Question 28: Under what conditions will you strip sulfur from hydrotreating/hydrocracking catalysts?
SCHOELLKOPF (Advanced Refining Technologies)
Generally speaking, the catalyst is above 500°F. In the presence of hydrogen without the presence of H2S (hydrogen sulfide), the rate in which the sulfur can be stripped off the metal sulfide is very quick. Note that the rate of reduction reaction is determined by the hydrogen partial pressure, temperature, and time, with temperature having the strongest impact. There are a multitude of scenarios that can cause H2S to not be present in the reactor and, therefore, strip sulfur from the catalyst. Typically, during sulfiding, your sulfiding agent pump trips, which is the origin of your H2S, or the H2S is purged for the open valve misalignment. Another possibility is that the aiming system is accidentally lined up. Depending on during which stage of the startup this occurs, you will have a relatively minor inconvenience or a more complicated issue. In the case where DMDS (dimethyl disulfide) is lost and you are above 500°F and at pressure, the reduction reaction will occur quickly. The same is true for mechanical failures of equipment such as recycle compressors or feed pump trips.
Figure 1 on the slide shows the reactions associated with sulfiding. The reversible reaction there on the left actually has to be conducted outside of the reactor. So, once you have stripped the sulfides off the catalyst, you will basically have to start all over again. If H2S is lost for any reason during the startup, ART) recommends immediately beginning to reduce the temperature to get the catalyst below 350°F. If possible, continue circulating hydrogen until the unit can restore the operating conditions. If the reason H2S was lost is expected to continue longer than 24 hours, then cooling to below 250°F is recommended to minimize any reduction opportunities. You just do not want to have any hot spots within the reactor.

Hydrogen stripping can also be very useful for removing soft coke and restoring some lost catalyst activity. However, that process can also lead to removal of sulfur from the catalyst. A minimum of a 1,000 ppm H2S is recommended to be maintained within the recycle loop during the hydrogen stripping procedure to avoid any accidental reduction. We also suggest working with your catalyst supplier for any additional specific guidelines.
For a temporary shutdown, which can be defined as less than 24 hours or up to 48 hours, it is preferred that you shut down the scrubbing device, of course, and purge with nitrogen. However, depending on the H2S content, recycle gas can be at some acceptable temperatures to hold the unit: the cooler, the better. You continue circulating hydrogen, assuming you have plenty of H2S in the recycle loop: 1,000 ppm or better; 2,000 ppm or better is recommended. Then of course, it is always recommended to work with your catalyst vendor for any specific guidelines in unit and anything specific to your unit.
LONG (HollyFrontier Corp - Navajo)
At Navajo of HollyFrontier, we have not had any experience – in recent history – of stripping sulfur from the catalyst. Most incidental or inadvertent stripping of sulfur from hydrotreating catalyst occurs during the startup of the unit. We mitigate that potential within our startup procedures which state that the temperatures are not to exceed 400°F during the hydrogen once-through heat-up purge before introducing the feed. The biggest impact would be with regard to catalyst run-length. The highest risk pertains to if all sulfur is removed and the catalyst is stripped to base metal. At that point, the catalyst is completely deactivated.
AL-FUDHAIL (Saudi Aramco)
Just to add to what has been mentioned already: Pilot plant testing has verified that cobalt-based catalysts require higher H2S concentration than nickel in order to remain sulfided. The tendency to reduce, again as mentioned, will be higher for a clean catalyst system in startup cycle or even clean feed service. That is basically it for me. Everything else has already been mentioned.
UNIDENTIFIED SPEAKER
As you said, a common catalyst requires a higher H2S concentration. Do you have any idea of how much higher? Is it 20% or 50% higher?
AL-FUDHAIL (Saudi Aramco)
I do not really have a quantitative number. However, you would typically want it to be in the 100 to 500 ppm range. Imagine a round-up higher number – 500 ppm or close to 1,000 ppm – of H2S concentration to keep it in a sulfided state.
SERGIO ROBLEDO (Delek US)
I think the point of the question was that we all understand where you are in oxidic state. You are going to reduce the catalyst very fast, right? Often, the question comes up when you are up in operation and have been running for a year or two. My question to the audience is: How many of you have run a hydrotreater at 600°F with no H2S present and for how long of a window activity penalty?
AGGUS (Becht Engineering Co., Inc.)
Can I answer that for those who do not wish to be identified? I do know of one instance, during a hot hydrogen strip, where it had not been previously carried out on the unit. The procedure that was utilized had been previously been employed for another unit without an amine absorber in the recycle circuit. In this case, the H2S absorber is left in operation and the temperature run up to 700°F; so, eight hours and no loss of activity. At least the way that it was monitored against the budget curve, for the remainder of that run, there was no decrease in overall catalyst activity. Therefore, the amount of energy required to get stripping of sulfur done may be higher than some may think.
ANDREW MORELAND (Valero)
We had a similar incident where we had a unit on standby circulation. Per procedure, we cooled the reactor down to 450°F. The amine scrubber was off, so we monitored the H2S build in the circulating gas. It had built up to between 50 and 100 ppm, at which point we have sufficient concentration of H2S to keep the catalyst sulfided. So, I agree with what was said: There is no activity effect, but sulfur will come off the catalyst. I will say that some of the sulfur that comes off the catalyst can be put back on as soon as feed is introduced without much of an activity penalty.
AGGUS (Becht Engineering Co., Inc.)
Just turning into an AA meeting. [Laughter]
AL-FUDHAIL (Saudi Aramco)
Actually, I have worked with a hydrocracker, and my experience was that it was quite a troublesome unit. We had a lot of shutdowns and many ups and downs. Really, there were times when we ran the recycle gas with fresh catalyst after a shutdown and after a purge. There is not really much H2S in the system. Again, this experience is similar to what has already been mentioned. Once you get the feed into the unit, whatever sulfur that has come off will soon come back and be sulfided in the catalyst. Really, not much penalty or any reduction in activity has been noticed.
Now coming back to when we are done with the unit or getting ready to shut it down for a catalyst changeout, we do the hydrogen hot strip. And boy, that catalyst system still emits sulfur H2S, even after we have done the 750°F hydrogen strip with no H2S, clean hydrogen. You take it offline and try to slip that blind to get out a lot of H2S from that reactor. So, I do not know, because I have never experienced sulfur stripping out of a catalyst system.
PATRICK GRIPKA (Criterion Catalyst & Technologies L.P.)
I am going to respond to Brant’s comment and the other comments made after his. There will be some H2S coming off because you have coke on the catalyst. There is some sulfur inside that coke which you put on the catalyst, so a lot of it depends on how heavy the feed you are operating, how long you have operated, etc. I think the recommendation will still be to err on the safest side, like Lyle suggested. If you are doing a hydrogen strip, 1,000 ppm H2S is a good place to be. Like Andy said, “It will build up some.” Therefore, 1,000 ppm H2S is essentially a safety margin for you to operate under.
AGGUS (Becht Engineering Co., Inc.)
Yes. We are not trying to encourage bad behavior. [Laughter]
BRANT AGGUS (Becht Engineering)
I saw an incident where a recycle hydrogen absorber in a gasoil hydrotreater circuit was inadvertently left in service during a hot hydrogen strip. The recycle hydrogen had essentially a 0 ppm H2S concentration, as reactor inlet temperature was held at 700°F for nearly eight hours. After the unit was brought back online, no deviation from the pre-strip required WABT (weighted average bed temperature) was observed nor did the required WABT overtime deviate from the pre-strip deactivation trend. Stripping sulfided catalyst might require more energy than many think.
SUHEIL ABDO (Honeywell UOP)
Base-metal hydrotreating and hydrocracking catalysts are susceptible to sulfur stripping at high temperature in the presence of flowing hydrogen and in the absence of H2S. For that reason, we advise unit operators to avoid prolonged exposure of sulfided catalysts to flowing hydrogen at temperatures exceeding 500°F if the H2S content of the hydrogen is below 50 ppmv (parts per million by volume). It is recommended to maintain between 50 and 100 ppm H2S in the recycle gas to ensure adequate sulfur availability. Other factors, such are exposure time, may impact the severity of stripping, but keeping the temperature below the 500°F limit should protect the catalyst for a prolonged period.
PATRICK GRIPKA (Criterion Catalysts & Technologies)
There are three operating scenarios in which hydrotreating/hydrocracking catalysts can be reduced: 1) upon startup, 2) upon abnormal operations in a very low H2S environment that is usually a result of a unit upset, and 3) during normal operation in a very low H2S environment.
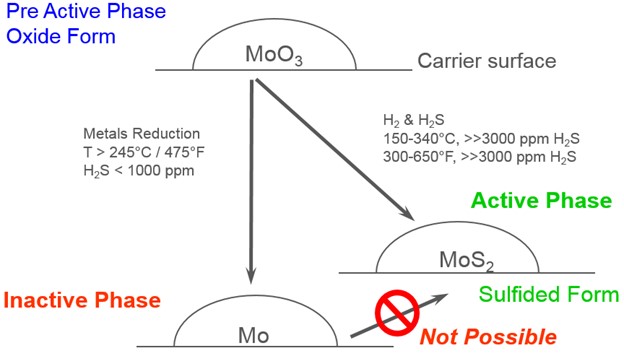
-
Likewise, in instances of a unit upset in which recycle gas is lost, our primary recommendation is to cool the catalyst beds to 450°F or below as soon as it is safe to do so. Upon restart, establish at least 1,000 ppm H2S in the recycle gas before heating above 450°F. Depending on the nature of the shutdown and cooldown, an LCO/diesel flush or a hot H2 strip may be recommended to minimize the loss of catalyst activity to the shutdown.
-
During normal operation in a low H2S environment [e.g., a very low feed sulfur NHT (naphtha hydrotreater) unit], it is recommended to inject some sulfur source [e.g., DMDS (dimethyl disulfide)] in order to keep a pre-determined level of H2S in the recycle gas.
In reality, only 50 to 100 ppm H2S is needed to keep metals sulfided. Some will argue that even a trace of H2S is sufficient. But the reality is that the lower the H2S content, the better the distribution that is required; otherwise, you may have pockets where no H2S is present. Also, reduction requires time and temperature; so, it is not an immediate process. Having a conservative guideline of 1,000 ppm H2S to prevent sulfur stripping/metals reductions provides a comfortable safety factor. For specific details on your operation consult your Criterion representative.