Question 28: Is the changing quantity of pentanes and pentenes in refinery streams and tightening gasoline regulations leading to operators considering different processing strategies in order to maintain gasoline blend pool specifications? Comment on increased pentene alkylation, decreased pentane isomerization, or other disposition sources.
ADAMS (HollyFrontier Corporation)
The pentenes, also called amylenes, can be fed to the alkylation unit and be alkylated. However, you make a lot of ASO (acid-soluble oil), and the yield is not that great; so, most people prefer not to do it. We do not alkylate our amylenes at the moment. If you need a place to get rid of olefin or have some other constraint that is really expensive, then you may be forced into that situation.
As far as isomerization, the only reason that we will decrease isomerization is if we have excess octane in the gasoline pool; and with the ethanol-blended gasolines, we need less octane. Most likely, we would back out other feedstocks. These feedstocks might be cheap, and we could drop them into the gasoline pool. So, it is really an economic decision about your interest in backing out butanes and natural gasoline and creating RVP in your refinery by putting a light straight-run through an isomerization unit.
One final comment: You might have an isomerization unit and discover a lot more pentanes than would be beneficial in isomerizing. Not all isomerization units were built with a deisopentenizer in front of the unit. The addition of a deisopentanizer is a relatively cheap way to open up some isomerization unit capacity by removing material that is not going to get converted in the isomerization unit anyway.
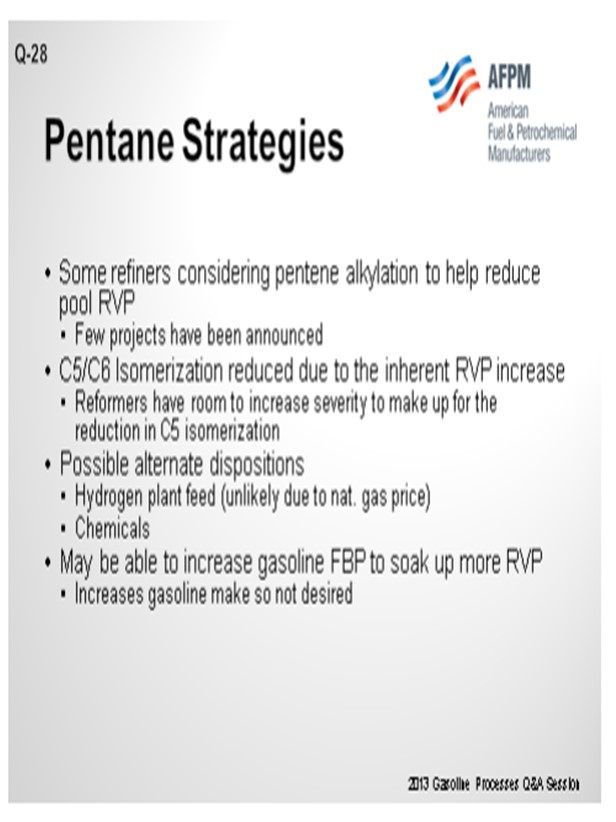
STREIT (KBC Advanced Technologies, Inc.)
There is some talk of increased pentene alkalization or amylene alkalization, but it does not seem like there are very many projects on the books to move in that direction. Whatever your alkylation unit can handle is worth investigating. Although as Mark pointed out, it probably cannot handle a lot.
With respect to the isomerization units, I talked about them before. Generally, their values and throughputs are getting reduced. In some cases, they are being shut down because of the RVP increase. It just depends on your refinery layout. In most cases, you have the ability to increase your reformer to make up that octane that you are going to lose by not isomerizing; so, it is not like you necessarily need the octane from the isomerization unit. If you do not need that octane and cannot handle the RVP increase, then what else are you going to do other than stop isomerizing?
So, what are you going to do with the pentanes? This has been a question for a while, and no one has come up with a really great solution for it. There are a couple of places you can route the pentanes now. You could put it in the hydrogen plant and make hydrogen out of it. The problem is that natural gas is so cheap right now, why would you want to use anything but natural gas to make hydrogen? The other possibility is just to send it off to chemicals, if you have access to some place that needs a light naphtha.
One other possible strategy is to increase your gasoline endpoint. That will give you more RVP soak on your gasoline pool, and you might be able to handle more light material in that pool at the same RVP. However, directionally this is not a very economically attractive idea because current economics support reducing gasoline endpoint to maximize distillate production.
MARK ADAMS (HollyFrontier Corporation)
Historically, octane has been the most important constraint on the gasoline pool in most refineries. Reduced octane requirements in ethanol-blended subgrades are changing that. Pentenes from the FCCU or coker are 90 RON and 77 MON. Alkylation is a possibility, but the volume shrink and ASO generation are rarely worth the trouble unless the gasoline pool is constrained by MON or olefin content in the gasoline. FCCU pentenes usually go to gasoline blending. Isomerization debottlenecking projects may look attractive since isomerization helps with benzene reduction. A deisopentanizer can be added upstream of the isomerization unit to bypass isopentane in the feed around the unit, opening capacity for convertible C5s and C6s.
CRAIG MELDRUM (Phillips 66)
Initial questions on C5 alkylation have been asked, but not much action has been taken thus far. Some considerations about C5 alkylation, provided by Daryl Dunham of UOP, include the following:
• More gasoline yield but not as much as anticipated. Stoichiometry and density calculations would indicate 1 bbl (barrel) C5 = + 0.96 bbl iC4 - 1.6 bbl alkylate. BUT, hydrogen transfer occurs; therefore, 1 bbl C5 = + 1.25 bbl iC4 - 1.12 bbl C9 + 0.45 bbl C8 + 0.32 bbl iC5. Since alkylate is C5+ gasoline, then iC5 is included for a total of 1.89 bbl of C5+ at 30% conversion. At 60% conversion, 1 bbl C5 = + 1.55 bbl iC4 - 0.64 bbl C9 + 0.90 bbl C8 + 0.65 bbl iC5 or 2.2 bbl of C5+ at 60% conversion.
• Increased iC5 production
• Lower gasoline RVP as C5s is converted to gasoline: nC5 RVP is 15.6 psi; iC5 RVP is 20.4 psi; C8 RVP is 1.0 psi; and C9 RVP is 0.5 psi.
• Lower alkylate RON and increased alkylate T90 (5 number drop in RON and 100°F increase in T90 when moving from a mixed PB stream with 10% C5 = to a 100% C5 = feed).
• Increased ASO production (more “stuff” comes into unit as feed gets heavier).
ERIC STREIT (KBC Advanced Technologies, Inc.)
There is growing concern regarding the quantity of light naphtha available relative to total gasoline volumes. This requires some head-scratching to create innovative solutions to this potential bottleneck. There are certain areas of the country where light naphtha cannot be blended into the pool while meeting volatility specifications and are Therefore, sold at a discount. Some refiners are considering alkylating pentenes from FCC gasoline as a means to reduce gasoline pool RVP to allow for upgrading light naphtha in isomerization units. However, not many projects have been announced to date. Most reformers are running at much reduced severity due to the decreased octane demand associated with increased ethanol blending. As a result, they may have some flexibility to increase severity to compensate for lower light naphtha octanes resulting from decreased pentane isomerization. Another possible destination for pentanes is to feed them to a hydrogen plant. This may not be economical because natural gas is so inexpensive, but it is an option. Finally, increasing gasoline FBP (final boiling point) may allow a refiner to soak up more RVP in the gasoline pool. Directionally, this is not desired because it converts more valuable diesel into gasoline. However, if it helps to get a refiner in terms of gasoline RVP, it may need to be considered.
ROBERTSON (AFPM)
Those are the responses from the panel. Since there are no additional comments or questions from the audience, we will now conclude the Gasoline Q&A session. I want to thank the panelists for the great job they did today and for all of their work over the last couple of months. I also want to thank Allen Kaiser for being the coach for this group.