
EPSTEIN [Flint Hills Resources, LP (FHR)]
At Flint Hills Resources Pine Bend Refinery, the high pressure side NH4HS concentration in the sour water is calculated according to API 932B assuming that all organic nitrogen removed (from mass balance between feed and product nitrogen) forms NH4HS with the excess H2S available and is washed to the high pressure sour water boot. Feed and product nitrogen analysis is key in this calculation. Use of the calculation is conservative for NH4HS concentration and eliminates the need for frequent water sampling. In addition, sample stations that are designed with restriction orifices, valves, and flow-through design around the high pressure letdown valves are used. A septum lid on the glass bottle allows flow sampling of the lower pressure liquid. This water is tested for chlorides, pH, iron, NH3, and H2S which are used for verification of adequate separation and waterwash mixing.
Samples are taken of the sour water on the hydroprocessing unit’s low-pressure side (cold low-pressure separator boot and fractionator overhead accumulator) for ammonia, sulfur, pH, chlorides, and iron testing. These samples are taken in bottles and tested at the site laboratory using Standard Method 4500-NH3 D for NH3. The laboratory system of labelling for these samples includes warning of the presence of H2S and NH3 for safety in handling.
MORELAND (Valero Energy Corporation)
First of all, I agree with what Scott and Paul said about safe practices for sour water monitoring. At Valero, we also require fresh-air and closed-loop sampling for those hazardous samples. Our standard is to compare the feed-based nitrogen calculation for ammonia bisulfide, which is outlined in the API 932B, based on pounds of nitrogen removed. We compare that ammonium bisulfide result to the lab sample result based on ammonia and H2S. The calculation and lab results tend to agree within about 10%. If they do not, then that gives us a good indication that we need to go look at the sampling method. Potentially, we could be losing some H2S from those samples. We also check sour water pH, iron, and chloride content, like Paul mentioned. We have a system in place at Valero to flag these sample results if they are above a predefined limit. Those flags are communicated up not only to the refinery leadership team, but also to our corporate refinery management as well.
ALMA SCHURIG(Big West Oil, LLC)
We had a one-off situation where there was hard water leaking into our sour water system from a cold water exchanger (in the crude overhead cooling system). Since then, we have also started monitoring for hardness in our sour water feed. The hard water quickly caused us problems in our sour water stripper. It plugged the stripper with hard water deposits and shut down the unit. So I am curious if anyone has had enough problems with hard water ingress that they have implemented regular hardness monitoring of the sour water.
MORELAND (Valero Energy Corporation) I do not know if we have had an issue with the hardness, but we do have hardness specifications for the water we use for waterwashing our hydrotreating units which have been specifically placed for those issues. I am not aware of Valero has experienced the issue.
McARTHUR (Phillips 66) Likewise here. We do have hardness specifications for washwater supply, but I do not think we typically test the foul water.