Question 31: What are the potential impacts to hydrocracking units [i.e., deactivation rate, HPNA (heavy polynuclear aromatics) formation, etc.] as heavy coker gasoil (HCGO) rate/endpoint are increased?
JOHNSON (Motiva Enterprises LLC)
What we have modeled here for you today is both cases. So, obviously, in a general sense, increasing heavy coker gasoil content will increase Conradson carbon and nitrogen. Then, the coking tendency in deactivation rate will also increase.
To walk you through the curves, the top case shows when we are looking at the treating and cracking reactors relative to increasing the endpoint only. As you can see, in the beginning, the curve is fairly ‘flat’, in terms of the deactivation rate. However, depending on the ‘severity’ of the endpoint shift, you will get more of an exponential curve increase in deactivation. In the other case where we hold cutpoint constant and increase the percentage of heavy coker gasoil within the feed pool, we get more of the linear relationship, in terms of deactivation rate on cracking and treating reactors.
Obviously, the more ‘difficult’ nitrogen species will increase contaminants such as nickel, vanadium, and arsenic, which will also cause more carbon buildup on the catalyst and increase catalyst plugging and aging. With heavy coker being as olefinic as it is, we are also increasing the polynuclear aromatic precursors and then, therefore, increasing the buildup of our polynuclear aromatics. It is interesting to see what truly happens at cutpoint versus just barrels on qualities.
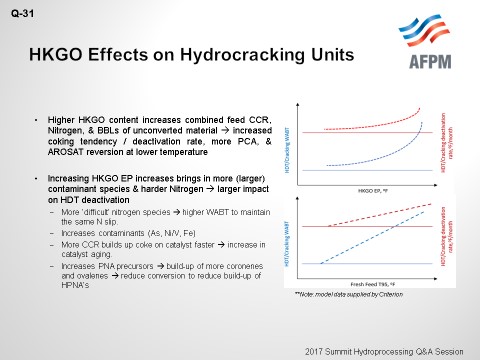
RAMACHANDRAN (Bharat Petroleum Corporation Limited)
From a practical standpoint, the impact of higher feed rate and endpoint increases
-
Fouling of heat exchangers,
-
Plugging of high-pressure vapor coolers,
-
Pressure drop on the catalyst bed,
-
Deactivation of catalyst, and
-
The formation of coke, and also causes coloration and instability in the product.
The impacts of this higher feed rate and end point can be reduced by ensuring that we have an amount of drag or purge stream – sometimes at the cost of conversion – which will split unconverted oil into light and heavy fractions. Only the light stream is recycled; the heavier stream is taken away as rejects. What helps is selective HPNA absorption from the recycled stream, as well as maintaining the feed endpoint typically around 1022°F instead of 1100+°F in case of once-through hydrocrackers with about 85 to 90% conversion. Maintaining a high recycle ratio in the coker also helps, although it will result in more coke formation and will crack into lighters at the cost of distillates.
PAPPAL (Valero)
In an extinction recycle hydrocracker with high conversion targets, HPNA (heavy polynuclear aromatics) production likely increases as CHGO is added to the feed. Generally, you have to reduce conversion and increase unconverted oil purge rate to compensate for the increased HPNA production. To judge the viability of CHGO upgrading through an extinction recycle hydrocracker, an economic analysis is likely required. The overall value of processing CHGO through the hydrocracker would be compared to the next best non-hydrocracking alternative for processing the CHGO. In general, the higher the pressure of the hydrocracker, the more improved the capability for upgrading CHGO at high conversion levels will be.
SALVATORE TORRISI (Criterion Catalysts & Technologies, L.P.)
I have a response and a question. In general, my experience is that coker fractionators perform differently than vacuum towers. A10ºF increase in endpoint for a coker gasoil adds more difficult species than when you increase HVGO endpoint by 10°F. The actual fractionation quality is not quite as good in a coker, so that seems to drag in a lot or all of the elements you mentioned.
I heard you speak about many of the impurity implications except for asphaltenes. Do you have any general rules for asphaltenes, in terms of increasing endpoint by 10ºF? Is there a maximum value you recommend for color, asphaltene content, or metals level, from a coker feed quality standpoint? Do any of the panelists have an opinion? When is an endpoint too high?
PAPPAL (Valero)
CHGO in a properly functioning unit should be very low in asphaltene content. A typical number quoted is 300 to 500 ppm as the limit of asphaltene content to a hydrocracker. So, if a blended feed starts exceeding that value, deactivation will likely increase. Online measurement of HPNA in unconverted oil is currently unavailable. What is needed, from an operating standpoint, is a quick-and-dirty workaround that relates the laboratory-measured HPNA values with an easily measured property. An example is using the color of the UCO as a proxy for the HPNA content of that stream. The objective is to limit the HPNA within targeted levels. As more difficult feed is added to the hydrocracker, optimization within limits is required.
JOHNSON (Motiva Enterprises LLC)
In terms of Motiva’s experience with processing heavy coker gasoil, typical limitations you are up against are the coke fines themselves, especially if we have drum switching issues, just like David was saying with the color as a ‘go-by’ and not directly measuring the PNAs. However, the color is an indicative point of where you stand, in terms of how much higher you can push conversion. We have never had an experience when we were able to maintain conversion targets in the 96 to 98% range. But when pushing the percentage of the pool, we do start to see some color changes and other limitations on filtration and pressure drops.
HEIDI DALEY (Haldor Topsoe, Inc.)
HCGO will contain very high nitrogen content and can also have high concentration of polyaromatics and carbon residue as the endpoint is increased. Higher HCGO rate and/or endpoint will, therefore, increase the catalyst deactivation rate in a hydrocracker. Obviously, from a catalyst vendor’s perspective, we recommend that you utilize a catalyst with maximum HDN (hydrodenitrification) activity in this application to deal with the higher nitrogen feedstocks. In addition, a tailored guard bed will help to minimize contamination of those high-activity catalysts that are designed specifically for some of the contaminants that will be present.
For a full conversion unit with recycle, HPNA formation will increase as you increase the endpoint and/or the amount of coker gasoil in the feedstock. HPNAs will have to be managed to avoid buildup in the recycle oil. Haldor Topsoe’s solution is our HPNA Trim™ technology which can be added to an existing hydrocracking unit. It basically involves removing the HPNAs with a simple stripping operation added to the backend on the recycle oil – as was mentioned previously – and separating HPNAs out based on their higher boiling point, thereby greatly reducing the likelihood of deactivation of the catalyst due to the condensation of the heavy PNAs.
ANDREW MORELAND (Valero)
Waterwash is another limit you will hit. A lot of our units cannot handle increasing heavy coker gasoil or any increase in feed nitrogen content based on waterwash limitations.
RAJESH SIVADASAN and SIMERJEET SINGH (Honeywell UOP)
Processing heavier and cracked feedstocks poses many challenges to the hydrocracking unit. Thermally-cracked feedstock such as HCGO, apart from being unsaturated, has relatively lower API, higher sulfur, and nitrogen content, higher proportion of C7 insoluble, and Conradson carbon residue (CCR). An increase in the HCGO distillation endpoint results in a significant increase in the proportion of polynuclear aromatics (PNA) and asphaltenes, both of which are coke precursors, which results in an exponential increase in catalyst deactivation rates.
Analysis of a commercial HCGO feed sample indicates that the proportion of 4- to 5-ring aromatic compounds, which are HPNA precursors, begins to appear in the feed as the HCGO 95% distillation point approaches 775°F (410°C) and increases exponentially with each incremental step change. Figure 1 below shows a typical change in HCGO feed PNA concentration with the increase in the tail-end distillation.
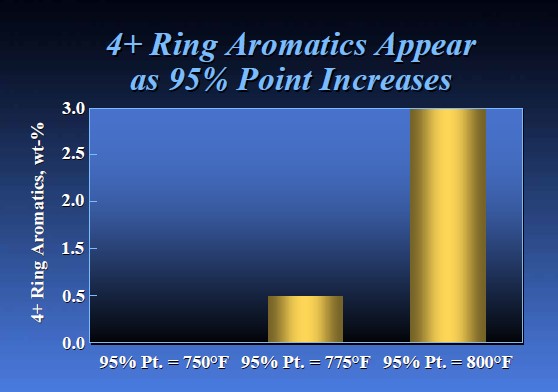
Figure 1.4+-Ring Aromatics
Figure 2 below shows four different feed streams with their PNA type breakup. Red dots are the distillation endpoint of each of the feed blend components. It can be seen that even though the HCGO endpoint is much lower than the SR VGO, relative concentration of 5- and 7-ring+ compounds or PNA precursors is much higher. Increased proportion of these precursors in the feed may result in HPNA buildup in the unit for the same conversion.
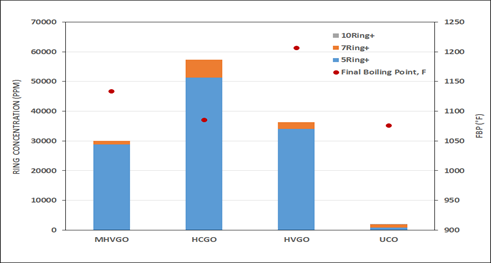
Figure 2.PNA-Type Breakup
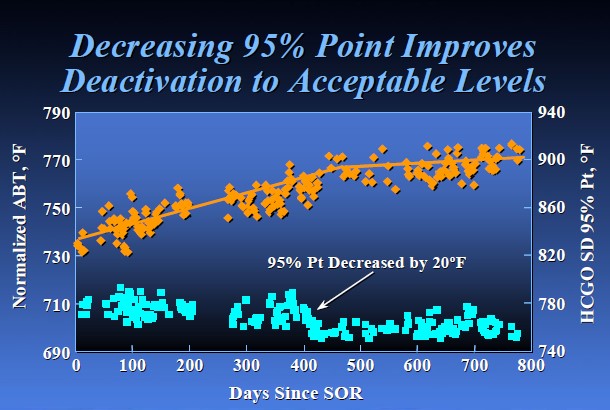
Figure 3. Increased HCGO Endpoint
Increased quantities of HCGO processing also increases the pounds of silica entering into the unit. If the guard bed catalyst does not have sufficient margin to remove this silica from the feed, it may lead to premature breakthrough into the main treating catalyst leading to shortened life; so, the guard bed catalyst also needs to be customized for processing HCGO in the unit.
Other issues with HCGO processing in a hydrocracker unit is the inability to or difficulty in maintaining the design HCGO endpoint due to transient nature of delayed coker unit operation. Increasing the sampling frequency, Advanced Process Control implementation on coker fractionator, and use of SIMDIST test methods D2887/D7169 (instead of D1160) often prove useful in monitoring and controlling the quality of HCGO feed. Advanced characterization methods like high-resolution mass spectroscopy (HRMS) can be also be utilized, especially during the design stage, to identify the feed contaminants at the molecular level and customize the catalyst system and unit design.
Both new and existing units with the capability of processing these types of feeds should have high operating pressure (preferable greater than 2,000 psi), larger reactor volume, and sufficient capacity margin in the existing hydrogen supply to cater to the increased demand. Depending on the unit operating severity, recycle gas scrubber, hot separator, and some sort of HPNA management option may also need to be included in the unit process flow scheme to improve the unit’s reliability and maintain or exceed the existing catalyst cycle lengths.
RICHARD TODD (Norton Engineering Consultants, Inc.)
Heavier feeds will definitely have an impact on both the pretreating catalyst and the cracking catalyst. Pretreat deactivation may increase significantly and affect cycle life. The potential of fouling exchanger surfaces also increases due to HPNA formation, which may also limit cycle lengths. In an HC without recycle or with the bottoms going to an FCC, catalyst aging may be the primary effect.