Question 28: What is the panel's experience in block mode operating between VGO and diesel modes? What is the frequency of change of mode and do they see any impact on catalyst activity after each switch?
OHMES (KBC Advanced Technologies, Inc.)
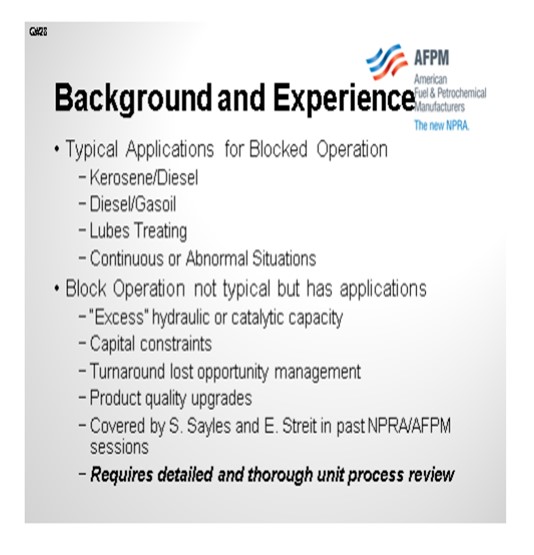
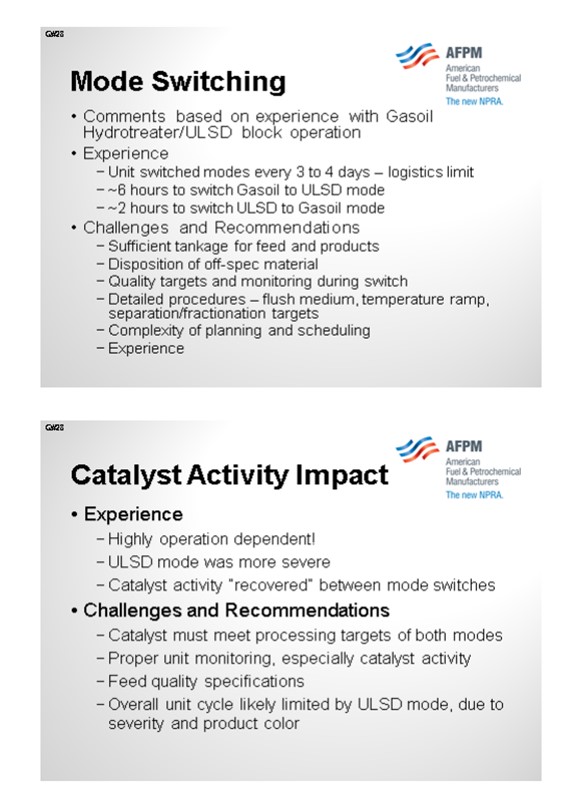
ESTEBAN (Suncor Energy, Inc.)
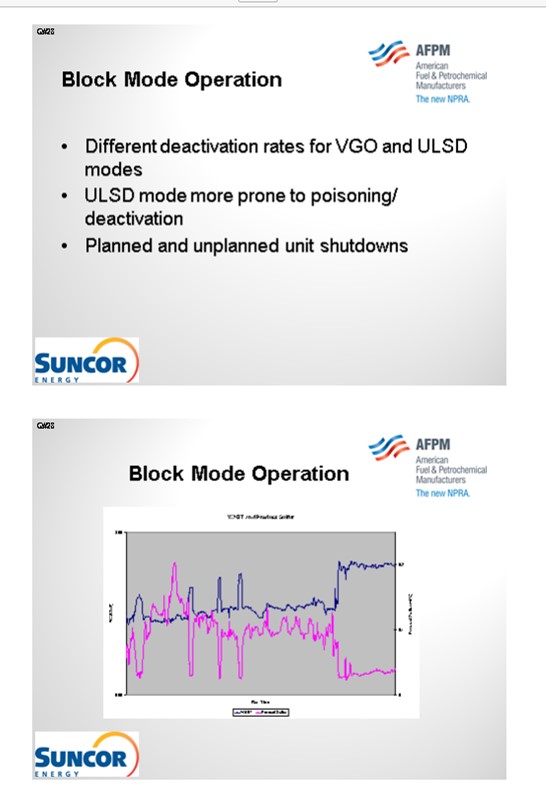
OHMES (KBC Advanced Technologies, Inc.)
To clarify this question, the term “block mode” relates to the use of a single hydroprocessing unit to operate in at least two different operations, as defined by the feedstock and operating severity. Block mode operation has several applications in the refining industry:
• Kerosene and diesel,
• Diesel and gas oil, and
• Lubes treating.
In addition, this block mode operation can be applied on a continuous operating basis or used for abnormal situations, such as turnaround lost opportunity management or brief unit maintenance outage management.
Based on KBCs experience, using a single unit in multiple modes is not a typical application but does occur in the industry. The instances where block operation occurs are:
• Refineries with hydroprocessing unit(s) with “excess” hydraulic or catalyst activity capacity,
• Capital is highly constrained and maximization of existing assets are required,
• Managing abnormal situations, and
• Ability to upgrade product quality or move away from a product quality constraint.
These situations have been discussed in more detail by Scott Sayles and Eric Streit in previous NPRA/AFPM conference papers. Before attempting to utilize an existing unit in an alternate operation, a detailed and thorough unit process review and Management of Change are highly recommended and required.
Mode Switching
In response to the question, the following information is based on KBC’s experience with refiners using a single unit to 1) produce ultra-low sulfur diesel and 2) hydrotreat gas oil for FCC processing. In this scenario, the unit ran in each mode for three to four days, and the length of time for each block was dictated by logistics (storing of unit feed and primary products). Therefore, the main constraint with a block mode operation is to have sufficient tankage to allow for storing material during the “down” mode.
The Best Practice mode switch times are about six hours when going from gas oil to ULSD mode and about two hours when going from ULSD to gas oil mode. Achieving these times requires very experienced Operations staff and detailed mode switch procedures. These procedures should cover such items as:
• Product quality targets and monitoring frequency during a mode switch, as well as certifying when the product is on specification, particularly when going to ULSD service,
• Reactor temperature ramping rates, as the two modes will normally have the reactor run at different WABTs, and
• Operating targets and ramping details for separator and fractionator operations.
• Unit flush procedures, including the order and rate that certain feed types are introduced (virgin versus cracked stocks)
For one particular client, virgin diesel was used as the primary flush material when moving from gas oil to ULSD mode. KBC worked with the client to introduce FCC LCO early in the flush period, thereby allowing the reactor to heat up quicker, due to the inherent exotherm, and improving removal of heavy gas oil components, which lead to improved switch times.
In addition to feed and product logistics, a significant challenge with block operation is the disposition of off-specification product. Therefore, including this material in the economics of the operation, as well as the planning and scheduling aspects, is critical to a successful and profitable operation.
Catalyst Activity Impact
As far as impact to catalyst activity, this impact is highly dependent on the operating modes selected, catalyst, feedstock, contaminants, and stable control. Based on KBC’s experience for well-run ULSD/gas oil operations, the catalyst activity normally recovers between the modes and mode switching, such that conventional catalyst deactivation is observed.
For successful catalyst activity management, several components must be in place. First, the catalyst, itself, should be capable of meeting the processing targets for both modes. The catalyst vendor can assist in that selection. Second, the Operations & Engineering staff needs to define and adhere to strict feed quality targets. Regular unit monitoring and catalyst activity tracking become more critical than a conventional operation.
One final point on catalyst activity involves the impact on overall cycle length. The typical scenario is that gas oil operations are limited at end-of-run (EOR) by reactor metallurgical design temperature or heat input, whereas ULSD operations are limited by product quality, such as color or cetane. When a block mode operation is utilized for both of these services, the ULSD mode will limit the unit cycle length, meaning that the catalyst still has activity for gas oil mode. Therefore, one has to either accept this giveaway of activity or consider alternative ways to produce ULSD during this extended period when ULSD mode is not possible, catalytically.
ESTEBAN (Suncor Energy, Inc.)
While Suncor Energy, Inc. does not have any hydroprocessing units designed to routinely operate in block mode between VGO and diesel, at our Denver Refinery we have operated our ULSD unit in AGO/VGO service and routinely operate our gas oil unit in ULSD service for various reasons. Our existing ULSD unit was revamped in 2006 from AGO/VGO service to ULSD service when Suncor constructed our new gas oil unit. Since the gas oil unit was not completed following a full plant turnaround the ULSD unit was initially started in AGO/VGO service and operated for three months prior to the swap to diesel service. Following the swap in service the unit performed well and easily met its designed life cycle. However, two distinct deactivation rates were noted during the course of the run. During operation in AGO/VGO service the deactivation rate was nearly double the deactivation rate in ULSD service, but these rates were predicted.
Similarly, also at our Denver Refinery, prior to the ULSD specification for non-road diesel Suncor often would feed a large volume of diesel along with AGO/VGO to the gas oil unit and increase severity to produce a side stream ULSD product from the unit, and the unit was revamped in 2011 to accommodate continuous operation in ULSD mode. Even though this mode of operation is not the same as block operation, the impact to catalyst deactivation rate of the varying modes of operation is predictable given known feed properties and target desulfurization.
Some of the challenges to this operation are unknown feed properties or contaminates that accelerate deactivation or cause pressure drop build. As with any operation poisons and contaminates will result in the loss of activity, but this loss is much more noticeable when operating in ULSD service due to the difficult desulfurization required for ULSD production. In our experience with our gas oil unit, we have noticed step changes between periods of operation in ULSD service primarily due to feed contaminates in our AGO/VGO streams and purchased CGO streams that have both resulted in deactivation and pressure drop build, while our deactivation rate during periods of lower severity service is positive but steady. Operation of our gas oil unit in ULSD mode also has presented challenges meeting sulfur specifications as reactor weighted average bed temperatures (WABT) increase in the run due to the increase in cracking which results in more difficult sulfur molecules in the diesel boiling range. In order to counteract this we make efforts to balance our reactor temperatures with adjustments to our diesel cutpoint. The following chart depicts the impact on reactor WABT when adjusting product sulfur on the unit to operate in ULSD mode.
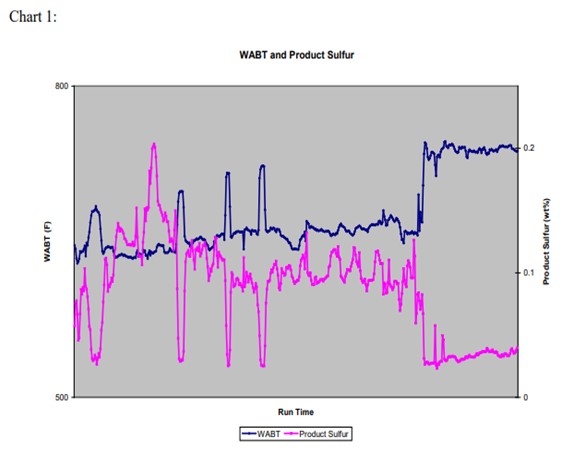
Based on our experience, we have ultimately found that the impact to catalyst activity in varying modes of operation regardless of frequency can be predictable given the proper information on feed stream properties and those impacts are amplified in ULSD production due to the level of desulfurization required.
ROBERTSON (AFPM) That concludes the Hydroprocessing session of this Q&A. I want to thank the panelists. They did a great job. And thank you all for coming.