Question 30: What factors influence your decision to conduct air versus inert reactor entry for catalyst changeout? For, what methods do you use to avoid stress corrosion cracking?
WRIGHT (Hunt Refining Company)
For us to enter a reactor that is under an inert atmosphere, the conditions need to warrant it, such as when there are large amounts of pyrophoric material still present, when a specific job is required, an old catalyst needs to be vacuumed out for sampling purposes, or if there is filtration material on top that requires removal in order to allow the catalyst below to dump freely. What we have had at times is an encrusted catalyst layer that needs to be jackhammered out in order to be removed or if we have to disassemble a bed distribution tray. Those are some of the reasons why we would enter inertly.
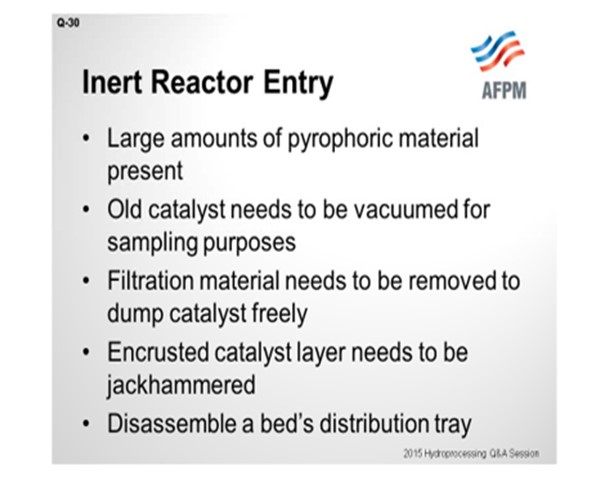
For reactor entry in a fresh air environment, no benzene or high LEL (lower explosive limit) must be present. We generally require this type of atmosphere when an internal inspection is needed.
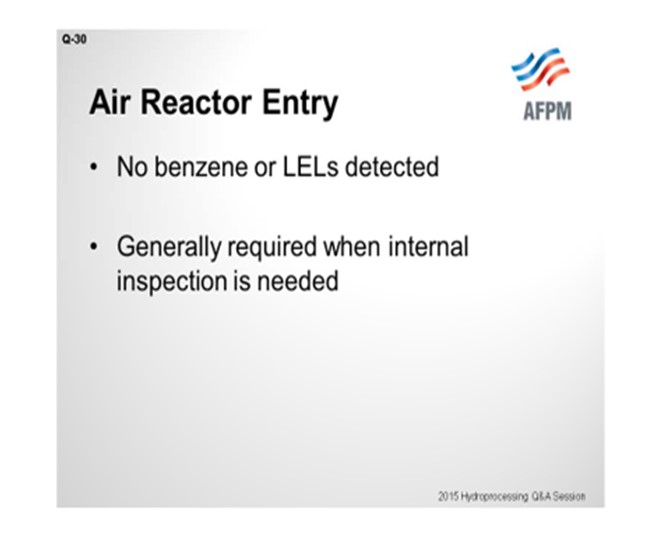
The second part of the question asked about methods to avoid stress corrosion cracking, or SCC. As a review, SCC occurs when you have a mechanical stress, plus a corrosive environment, that leads to a crack. There are several different types: chloride, polythionic, caustic, sulfide, and others. I will just focus on those first two.
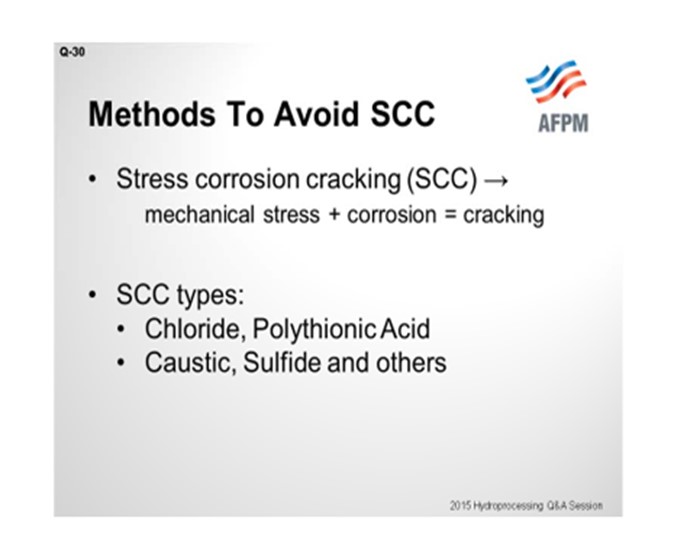
When we have tried to combat those problems, we utilized a soda ash solution which we would apply to the internal surface of the reactor either by spray washing or by simply filling up the vessel. The slide lists a few documents that may be helpful: API (American Petroleum Institute) 571, as well as these other two NACE (National Association for Corrosion Engineers) reports.
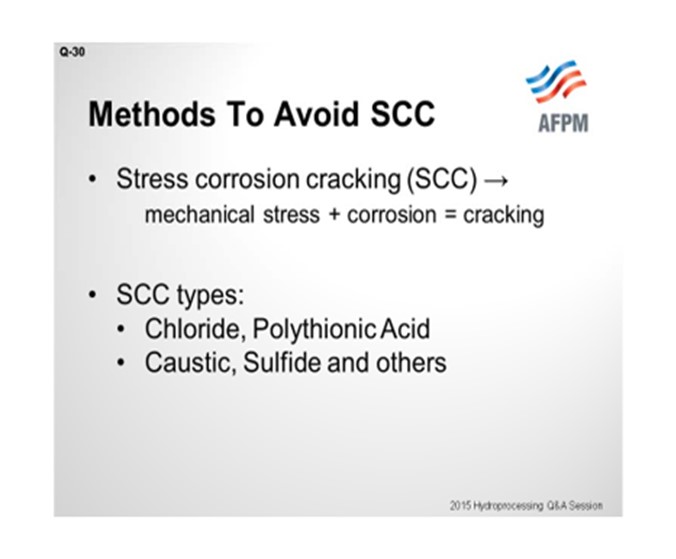
EPSTEIN [Flint Hills Resources, LP (FHR)]
The decision between air and inert entry at Flint Hills Resources Pine Bend Refinery comes down to whether or not the reactor vessel has internal hardware and whether an inspection of the vessel for mechanical integrity is necessary. If the shutdown is only to change catalyst and the reactor has only a bottom outlet collector, then the bed is kept inert during the removal and loading processes. For multi-bed reactors or those reactor vessels that require internal vessel inspection, the catalyst is removed under an inert atmosphere. The vessel and its internals are then washed using a soda ash solution via a top-down spray system with several passes and additional focus on the tray areas. The atmosphere is then turned over to air.
MORELAND (Valero Energy Corporation)
In Valero, we make the decision on air entry versus inert entry on a case-by-case basis for each reactor. Typically, we favor air – as the other panelists have said – when there is internal inspection to be done, though it does require an extra atmosphere change. We typically recommend air entry for all hydrocrackers, but we do not require it of our plants. As far as the soda ash washing, guidance from our metallurgist has been that soda ash washing is not needed unless the reactor had seen temperatures above 825°F for an extended period of time. Many of our reactors still soda ash wash even so, just for an extra measure of safety. Inert entry is quicker. It is one less atmosphere change to do. We find that work productivity during inert entry inside the reactor is almost as high as work productivity in air with a good catalyst contractor.
PEDERSEN (UOP LLC, A Honeywell Company)
I encourage you, if you are interested in more details on avoiding stress corrosion cracking, to please check out the answer to Question 36 from last year’s discussion.
DANIELLE OTWINOWSKI (UOP LLC, A Honeywell Company)
Because of the safety concerns with the nitrogen purge and the fact that soda ash washing can be partially ineffective, depending on the solution and how it is applied, to completely eliminate the polythionic acid stress corrosion cracking issues, UOP will be offering a new metallurgy option in conjunction with Nippon Steel & Sumitomo Metal/Mitsui. This metallurgical solution would be for all reactor section components that currently require austenitic stainless steel metallurgy. It is a subset of 347LN which uses patented trace stabilizers to completely eliminate the need for neutralization or soda ash washing. In addition, this new metal does not require thermal heat stabilization during fabrication, which it is an added benefit.