Question 27: What options are refiners considering addressing upcoming Tier 3 Fuel Standards [10 wppm (weight parts per billion) annual average sulfur in gasoline]?
STREIT (KBC Advanced Technologies, Inc.)
Tier 3 fuel is lowering sulfur yet again in gasoline. The crude oil sulfurs have been coming down also with the tight oil, so some people have asked the question: Is processing more tight oil actually going to get us on-spec on Tier 3? The answer is no, not really. It is not going to have that significant of an impact on your gasoline sulfurs, obviously, without other processing.
As of right now, it does not seem like there is a lot of capital being mobilized to meet Tier 3 specs. There are people who are doing things, but they not building as many new units as you might think or not doing quite as many sizable revamps. Many places are tied in with their investments to be on-spec for Tier 2. They are trying to exploit those facilities to get on-spec for Tier 3 with the addition of, say, a polishing reactor on the backend of a gasoline desulfurizing unit. Some places are trying to add more catalyst into that existing unit to try to get the sulfur down.
Some refiners have discussed exporting gasoline blendstocks in order to be able to get on-spec on Tier 3. It does not look like a long-term option because there is not a market that will support that for very long, if it is currently available in your area anyway. Some places have discussed increasing gas oil hydrotreating. One of the drawbacks to putting all your eggs in that basket is that if you have problems with the gas oil hydrotreater, then you will not be able to make gasoline. If you have desulfurizing on the backend, you are relying on a unit that is inherently a little more reliable or less likely to trip off and cause you problems. It is just something to keep in mind if that is a solution that you are considering getting on-spec on Tier 3.
Another problem coming up with making 10 ppm sulfur gasoline is that blendstocks which did not used to be a problem may now be one. A lot of places that did not ever think about how much sulfur their butane stream contained are now realizing their butane has 7 ppm, 10 ppm, or 12 ppm sulfur just depending on its source. In those cases, you might actually have to put in a facility to remove the sulfur from butane. Many people think of alkylate as sulfur-free. It is not. It can contain as high as 7 to 20 ppm sulfur, so you must be aware of that. I think the main options being considered right now are trying to expand on the solutions to get on-spec for Tier 2. It does not look like there is not a lot of capital at this time which is being mobilized to do anything different.
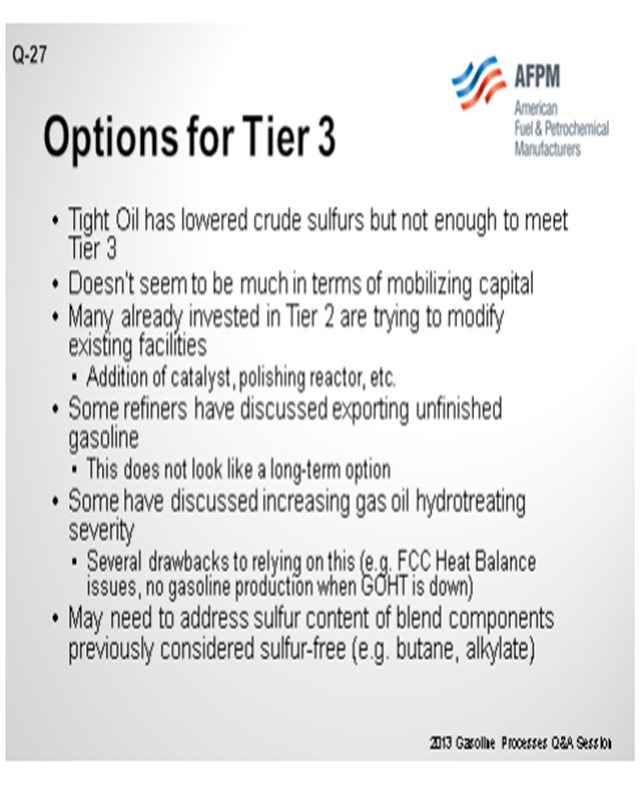
MELDRUM (Phillips 66)
Current sulfur specifications in the finished gasoline are 30 ppm with an average 80 ppm on a cap, reducing down to 10 ppm, on average, with an anticipated cap of 50 ppm effective in 2017.
In Phillips 66, we will exploit the previous Tier 2 compliance projects as much as we can, but that is not going to get us to a solution in all cases. We will be expending quite a lot of capital in order to meet those Tier 3 regulations, either from polishing units or building some additional one into the refinery process.
I have provided a table showing a typical Tier 2 blend to give you a feel for the order of magnitude of where the sulfur is coming from within the streams. You will notice the two dominant areas of focus will be for the straight-run and cat naphtha streams. Straight-run treatment is fairly straightforward with some conventional or mild hydrotreating. You can expect expected to see about 1-number octane loss in that stream.
The cat naphtha streams are a different story. If traditional methods are employed to treat that stream, you can expect to see as much as a 10-number octane drop in that stream. That is not acceptable in almost all cases, so “advanced” hydrotreating technologies have been developed which utilize the characteristics of the light cat naphtha compared to the heavy cat naphtha. Light cat naphtha has few light mercaptans and a lot of olefins; heavy cat naphtha has a lot of sulfur and few olefins. A simplified process description is as follows:
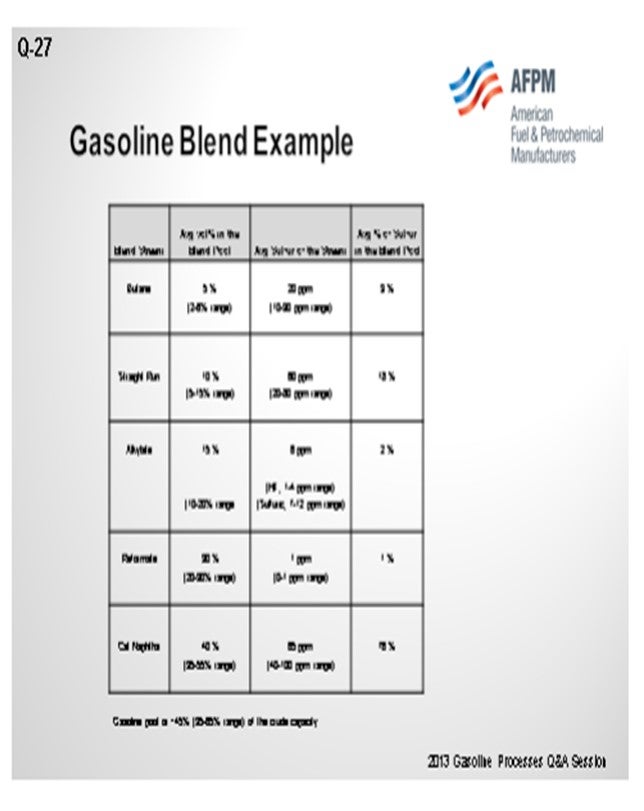
Treat the full-range cat naphtha with a mild hydrotreating to convert the light sulfur compounds (the mercaptans) into a heavier sulfur compound through thioetherification. The naphtha should also be treated with minimal olefin saturation, fractionation to separate the light from the heavy naphtha streams, and additional treatment of the heavy cat naphtha to remove the sulfurs, disulfides, and thiophene conversion. Expect octane loss with this process sequence to be a 2- to 4-number drop.
Another process is the absorption removal of sulfur compounds, the S-Zorb process, which achieves sulfur compliance with about a 2-number octane drop.
I want to echo what Eric mentioned: Some of the streams which had not been given much attention in the past (butane and extraction raffinate) might need additional treatment and/or washing to meet final blend specifications.
CHRIS GREEN (Marathon Petroleum Corporation)
With regard to the butane sulfur, do you have any comments about dealing with dimethyl sulfide in butane? Also, what strategies can you use to remove dimethyl sulfide and reduce the butane sulfur?
STREIT (KBC Advanced Technologies, Inc.)
I think in most cases what I have seen is all mercaptan-based. So, I am not personally aware of anyone dealing with dimethyl sulfide, specifically, in the butane stream. I would imagine that means you will have to route it to a naphtha hydrotreater or something like that to get that material out. I have not personally seen anyone who had to do that yet.
DAVID SMITH (UOP LLC, A Honeywell Company)
A number of adsorbents have been utilized in a regenerative mode to remove dimethyl sulfide and dimethyl disulfide from C4 streams, either butane or mixed C4 (butane, butenes) streams. There are high capacity molecular sieves for the removal of these sulfur compounds if it is a paraffinic stream. The product AZ-300, a hybrid adsorbent, has widely been used to remove these sulfur-based contaminants from both butane and butane streams. It is not economically feasible to remove hundreds of parts per million of DMS (dimethyl sulfide) or DMDS (dimethyl disulfide); but if you have relatively low concentrations, adsorption is an attractive option for their removal.
JESSY TRUCKO (UOP LLC, A Honeywell Company)
I want to add to that comment. Typically, the DMS follows the C5 stream; so, you should be looking for about a 1.4 reflux-to-feed ratio in your debutanizers. In addition, as you mentioned, we have also done some combinations of Merox™ and adsorbent, which allows us to achieve less than 1 ppm sulfur in the product. BULLEN (UOP LLC, A Honeywell Company) If you do need a hydrotreater, UOP sells LPG hydrotreaters. We do not design them very often, but the technology does exist. Question 27: Answer Book Responses
CRAIG MELDRUM (Phillips 66)
Tier 3 regulations for finished gasoline reduce the sulfur specification from 30 ppm average (80 ppm cap) to 10 ppm average (anticipated 50 ppm cap), effective January 2017. Typical Tier 2 compliant gasoline blend data clearly indicates that lowering finished gasoline sulfur will focus on straight-run and cat naphtha treatment (see table in shown below). Pushing process units used for Tier 2 compliance to maximum severity is not expected to provide full compliance with Tier 3 specifications; additional treatment projects are expected.
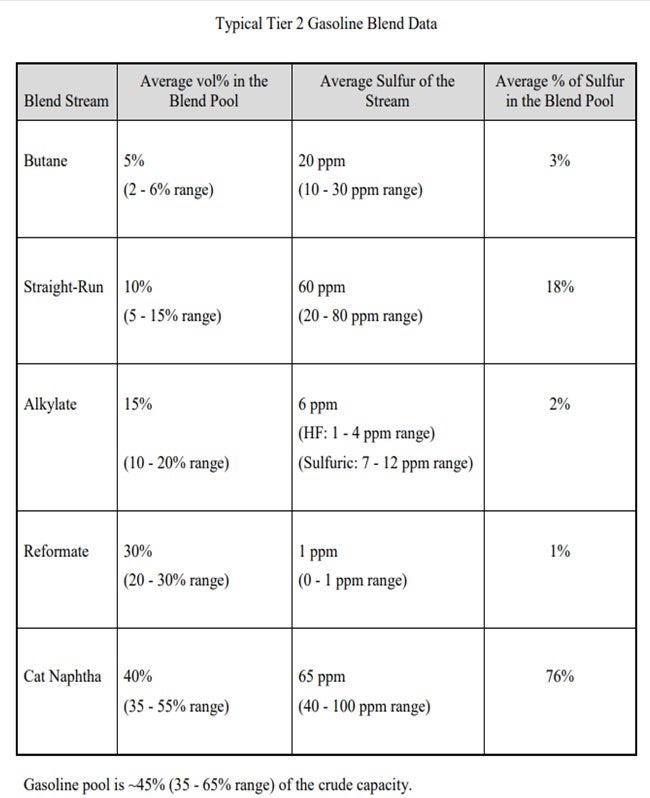
Straight-run treatment is best achieved with mild hydrotreating (typical parameters of 350 to 500 psig, 300 to 700 scfb, and 5 to 8 LHSV). It is expected to see less than 1 octane number loss in the stream. If used, conventional treatment of cat naphtha (700 psig, 1000 scfb, and 2 LHSV) is expected to result in as much as a 10 octane number loss; therefore, advanced hydrotreating technology is used to give the needed desulfurization with only a 2 to 4 octane number loss.
Advanced hydrotreating recognizes the characteristics of light and heavy cat naphtha (HCN) fractions. LCN (light cat naphtha) is characterized with few light mercaptan sulfurs and a lot of olefin. HCN is characterized with a lot of sulfur and few olefins. Three treatment steps are used: 1. Full-range mild treatment for light sulfur conversion (mercaptans to heavy sulfur compounds through thioesterification) with minimal olefin saturation, 2. Fractionation of LCN and HCN, and 3. Conventional treatment of HCN (sulfides, disulfides, and thiophene conversion). Another technology is absorption removal of the sulfur compound, such as the S-Zorb process. The octane loss is expected to be 2 numbers. Butane treatment and additional aromatic extraction raffinate washing may be needed.
ERIC STREIT (KBC Advanced Technologies, Inc.)
Most refiners are apparently not mobilizing much in terms of external capital. Many invested in Tier 2 regulations and are primarily looking to extend the solution that they already have. They are either doing this internally or asking the current licensor to provide options for expanding the capability with a minor investment of a polishing reactor or something similar. Upgrading or expanding gasoline desulfurization units to reach the new sulfur level will result in an even greater octane loss in the treated naphtha than is currently seen.
Some refiners have discussed getting to the Tier 3 sulfur level with gas oil hydrotreating only. Although this may be possible, there are risks involved with this strategy. Gas oil hydrotreating removes the coke-producing material from the FCC feed. Increasing hydrotreating severity in the past has caused problems with FCC heat balances in several locations. Further increasing severity to try to get to Tier 3 compliance will cause further problems with FCC coke formation for many units. Also, hydrotreater cycle length may have to be decreased significantly to reach the new desired sulfur levels. In addition, relying only on an upstream hydrotreater to be able to meet the gasoline specification increases the risks associated with unplanned shutdowns of those units. During an unplanned shutdown of the gas oil hydrotreater, the refinery would not be able to make gasoline. With a gasoline desulfurizer, rates may be able to be reduced enough that some gasoline could still be produced during an unplanned gas oil hydrotreater shutdown.
Some refiners took full advantage of credits while meeting Tier 2 regulations to avoid additional octane loss. If there is a similar credit arrangement with the Tier 3 legislation, it is possible. Tier 2 precipitated a significant build-out of treatment facilities for refiners to meet the 30 ppm specification. Early movers generated credits that were useful. The incremental investment and associated timeline to startup will be less varied to go from Tier 2 compliance to Tier 3 for most folks.
Some refiners may need to look into treating streams previously considered diluents. Butane, for example, has not typically been treated to remove sulfur because the sulfur level of the butane was below the sulfur level of the gasoline. Now, that same butane stream may need to be treated to remove the small amount of sulfur that it contains.
Exporting sour naphtha will not be a feasible long-term solution for anyone. The outlets to the south will eventually close. There could be some transient opportunities for units with treating capacity to take some sour naphtha in the short term.
ROBERTSON (AFPM)
Before we get to the last question, I just want to remind you that the Gasoline P&P is this afternoon. It is subtitled, “Alkylation 101”. Robert Ohmes with KBC and Joe Zmich with UOP are the champions of that topic. I encourage you to attend, if those subject interests you.