Question 28: How is the acid soluble oil (ASO) disposal system operated in an HF alkylation unit? - where / how do you dispose of the ASO? - do you operate the rerun continuously or in batch mode? - do you have problems with the ASO line fouling or plugging? - is there a min velocity, min/max temperature or something else that controls your rate of ASO disposal from the rerun?
Erik Myers (Valero)
The summary response is: Collect the ASO, neutralize it in KOH or NaOH and then dispose of it in another refinery product stream. In our system, the most common destination for the ASO is FCC slurry oil, either in a separate rundown line to the tank or combined with the slurry oil rundown. It can be routed to other streams such as slop oil or crude. However, in these cases care must be taken relative to metallurgy in units where the material is processed as it can still contain some fluorides and other trace materials that could lead to issues. A key component, regardless of destination is to ensure good neutralization. We have sites that have utilized the licensor technology for ASO neutralization and others that have expanded on this. Separation of the KOH (or NaOH) prior to transfer of the neutralized ASO is also key. Using an additional separation or surge drum can be effective for this. In the 2011 UOP Alkylation Symposium earlier this year, UOP outlined an industry summary of ASO routing (see chart)
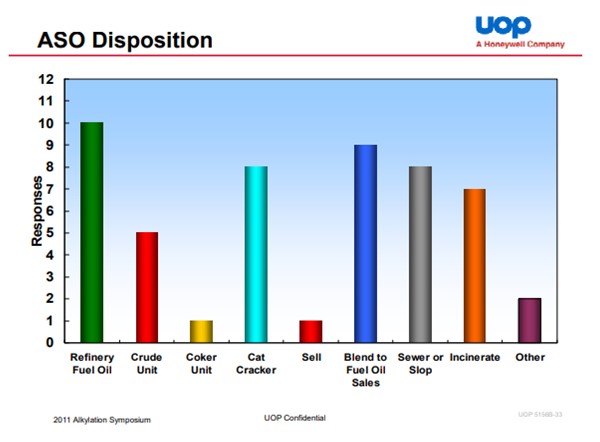
Regarding rerun or acid regenerators in batch or continuous mode, both batch and continuous rerun tower / acid regenerators are implemented at our sites. This is typically dependent on which heritage licensor designed the unit (Phillips or UOP). Some of our sites choose to run their continuous rerun columns in a batch mode, finding this to more effective from an overall operations or steady tower operation, then batch neutralizing and routing to eventual disposal destination. For those operating in batch mode a step to flush the ASO lines should be implemented after the ASO transfers. LCO is most effective due to its aromatic content. If a lighter stream is used consideration relative to product RVP / flash needs to be taken into account. Flushing of the ASO wash system lines is also appropriate as these are more typically operated in a batch mode.
Relative to system plugging, we have experienced line restrictions at several of our sites, primarily when the ASO rundown is combined with the FCC slurry oil rundown line to storage. At some locations a separate run-down line has been installed or utilized to alleviate this. KOH (or NaOH) carryover from the ASO washing system is thought to be one major contributor to this line plugging as the KOH, ASO and FCC catalyst fines in the slurry oil combine. One site has experienced plugging in the wash system. See previous comments online flushing.
Rate of transfer is typically on a batch basis when either the neutralizing drum or washer is at high level (or the downstream or upstream collection vessel is at high level). If there is adequate hold up time in these vessels, then transfer from the rerun system (or the feed to the rerun system) should not be limited by ASO disposal. If there is a step change increase in ASO production, then upstream unit operations should be carefully reviewed for items such as increased feed sulfur, moisture, diolefins, acid strength, I:O ratio or significant change in feed composition such as shifting to increased propylene or amylene.
Brad Palmer (ConocoPhillips)
UOP reported in their 2009 Alky Symposium the following industry wide acid soluble oil (ASO) dispositions: Fuel Oil/Sales 36%, Burn 20%, Slop 16%, FCC 13%, Crude 7%, and Coker 4%. The ASO is to be neutralized with KOH or NaOH with consideration given to how fluorides and potassium or sodium may impact the disposition of the ASO, especially if going to a catalyst process unit such as an FCC or hydrotreater.
The rerun tower should be operated continuous. Some sites run the tower bottom level control in a "gap" control mode, cycling the control valve between full open or full closed based on a low level of 30% and a high level of 70%. This "gap" control is to minimize valve wear if trying to throttle a small continuous flow of ASO. If the rerun tower is operated in batch mode then the lines need to be flushed between batches to avoid plugging.